When searching for the perfect panel bender machine for sale, it’s essential to consider various aspects to ensure you get the best value for your investment. A panel bender machine for sale can significantly enhance your production capabilities, providing precise and efficient bending solutions for various materials. This buyer's guide will walk you through the top options available, key features to look for, and tips on making an informed purchase to meet your specific manufacturing needs.
Table of Contents
What Is A Panel Bender Machine
A panel bender is a specialized machine used in metalworking and sheet metal fabrication processes. It plays a crucial role in bending and shaping flat metal sheets, transforming them into various forms required for specific applications. Panel benders are known for their precision, efficiency, and versatility in handling a wide range of sheet metal bending tasks.
Definition of a Panel Bender
A panel bender, also known as an automatic bending machine or panel bending brake, is designed for bending and forming flat metal sheets into specific shapes. This machine is widely utilized in industries such as manufacturing, automotive, aerospace, and construction, where precise bends and angles are essential for producing high-quality components.
Key Components of a Panel Bender Machine
To harness the full potential of panel bender machines in the realm of efficient fabrication, it’s essential to delve deeper into the key components that drive their functionality. Each part plays a pivotal role in ensuring the machine operates at peak efficiency, delivering precision and reliability in every bend. Here, we explore these components and their indispensable functions within the system.
Bending Blade:
The heart of the panel bender, the bending blade is responsible for the actual bending of the metal sheets. Its design is tailored to accommodate various material thicknesses and bend angles, ensuring flexibility across a range of applications. The quality and material of the blade directly influence the precision and quality of the bends it produces.
Control System:
Acting as the brain of the machine, the control system orchestrates the bending process with precision and efficiency. Advanced software enables operators to set detailed parameters, such as bend sequences and angles, while also offering the capability to store programs for future use. This digital backbone ensures repeatability and accuracy in production runs.
Clamping System:
Essential for securing the metal sheet in place during bending, the clamping system prevents movement that could lead to inaccuracies. Depending on the machine’s design, these clamps may be operated pneumatically or hydraulically, offering robust performance and reliability.
Backgauge:
Precision in bending is not solely about the bending action but also about the correct positioning of the sheet prior to bending. The backgauge facilitates this by accurately positioning the metal sheet for each bend. Adjustable and programmable, it ensures that each piece is bent at the correct location, crucial for consistent output.
Frame:
The structural backbone of the panel bender machine, the frame supports all other components. Its robust construction is designed to absorb the forces exerted during bending operations, maintaining machine stability and alignment, which are vital for achieving precise bends.
Together, these components form a cohesive system that defines the panel bender machine’s capabilities. Understanding the role and importance of each component can help operators maximize the machine’s efficiency and productivity, leading to streamlined operations and superior fabrication quality.
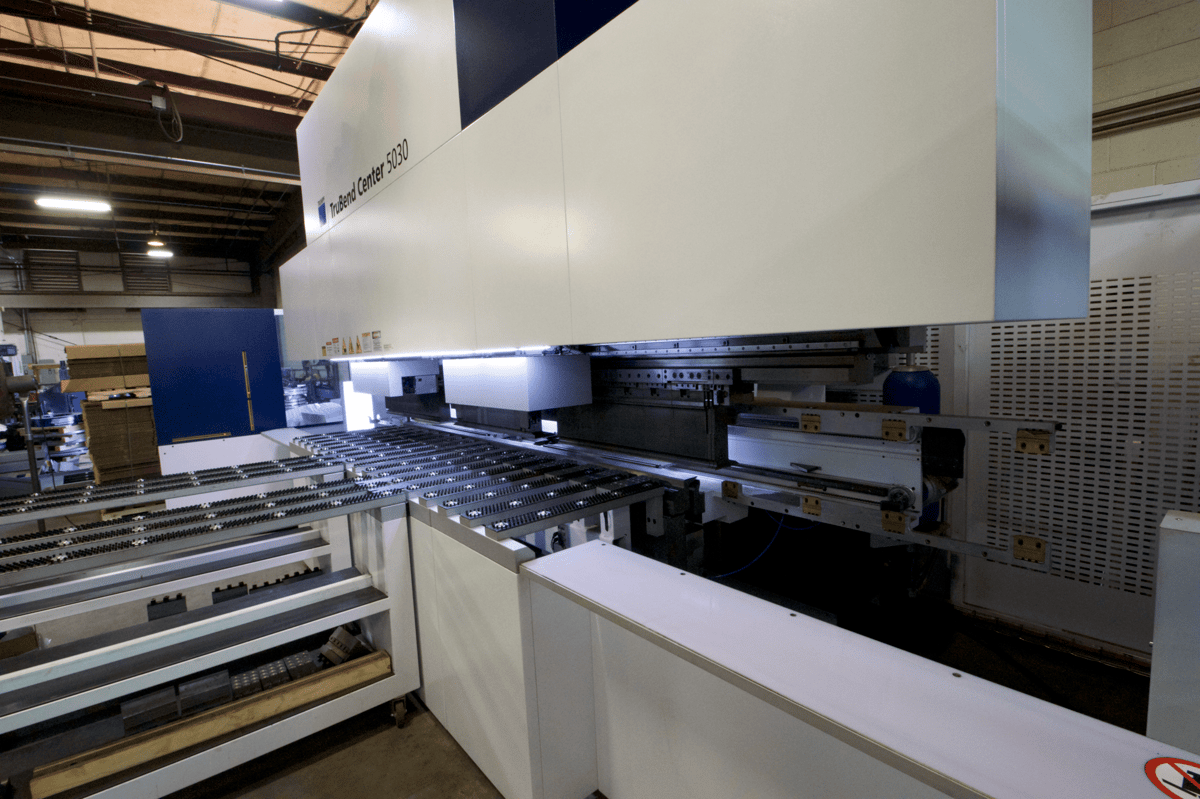
Working Principle of a Panel Bender
The working principle of a panel bender involves several coordinated steps to transform flat metal sheets into precisely shaped components. First, the flat metal sheet is loaded onto the machine, either manually by an operator or through automated feeding systems, ensuring efficient and accurate placement. Once in position, the clamping system secures the sheet, maintaining its stability and preventing any unwanted movement during the bending process.
The bending beam, equipped with the appropriate tooling, then exerts controlled force on the metal sheet, bending it to the specified angles and shapes with high precision. After the bending operation is complete, the formed sheet is released from the clamping system and unloaded, ready for further processing or assembly. This streamlined process ensures consistent quality and accuracy, making panel benders essential in industries that require precise metal forming.
Panel Bender Machine- Unparalleled Advantages
Accuracy
The panel bender has unparalleled accuracy and repeatability numbers. The panel bender’s integrated advanced sensors measure the blank, including material thickness, for precise placement and bending. The sensors also detect any deformations caused by variations in temperature. The collected data is used to instantly calculate the correct force required to bend the sheet metal. From the inside bend line to the inside bend line, the accuracy is +/- .008″ on the overall panel dimension. The repeatability of the panel bender is +/- .004″.
Efficiency
panel bender utilizes a part manipulator to move the metal sheet. Once the sheet is inserted against the locating device, the entire piece is formed without the operator having to touch it until it is completed. Intelligent sensors measure the thickness, size of the material, and environmental temperature and adapt the panel bender tooling to those changes, eliminating waste, mistakes, and inefficiencies. In other words, truly automated process.
This advantage speeds up the bending process for panel bender by 2 to 3 times compared to that of a traditional press brake. It also guarantees efficiency and consistency. For example, the Salvagnini P4 Panel Bender can complete, on average, 17 bends per minute.
Advantages of Soft Bending Center
The unique control system of the flexible soft bending center allows the bending knife to perform complex and unique travel bending, and realizes precise multi-angle bending, semi-open edge pressing and other forming technologies. At the same time, the automatically adjustable bending mold and adaptive bending compensation technology ensure high efficiency without mold change and high quality with precise angles.
The biggest advantage of the one-time forming of the flexible bending center is that it improves production efficiency. Since the single-sided bending machine needs to manually adjust the direction and then bend, a lot of working time is wasted. In theory, the operating efficiency of the multilateral flexible bending machine is 4 times that of the single-sided bending machine.
The servo design of the flexible soft bending machine allows for quick start and stop of the machine, fast processing speed, and can shorten processing time. The advantage is that it can automatically bend the four sides of the plate in sequence, realizing automation.
Flexible bending is suitable for new energy, home appliances, electricity, western kitchens, elevators, communications, network computer cabinets, medical machinery, fashion home furnishings, sheet metal processing, etc.
Soft Bending Center: Machine Performance Characteristics
The advantage of the soft bending machine is that it is not limited by the column spacing and throat depth of the C-type structure frame design, and can make full use of the bending machine processing, which is more flexible and convenient. Moreover, its servo design allows the machine to be started and stopped quickly, with fast processing speed and shortened processing time.
The advantage of the flexible bending machine is that it can automatically bend the four sides of the plate in sequence, realizing automation. The universal bending mold can realize the bending of the plate on both sides. The CNC positioning device is used for automatic positioning, and the multi-sided bending is completed in one positioning.
The flexible bending center adopts a new generation of CNC system, which is professionally developed for CNC equipment systems. After in-depth development by Zhihang CNC Company, it accurately realizes the perfect matching of all axes of the equipment in parallel, and the program programming is faster and easier;
The flexible bending machine is suitable for new energy, home appliances, electricity, western kitchens, elevators, communications, network computer cabinets, medical machinery, fashion home, sheet metal processing, etc.
What are Advantages of Soft Bending over Traditional Bender
Bending is the second step in the four steps of a sheet metal workpiece from raw materials to finished products. Originally, many ordinary bending machines required operators to perform production when bending, but this situation is gradually changing with the advancement of technology. Due to technological innovation, faster and better bending machines are replacing ordinary bending machines, and flexible fully automatic bending machines are one of the representatives.
In the past, when the bending machine was operated manually: the worker picked up a cut sheet from the pile; oriented it, slid it between the upper and lower tools until it hit the rear block, and finally lowered the upper die mechanism to bend the workpiece. Making another bend means: retrieving the sheet, adjusting the direction and position of the sheet; sometimes flipping the sheet to make the metal sheet bend in another direction. This is a hard job, especially for large and heavy metal sheets, which requires several people to handle. Moreover, it is easy for humans to make mistakes under high-intensity physical labor. Manual operation may accidentally put the wrong bend position or form the wrong angle, or even completely forget that the machine is working, which is very troublesome and laborious and cannot guarantee the completion of the workpiece.
Now with the development of technology and the advancement of CNC technology, the entire metal sheet production line is slowly being automated. And a large number of operations also show that for the manufacturing industry, the flexibility of sheet metal bending can make full use of the advantages of machinery, replace manual labor with machines, and use the bending settings of the CNC system to complete the process from material collection, loading and unloading, bending, and plate collection in one go, greatly reducing processing time and manpower and material resources.
For example, KRRASS Soft Bending Center, PBE series, is a new generation of fully automatic multilateral bending center, which is a benchmark product for the sheet metal manufacturing industry to enter automated production. The product not only saves a lot of manpower, but also has a bending speed that is three times that of CNC bending machines, reaching 0.5 s/time, and full servo control can control the product accuracy within 3S.
KRRASS Intelligent Flexible Intelligent Bending Center does not require molds to bend sheet metal, and can bend various complex shapes. It can bend right angles, non-right angles, arcs, up and down folds, and other complex shapes, which are used in the metal forming field of different industries and different workpieces. The equipment is equipped with a pure electric servo system to replace hydraulic drive, which has the advantages of environmental protection, fast speed, high precision, and maintenance-free.
Therefore, compared with ordinary bending machines, the operation of flexible bending machines has fast bending speed and high efficiency, and can maintain the consistency of workpieces, and there will be no error in the bending angle of the previous workpiece and this workpiece, and the efficiency and quality have achieved a qualitative leap!
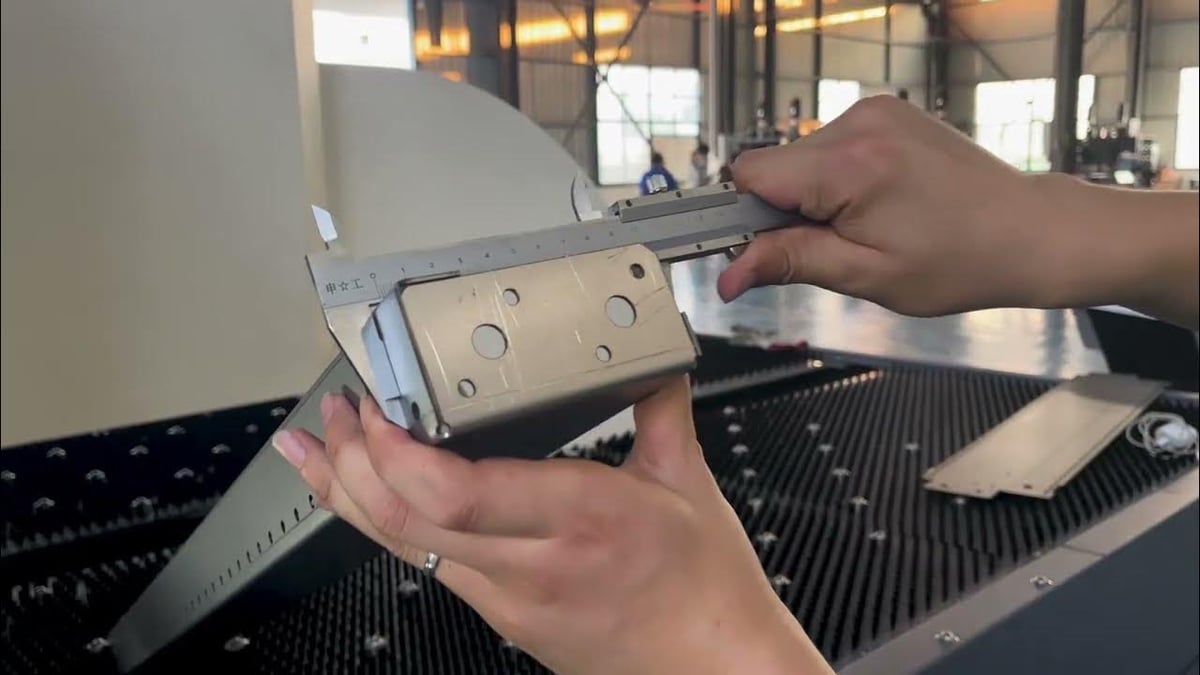
Panel Bender Machine for Sale - What You Should Know
Types
Automatic Panel Benders: These machines are fully automated and can handle a wide range of bending operations without the need for manual intervention. They are capable of bending complex shapes and are suitable for high-volume production.
Semi-Automatic Panel Benders: These machines combine automated features with some manual operation. They are versatile and often used for medium to large production runs where automation is beneficial but not fully required for every operation.
Manual Panel Benders: Also known as hand-operated or manual folding machines, these are operated entirely by hand or foot pedal. They are suitable for smaller production volumes or workshops where flexibility and cost-effectiveness are priorities over high-volume automation.
Servo-Electric Panel Benders: These machines use servo-electric motors for precise control over bending operations. They offer high accuracy, energy efficiency, and reduced maintenance compared to hydraulic systems.
Hydraulic Panel Benders: These machines use hydraulic systems to generate bending force. They are known for their high power and capability to handle heavy-duty bending tasks. Hydraulic panel benders are often preferred for applications requiring high bending force and versatility.
Applcations
Automotive Industry: Used for producing components such as vehicle body panels, interior parts, brackets, and structural components requiring precise bends.
Electronics and Electrical Enclosures: Used to manufacture enclosures, cabinets, racks, and chassis for electronic equipment and electrical control panels.
Aerospace and Aviation: Used for bending components like aircraft panels, brackets, structural parts, and interior fittings that require high precision and strength.
Furniture Manufacturing: Used to bend metal components for furniture frames, brackets, supports, and decorative elements in modern and industrial furniture designs.
Construction and Architecture: Used for bending metal components used in building facades, cladding, roofing, and structural elements where precise bending is essential for fit and function.
Industrial Equipment: Used to fabricate components for machinery, equipment frames, conveyor systems, and other industrial applications requiring custom-shaped metal parts.
Renewable Energy: Used in the production of components for solar panels, wind turbines, and other renewable energy systems where durable and precise metal bending is crucial.
Medical Equipment: Used for fabricating components for medical devices, diagnostic equipment, and medical furniture that require precise and hygienic metal bending solutions.
Consumer Goods: Used in manufacturing various consumer products requiring sheet metal components, such as appliances, fixtures, and decorative items.
Price Range
The price of panel bender machine for sale can vary significantly based on factors such as the machine type, size, automation level, brand, and specific features. Here's a general price range based on the types of panel benders:
- Manual Panel Benders: Typically range from $5,000 to $20,000 USD, depending on size and features.
- Semi-Automatic Panel Benders: Prices generally range from $20,000 to $50,000 USD, depending on size and automation features.
- Automatic Panel Benders: Prices can range from $50,000 to over $200,000 USD, depending on size, automation level, and capabilities such as complex bending, high-speed operation, and integrated tooling systems.
- Servo-Electric Panel Benders: These machines tend to be on the higher end of the price spectrum, starting from around $80,000 USD and going up based on size and features.
- Hydraulic Panel Benders: Prices can vary widely based on size and capacity, typically starting from $30,000 USD for smaller models and ranging upwards depending on the bending force and automation features.
It's important to note that these price ranges are approximate and can vary based on market conditions, geographical location, additional features, and the specific requirements of the buyer. Additionally, costs may include installation, training, and ongoing maintenance, so it's advisable to consider the total cost of ownership when evaluating panel bender machines.
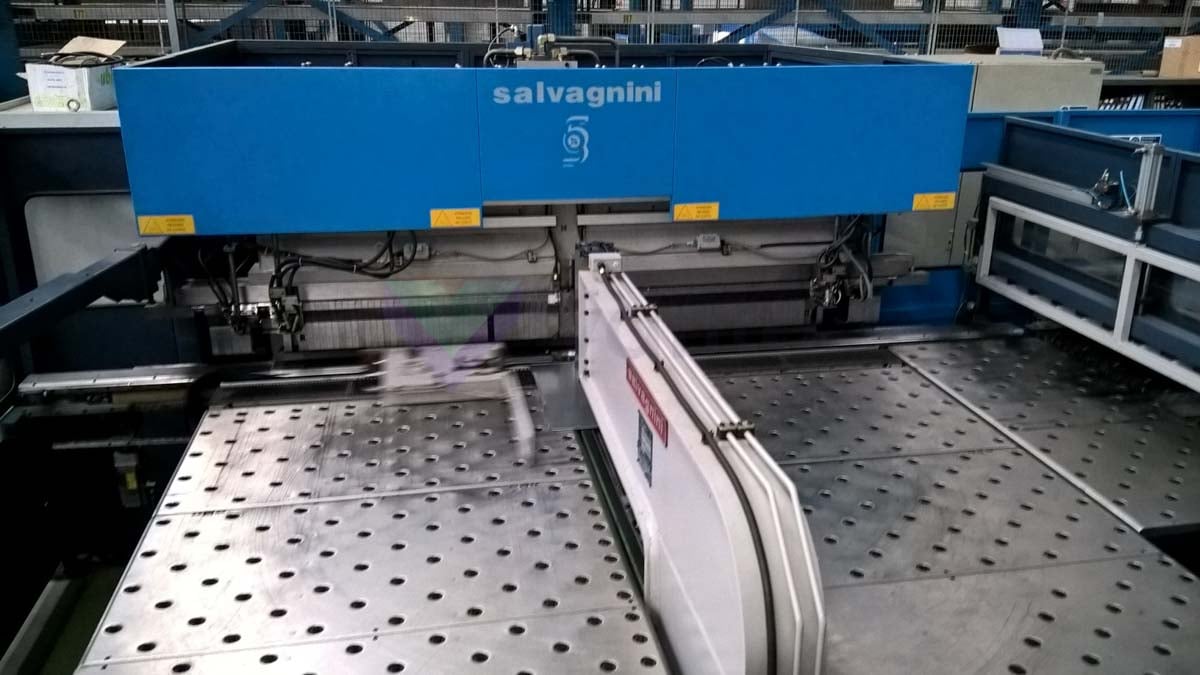
Top Panel Bender Machine Brands
Several top brands are renowned for manufacturing high-quality panel bender machines, each offering various models tailored to different production needs and specifications. Here are some of the top panel bender machine brands known for their reliability, innovation, and performance:
Salvagnini:
A leader in flexible sheet metal processing solutions, known for its highly automated and versatile panel bender machines.
TRUMPF:
Offers a range of panel bender machines known for their precision, efficiency, and integration with other sheet metal processing technologies.
Amada:
Known for innovative solutions in sheet metal fabrication, Amada's panel bender machines are recognized for their reliability and productivity.
Gasparini:
Specializes in both hydraulic and servo-electric panel benders, offering a range of models suitable for various sheet metal bending applications.
Schroeder:
Known for robust hydraulic panel benders capable of handling heavy-duty bending tasks with high precision.
Boschert:
Offers a range of manual, semi-automatic, and fully automatic panel benders suitable for diverse sheet metal bending requirements.
Haco:
Provides a variety of panel bender machines known for their durability, precision, and ability to handle complex bending operations.
RAS (Rainer Albrecth Stahlbau):
Innovators in panel bending technology, RAS machines are recognized for their high-speed bending capabilities and accuracy.
CIDAN Machinery:
Offers a range of panel benders known for their flexibility, precision, and ease of operation, suitable for various sheet metal bending tasks.
Durma:
Known for their range of servo-electric and hydraulic panel bender machines, Krrass offers solutions for both small-scale and industrial sheet metal bending applications.
These brands are highly regarded in the industry for their commitment to quality, technological innovation, and customer support, making them popular choices for businesses involved in sheet metal fabrication and bending operations.
How to Choose a Right Panel Bender for Sale
Assessing the Type and Volume of Work:
Understanding your fabrication needs begins with a thorough assessment of the type and volume of work you’ll be handling. Consider whether your projects primarily involve small-scale production runs, custom one-off pieces, or high-volume manufacturing. This assessment will help you determine the level of automation, precision, and throughput required from your panel bender.
Identifying the Materials and Specific Requirements:
Different materials present unique challenges in panel bending, so it’s essential to identify the types of materials you’ll be working with. Whether you’re bending aluminium, stainless steel, mild steel, or other alloys, each material has its own characteristics that influence bending capabilities and techniques. Additionally, consider any specific requirements such as tight tolerances, complex geometries, or surface finishes that may impact your choice of panel bender.
Considering Workflow Constraints and Preferences:
Take into account your workflow constraints and preferences when selecting a panel bender. Evaluate factors such as available floor space, layout efficiency, and ergonomic considerations to ensure seamless integration into your fabrication process. Consider whether you require a standalone machine or a fully automated cell with material handling and auxiliary equipment. Understanding your workflow preferences will help you choose a panel bender that optimizes productivity and minimizes downtime.
Conclusion
Compared with the press brake, the panel bender has more complete functions, higher automation and safer operation in the metal fabrication industry. The cost of the press brake is much less than that of the panel bender, but the operation of the panel machine is simple. CNC (Computer Numerical Control) panel benders represent the pinnacle of panel bending technology.
When choosing between the press brake and the panel bender, manufacturers should consider the specific needs of their production processes. Precision and efficiency are paramount in metal fabrication, and panel benders excel in delivering both. Using the panel bending machine can also reduce the cost of manpower and material resources through efficient batch production.
Our company, Krrass Machine Tool, has been providing boosts for manufacturing press brakes, panel benders, shearing, and fiber laser cutting machines for over 20 years to meet different customers' production needs. Our product experts can provide you with suggestions to choose the most appropriate and cost-effective machine.
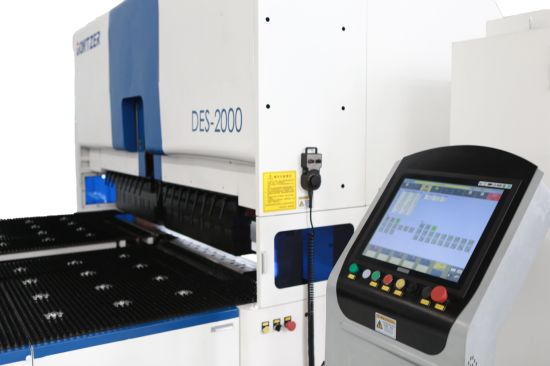