When it comes to metal fabrication, precision and efficiency are paramount, and a press brake is an essential tool in achieving these goals. Among the various sizes and types of press brakes available, the 4m press brake stands out for its versatility and capacity. Designed to handle large metal sheets with a bending length of 4 meters, this machine is ideal for a wide range of industrial applications, from heavy machinery manufacturing to structural metalwork and custom fabrication. Offering substantial benefits in terms of productivity and accuracy, the 4m press brake can significantly enhance your operations. In this article, we’ll explore its key features, benefits, and considerations, helping you make an informed decision when looking for a 4m press brake for sale.
Key Features of 4m Press Brakes
Capacity and Size: A 4m press brake is designed to accommodate metal sheets up to 4 meters in length, making it ideal for handling large and heavy materials. This extended bending length allows for the production of sizable components and complex shapes, enhancing the versatility of your fabrication processes. The increased capacity ensures that you can tackle a wider range of projects, from structural elements to custom metal parts, with precision and efficiency.
Hydraulic vs. Electric Options: 4m press brakes are available with either hydraulic or electric drive systems. Hydraulic press brakes utilize fluid pressure to apply force, offering robust performance and high bending power, especially for thicker materials. Electric press brakes, on the other hand, use servo motors for movement, providing greater energy efficiency, faster operation, and reduced maintenance requirements. Both systems have their own advantages, and the choice between them depends on your specific production needs and operational priorities.
Control Systems: Modern 4m press brakes are equipped with advanced CNC (Computer Numerical Control) systems that streamline the bending process. These controls come with user-friendly interfaces, such as touchscreens, that allow operators to input detailed bending instructions with ease. CNC controls offer precise programming capabilities, enabling complex bending sequences, accurate angles, and repeatable results. Features such as real-time monitoring and automatic adjustments further enhance precision and efficiency.
Tooling and Dies: The effectiveness of a press brake largely depends on the tooling used. For a 4m press brake, various options for upper and lower dies are available to accommodate different bending requirements. Selecting the right dies and tooling is crucial for achieving the desired bends and maintaining high-quality standards. Tooling options include a range of shapes and sizes, allowing for customization based on specific project needs and material types.
Safety Features: Ensuring operator safety is a critical aspect of modern press brake design. 4m press brakes are equipped with several safety measures, including protective guards, emergency stop buttons, and advanced sensors that prevent accidents and injuries. Safety features also include automatic shutoff systems if the machine detects any malfunctions or safety breaches. These measures not only protect the operators but also enhance the overall reliability and longevity of the equipment.
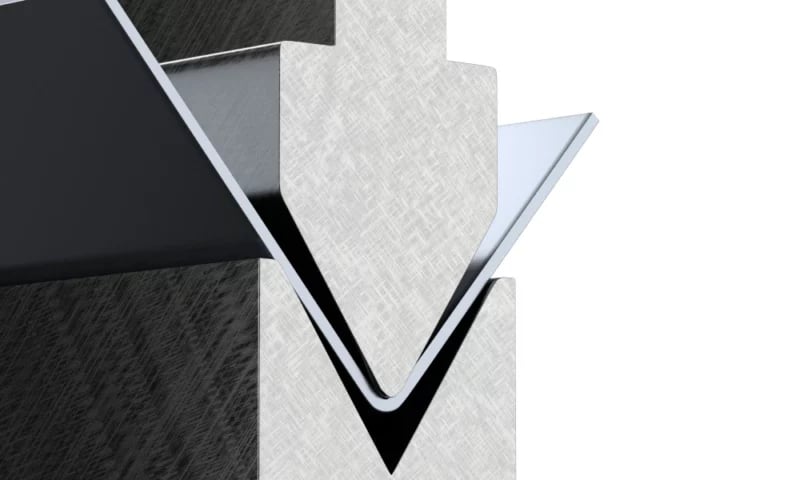
What Are the Corresponding Tonnages of 4m Press Brake
The tonnage of a 4m press brake refers to its bending capacity, which is the amount of force the machine can apply to bend metal sheets. The required tonnage for a press brake is typically determined by the thickness and type of material being processed. For a 4m (4-meter) press brake, the tonnage can vary significantly based on the machine's design and manufacturer, but here are some general guidelines:
- Light Duty: For lighter materials (such as thin sheets of aluminum or mild steel), a 4m press brake might have a tonnage in the range of 80 to 150 tons. This capacity is sufficient for standard bending tasks and lighter gauge materials.
- Medium Duty: For more common industrial applications, such as medium-gauge steel or other standard metals, a 4m press brake typically has a tonnage between 150 and 300 tons. This range allows for handling a broader variety of materials and thicknesses effectively.
- Heavy Duty: For heavy-duty applications involving thick plates of steel or other strong materials, a 4m press brake may require a tonnage of 300 tons or more. High-tonnage machines are designed to provide the necessary force to handle thicker and tougher materials, ensuring reliable bending performance.
The exact tonnage required for your specific needs will depend on factors such as the material type, sheet thickness, and the complexity of the bends. It's essential to consult with machine suppliers or manufacturers to determine the appropriate tonnage for your application to ensure optimal performance and efficiency.
Applications Insight
Industrial Manufacturing:
In the automotive, aerospace, and heavy machinery industries, a 4m press brake plays a crucial role in fabricating large, precise components. These industries often require the bending of sizable metal sheets to produce parts such as chassis, aircraft frames, and machinery components. The 4m press brake’s ability to handle large sheets efficiently makes it ideal for producing high-strength parts with exacting specifications, crucial for maintaining performance and safety standards in these demanding sectors.
Metal Fabrication Shops:
For custom metal fabrication and production, a 4m press brake offers significant advantages. Metal fabrication shops use these machines to create a wide range of custom parts, from intricate designs to straightforward components. The 4-meter length allows fabricators to work with larger sheets, enhancing their ability to handle diverse projects and scale up production. This flexibility is essential for meeting various client requirements and achieving high-quality results in custom metal work.
Construction and Infrastructure:
In construction and infrastructure projects, a 4m press brake is indispensable for producing structural metalwork and construction components. This includes bending large plates for use in bridges, buildings, and other structural elements. The press brake’s capacity to handle extensive metal sheets ensures that construction projects benefit from strong, durable components that meet design specifications and structural integrity requirements. Its ability to efficiently produce large quantities of accurately bent materials is vital for timely project completion and adherence to safety standards.
4m Press Brake Bending Capacity
The bending capacity of a 4m press brake is influenced by several key factors, each of which determines how effectively the machine can handle various materials and thicknesses. Here’s a detailed look at these factors:
Material Thickness:
The bending capacity of a 4m press brake varies depending on the thickness of the metal being processed. Generally, for a press brake with a tonnage range of 150 to 300 tons:
- Mild Steel: Capable of bending sheets up to 12mm thick. For heavy-duty models exceeding 300 tons, this capacity can extend to 20mm or more, making it suitable for industrial-grade applications.
- Stainless Steel: Due to its higher hardness, stainless steel is more challenging to bend. A 4m press brake typically handles stainless steel sheets up to 6-8mm thick, although higher-tonnage machines may manage thicker material.
- Aluminum: As a softer material, aluminum can be bent to greater thicknesses. A 4m press brake can effectively handle aluminum sheets up to 15mm thick, depending on the machine’s tonnage and tooling.
Material Type:
The type of metal being processed impacts the bending capacity. Each material requires different force levels to achieve precise bends:
- Mild Steel: Standard for most press brakes; common thicknesses range from 2mm to 12mm.
- Stainless Steel: Requires more force due to its hardness, limiting bending capacity to around 6-8mm.
- Aluminum: Easier to bend, allowing for thicker sheets, often up to 15mm, with a 4m press brake.
Machine Tonnage:
The tonnage rating of a press brake is directly related to its bending capacity:
- 150-200 Tons: Suitable for lighter to medium thickness materials, often used in general fabrication tasks.
- 200-300 Tons: Handles thicker materials and more demanding applications, such as structural components and larger assemblies.
- 300+ Tons: Designed for heavy-duty operations, capable of bending very thick and tough materials, ideal for large-scale industrial applications.
Tooling and Dies:
The type and configuration of tooling and dies play a crucial role in determining the machine’s effective bending capacity. Specialized dies can be used to accommodate different material types and bending angles, optimizing the performance of the press brake:
- V-Dies: Commonly used for general bending applications; available in various sizes to handle different material thicknesses.
- Custom Dies: For specialized bending tasks, custom dies can be designed to meet specific requirements, allowing for greater flexibility and precision.
Bend Length and Angle:
The maximum bend length that can be achieved with a 4m press brake is up to 4 meters. The bending capacity can also be affected by the angle of the bend and the length of the material:
- Long Bends: Bending longer sheets may require adjustments to machine settings to ensure even force distribution.
- Sharp Angles: Achieving sharp bends may necessitate additional force and precise adjustments to tooling.
Machine Specifications and Maintenance:
Regular maintenance and proper machine specifications ensure optimal performance. Ensuring that the press brake is well-maintained, calibrated, and using the correct tooling can significantly impact its bending capacity and overall efficiency.
To maximize the performance of a 4m press brake, it's essential to consult the manufacturer's specifications and tailor the machine settings and tooling to meet the specific requirements of your material and application. This approach ensures precision, efficiency, and durability in your bending operations.
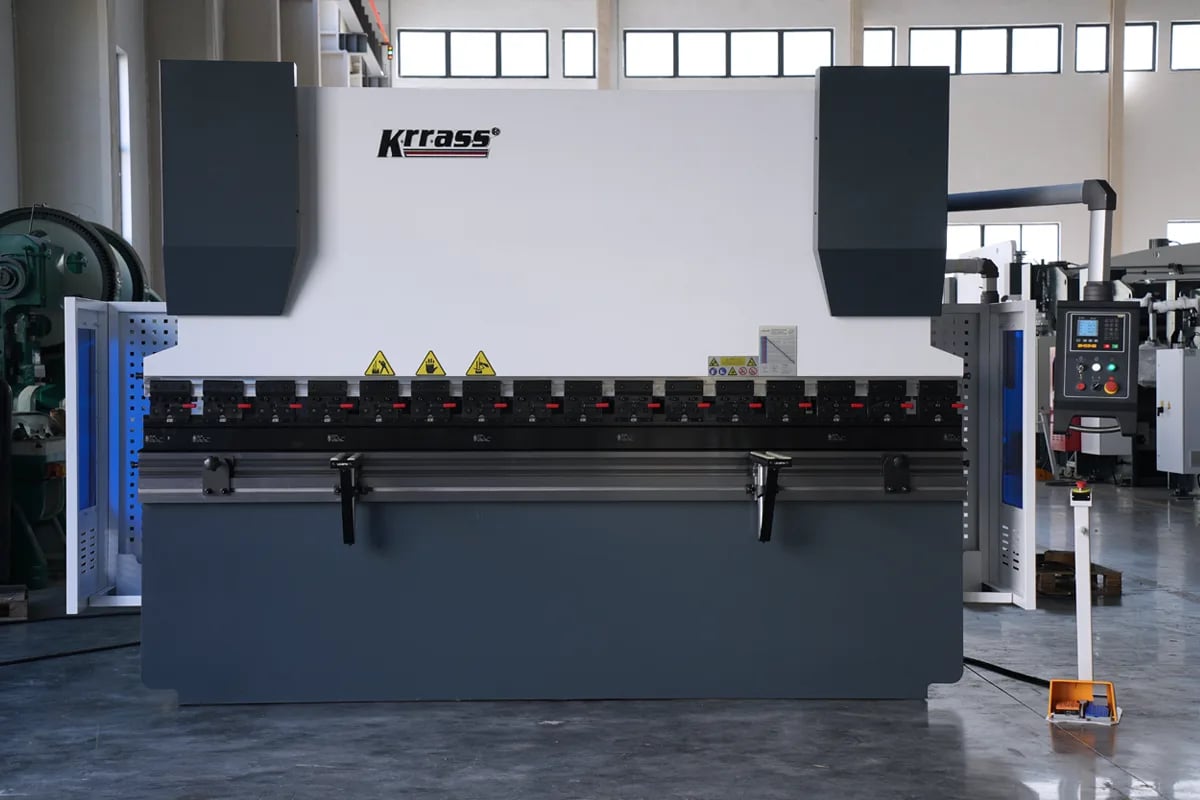
4m Press Brake for Sale: How to Choose Right One
Selecting the right 4m press brake is crucial for ensuring efficiency, accuracy, and long-term reliability in your manufacturing operations. Here’s a comprehensive guide to help you make an informed decision:
Assessing Your Needs: Start by evaluating your specific production requirements to determine the most suitable 4m press brake for your operations. Consider factors such as:
- Material Types and Thicknesses: Determine the types of metals you will be bending and their maximum thicknesses. Ensure the press brake has the appropriate tonnage and tooling options to handle these materials.
- Production Volume: Assess your production volume and frequency. High-volume production may require a machine with advanced automation and faster cycle times.
- Precision Requirements: If your work demands high precision, look for press brakes with advanced CNC controls and features that ensure accurate bending.
- Space and Layout: Measure the available space in your workshop to ensure the press brake fits comfortably and allows for safe operation and material handling.
Brand and Manufacturer: Choose a reputable brand and manufacturer known for producing reliable and high-quality press brakes. Consider:
- Industry Reputation: Research brands with a strong reputation in the industry for durability, performance, and innovation. Brands like Trumpf, Amada, and KRRASS are well-regarded.
- Customer Reviews and Case Studies: Look at customer reviews, testimonials, and case studies to gauge the performance and reliability of the press brakes from different manufacturers.
- Service Network: Ensure that the manufacturer has a robust service network and support system to address any issues that may arise.
New vs. Used: Evaluate the pros and cons of purchasing a new versus a used 4m press brake:
- New Press Brakes:
- Advantages: Come with the latest technology, warranties, and the assurance of being in pristine condition. Ideal for ensuring reliability and access to the newest features.
- Disadvantages: Higher upfront cost compared to used machines.
- Used Press Brakes:
- Advantages: More cost-effective and may provide significant savings. Suitable for budget-conscious buyers.
- Disadvantages: Potential for wear and tear, reduced warranty, and possible need for immediate repairs or upgrades. Ensure thorough inspection and testing before purchase.
After-Sales Support: After-sales support is crucial for maintaining the performance and longevity of your press brake. Consider:
- Warranty: Check the warranty terms offered by the manufacturer or dealer. A comprehensive warranty provides peace of mind and protection against potential defects.
- Maintenance Services: Ensure that the manufacturer or dealer offers maintenance services and support. Regular maintenance is essential for keeping the machine in optimal condition.
- Training: Look for training programs or resources provided by the manufacturer or dealer. Proper training for your operators ensures efficient and safe use of the press brake.
By carefully assessing your needs, researching reputable brands, weighing the pros and cons of new versus used machines, and considering after-sales support, you can make a well-informed decision and select the right 4m press brake to meet your production requirements.
Price of 4m Press Brake
The price of a 4m press brake can vary significantly based on several factors, including the brand, specific model, features, and whether it is new or used. Here is a general overview of the pricing ranges:
New 4m Press Brakes:
- Standard Models: Typically range from $30,000 to $60,000. These models come with essential features and capabilities suitable for a variety of bending tasks.
- Advanced Models: Can range from $60,000 to $100,000 or more. Advanced models include high-end CNC controls, enhanced precision, and additional features such as automation and advanced safety systems.
Used 4m Press Brakes:
- Good Condition: Prices generally range from $15,000 to $35,000. Used press brakes in good condition can offer significant savings compared to new models but may require careful inspection for wear and potential maintenance needs.
- Refurbished Models: Prices can range from $25,000 to $50,000. Refurbished machines often come with updated components and a limited warranty, providing a balance between cost and reliability.
Custom and Specialized Models:
- Custom Features: Press brakes with custom features or specialized applications may exceed the standard price ranges, depending on the complexity and customization involved.
Factors Influencing the Price
Brand and Manufacturer: Renowned brands like Trumpf, Amada, and KRRASS may command higher prices due to their reputation for quality and reliability.
Tonnage and Specifications: Higher tonnage and additional specifications (e.g., extended stroke, advanced CNC controls) can increase the price.
Technology and Automation: Press brakes with advanced CNC controls, automation options, and other high-tech features tend to be more expensive.
Additional Features: Safety features, tooling options, and customization can also impact the overall cost.
Additional Costs
Shipping and Installation: Costs for shipping and installation can add to the total price. These are often calculated separately and should be factored into the overall budget.
Training and Support: Some suppliers offer training and support services, which may be an additional cost to consider.
For precise pricing, it is best to contact manufacturers or authorized dealers directly. They can provide specific quotes based on your requirements and any ongoing promotions or discounts.
Parameters of 4m Press Brake at Krrass
Bending Length:
Maximum Bending Length: 4 meters (4000 mm). This allows the press brake to handle large metal sheets efficiently.
Tonnage Capacity:
Maximum Tonnage: Typically ranges from 150 to 300 tons, depending on the specific model and configuration. The tonnage determines the press brake's ability to handle different thicknesses and materials.
Bending Thickness:
- Mild Steel: Up to 12 mm for standard models; can reach 20 mm with higher tonnage configurations.
- Stainless Steel: Up to 6-8 mm, depending on the model.
- Aluminum: Up to 15 mm, depending on the press brake’s specifications.
Control System:
- CNC Control: Equipped with advanced CNC controls for precision and automation. The controls typically feature large touchscreens and intuitive interfaces for easy programming.
- Software Features: Includes options for precise angle setting, bend sequencing, and material compensation.
Tooling:
- Upper and Lower Dies: Interchangeable dies for various bending tasks. The selection of tooling impacts the machine’s flexibility and capability.
- Tooling Options: Includes standard V-dies, custom dies for specific applications, and specialized tooling for complex bends.
Stroke and Distance:
- Maximum Stroke: Usually around 200-300 mm, allowing for various bending operations and thicknesses.
- Distance Between Housings: Sufficient to accommodate different sheet sizes and bending needs.
Back Gauge:
- Accuracy: High-precision back gauge system for accurate positioning of metal sheets. Typically adjustable with a range of 1000 mm to 1500 mm.
Machine Dimensions:
- Overall Dimensions: Varies depending on the specific model but generally includes the length, width, and height dimensions to ensure compatibility with your workshop space.
Speed and Efficiency:
- Bending Speed: Variable speed settings for optimizing production efficiency and precision.
- Return Speed: Adjustable to ensure smooth operation and reduce cycle times.
Safety Features:
- Safety Guards: Equipped with safety barriers and emergency stop functions to protect operators.
- Anti-Collision Systems: Sensors and alarms to prevent collisions and ensure safe operation.
These parameters highlight the capabilities and features of the KRRASS 4m press brake, making it suitable for a wide range of bending applications in industrial and metal fabrication settings. For detailed specifications and customization options, it's advisable to consult directly with KRRASS or an authorized distributor.
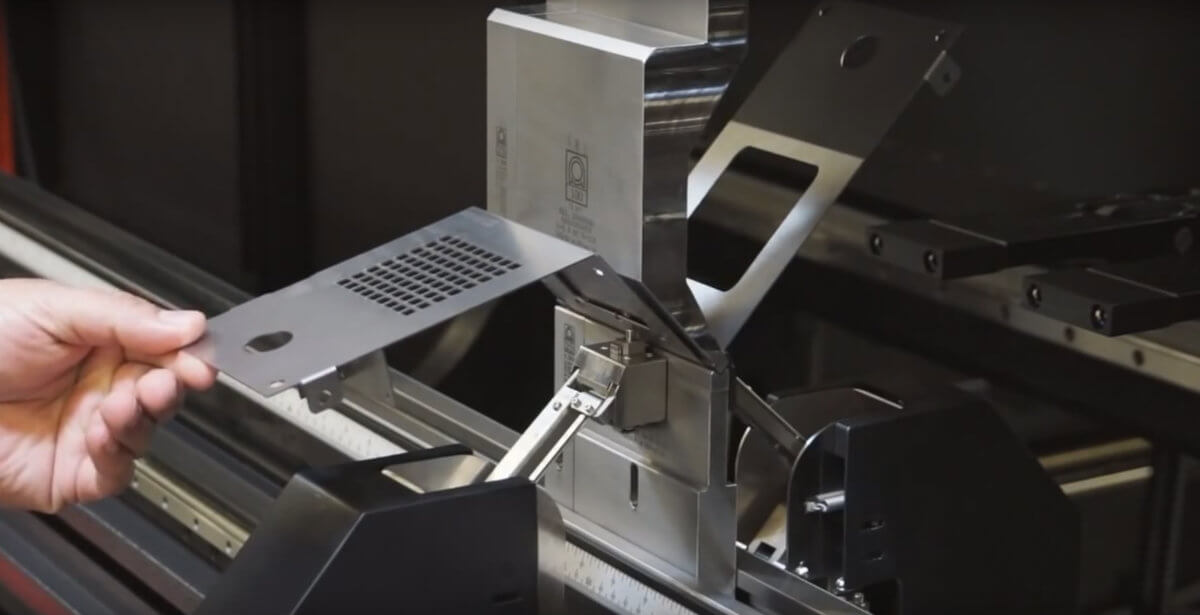
Conclusion
In conclusion, a 4m press brake for sale offers exceptional value for any metalworking shop, combining a substantial bending length with precision and efficiency to handle large metal sheets and complex tasks. Featuring advanced CNC controls, customizable tonnage, and options for both hydraulic and electric drive systems, these machines are designed to meet diverse production needs. The pricing for a 4m press brake varies, typically ranging from $30,000 to $100,000 for new models and $15,000 to $50,000 for used or refurbished units. Investing in a 4m press brake enhances accuracy and productivity, making it a significant asset for any manufacturing setup. For tailored information and quotes, consulting with reputable suppliers or manufacturers is recommended to ensure you find the best fit for your specific requirements.