A press brake is a machine tool used in metalworking and fabrication processes to bend and shape sheet metal. It is a crucial tool in the manufacturing industry, especially in industries that involve metal forming for various applications, such as automotive, aerospace, construction, and electronics.
The primary function of a press brake is to apply force to a piece of sheet metal, causing it to bend or deform along a predetermined axis. The machine consists of a sturdy frame, a bottom die, and an upper tool, often called the punch. The sheet metal is placed between the two tools, and as the upper tool descends, it exerts pressure on the metal, bending it to the desired angle.
Press brakes come in various sizes and configurations, ranging from manual or hydraulic machines for smaller-scale operations to large CNC (computer numerical control) press brakes for high-precision and automated bending in large-scale manufacturing settings. CNC press brakes allow for precise control over factors such as bend angle, bend radius, and back gauge positioning, making them versatile and efficient for producing complex metal components with consistent accuracy.
Press brakes are essential for creating a wide range of metal components, including brackets, enclosures, chassis, and other parts used in various industries. They play a crucial role in the metal fabrication process, enabling the production of components with precise shapes and dimensions.
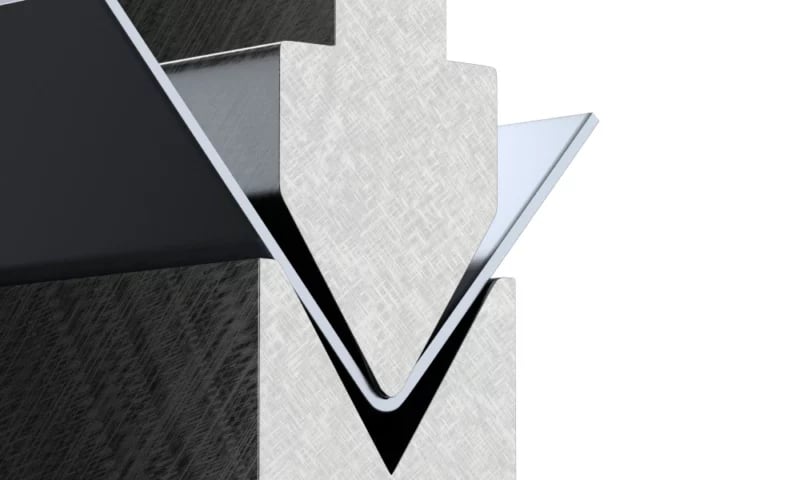
What do press brakes do?
Press brakes are used to bend and shape sheet metal into various forms and angles. The primary function of a press brake is to apply force to a piece of sheet metal, causing it to deform and bend along a predetermined axis. Here are the key tasks that press brakes perform:
1.Bending:The main purpose of a press brake is to bend sheet metal to a specific angle. This is achieved by placing the metal between the punch (upper tool) and the die (bottom tool) and applying force to deform the material.
2.Forming:Press brakes are used to form sheet metal into different shapes and contours. This is crucial in manufacturing components with specific geometric requirements, such as brackets, enclosures, or structural elements.
Die Cutting:
Some press brakes can be equipped with specialized dies for cutting shapes out of the sheet metal. While not as common as bending, die cutting can be performed on certain press brake configurations.
3.Coining:
Coining is a precise forming process that involves applying high pressure to achieve extremely accurate bends and shapes. Press brakes can be used for coining operations when a high level of precision is required.
4.Embossing and Ribbing:Press brakes can create raised patterns, embossing, or ribs on the surface of the sheet metal. This is often done for decorative or functional purposes.
5.Flanging:Flanging involves forming a flange (an edge or rim) on a piece of sheet metal. Press brakes are used to achieve this by bending the edge of the material at a specific angle.
6.Hemming:Hemming is a process where the edge of the sheet metal is folded over onto itself to create a smooth and safe edge. Press brakes are commonly used for hemming operations.
7.Curling:Curling involves forming a curved or rolled edge on the sheet metal. Press brakes can be used for curling operations, particularly for creating rounded or circular shapes.
8.Backgauging and Precision Control:Modern press brakes often feature CNC (computer numerical control) systems with backgauges that allow for precise control over the positioning of the sheet metal. This enables accurate and repeatable bending operations.
Press brakes are versatile tools that play a critical role in metalworking and fabrication industries, contributing to the production of a wide range of components with different shapes and dimensions.
Why is it called a press brake?
The term "press brake" comes from the two primary components that define the machine's function: the "press" and the "brake."
1.Press:The term "press" refers to the machine's ability to apply force or pressure to deform and shape materials. In the case of a press brake, this force is applied to bend or form sheet metal.
2.Brake:The term "brake" in the context of a press brake does not refer to a braking mechanism as one might find in a vehicle. Instead, it is derived from the Middle English word "brak," which means "to bend" or "to slope." In this sense, the "brake" in press brake signifies the machine's primary function of bending or shaping sheet metal.
So, when combined, "press brake" essentially means a machine that presses (applies force) to bend or shape materials, particularly sheet metal. The name reflects the machine's fundamental capability to deform and manipulate metal sheets through the application of pressure, resulting in various bending and forming operations.
How does the bending process work?
The bending process in a press brake involves deforming a sheet metal workpiece to a specific angle by applying force. Here's a step-by-step explanation of how the bending process typically works:
Setup:The sheet metal workpiece is first positioned between the punch (upper tool) and the die (bottom tool) on the press brake. The die provides the bending surface, and the punch comes down to shape the metal.
Clamping:The sheet metal is securely clamped between the punch and the die to prevent any movement during the bending process. Proper clamping is essential for achieving accurate and consistent bends.
1.Selection of Tools:The appropriate punch and die tools are selected based on the desired bend angle, bend radius, and the thickness and type of material being used. Different tool setups can produce various bend profiles.
2.Programming (for CNC Press Brakes):In the case of CNC (computer numerical control) press brakes, the bending process is often programmed using software. The CNC system controls parameters such as the bending angle, backgauge position, and the sequence of bending operations.
3.Bending:The press brake's ram, which carries the punch, descends to apply force to the sheet metal. This force causes the metal to bend as it conforms to the shape of the die. The bending occurs along a predetermined axis, and the angle is determined by the depth to which the punch descends.
4.Springback:After the bending force is released, the sheet metal may experience a phenomenon known as "springback." Springback is the tendency of the metal to partially return to its original shape after being bent. Compensations for springback are often considered in the bending process to achieve the desired final angle.
5.Removal of the Bended Part:Once the bending operation is complete, the press brake's ram is raised, and the clamps are released. The bended part is then removed from the machine for further processing or assembly.
6.Quality Control:The bent part may undergo quality control checks to ensure it meets the specified tolerances and dimensions. This can involve measuring the bend angle and inspecting the overall geometry of the bent component.
Throughout the process, factors such as material type, thickness, tooling selection, and machine settings need to be carefully considered to achieve accurate and repeatable bending results. Modern press brakes, especially those with CNC capabilities, provide precise control over the bending parameters, allowing for efficient and high-precision metal forming operations.
Common press brake applications:
Press brakes are versatile machines used in a wide range of industries for various applications involving the bending and forming of sheet metal. Some common press brake applications include:
Metal Enclosures:
Press brakes are frequently used to manufacture metal enclosures for electronics, control panels, and machinery. These enclosures often require precise bends and shapes to accommodate components and provide protection.
Brackets and Supports:
The production of brackets, supports, and mounting components for various applications, such as in construction, automotive, or industrial machinery, is a common use of press brakes.
Automotive Components:
Press brakes are employed to fabricate various automotive components, including brackets, panels, frames, and chassis parts that require complex bends and shapes.
Aerospace Parts:
In the aerospace industry, press brakes are used to manufacture structural components, brackets, and panels for aircraft. The precision and repeatability of press brakes make them suitable for aerospace applications.
1.Appliance Parts:Press brakes are utilized in the production of metal parts for appliances, including components for ovens, refrigerators, washing machines, and other household products.
2.Architectural Metalwork:For architectural purposes, press brakes are employed to create decorative elements, railing components, and other metal features used in building construction.
3.Furniture Manufacturing:Press brakes play a role in the production of metal furniture components, such as chair frames, table bases, and other structural elements requiring precise bending.
4.HVAC Ductwork:The fabrication of HVAC (heating, ventilation, and air conditioning) ductwork involves the use of press brakes to create the necessary bends and shapes for duct components.
5.Lighting Fixtures:Press brakes are used to manufacture metal components for lighting fixtures, including lampshades, frames, and other decorative or structural elements.
6.Farm Equipment:Press brakes are employed in the production of components for agricultural machinery, such as brackets, panels, and supports for tractors and other farm equipment.
7.Medical Equipment:The manufacturing of certain medical equipment components, such as metal casings and supports, may involve the use of press brakes.
8.Electronic Components:Press brakes are utilized in the fabrication of metal components for electronic devices, ensuring precise shapes and dimensions for housings and enclosures.
These are just a few examples, and press brakes are widely used in many other industries and applications where precise metal bending and forming are essential. The versatility of press brakes makes them a crucial tool in metal fabrication and manufacturing processes.