Press brake tooling plays a pivotal role in any metalworking shop. It is the cornerstone of precision sheet metal fabrication, providing the necessary force and shape to bend and form sheet metal into desired configurations. Overall, press brake tooling is essential for achieving precise, efficient, and reliable bending operations in metal fabrication, ultimately contributing to the overall quality and profitability of the manufacturing process.
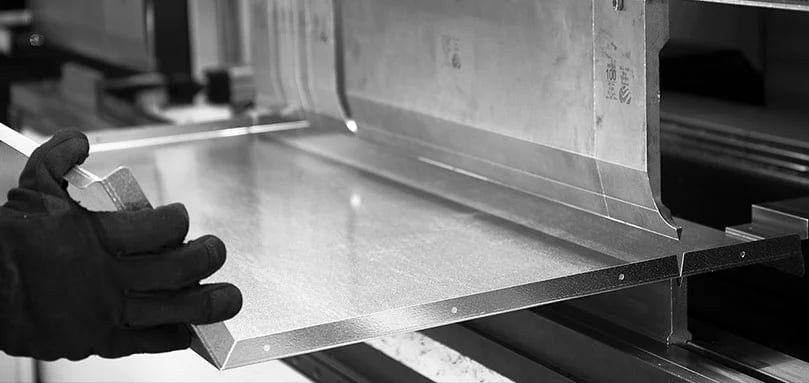
Press brake tooling plays a crucial role in the metal fabrication process, and its importance stems from several key reasons:
Bending Accuracy: The primary function of press brake tooling is to shape metal sheets accurately and consistently according to desired specifications. High-quality tooling ensures precise bending angles and dimensions, leading to accurate finished parts.
Versatility: Press brake tooling comes in various shapes and sizes to accommodate different bending requirements. With the right selection of tooling, operators can perform a wide range of bending operations, including straight bends, flanges, curls, and more complex shapes.
Efficiency: Well-designed tooling can streamline the bending process, reducing setup time and increasing production efficiency. Quick-change tooling systems allow operators to swap out tooling quickly, minimizing downtime between jobs.
Durability: Durable tooling materials, such as hardened steel or carbide, can withstand the high forces and pressures involved in bending metal sheets. This durability ensures that the tooling maintains its shape and integrity over many bending cycles, minimizing the need for frequent replacements.
Surface Finish: The condition of the tooling surfaces directly affects the quality of the finished parts. Smooth and properly maintained tooling surfaces help prevent surface imperfections, such as scratches or marks, on the bent parts.
Safety: Properly designed and maintained tooling contributes to a safer working environment for press brake operators. Sturdy tooling reduces the risk of tool breakage or bending accidents, minimizing the potential for injuries.
Cost-effectiveness: While high-quality press brake tooling may represent an initial investment, it can lead to long-term cost savings by reducing scrap, rework, and downtime associated with poor-quality tooling. Additionally, durable tooling requires less frequent replacement, resulting in lower maintenance costs over time.
What Is Press Brake Tooling
Press brake tooling refers to the components and accessories used in press brake machines to shape and bend metal sheets or plates into desired forms. These tools are essential for accurately bending metal parts in various industries, including manufacturing, automotive, aerospace, and construction.
Press brake tooling typically consists of the following components:
Punch: The punch is the upper tooling component that applies force to the metal sheet, causing it to bend against the lower tooling (die). Punches come in various shapes and sizes to accommodate different bending requirements, such as V-dies for straight bends or specialized shapes for complex bends.
Die: The die is the lower tooling component that supports the metal sheet during bending. It provides a surface against which the metal is formed by the punch. Dies also come in various shapes and sizes, including V-shaped dies, radius dies, and specialty dies for specific bending applications.
Press Brake Tooling Materials
Press brake tooling materials include hardened steel and tungsten carbide. Hardened steel is durable and capable of withstanding repeated use without significant wear. Tungsten carbide, while more expensive, offers superior strength and resistance to wear, making it ideal for high-volume or high-precision applications.
Punches and Dies Every Metalworking Shop Should Have
There are various types of punches and dies that a metalworking shop should have so that it can cater to a diverse range of projects. Standard punches and dies, gooseneck punches, acute angle dies, and hemming dies are just a few examples.
Standard punches and dies are versatile and can handle most common bending tasks. Gooseneck punches are perfect for forming deep channels or boxes, while acute angle dies allow for bending at sharp angles. Hemming dies are used to create clean, flat edges on sheet metal.
Solutions for Long Sheet Metal
Working with long sheet metal can be challenging due to its size and weight. One solution is to use tandem press brakes, also called synchronized hydraulic press brakes. These two press brakes work together to handle long sheet metal. This setup increases bending capacity and precision, allowing for the efficient processing of large sheets.
Press brakes can’t bend metal accurately without critically important press brake tooling. Tooling is essential to any metal fabrication shop’s productivity and the quality of its output.