The selection of cutting process parameters for CNC plasma cutting machines is crucial to the quality, speed and efficiency of the cutting results.
To use a CNC plasma machine correctly for high-quality and fast cutting, it is essential to have a profound understanding and mastery of the cutting process parameters.
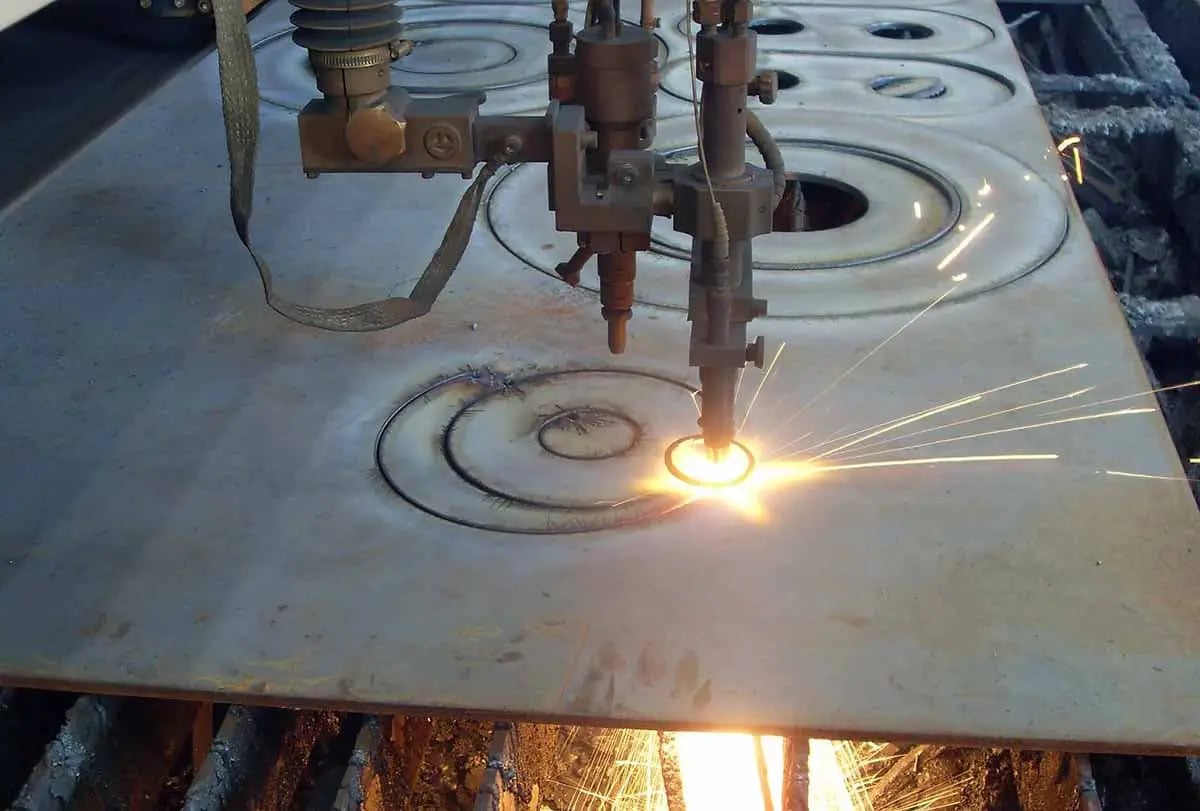
Table of Contents
I. Cutting current
It is the most important cutting process parameter which directly determines the thickness and speed of the cutting, i.e., the cutting ability. Its effects are as follows:
1. As the cutting current increases, the arc energy also increases, resulting in higher cutting ability and increased cutting speed.
2. As the cutting current increases, the diameter of the arc also increases, making the cut wider.
3. If the cutting current is too high, the nozzle will overheat, leading to premature damage and a decrease in cutting quality, or even preventing normal cutting from occurring. Therefore, it is necessary to choose the appropriate cutting current and corresponding nozzle based on the material thickness before cutting.
II. Cutting speed
The optimal cutting speed range can be determined according to the equipment instructions or by experimentation.
Due to factors such as material thickness, material type, melting point, thermal conductivity, and surface tension after melting, the cutting speed also changes accordingly. Its main effects are as follows:
Moderately increasing the cutting speed can improve the quality of the cut, i.e., slightly narrowing the cut, making the cut surface smoother, and reducing deformation.
If the cutting speed is too fast, the energy of the cutting line will be lower than the required value, and the jet cannot blow off the melted cutting melt immediately, resulting in a larger amount of back drag and slag hanging on the cut, causing a decrease in cut surface quality.
When the cutting speed is too low, as the cutting position is the anode of the plasma arc, in order to maintain the stability of the arc itself, the anode spot or anode area must find a place to conduct current near the nearest cut, which will transfer more heat radially to the jet.
Therefore, the cut becomes wider, and the molten material on both sides of the cut gathers and solidifies at the bottom edge, forming hard-to-clean slag. Additionally, the upper edge of the cut forms a rounded corner due to excessive heating and melting.
When the speed is extremely low, the arc may even extinguish. Thus, good cutting quality and cutting speed are inseparable.
III. Arc voltage
The normal output voltage of the power supply is generally regarded as the cutting voltage.
CNC plasma arc cutting machines usually have high no-load voltage and working voltage.
When using gases with high ionization energy such as nitrogen, hydrogen, or air, the voltage required for stable plasma arc is higher. When the current is constant, an increase in voltage means an increase in arc enthalpy and cutting ability.
If the diameter of the jet is reduced while increasing gas flow rate at the same time with an increase in enthalpy, it often results in faster cutting speed and better cutting quality.
IV. Working gas and flow rate
The working gases include cutting gas, auxiliary gas, and some equipment also requires starting gas. Usually, the appropriate working gas should be selected based on the type, thickness, and cutting method of the material.
The cutting gas needs to ensure the formation of plasma jet while removing molten metal and oxides from the cut.
Excessive gas flow can take away more arc heat, shorten the length of the jet, lead to a decrease in cutting ability, and unstable arc; insufficient gas flow can cause the plasma arc to lose its necessary straightness, resulting in shallow cuts, and also easily causing slag hanging.
Therefore, gas flow rate must be well coordinated with cutting current and speed.
Most modern plasma arc cutting machines control flow rate by gas pressure because when the gun aperture is fixed, controlling gas pressure also controls flow rate.
The gas pressure used for cutting a certain thickness of material usually needs to be selected according to the data provided by the equipment manufacturer.
If there are other special applications, the gas pressure needs to be determined through actual cutting trials.
The most commonly used working gases are argon, nitrogen, oxygen, air, and H35, argon-nitrogen mixed gas, etc.
1. Argon gas has almost no reaction with any metal at high temperatures, and the plasma arc of argon gas is very stable.
Moreover, the nozzle and electrode used have a relatively long service life. However, the voltage of argon plasma arc is lower, and the enthalpy value is not high, resulting in limited cutting ability.
Compared with air cutting, its cutting thickness will approximately decrease by 25%.
Additionally, in an argon protective environment, the surface tension of melted metal is greater, about 30% higher than that in a nitrogen environment.
Therefore, there may be more slag hanging problems.
Even when cutting with a mixed gas of argon and other gases, there will be a tendency to have sticky slag. Thus, pure argon gas is now rarely used alone for plasma cutting.
2. Hydrogen gas is usually used as an auxiliary gas mixed with other gases.
For example, the well-known H35 gas (hydrogen volume fraction of 35%, the rest is argon) is one of the strongest gases in plasma arc cutting ability, which is mainly due to hydrogen gas.
Because hydrogen gas can significantly increase the arc voltage, making the hydrogen plasma jet have a high enthalpy value. When mixed with argon gas, the cutting ability of the plasma jet is greatly improved.
Generally, for metal materials with a thickness of more than 70 mm, argon + hydrogen is commonly used as the cutting gas. If using water jet to further compress the argon + hydrogen plasma arc, even higher cutting efficiency can be achieved.
3. Nitrogen is a commonly used working gas for CNC plasma cutting machines
Under high power supply voltage conditions, nitrogen plasma arc has better stability and higher jet energy than argon gas.
Even when cutting materials with high viscosity such as stainless steel and nickel-based alloys, the amount of slag hanging under the incision is also very small. Nitrogen can be used alone or mixed with other gases.
In automated cutting, nitrogen or air is often used as the working gas in plasma cutting machine, and these two gases have become standard gases for high-speed cutting of carbon steel. Sometimes nitrogen is also used as the arc starting gas in oxygen plasma cutting.
4. Oxygen can increase the cutting speed of low carbon steel materials.
When using oxygen for cutting, the cutting mode is similar to flame cutting. The high-temperature and high-energy plasma arc makes the cutting speed faster, but it must be used in conjunction with electrodes that are resistant to high-temperature oxidation.
At the same time, the electrode should be protected against impact during arc initiation to extend its life.
5. Air contains about 78% volume fraction of nitrogen, so the slag hanging situation formed by using air for cutting is similar to that when using nitrogen for cutting.
Air also contains about 21% volume fraction of oxygen, and due to the presence of oxygen, the cutting speed of low carbon steel material using air is also high. At the same time, air is also the most economical working gas.
However, when air is used for cutting alone, there are issues with slag hanging, as well as oxidation and nitrogen increase at the incision. The low lifespan of electrodes and nozzles can also affect work efficiency and cutting costs.
V. Nozzle height
Refers to the distance between the nozzle end face and the cutting surface, which constitutes a part of the entire arc length. Since plasma arc cutting generally uses constant current or steep drop characteristic power sources, the current changes very little after the nozzle height increases.
However, it will increase the arc length and cause the arc voltage to increase, thus increasing the arc power. But at the same time, it will also increase the energy loss of the arc column exposed to the environment.
Under the combined effect of these two factors, the effect of the former is often completely offset by the latter, which may reduce the effective cutting energy and lower the cutting ability.
This is usually manifested as a weakening of the cutting jet force, an increase in residual slag at the bottom of the incision, and rounding of the upper edge.
In addition, considering the shape of the plasma cutting machine jet, the jet diameter expands outward after leaving the gun, and the increase in nozzle height will inevitably cause an increase in the width of the incision.
Therefore, choosing the smallest possible nozzle height is beneficial for improving cutting speed and quality.
However, when the nozzle height is too low, double arcs may occur. Using ceramic outer nozzles can set the nozzle height to zero, that is, the nozzle end face directly contacts the cut surface, which can achieve good results.
VI. Cutting power density
In order to obtain a high-compression plasma arc for plasma cutting, the cutting nozzle uses a small nozzle aperture, a longer bore length, and strengthened cooling effect. This can increase the current passing through the effective cross-sectional area of the nozzle, that is, increase the arc power density.
However, compression also increases the power loss of the arc, so the actual energy used for cutting is smaller than the power output of the power source, and its loss rate is generally between 25% and 50%.
Some methods, such as water compression plasma arc cutting, may have a higher energy loss rate. This issue should be considered in the design of cutting process parameters or economic accounting of cutting costs.
For example, the metal plate thickness commonly used in industry is mostly below 50mm.
Within this thickness range, conventional plasma arc cutting often forms a cut with a larger upper edge and a smaller lower edge, and the upper edge of the cut may cause a decrease in the size accuracy of the incision and increase subsequent processing work.
When using oxygen and nitrogen plasma arc cutting of carbon steel, aluminum, and stainless steel, when the thickness of the plate is within the range of 10-25mm, the material is thicker, the verticality of the edge is better, and the angle error of the cutting edge is 1 degree to 4 degrees.
When the plate thickness is less than 1mm, as the plate thickness decreases, the angle error of the incision increases from 3-4 degrees to 15-25 degrees.
It is generally believed that the cause of this phenomenon is due to the uneven heat input of the plasma jet on the cutting surface, that is, the release of plasma arc energy in the upper part of the incision is more than the lower part.
This energy release imbalance is closely related to many process parameters of CNC plasma cutting machine, such as the degree of plasma arc compression, cutting speed, and nozzle-to-workpiece distance.
Increasing the compression degree of the arc can extend the high-temperature plasma jet to form a more uniform high-temperature area, and at the same time increase the speed of the jet, which can reduce the width difference of the upper and lower edges of the incision.
However, excessive compression of conventional nozzles often causes double arcs, which not only consume electrodes and nozzles, making the cutting process impossible to proceed, but also lead to a decrease in the quality of the incision.
In addition, excessive cutting speed and nozzle height can also increase the width difference between the upper and lower edges of the incision.
VII. Plasma cutting machine process parameter table
Low-carbon steel air plasma/air protection cutting current 130A
Select gas | Set cutting airflow | Material thickness | Arc voltage | Distance from cutting torch to workpiece | Cutting speed | Initial piercing height | Piercing delay | |||
Plasma | Protective gas | Plasma | Protective gas. | mm | Voltage | mm | mm/min | mm | Coefficient % | Second |
Air | Air | 72 | 35 | 3 | 136 | 3.1 | 6000 | 6.2 | 200 | 0.1 |
4 | 137 | 3.1 | 4930 | 6.2 | 200 | 0.2 | ||||
6 | 138 | 3.6 | 3850 | 7.2 | 200 | 0.3 | ||||
10 | 142 | 4.1 | 2450 | 8.2 | 200 | 0.5 | ||||
12 | 144 | 4.1 | 2050 | 8.2 | 200 | 0.5 | ||||
15 | 150 | 4.6 | 1450 | 9.2 | 200 | 0.8 | ||||
20 | 153 | 4.6 | 810 | 10.5 | 230 | 1.2 | ||||
25 | 163 | 4.6 | 410 | Start from the edge | ||||||
32 | 170 | 5.1 | 250 |
Low-carbon steel oxygen plasma/air protection cutting current 130A.
Select gas | Set cutting airflow | Material thickness | Arc voltage | Distance from cutting torch to workpiece | Cutting speed | Initial piercing height | Piercing delay | |||
Plasma | Protective gas | Plasma | Protective gas | mm | Voltage | mm | mm/min | mm | Coefficient% | Second |
Oxygen | Air | 65 | 48 | 3 | 128 | 2.5 | 6500 | 5.0 | 200 | 0.1 |
4 | 129 | 2.8 | 5420 | 5.6 | 200 | 0.2 | ||||
6 | 130 | 2.8 | 4000 | 5.6 | 200 | 0.3 | ||||
10 | 134 | 3.0 | 2650 | 6.0 | 200 | 0.3 | ||||
12 | 136 | 3.0 | 2200 | 6.0 | 200 | 0.5 | ||||
15 | 141 | 3.8 | 1650 | 7.6 | 200 | 0.7 | ||||
43 | 20 | 142 | 3.8 | 1130 | 7.6 | 200 | 1.0 | |||
25 | 152 | 4.0 | 675 | 8.0 | 200 | 1.5 | ||||
32 | 155 | 4.5 | 480 | Start from the edge | ||||||
38 | 160 | 4.5 | 305 |