In industries such as shipbuilding and aircraft manufacturing, the production of large metal components often requires the utilization of a tandem bending machine – two bending machines operating simultaneously to handle sizable workpieces. This necessitates the integration of a CNC system to coordinate the control of both bending machines, a feature currently exclusive to expensive electro-hydraulic synchronous bending machines and their corresponding CNC systems. If twist-axis bending machines were employed, it could further reduce costs, potentially saving up to RMB 200,000 for each set of tandem bending machines linked to a bending machine.
Table of Contents
Features of Tandem Bending Machine
- Typically, two sets of the same series and specifications of the main machine are employed, equipped with a tandem bending machine linkage synchronization device.
- A fully steel plate welded structure is chosen, undergoing vibration stress relief, ensuring high strength and excellent machine rigidity.
- The hydraulic system is sourced from a specialized hydraulic system in the United States – simple, compact, stable, reliable, and durable.
- The synchronization mechanism utilizes machine-hydraulic servo and mechanical blocking, connected to the slider with a joint bearing. This ensures high synchronization and the capability to handle a certain bias load, preventing damage to the synchronization mechanism and maintaining workpiece precision despite any bias load.
- The slider stroke organization employs motorized adjustment with an LED digital display, ensuring accuracy of 0.01mm for a high-precision forming point on the board.
- The backstop distance is adjusted using a motorized mechanism with manual fine-tuning via an LED digital display, achieving high accuracy of 0.01mm. This eliminates gear gaps common in general digital displays, ensuring high precision.
- The slider stroke adjustment organization is an independent motorized system, replacing the previous cylinder internal adjustment type. This provides high positioning accuracy, convenient repair, and eliminates issues such as oil leakage and jamming resulting from slider stroke adjustment exceeding limits.
- The upper die is equipped with deflection compensation organization and an optional fast clamping mechanism. For 250 tons or more, lower die deflection compensation equipment is provided, with optional inclined block compensation or cylinder compensation.
- This machine represents the latest equipment, belonging to the third generation of bending machines. The two machines can also be used separately simultaneously, enhancing production efficiency. They offer high positioning accuracy, ease of repair, and an aesthetically pleasing appearance.
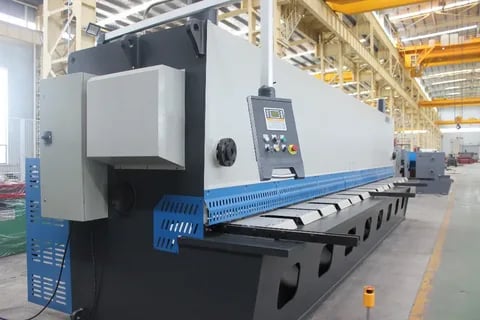
Structure Design
A type of bending machine is designed to process large metal parts by utilizing two bending machines working in parallel. This allows for the simultaneous bending of a workpiece, improving productivity and maintaining high precision. The structural design encompasses several key components and features to achieve optimal performance.
Main Components
- Frame: The frame serves as the primary structural support for the tandem bending machine. It is typically made of high-strength materials, providing stability and rigidity to the entire system.
- Slider: The slider, or ram, is a moving component that carries the upper die and is responsible for the up-and-down movement during the bending process.
- Upper Die: The upper die is a tooling component that shapes the workpiece during the bending operation. It is attached to the slider and can be designed with various profiles to accommodate different bending requirements.
- Table: The table is the work surface where the metal sheet or workpiece is positioned for bending. It is typically fixed and provides support for the lower die.
Hydraulic Drive System
- The hydraulic drive system is a critical component responsible for powering the movement of the slider and, consequently, the bending of the workpiece.
- Oil Tank: The oil tank holds the hydraulic fluid required for the system's operation.
- Oil Chestnut: This component is part of the hydraulic system and facilitates the flow of hydraulic fluid.
- Solenoid Pressure Valve: The solenoid pressure valve controls the flow of hydraulic fluid, regulating the pressure in the system.
- Proportional Flow Valve: The proportional flow valve helps adjust the speed and flow of hydraulic fluid, providing precise control over the bending process.
- Oil Cylinder: The oil cylinder is a key hydraulic component responsible for generating the force needed to move the slider.
Synchronization Mechanism
- The synchronization mechanism ensures that both bending machines operate in tandem, maintaining uniformity in the bending process.
- Machine-Hydraulic Servo: This component, along with mechanical blocking, is part of the synchronization mechanism. It is responsible for coordinating the movement of the sliders.
- Joint Bearing: Connected to the slider, the joint bearing helps maintain high synchronization and can handle certain bias loads.
Slider Stroke Adjustment
- The slider stroke adjustment mechanism allows for precise control of the slider's movement, contributing to the accuracy of the bending process.
- Motorized Adjustment: An electric motorized system is employed for adjusting the slider's stroke, ensuring fine control over the bending operation.
- LED Digital Display: An LED digital display provides accurate feedback on the slider's position, with high precision (e.g., 0.01mm).
Backstop and Die Compensation
- These features enhance the versatility and precision of the press brake.
- Motorized Backstop: An electrically adjustable backstop ensures precise positioning of the workpiece.
- Die Compensation: The upper die may be equipped with deflection compensation and fast clamping mechanisms to accommodate different bending requirements.
Structure Material
- The entire machine structure is commonly constructed using a full steel plate welded structure. This design provides strength, rigidity, and durability to withstand the stresses of the bending process.
Latest Generation Features
- Tandem bending machines may incorporate the latest technological advancements, making them part of the third generation of bending machines.
- Dual Usage: The ability to use the two machines separately, simultaneously improving production efficiency.
- Aesthetic Design: Attention to the overall aesthetics of the machine, contributing to a modern and visually pleasing appearance.
Structure Diagram
- The structure design is often represented in a schematic diagram, illustrating the arrangement of components, such as the tandem setup of two bending machines, the positions of the slider, upper die, and table, as well as the synchronization mechanisms.
The key challenge in achieving dual-machine linkage is adjusting the bending machine speed synchronization of the two bending machines to bend a workpiece simultaneously, thereby fulfilling the goal of processing large workpieces. Presently, the downward pressure speed of the twist-axis bending machine is non-adjustable, hindering the realization of dual-machine linkage operation with the twist-axis bending machine. This limitation stems from the structure and function of the twist-axis bending machine and its CNC system. The application of two twist-axis bending machines for tandem tandem bending machine linkage poses technical difficulties, resulting in a lack of demand in the market from bending machine manufacturers and users for twist-axis bending machines in tandem bending machine linkage operations.
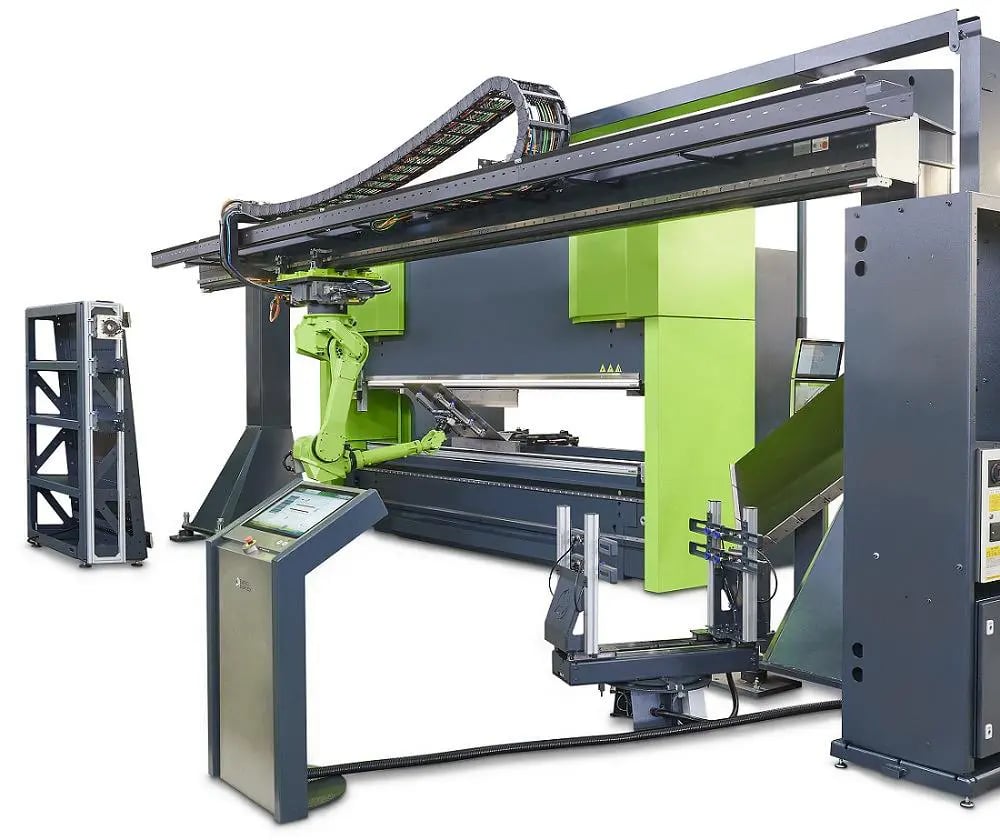
Technical Solutions & Principle
Tandem Bending Machine Linkage System Overview
The tandem bending machine linkage system addresses the challenge of achieving the linkage of two bending machines for synchronous control. This innovation involves the integration of a hydraulic drive system, control system, detection device, and electric servo drive system.
Hydraulic Drive System Configuration
Each bending machine in the tandem setup includes a frame, slider, upper die, hydraulic drive system, and control system. The hydraulic drive system comprises essential components such as an oil tank, oil chestnut, solenoid pressure valve, proportional flow valve, and oil cylinder. The interaction of these components facilitates the controlled movement of the slider and, consequently, the upper die.
- The oil chestnut's oil outlet connects to the solenoid pressure valve's oil inlet.
- The pressure oil outlet of the solenoid pressure valve is linked to the proportional flow valve's oil inlet.
- The oil outlet of the proportional flow valve is connected to the oil cylinder.
Detection Device Integration
A crucial feature of the tandem bending machine is the inclusion of a detection device to measure the position and speed of the upper die under pressure. This device communicates with the control system, providing real-time feedback on the position of the upper die during the bending process.
Synchronization of Control Systems
The control systems of the two twisted-axis bending machines operate synchronously through synchronization signals. One control system functions as the host, sending control signals to ensure synchronous control of both machines.
Electric Servo Drive System
The electric servo drive system plays a pivotal role, consisting of a servo motor, a transmission device, and a gear-rack mechanism. This system enables precise control of the up and down movement of the slider, contributing to the overall synchronization of the bending machines.
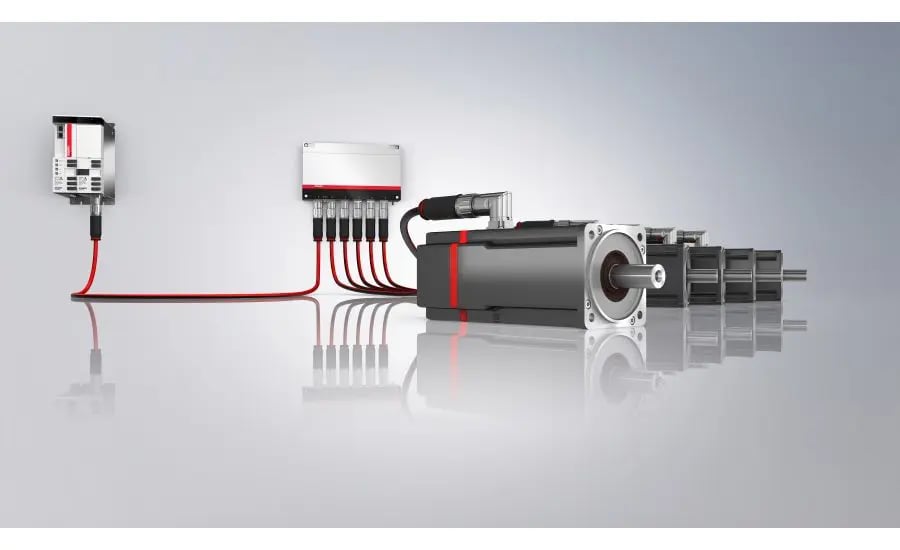
Operational Stages and Adjustments
- The proportional flow valve is fully open during the initial operation.
- As the upper die approaches the variable speed point, the proportional flow valve engages, allowing individual adjustments to the downward speed of the upper die by the control systems.
- The tandem bending machines synchronize the downward position and speed during the bending process.
- Operational stages include upper die fast-down and fast-up, each controlled by the servo motor based on commands from the control system.
Conclusion
The tandem bending machine linkage system achieves precise and synchronized control through innovative hydraulic and electric servo drive configurations, providing a solution for the effective tandem operation of two bending machines.