A press brake operator plays a crucial role in metal fabrication, and there are several key things they need to know to ensure efficient and accurate bending processes:
Table of Contents
Operator
At the forefront of the metal fabrication process are the press brake operators, whose effectiveness relies on comprehensive training and regular updates on utilizing the shop's brake equipment.
Operators must possess a keen awareness of the significance of the aforementioned factors and adeptly leverage these elements to achieve the highest accuracy in part production within the shortest timeframe. Their objective extends beyond merely producing quality parts; it includes minimizing setup time within the constraints of a specific press brake.
It is crucial for press brake operators to recognize that time spent on setup is time not dedicated to actual part production, underscoring the importance of reducing setup duration. The expertise of the operator stands as the primary means to achieve a streamlined setup process on a given machine.
Furthermore, operators should bear in mind the intrinsic connection between setup time and the overall production volume. This awareness allows them to incorporate setup time considerations into the calculation of time per part, thereby optimizing the efficiency of the entire manufacturing process.
In instances of short production runs, the emphasis is on minimizing setup time, especially when contrasted with longer runs involving intricate parts. Consequently, straightforward components that demand minimal setup time can and should be economically manufactured in small quantities. On the other hand, intricate parts with extended setup requirements are more economically viable when produced in larger quantities. The responsibility of determining the appropriate production approach lies with press brake operators, underscoring the necessity for their expertise in making informed decisions aligned with the nature of the fabrication task at hand.
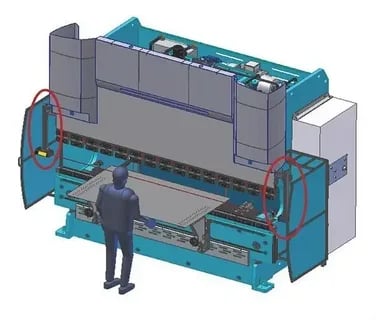
Press Brake
Matching Expertise With Machine
Many years ago shops had only two types of press brakes to choose from — mechanical and hydraulic. Since both of these required long setup times, it was practical to make many parts resulting in large inventories.
With the subsequent introduction of retrofitted CNCs and then full CNC press brakes, setup time was reduced greatly, and the expertise the operator needed changed. Setup and operation of a retrofit CNC or a full CNC brake require a different level of experience and knowledge than manual (non-CNC ) brake setup and operation.
Therefore, the type of brake available determines the required level of operator knowledge, as well as the outflow of formed parts. An operator with extensive experience on a non-CNC brake must be completely retrained for a CNC brake; operators must become intimately familiar with their machines and know those machines' physical limitations.
Limits
Every press brake has a concentrated load limit calculated in tons per inch in the center of the machine. Exceeding the tons-per-inch limit can damage the machine, the tooling, or the formed part.
For example, I once saw a shop apply the full tonnage of a 600-ton press brake over an 8-in. part in the center of the brake. Big no-no — using the machine in this fashion caused severe ram upset (permanent deformation) in the center of the ram.
To determine the tons per inch load limit, multiply the distance between the side frames by 60 percent, and divide the result into the machine tonnage. For example, if you have a 150-ton brake that and your machine has 10 feet between the side frames, multiply 120 inches by 60 percent; the result is 72 inches. Now divide 150 tons by 72 inches and you get a limit of 2.08 tons per inch for your machine. Therefore, you should not apply more than 25 tons to a 12 in. part.
It follows that the operator must estimate the tonnage required to form a part before making the first bend. Of course, this is critical only if the operator is bottom-bending or coining. You can't exceed the tonnage limit during air bending. Only during bottom bending or coining can the tonnage applied escalate to the rated tonnage of the machine.
Tonnage charts are available from all press brake manufacturers, and charts sometimes are mounted on the press brake itself. Keep in mind, however, that tonnage charts are for air bending only. To use the chart to estimate tonnage for bottoming or coining, simply multiply the air bend tonnage by 4 for bottoming and by 8 for coining.
Sometimes it is better to form a part off-center if your press brake can do this. Check with the manufacturer of your machine before attempting this, though. If a machine is not designed for off-center loading, you can damage it severely if you try it.
Maintenance
In addition, operators should know all of their machine's maintenance requirements. This includes periodic oil and filter changes (for hydraulic machines), regular lubrication, and proper machine level. Even if maintaining the machine isn't the operator's responsibility, he should at least be familiar with the procedures.
Tooling
The press brake operator should know and understand the terms air bending, bottom bending, and coining. Each type of bending requires different tooling, and while there can be some overlap, it just isn't practical to use the same set of tools for all types of bends.
Air bending is always the preferred method of bending, but the angle tolerance and the required inside radius sometimes make it necessary to bottom-bend or coin.
The formed inside radius in air bending is related to the die opening (0.156 multiplied by the die opening) or 1.25 times the material thickness. For bottom bending, the inside radius is approximately equal to the material thickness; for coining, the inside radius is equal to the radius of the punch. Angle tolerance of the part is determined by the accuracy of the machine and the accuracy of the tooling.
Operators must be familiar with all available tooling. In addition, they really should check tooling tolerances each time a punch and die is pulled from storage. It is the responsibility of the operator to make sure that the tooling always is within the manufacturer's specifications; if it is not, the tooling must be remachined or replaced. It is almost impossible to make good parts with bad tooling.
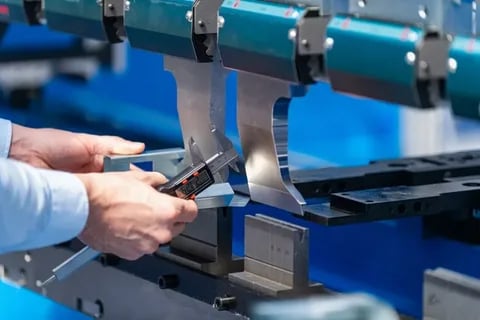
Drawings - Last But Not Least for Press Brake Operator
All pertinent information for making the part should be on the drawing.
This includes the dimensions of the part, bend angle, inside radius, and the blank size, complete with acceptable tolerances for each. The drawing should be based on the capability of the press brake and tooling that are available for the job. If any information is omitted from the drawing, an operator faces the problem of filling in the blanks. This takes time away from making parts and more often than not leads to a high percentage of scrap.
Operators need training in all aspects of a drawing's information and how this information is related to the tooling and the machine.
It is the knowledge and experience of press brake operators that help to guarantee part accuracy and economy; it is management's responsibility to provide the training necessary to give that expertise to the operators in the first place.