The press brake is a device that utilizes a mechanical device to bend metal sheets. It is usually used to produce metal sheets and components fabrication. This machine is paramount in metal sheet manufacturing and can be widely applied to automobiles, electronics, construction, and many other industries.
Table of Contents
The press brake performs the bending process efficiently and precisely, which can significantly improve production.
To put it simply, the bending process is to fix the metal material on the bottom die.
The upper punch decreases in high speed driven by hydraulic and motor, then presses the metal.
Machine control systems strictly control the pressing angle and force, achieving standard bending forming.
When the bending is finished, the upper punch rebounds automatically, and the processed metal parts can be removed.
In this passage, we will focus on the press brake air bending.
We will introduce the definition of air bending, its importance, process, and so on, to help readers better understand and apply this sheet metal fabrication method.
Understanding Press Brake Air Bending
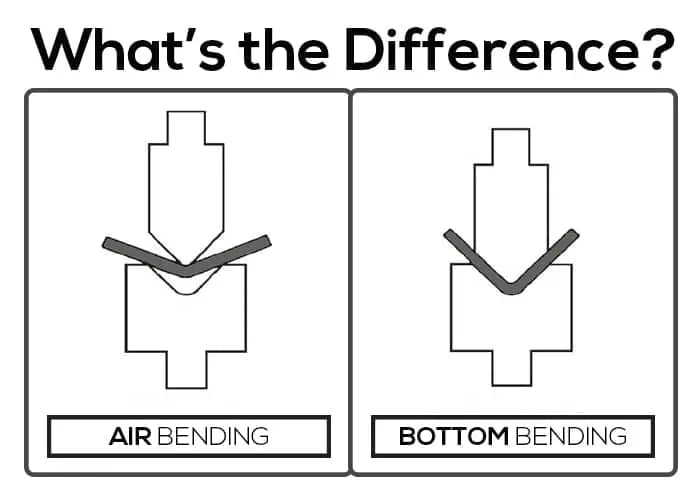
What is air bending?
Air bending is a relatively moderate bending-forming technology. The tool contacts the material only on three points (the tip of the punch, and edges of the die).
The upper die presses the metal sheet into the v groove in the bottom die until the predestinate depth without contacting the bottom die. It uses depth to define the bending angle.
Commonly, the same die can be adapted to different materials, bending radium, and bending angle based on the punch outline and depth.
As a press brake bending method, air bending is one of the most moderate and popular technologies because the CNC controller has eliminated the mass prediction in forming, such as rebound.
This method is fast used and has been regarded as the most common press brake forming technology in today's metal workshop owing to it significantly saving time for forming multiple angles and replacing the tools.
When to use air bending?
When a wide range of bending angles is required; when changing the angle required instead of changing the tool; when the operator needs to better control the bed radium; when using the CNC controller, the rebound can be adjusted automatically; when the operator wants to bend different types of components; when the rather small bending force is needed; when hoping fewer maintenance problems; when tool cost needed to be saved.
How does air bending work?
Air bending involves enough pressure on the material.
It gains the correct angle to generate the correct shape by pushing the die far enough.
Here is the process of air bending:
Die preparation
The top punch is usually narrow, and the bottom die is usually a V-shaped or U-shaped groove. Choosing the proper mold is determined by the metal sheet’s types, thickness, and required bending angle.
Placing the metal sheet
The metal sheet is placed on the v-shaped or u-shaped groove of the bottom die.
Apply the pressure
The top punch descends and presses the metal sheet to make it bend.
The top punch will not press the metal sheet to the bottom of the bottom die but stops in the middle. That is why called “air bending”---because there is an air interval between the material and the bottom die.
Forming the bend
Due to the upper die’s pressure, the metal sheet will form an arc through bending in the v-shaped or u-shaped groove of the bottom die. The bending angle will be determined by the upper die’s descending depth, the bottom die’s shape, and the metal sheet’s thickness.
Evaluate and adjust
The operator will evaluate the bending angle. If needed, the operator can change the bending angle through adjusting the upper die’s pressure and descending depth.
What’s the function of air bending?
Air bending is used to get the correct angle on the metal sheet during the process of press brake forming, and turns the metal into the required shape.
Although the air bending features many advantages, you should not use this on old and out-of-date press brakes because the margin of error will be much higher.
It is difficult to control the plunger depth, and the operator must calculate the material rebounding and ultimate punch depth by hand.
When performing the air bending on the press brake, the operator can control the bending radium, thus improving the precision and control force.
Advantages
No need to reprocess that different bending angles can be achieved, thus saving labor time and costs.
Able to bend most materials with different thicknesses.
Faster than bottom bending.
The required pressure is relatively small when operating the bending.
The contact with the die is fewer, and surface damage is less.
Disadvantages
The variation of material thickness and part abrasiveness between the top and bottom die may lead to unacceptable errors, not suitable for components that require high precision bending angles.
The variation of material properties also can affect the bending angle caused by rebounding.
The relatively old press brake equipment usually leads to inaccurate bending results.
Applications
Air bending is widely applied to various metal fabrication, especially for occasions that require high-speed, high-efficiency, and accurate bending. For example, the automotive, aerospace, and construction industries, always use this technology to generate various components and structures.
Other Bending Methods
Definition
Coining is one of the common use methods in metal fabrication.
The operator utilizes the press brake with the punch and dies to bend the metal to the required angle.
During this process, the sheet is placed on the top of the die horizontally. Then, the metal is compressed between the punch and die at extremely high tonnage. Thus, an accurate bending angle can be achieved.
The die forms various shapes and angles, like obtuse, acute, and right angles.
Whatever the bending angle is chosen, the metal sheet can be bent accurately to its angle.
Coining can achieve accurate and consistent bending every time.
Advantages
High custom: the press brake process allows manufacturers to create different coin designs according to their needs, including patterns, letters, and shapes.
Cost economy: compared with other methods, the cost is relatively low because it can use a common metal alloy.
Production efficiency: the press brake can produce large amounts of coins in a short time, which is beneficial to mass-scale production.
Disadvantages
Quality control: it will be a challenge for coining to control the quality because each coin must keep its quality, size, and texture consistent.
Restriction to metal: the coining process is mainly used for metal production, rather than other materials.
Professional knowledge required: operating the press brake requires specific technology and knowledge, thus experienced operators are needed.
Applications
Coin production: the obvious application is coin production. The coining is used to make various denominations circulate in the economy.
Souvenir production: coins are not just currency, but also an ideal choice for souvenirs. The process is used to produce meaningful coins, such as commemorative events or commemorative items.
Medals and badge production: coining is also used for making badges, and medals, to recognize outstanding achievements of individuals or groups in various fields.
Bottom Bending
Definition
Bottom bending is a press brake technique. The metal sheet can be formed at the required angle at the v-shaped groove of the bottom die under the die pressure.
Compared with air bending, bottom bending needs more tonnage to achieve high accuracy and fewer rebounds.
It is suitable for higher-precision programs. What’s more, it can reduce the impact of material stress on bending results.
Bottom bending needs different tools to achieve different radium bending results.
In bottom bending, the punch and die will never directly come into contact with metal sheets. An arc may occur that easily rebounds back to its interior original shape.
Once the metal sheet is released, it will go back a little to get to the required bending angle.
Different materials and thicknesses react differently to rebound when bent, thus the operator must know well about the distinctive properties of each metal.
Some manufacturers do not recommend the bottom bending owing to its risk existence.
Advantages
Shape versatility: bottom bending allows for metal components with different shapes and structures production, thus satisfying diverse needs.
High precision: the bottom bending is usually very precise, which can produce high-quality, precise metal components.
Extensive application: this process applies to various types of metals, including steel, aluminum, and copper.
Disadvantages
Requirements for equipment and technique: the bottom bending needs special equipment and technique, thus a skilled operator is needed.
High cost: the bottom bending requires a higher investment cost, not suitable for small-scale production.
Restriction: for metal components with specific shapes and structures, the bottom bending is not the best choice.
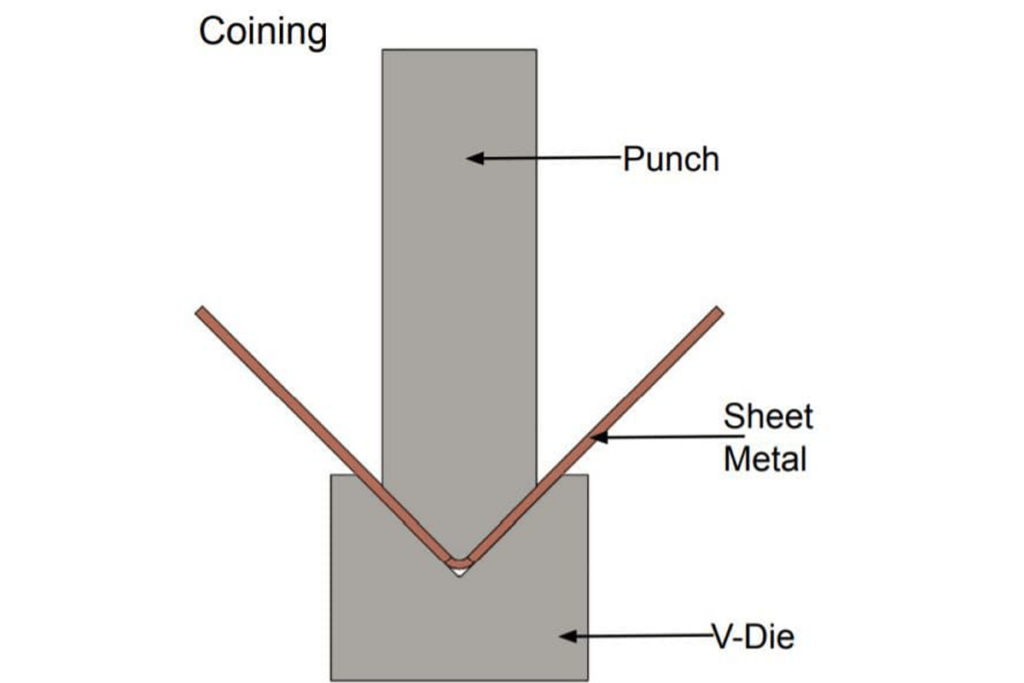
Material Considerations
Materials suitable for air-bending
Air bending is suitable for low-strength metals such as aluminum alloys and stainless steel. Aluminum is the ideal choice for air bending due to its light and plasticity. Stainless steel can be also processed effectively although it is harder than aluminum. Carbon steel is also suitable for air bending at appropriate thickness and solidness.
Material properties affecting the bending process
such as bending strength, solidness, and plasticity. Low-strength, softer materials are easier to bend.
Precautions for materials prone to cracking
high-strength steel is easy to crack when bent. To prevent cracks, it is necessary to control the pressure force and arc, reserve edges, or use a secondary bending process. Owing to the bending force being small, air bending is mainly suitable for low-strength materials fabrication. As for high-strength or easy-to-crack material, the operator needs to adjust according to its property.
Technical Aspects
Bending spring back and compensation techniques
Air bending bends the material by squeezing the material between the punch and die without utterly contacting. This process may cause springback, that is the material will be recovered to its original shape after bending. To compensate for spring back, it is recommended to use overbending or adjusting angle techniques.
Bend allowance calculation
Bend allowance refers to the amount of material consumed physically during the bending process, the accurate bend allowance calculation is vital for determining the initial expanded model size. It takes the material’s thickness, bending radium, and bending angle into consideration to ensure the final bending components can match the required specifications.
Influence of material thickness and bending angle
Material thickness and bending angle play a paramount role in air bending. The thicker material needs larger force to bend, and also easy to get the spring back. The bending angle also affects the amount the material deformation, further affecting the final shape of bending components. It is necessary to choose the proper tools and parameters to achieve anticipated results based on these factors.
FAQs
What is the minimum bend radius for a press brake?
The minimum bending radium on the press brake is determined by the used material and bending angle.
When using air bending, the interior bending radium is about 16% of the v-shaped die opening mouth.
Thus, when 1 1-inch v-shaped die is used, the interior bending radium is about 0.16 inch.
This digital is only for reference, the actual minimum bending radium is determined by the used material and bending angles.
What type of press is used for air bending?
The press brake suitable for the air bending process is usually a hydraulic press brake or electric press brake.
These two types of press brakes can exert appropriate pressure on the metal sheet to bend the material into the required shape.
Air bending is achieved by air pressure exerted on the metal sheet.
The hydraulic press brake utilizes the hydraulic system to control the pressure and bending angle, while the electric press brake uses an electric-driven system.
These press brakes are used to generate metal components and structures because they can offer precise control and high-quality bending.
Conclusion
After delving into the topic “press brake air bending”, we know the
importance of air bending in the industry manufacturing and its wide applications.
It can not only balance efficiency and precision but also meet the requirements for adapting various materials and thick metals.
However, to fully implement this technique’s potential, choosing a supplier with professional technology and skills is of vital importance.