Hydraulic shears, like any other equipment, can experience various issues that may affect their performance and efficiency. Here are some common issues related to hydraulic shears:
Table of Contents
Hydraulic Shears Adjusts the Back Length:
For the length adjustment of the Hydrulic Shears, the specific operating steps are as follows:
- First, you need to remove the blade and clean it. Because the blade can be used on four sides, you need to choose a better side for installation. Also, check the blade for horizontal and vertical straightness.
- The lower blade can be adjusted, but the key to adjustment lies in the upper blade. The upper blade is usually fixed, so we need to adjust the blade gap of the hydrulic shears by adjusting the lower blade.
- In order to adjust the fixed length of the trigger, we need to find the two screws on the left and right of the lower blade that widen the gap, and the set screws that push the lower blade to narrow the gap. These screws are usually located on the inside, while the upper blade's locking backup nut is on the outside.
- Loosen the four left and right bolts on the lower blade table, and then manually turn the upper blade to the appropriate shearing height. The operator starts the adjustment in the blanking area of the shearing machine.
- Use a feeler gauge to make a rough adjustment to 0.5 mm starting from the unengaged parts of the upper and lower blades of your left hand. Then, manually turn the blade up to the middle position and continue coarse adjustment to 0.5 mm. Finally, manually turn the blade up to the position where the upper and lower blades are not disengaged on the right side, and also adjust it roughly to 0.5 mm.
- After the above steps, we can get a preliminary cutting size. Next, we need to make precise adjustments to this size. This can be achieved by repeating the process of steps 5 and 6.
It should be noted that when adjusting the length of the shearing machine, the factors of the tool and steel plate material should be taken into consideration, and adjustments should be made on a reasonable basis. Once adjustments are completed, settings should be saved to avoid confusion when adjusting again.
How to Adjust the Parameters of CNC Shearing Machine
Enter the CNC hydraulic shears interface:
Press the "Open/Close" button on the CNC shearing machine panel to enter the operation interface.
Enter the counting setting interface:
Select "Counting Settings" in the operation interface.
Adjust the count value:
Check the current count value in the count setting interface.
Use the "Up/Down" buttons to increase or decrease the count value.
After the adjustment is completed, press the "OK" button to save the new value.
Verify the count value:
When cutting metal materials, check that the count value on the display has updated and is as expected.
In addition, there are other parameters of the CNC shearing machine that can be adjusted, including:
Tension setting: Adjust the tension according to the thickness and hardness of the material to ensure shearing accuracy and effect.
Cutting angle setting: Set different cutting angles according to needs to obtain different cutting effects.
Knife edge gap setting: Reasonably adjust the knife edge gap to improve cutting quality.
Backcut settings: Adjust backcut depth and angle based on material properties.
Bedding Settings: Add appropriate bedding to protect the cutting edge and material during cutting.
Cutting length setting: Set the cutting length according to specific needs.
Automation settings: Set up the degree of automation on your CNC hydraulic shearing machine to improve efficiency and shear quality.
Please note that the specific adjustment methods and precautions may vary depending on the device model and usage environment. It is recommended to consult the device manual or make adjustments under the guidance of professionals.
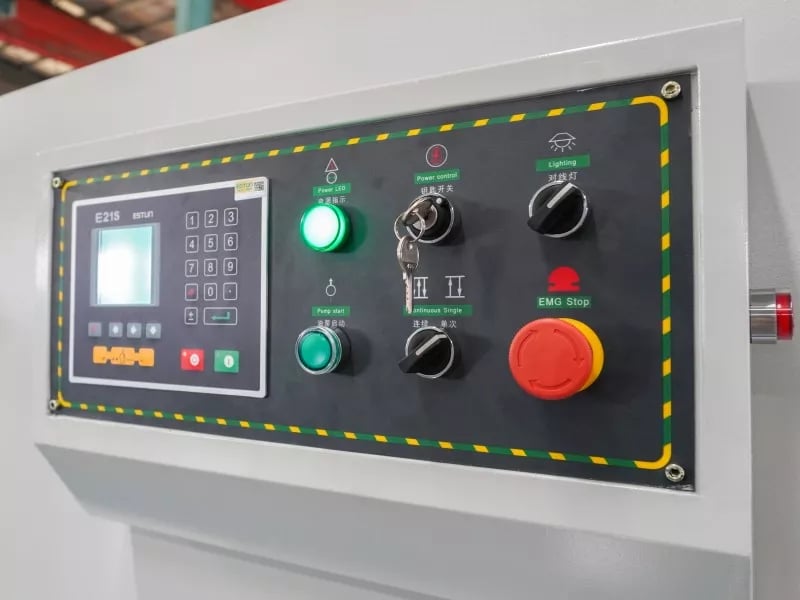
How to Adjust the Shearing Size Deviation of the Hydraulic Shears
- The back baffle and the lower knife are not parallel.
- The actual value is inconsistent with the programmed value and needs to be compensated or corrected on the system.
- Caused by changes in the straightness of the backsplash: there are deviations in the cutting size at different locations on the workbench.
- Caused by the non-perpendicular positioning of the side positioning and the lower knife: the shear knife cannot cut the steel plate vertically.
If the size of the shearing machine is not allowed, try the following solutions:
- Adjust the parallelism between the rear baffle and the lower knife.
- Compensate or correct the X-axis reference point on the operation interface.
- Adjust the straightness of the rear fender, but be careful, make sure to confirm it repeatedly, and only experienced people can adjust it.
- Correct the perpendicularity between the side positioning and the tailgate.
By addressing these common issues proactively and implementing preventive maintenance measures, you can ensure the optimal performance and longevity of your hydraulic shearing machine.