What is A Plate Rolling Machine
A plate rolling machine, also known as a plate roller or sheet metal roller, is a mechanical device used in metal fabrication to bend flat metal sheets or plates into curved or cylindrical shapes. It utilizes a series of rollers to gradually deform the metal sheet, allowing it to conform to the desired curvature without causing damage or distortion.
Plate rolling machines come in various types and sizes, each suited for different applications and materials. They can be manual, hydraulic, or CNC-controlled, with varying capacities and capabilities. These machines are widely used in industries such as construction, automotive, aerospace, shipbuilding, and metalworking for forming curved components used in structures, machinery, and equipment.
Key components of a plate rolling machine include rollers, frame, hydraulic system (in hydraulic models), control panel, and safety features. Modern plate rollers often feature digital controls and advanced hydraulic systems for precise bending operations with tight tolerances.
Plate rolling machines offer several advantages, including versatility in bending various metal materials such as steel, aluminum, and stainless steel, precision in forming complex shapes, efficiency in high-volume production, and cost-effectiveness by reducing manual labor and material waste.
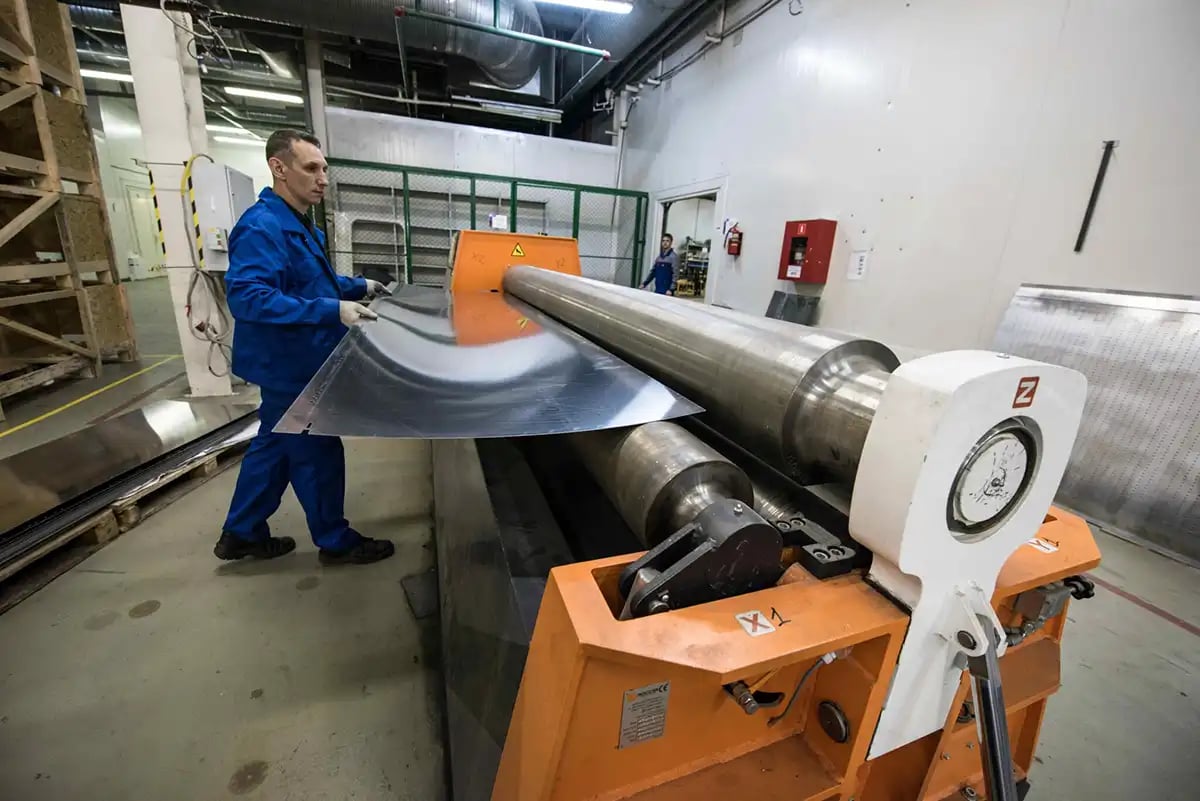
Varieties:
The main varieties of plate rolling machines include:
Three-Roll Plate Rollers:
Three-roll plate rollers have three rollers arranged in a triangular configuration, with two bottom rollers providing the primary bending force and a top roller providing additional support.
These machines are often used for simple bending operations and can accommodate a wide range of sheet thicknesses and widths.
Three-roll plate rollers are relatively easy to operate and are suitable for small to medium-sized fabrication shops.
Four-Roll Plate Rollers:
Four-roll plate rollers have four rollers arranged in a pyramid or quadrilateral configuration, offering greater bending precision and the ability to pre-bend both ends of the plate.
These machines provide more control over the bending process and are ideal for applications requiring high accuracy and repeatability.
Four-roll plate rollers are commonly used in large-scale fabrication facilities, aerospace industries, and shipbuilding yards.
Variable Geometry Plate Rollers:
Variable geometry plate rollers feature adjustable roller arrangements, allowing for complex bending operations and the production of a wide range of curved shapes.
These advanced machines offer maximum flexibility and versatility, making them suitable for custom fabrication projects and specialized applications.
Variable geometry plate rollers are often equipped with CNC controls and advanced automation features for precise and efficient bending operations.
Pyramid Type Plate Rollers:
Pyramid type plate rollers have three or more rollers arranged in a pyramid configuration, with the top roller serving as the driving roller and the bottom rollers providing support.
These machines are capable of bending thicker and heavier plates than traditional three-roll plate rollers, making them ideal for heavy-duty fabrication work.
Pyramid type plate rollers are commonly used in industries such as construction, shipbuilding, and heavy machinery manufacturing.
Section Bending Machine:
Section bending machines are specialized plate rollers designed for bending profiles and sections, such as angle iron, flat bars, and pipes.
These machines feature adjustable rollers and bending dies to accommodate different profile shapes and sizes.
Section bending machines are widely used in metalworking, construction, and architectural industries for bending structural components and architectural elements.
Components:
Plate rolling machines, also known as plate rollers or sheet metal rollers, consist of several key components that work together to bend flat metal sheets or plates into curved shapes. The main components of a plate rolling machine include:
Rollers: Rollers are the primary components responsible for bending the metal sheet. They can be arranged in different configurations depending on the type of plate roller. In a three-roll plate roller, there are two bottom rollers and one top roller, while a four-roll plate roller has additional side rollers for more precise bending.
Frame: The frame provides structural support for the machine and houses the rollers and other components. It is typically made of welded steel plates to ensure rigidity and stability during operation.
Hydraulic System: Many plate rolling machines utilize hydraulic systems to apply pressure to the rollers and control the bending process. The hydraulic system includes hydraulic cylinders, pumps, valves, and hoses that work together to generate the force needed to bend the metal sheet.
Control Panel: Modern plate rolling machines feature digital control panels for setting parameters such as bending angle, roller position, and feed rate. The control panel allows operators to program and monitor the bending process, ensuring precise and consistent results.
Safety Features: Plate rolling machines are equipped with various safety features to protect operators and prevent accidents during operation. These may include emergency stop buttons, safety guards, interlocks, and safety sensors that detect obstructions or malfunctions.
Drive System: The drive system provides power to the rollers and controls their movement during the bending process. It may consist of electric motors, gears, belts, or chains that transmit rotational motion to the rollers.
Alignment Devices: Plate rolling machines are equipped with alignment devices to ensure accurate positioning of the metal sheet during bending. These devices may include guides, fences, or laser pointers that help operators align the sheet with the rollers for precise bending.
Supports and Worktable: Plate rolling machines often include supports and worktables to hold the metal sheet in place during bending. These supports may be adjustable to accommodate different sheet sizes and thicknesses.
Working Principles:
The working principles of a plate rolling machine involve the gradual deformation of a flat metal sheet or plate into a curved or cylindrical shape through the application of bending force by a series of rollers. The process typically follows these general steps:
Preparation: The operator sets up the plate rolling machine by adjusting the roller positions, aligning the metal sheet, and selecting the appropriate bending parameters on the control panel.
Feeding the Metal Sheet: The flat metal sheet or plate to be bent is placed between the rollers of the plate rolling machine. The rollers may be adjusted to accommodate the width and thickness of the metal sheet.
Initial Bending: The operator starts the machine, and the rollers begin to rotate. The metal sheet is fed through the rollers, and the initial bending action starts to deform the sheet into a curved shape. In some cases, pre-bending or edge pre-forming may be performed to achieve the desired curvature.
Gradual Bending: As the metal sheet passes through the rollers, the bending force is applied uniformly across its width, gradually forming it into the desired curved shape. The operator may need to make adjustments to the roller positions or bending parameters during the process to ensure accurate and consistent bending.
Multiple Passes: Depending on the thickness and curvature of the metal sheet, the bending process may require multiple passes through the rollers. The operator may incrementally adjust the roller positions between passes to achieve the desired curvature gradually.
Final Inspection: Once the bending process is complete, the curved metal sheet is inspected for accuracy and quality. Any defects or imperfections may be corrected manually, or the bending process may be repeated if necessary.
Unloading the Curved Metal: Finally, the curved metal sheet is removed from the plate rolling machine, and the process is complete. The curved components may undergo additional finishing operations, such as welding, grinding, or polishing, before being used in their intended applications.
Benefits:
Plate rolling machines offer several advantages:
- Versatility: They can bend a wide range of metal materials, including steel, aluminum, stainless steel, and more.
- Precision: Modern plate rollers feature digital controls and advanced hydraulic systems, allowing for precise bending operations with tight tolerances.
- Efficiency: Plate rolling machines can bend large metal sheets quickly and efficiently, making them suitable for high-volume production.
- Cost-Effectiveness: By eliminating the need for manual bending and reducing material waste, plate rolling machines offer a cost-effective solution for curved metal fabrication.
- Flexibility: They can produce a variety of curved shapes and profiles, making them suitable for a wide range of applications in industries such as construction, automotive, aerospace, and shipbuilding.
In summary, plate rolling machines are essential tools in metal fabrication, offering versatility, precision, efficiency, and cost-effectiveness in producing curved metal components for various applications.