Table of Contents
What is Plate Bending Machine
A plate bending machine, also known as a plate roller or sheet metal roller, is a mechanical device used to bend or roll metal plates or sheets into curved or cylindrical shapes. It is commonly used in metalworking and fabrication processes to produce cylindrical or conical shapes for various applications in industries such as manufacturing, construction, automotive, and aerospace.
Plate bending machine typically consist of a set of rollers arranged in a specific configuration, such as three-roll or four-roll designs. The metal plate or sheet is fed between the rollers, and hydraulic or mechanical pressure is applied to bend the material into the desired shape. Plate rollers come in various sizes and configurations to accommodate different material thicknesses, widths, and bending requirements.
Plate bending machines are versatile machines capable of producing a wide range of curved shapes, including cylinders, cones, and arcs. They are commonly used to fabricate components such as pipes, tanks, cylinders, pressure vessels, and structural elements. Plate rollers play a crucial role in the metal fabrication industry, enabling the production of complex and precise curved metal components for various applications.
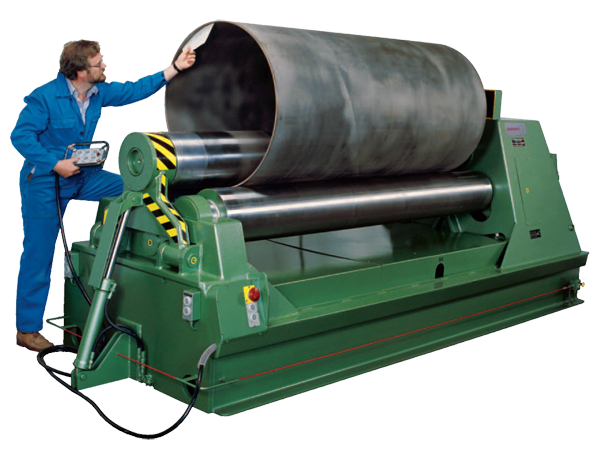
What is Plate Bending Machine Used For
Plate bending machines are widely used in various industries for a range of applications, including:
Manufacturing of Pressure Vessels: Plate bending machines are commonly used to form cylindrical or conical shells for pressure vessels used in industries such as oil and gas, chemical processing, and power generation.
Fabrication of Tanks and Silos: Plate rollers are used to bend metal plates into cylindrical or rectangular shapes to fabricate tanks, silos, storage bins, and other storage containers for liquids, gases, and bulk materials.
Production of Pipes and Tubing: Plate bending machines are employed to bend flat metal plates into curved or spiral shapes to manufacture pipes, tubing, and ductwork used in plumbing, HVAC systems, and industrial piping applications.
Construction of Structural Components: Plate rollers are used to form curved or arched structural components such as beams, columns, arches, and trusses used in building construction, bridges, and infrastructure projects.
Manufacturing of Industrial Equipment: Plate bending machines are utilized to fabricate curved or cylindrical components for various types of industrial equipment, including conveyor systems, material handling equipment, and machinery frames.
Production of Architectural Elements: Plate rollers are employed to create curved or bent metal components used in architectural applications, such as curved facades, canopies, railings, and decorative elements in buildings and structures.
Fabrication of Automotive Components: Plate bending machines are used in the automotive industry to produce curved or bent metal components for vehicle frames, chassis, body panels, exhaust systems, and other automotive parts.
Manufacture of Aerospace Components: Plate rollers are employed to form curved or contoured metal panels and skins used in the construction of aircraft fuselages, wings, tail sections, and other aerospace components.
Types of Plate Bending Machine
Three-Roll Plate Bending Machine:
Three-roll plate bending machines feature three rollers arranged in a triangular configuration, with two bottom rollers and one top roller. The top roller serves as the bending roller, while the bottom rollers provide support and drive the material through the machine. Three-roll machines are commonly used for simple bending operations and can handle a wide range of material thicknesses and widths.
Four-Roll Plate Bending Machine:
Four-roll plate bending machines have four rollers arranged in a pyramid or quadrilateral configuration. Two bottom rollers provide primary bending force, while two top rollers provide additional support and control. Four-roll machines offer greater bending precision and the ability to pre-bend both ends of the plate. They are ideal for applications requiring high accuracy and repeatability.
Pyramid Type Plate Roller:
Pyramid type plate rollers feature rolls arranged in a pyramid shape, with the top roll serving as the driving roller. These machines are capable of bending thicker and heavier plates than traditional three-roll plate rollers. They offer high bending force and are suitable for heavy-duty fabrication work.
Variable Geometry Plate Roller:
Variable geometry plate rollers feature adjustable roller arrangements, allowing for complex bending operations and the production of a wide range of curved shapes. These machines offer maximum flexibility and versatility, making them suitable for custom fabrication projects and specialized applications.
Section Bending Machine:
Section bending machines, also known as profile bending machines, are specialized plate rollers designed for bending profiles and sections such as angle iron, flat bars, and pipes. They feature adjustable rollers and bending dies to accommodate different profile shapes and sizes.
Horizontal Plate Roller:
Horizontal plate rollers have rolls positioned horizontally, and the material is fed horizontally through the machine. These machines are suitable for bending long and narrow plates or sheets.
Vertical Plate Roller:
Vertical plate rollers have rolls positioned vertically, and the material is fed vertically through the machine. These machines are ideal for bending shorter and wider plates or sheets and are commonly used in industries such as shipbuilding and construction.
Each type of plate bending machine has its advantages and is suitable for specific bending applications and material types. When choosing a plate bending machine, consider factors such as material thickness, width, curvature requirements, and production volume to select the most appropriate type for your needs.
Conclusion
Plate bending machines play a crucial role in the metal fabrication industry, enabling the production of complex and precise curved metal components for a wide range of applications across various industries.