Table of Contents
What is A CNC plasma cutting machine
A CNC plasma cutting machine is a type of industrial equipment used to cut various materials such as steel, aluminum, brass, and copper using a high-velocity jet of ionized gas, typically oxygen or nitrogen. The machine operates under the control of a computer program, which guides the cutting torch along a predetermined path to create precise cuts according to the desired design or pattern. CNC plasma cutting machines are widely used in metal fabrication, manufacturing, automotive, aerospace, and other industries due to their ability to produce accurate cuts quickly and efficiently.
Maintenance and Care for CNC Plasma Cutting Machine
The working environment of the CNC plasma cutting machine is relatively harsh, with significant metal dust.
Therefore, the Plasma Cutting Machine must be thoroughly cleaned and maintained, with designated personnel responsible for equipment lubrication, repair, and maintenance.
Safety operations:
A CNC cutting machine is a precision device, thus its operation must adhere to fixed roles (designated operator, machine, and post).
Only professionally trained operators should use the machine. It is not for non-professionals.
Before operation, ensure there are no external interferences. After everything is normal, place the cutting plate on the cutting platform. The plate should not exceed the cutting range (Note: Be careful when lifting).
Daily maintenance and care:
Each workday, the plasma cutting machine and guide rails should be cleaned of dirt to keep it clean. Turn off the air and power sources when leaving work, and release remaining air in the machine pipes.
If the machine will be left alone for a long time, shut off the power to prevent operation by non-professionals.
Ensure that the machine’s horizontal and vertical rails and rack surfaces have lubricating oil to keep them well-lubricated.
Weekly maintenance and care:
Every week, the machine should be thoroughly cleaned. Clean the horizontal and vertical rails, drive gears, and racks and add lubricating oil.
Check if the horizontal and vertical rail cleaners are working properly. If not, replace them in time.
Check all cutting torches for looseness, clean the garbage in the ignition gun mouth to keep the ignition normal.
If there is an automatic height adjustment device, check whether it is sensitive and whether the probe needs to be replaced.
Monthly and quarterly maintenance:
Check the main air inlet for debris, and check whether each valve and pressure gauge is working normally.
Check all air pipe joints for looseness and all pipe bands for damage. Tighten or replace if needed.
Check all transmission parts for looseness and check the meshing of gears and racks. Adjust if necessary.
Loosen the tensioning device and manually push the trolley. If there are any abnormal conditions, adjust or replace in time.
Check the clamp blocks, steel belts, and guide wheels for looseness. Adjust if needed.
Check the strong electric cabinet and operating platform, and whether any fastening screws are loose. Use a vacuum cleaner or blower to clean the dust inside the cabinet. Check if the wiring head is loose (for details, refer to the electrical instruction manual).
Check the performance of all buttons and selection switches. Replace damaged ones, and finally draw a comprehensive detection figure to check the accuracy of the machine.
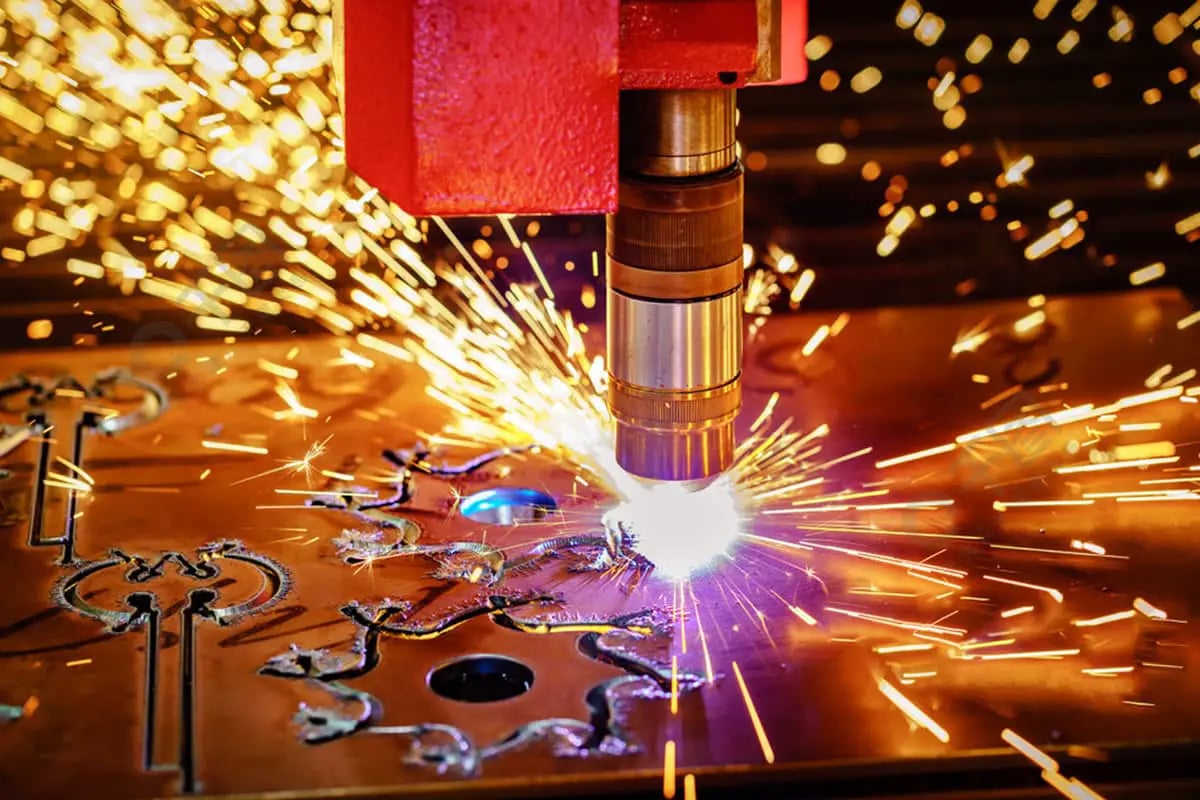
Maintenance of CNC Plasma Cutting MachineTorch
Assemble the torch correctly:
Assemble the torch of plasma cutting machine correctly and carefully, ensuring that all parts fit well and that gas and cooling air can circulate. Put all parts on a clean cloth to avoid dirt. Apply an appropriate amount of lubricant on the O-rings, just enough to make them shiny. Do not overapply.
Replace consumables in time:
Do not wait until consumables are completely worn out to replace them. Severely worn electrodes, nozzles, and swirl rings will produce uncontrollable plasma arcs, which can seriously damage the torch. Therefore, check the consumables as soon as you notice a decline in cutting quality.
Clean the torch’s connection threads:
When replacing consumables or during regular maintenance checks, ensure the internal and external threads of the torch are clean. Clean or repair connection threads as needed.
Clean the contact surface of the electrode and nozzle:
In many torches, the contact surface of the nozzle and electrode is electrified. If these surfaces are dirty, the torch will not work properly. Use a hydrogen peroxide-based cleaner for cleaning.
Daily check of gas and cooling air:
Check the flow and pressure of gas and cooling air daily. If insufficient flow or leaks are detected, stop the plasma cutting machine immediately to troubleshoot.
Avoid torch collision damage:
To avoid damage from torch collision, program correctly to avoid system overrun, installing anti-collision devices can effectively prevent damage from collisions.
Most common causes of torch damage:
Torch collision.
Destructive plasma arc caused by worn consumables.
Destructive plasma arc caused by dirt.
Destructive plasma arc caused by loose parts.
Precautions:
Don’t apply grease to the torch.
Don’t overuse O-ring lubricant.
Don’t spray anti-splatter chemicals while the protective cover is still on the torch.
Don’t use a manual torch as a hammer.
How to Extend the Lifespan of Consumables
Ensure the Correct Pressure and Flow of Plasma
The correct pressure and flow of plasma are critical to the lifespan of consumables. If the pressure is too high, the life of the electrode will be significantly reduced; if the pressure is too low, the life of the nozzle will be affected.
Use a Reasonable Cutting Distance
Adhere to the instructions in the manual and use a reasonable cutting distance — the distance between the cutting nozzle and the surface of the workpiece. When piercing, try to use twice the normal cut distance or the maximum height that can be transmitted by the plasma arc.
The Piercing Thickness Should be Within the Allowable Range of the Machine System
The plasma cutting machine cannot pierce steel plates that exceed the working thickness. The typical piercing thickness is half of the normal cutting thickness.
Don’t Overload The Nozzle
Overloading the nozzle (i.e., exceeding the working current of the nozzle) will damage the nozzle quickly. The current intensity should be set at 95% of the nozzle’s working current. For example, the current intensity for a 100A nozzle should be set at 95A.
Maintain Dry and Clean Plasma Gas
The plasma system requires dry and clean plasma gas to function correctly. Dirty gas, often a result of issues with the gas compression system, will shorten the life of consumables and cause abnormal damage. Test the quality of the gas by setting the torch in test mode and placing a mirror under it. If moisture or fog appears on the mirror, identify the cause and correct it.
Start Cutting from the Edge
Start cutting from the edge whenever possible instead of piercing. Using the edge as a starting point will extend the life of consumables. The correct method is to aim the nozzle directly at the edge of the workpiece and then start the plasma arc.
Avoid Prolonged Extension of the Plasma Arc
If the plasma arc can only reach the surface of the workpiece by extending, this extension will occur at the start and end of the cut, causing abnormal damage to the nozzle. By using the correct edge-starting technique and selecting the appropriate “arc-off” signal time, this issue can be avoided.
Reduce Unnecessary Arc-Starting Time
The nozzle and electrode wear out quickly during arc-starting. Before starting, place the torch within the travel distance of the cutting metal.
Apply Anti-Spatter Chemical Coating on the Protective Shell
Anti-spatter chemical coatings help reduce slag accumulation on the protective shell. However, only apply the coating after removing the protective shell from the torch.
Remove Slag from the Protective Shell
Regularly remove slag from the torch’s protective shell; otherwise, the slag will cause destructive double plasma arcs.
Purge Gas After Replacing Consumables
After replacing consumables or after a long shutdown, purge the gas (for 2-3 minutes) to ensure water and mist are expelled from the torch.
Keep the Torch and Consumables Clean
Any dirt on the torch and consumables will significantly impact the functionality of the plasma system. Place consumables on a clean cloth when replacing them, regularly check the torch’s connection threads, and clean the electrode contact surface and nozzle with peroxide-based cleaners.
Remove Oxides from Air or Oxygen Nozzles
When using air or oxygen plasma, oxides will accumulate inside the nozzle, affecting the gas flow and reducing the life of consumables. Wipe the inside of the nozzle with a clean cloth to remove oxides.
Use Softened Water in the Torch
Hard water can deposit metal impurities on the nozzle ring, affecting the gas flow, reducing the quality of the torch, and shortening the life of consumables.
Check Air Flow and Cooling Flow Daily
One of the most common causes of torch damage is insufficient cooling flow. Regularly check the airflow and pressure to the torch (if air-cooled) or the coolant (if water-cooled). If the airflow is insufficient or if there’s a leak, stop the CNC plasma cutting machine immediately and fix the issue.
By following these maintenance and care tips, you can ensure that your plasma cutting machine operates efficiently, reliably, and safely for years to come.