Table of Contents
In the world of metal fabrication, precision and efficiency are paramount. Whether you’re working with stainless steel, copper, or aluminium, the tools at your disposal must be up to the task. One tool that has risen to prominence for its precision and efficiency is the industrial laser cutter. Laser cutter machines offer significant advantages in the industrial sheet metal fabrication industry.
The Advantages of Laser Cutting
Laser cutters have earned their reputation as the leading technology in cutting systems for several compelling reasons. First and foremost, they are highly regarded for their energy efficiency, consuming less power, and requiring less maintenance compared to alternative cutting methods, resulting in a cost-effective choice.
Their high-speed cutting capabilities contribute to exceptional productivity, enabling more work to be completed in less time. Particularly noteworthy is their ability to deliver optimal cutting results, especially when working with reflective metals like brass, copper, aluminium, or stainless steel, unmatched in precision.
Laser cutting also minimises the chance of material warping, preserving the integrity of your workpieces. It is a clean process that significantly reduces contamination and the need for extensive clean-up.
How does an Industrial Laser Cutter work?
Industrial laser cutters work by focusing high-intensity laser beams, often CO2 or fibre lasers, onto materials. The laser source emits a concentrated beam, which passes through focusing optics to ensure precision. A computer numerical control (CNC) system directs the laser’s path based on a loaded design or pattern.
The laser rapidly heats, vaporises, or melts the material at the point of contact, resulting in clean and precise cuts. Assist gases, like nitrogen or oxygen, can be used to aid the cutting process, and an exhaust system removes by-products. Cooling systems dissipate the heat generated during operation, while operators monitor and adjust for quality control. The finished product boasts smooth edges with minimal post-processing. Industrial laser cutters find applications in diverse industries, delivering speed, precision, and versatility in manufacturing and design.
Why use an industrial laser cutter?
Industrial laser cutters are the epitome of precision and efficiency in the metal fabrication industry.Whether you’re in need of high-speed cutting, precision cuts, or a clean and efficient process, laser cutters have you covered.Here are some key reasons why industrial laser cutters are commonly used:
Precision: Industrial laser cutters offer high levels of precision and accuracy, allowing for the production of intricate shapes, fine details, and tight tolerances.
Versatility: Laser cutters can process a wide range of materials, including metals, plastics, wood, glass, ceramics, and composites. This versatility makes them suitable for diverse manufacturing applications.
Speed: Laser cutting is a fast and efficient process, enabling rapid production of parts and components compared to traditional cutting methods.
Automation: Many industrial laser cutting systems can be integrated with automation and robotics, allowing for continuous and unmanned operation, leading to increased productivity and efficiency.
Minimal Material Waste: Laser cutting produces narrow kerfs, resulting in minimal material waste and higher material utilization compared to traditional cutting methods.
Clean Edges: Laser cutting produces clean, smooth edges without burrs, dross, or other imperfections, reducing the need for secondary finishing processes.
Non-contact Cutting: Since the laser beam does not physically touch the material, there is minimal risk of damage or deformation to the workpiece, making it suitable for delicate or sensitive materials.
Flexibility: Laser cutting allows for quick and easy changes to design or production requirements, making it suitable for prototyping, customization, and small-batch production.
Cost-effectiveness: While the initial investment in an industrial laser cutter may be significant, the long-term cost savings from increased productivity, reduced material waste, and lower labor costs often outweigh the upfront expenses.
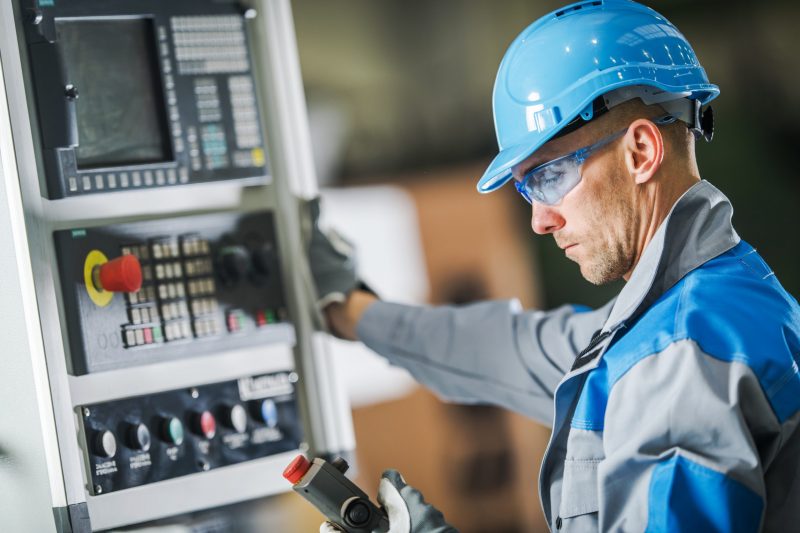
Do You Need Sheet Metal Machinery or a Laser Cutter?
Sheet metal professionals understand that using sheet metal machines safely and efficiently is crucial for workshops in China. That’s where KRRASS Machinery comes in. With 20 years of industry experience, KRRASS Machinery is a trusted partner for manufacturers in the sheet metal industry. Our team provides high-quality machinery maintenance, repairs and expert advice, ensuring that you can make informed decisions for your business.