Table of Contents
The speed of the return trip of the sliding block is slow, which will lead to the decrease of the production efficiency of the hydraulic press brake and affect the production efficiency of the enterprise. This paper analyzes the causes of the failure of the hydraulic press brake, makes a comprehensive diagnosis and eliminates the fault, which provides a new idea for the maintenance of the related faults in the future and has practical significance for improving the production efficiency of the enterprise.
Technical Parameters
The hydraulic sheet material bending model is wc67y-125t /3200 hydrauli press brake, the nominal pressure is 1250KN, the length of the table is 3200mm, the stroke of the slider is 120mm, the stroke speed of the slider is fast down/in/out is 36/9/45mm /s, and the maximum working pressure of the hydraulic system is 20MPa
Working Principle of Hydraulic Press brake
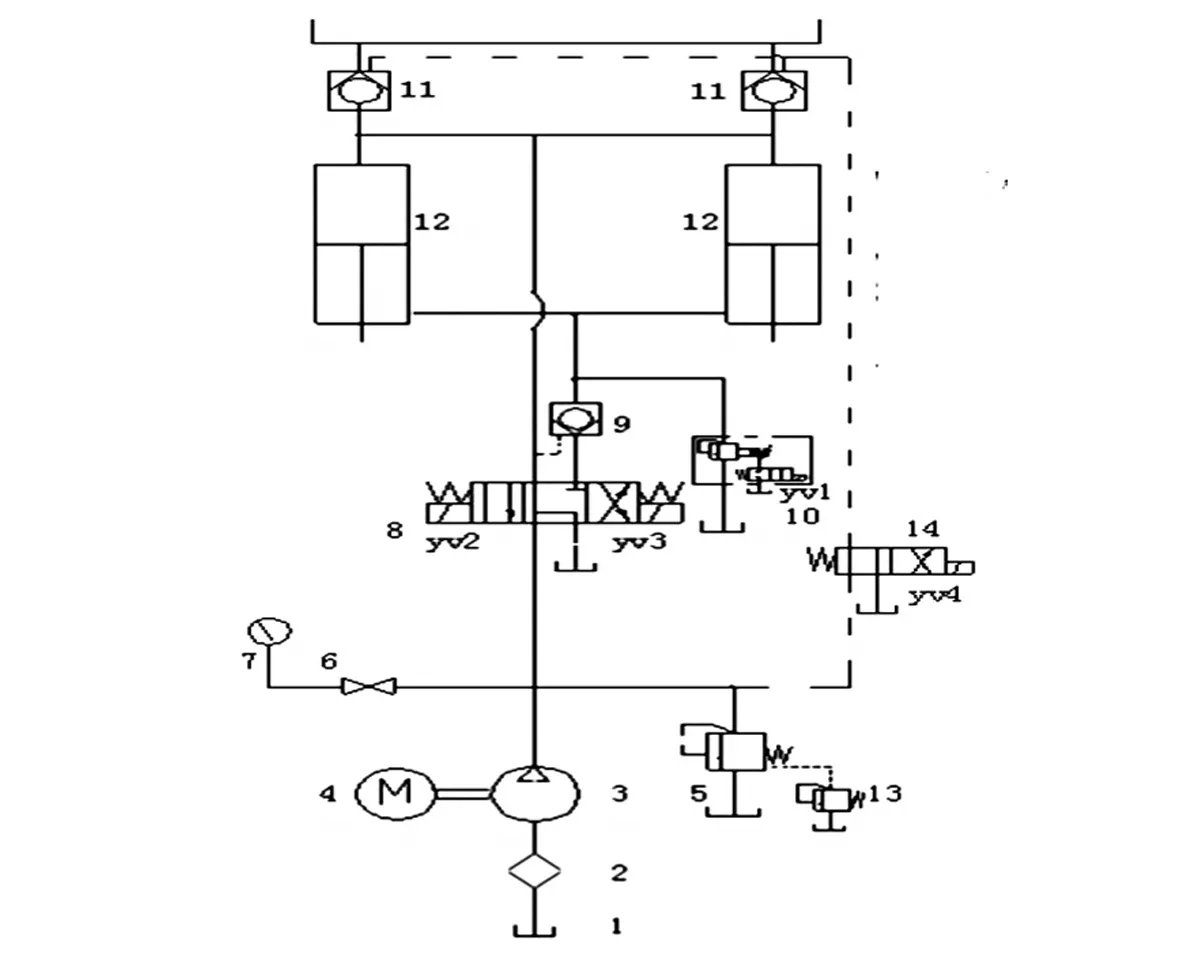
Through the cooperation of hydraulic transmission system and electrical control system, this hydraulic press brake can make the slider realize the working cycle of fast next slow next pressure maintenance, pressure relief and return journey, so as to meet the bending requirements of the workpiece.
1) Slide down quickly.
Solenoid reversing valve 8 YV2 electricity, electromagnetic overflow valve 10 YV1 electricity. Oil intake: the oil output from the oil pump 3, through valve 8 to the upper chamber of the two oil cylinders 12, pushes the piston rod of the two oil cylinders to drive the slider down. Control the oil in the oil circuit to open the liquid control one-way valve 9 and the liquid filling valve 11. In the descending process of the slider, valve 11 carries out high oil filling to realize the rapid descending of the slider. Oil return: the oil in the lower chamber of two oil cylinders is returned to the oil tank through the electromagnetic overflow valve for 10 times.
2) Slow down the slider.
Solenoid valve 8 YV2 power, two four-way valve 14 YV4 power. The oil; The oil output from the oil pump 3, through valve 8 to the upper chamber of the two oil cylinders 12, pushes the piston rod of the two oil cylinders to drive the slider down. Control the oil in the oil circuit to open the hydraulic control one-way valve 9. Oil return: the oil from the lower chamber of two oil cylinders 12 flows back to the oil tank through the liquid-controlled one-way valve 9 and the solenoid directional valve 8.
3) System voltage retention.
Controlled by the time relay KTI, the pressure holding of the slider can be carried out to achieve the shaping and bending of the workpiece. The pressure holding time can be adjusted.
4) System pressure relief.
In order to reduce the reverse impact on the return trip of the slider, Yv2 will lose power for a short time before the return trip of the slider. The system pressure relief is implemented first, and then the return trip of the slider. The pressure relief time can be adjusted.
5) Return trip of the slider.
Solenoid reversing valve 8 of YV3 power. Oil intake: the oil output from the oil pump 3, through the solenoid directional valve 8 and the hydraulic control one-way valve 9 until the lower chamber of the two cylinders 12 to push the two cylinders, the plug rod will drive the slider back.
At the same time, control the oil in the oil path through the two-position four-way reversing valve 14 to open the hydraulic control one-way valve 11, to prepare for the oil return from the upper chamber. Oil return: the oil in the upper chamber of the 12 cylinders is directly returned to the oil tank through the 11 hydraulic control one-way valve, so as to realize the rapid return of the slider.
6) Regulation of system working pressure.
According to the pressure required by the bending machine parts, it can be implemented by adjusting the knob of the remote pressure regulating valve 6. After the adjustment, the cap behind the knob should be locked and the high-pressure valve 5 should be adjusted before leaving the factory. The maximum working pressure of the system should not exceed 20MPa.
Failure Cause Analysis
Through the analysis of the working principle diagram and working process of the hydraulic system of this hydraulic press brake, the reasons for the slow return speed of the slider may be as follows :1) the hydraulic cylinder and the piston are not sealed strictly, resulting in mutual leakage between the upper and lower Chambers. 2) the electromagnetic overflow valve 10 is blocked and not closed strictly. 3) the hydraulic control one-way valve 9 is not in place. 4) plugging of the same core damping hole of 11 hydraulic control one-way valve leads to poor oil return. 5) the 8 reading core of the solenoid reversing valve is badly worn, resulting in the failure of the reversing.
Fault Diagnosis and Treatment Measures
1) Analyze the working status of the hydraulic press brake.
The sliding block is normal for pressing the sheet material down rapidly, and there is no leakage on the external surface of the hydraulic cylinder. Therefore, it can be excluded that the upper and lower cavities of the hydraulic cylinder are leaking into each other and the hydraulic control one-way valve 9 is not in place
2) Adjust the pressure of the electromagnetic overflow valve 10 when the pressure crossing cylinder makes a return trip, and the readings of the pressure gauge will change regularly accordingly, so that the performance of the electromagnetic overflow valve 10 is normal.
3) Check and verify the hydraulic control one-way valve 11.
There is no blockage in the damping hole of the valve core, and the valve 11 opens and closes in place with normal performance.
By checking, comparing and verifying the above conditions one by one, we can basically eliminate their influence on the fault, so we can preliminarily determine that the fault of the solenoid directional valve 8 is the cause of the slow return speed of the bending machine.
Through to overhaul of electromagnetic directional valve 8, found that electromagnetic directional valve valve core 8 surface wear serious, lead to sliding block electromagnetic directional valve 8 in the process of return YV3 electric.
Hydraulic oil need to the electromagnetic directional valve and hydraulic control one-way, and 9 to 8 cylinder 12 inferior vena push rod drives the sliding block on the way back, because the valve 8 tang with core loss is serious, directional control does not reach the designated position, push the slider a return of the hydraulic oil pressure is not enough, resulting in the return speed is slow.
Replace the solenoid directional valve 8, carry out the trial processing, the return trip speed becomes faster, and 1 works normally.
Conclusion
To sum up, in order to troubleshoot the hydraulic system, it is necessary to master the structure and working principle of the hydraulic system and related hydraulic components, have an in-depth understanding of the operation of each hydraulic press brake component during the relevant stroke work of the hydraulic equipment, and accurately troubleshoot the equipment by observing the equipment malfunction.