Table of Contents
Introduction:
Hydraulic bending machines are indispensable tools in metal fabrication, providing precision bending capabilities for a wide range of applications. However, like any mechanical equipment, they are susceptible to various faults that can disrupt operations. Understanding common issues and their solutions is essential for minimizing downtime and maximizing productivity.
Common Faults and Solutions of Hydraulic Bending Machine
Hydraulic Fluid Leakage:
Cause: Seal wear, hydraulic hose damage, or loose fittings can lead to hydraulic fluid leakage, compromising machine performance.
Solution: Regularly inspect hydraulic components, replace worn seals and hoses, and ensure proper tightening of fittings. Implement a preventive maintenance schedule to detect and address leaks promptly.
Inaccurate Bends:
Cause: Misalignment of tooling, worn dies, or hydraulic system malfunctions can result in inaccuracies in the bending process.
Solution: Conduct regular inspections to verify tool alignment and replace worn dies as needed. Calibrate hydraulic pressure settings to ensure consistent bending accuracy. Utilize precision measuring tools to verify bend angles and dimensions.
Hydraulic System Overheating:
Cause: Excessive friction, inadequate cooling, or fluid contamination can cause the hydraulic system to overheat, leading to reduced efficiency and potential component damage.
Solution: Check hydraulic fluid levels and quality regularly, ensuring proper filtration and cooling. Clean or replace clogged filters and coolers as needed. Reduce operating pressures or cycle times to mitigate heat buildup, and monitor temperature gauges during operation.
Slow Operation Speed:
Cause: Insufficient hydraulic pressure, worn components, or improper lubrication can cause the bending machine to operate at reduced speed.
Solution: Check hydraulic pump and valve settings to ensure adequate pressure for optimal performance. Lubricate moving parts regularly and replace worn components, such as seals or bearings, to improve efficiency. Consider upgrading to high-performance hydraulic fluids for enhanced lubrication and smoother operation.
Electrical System Malfunctions:
Cause: Wiring faults, motor issues, or control system failures can disrupt electrical functions, causing the bending machine to malfunction.
Solution: Inspect electrical connections for loose or damaged wires, and repair or replace as necessary. Test motors and control components for proper functionality, and recalibrate settings as needed. Implement regular electrical system maintenance and perform diagnostics using multimeters or oscilloscopes.
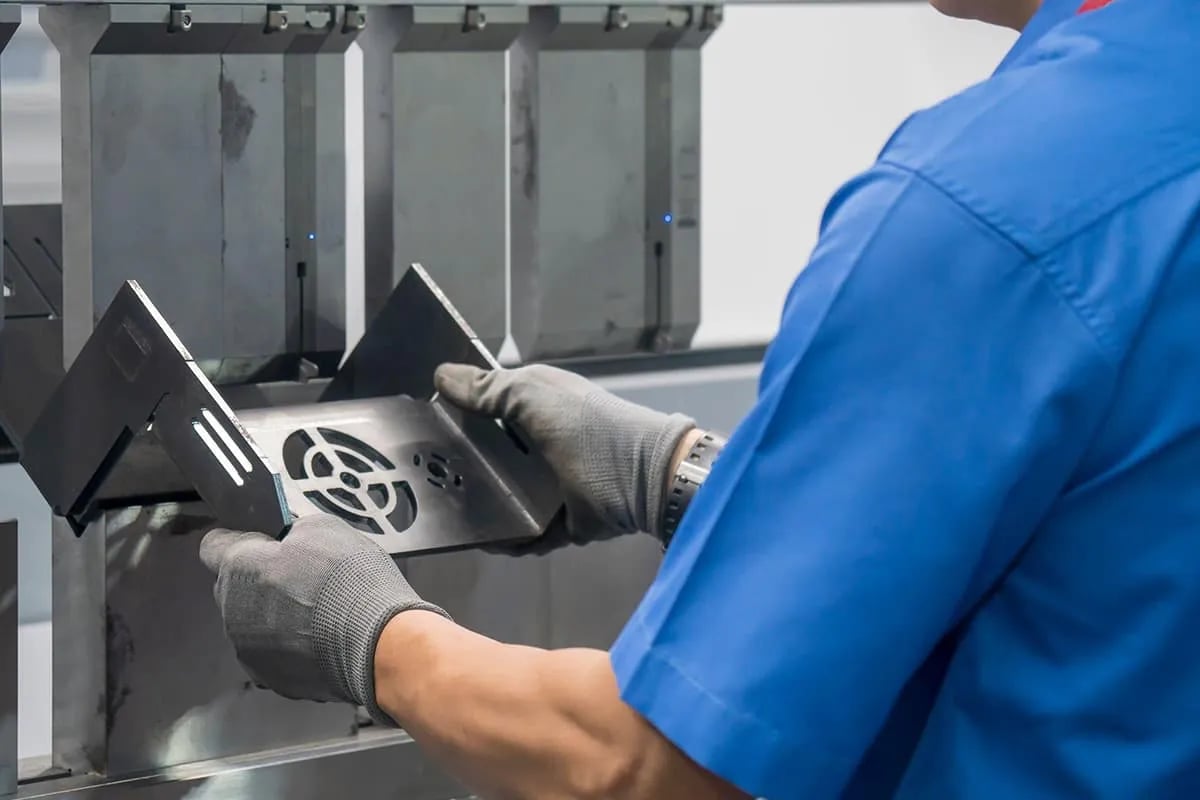
Conclusion:
Hydraulic bending machines play a critical role in metal fabrication processes, but they are susceptible to various faults that can impact performance and efficiency. By identifying common issues and implementing proactive maintenance practices, operators can minimize downtime, optimize bending accuracy, and extend the lifespan of their equipment. Prioritizing regular inspections, prompt repairs, and adherence to preventive maintenance schedules are essential for ensuring the reliable operation of hydraulic bending machines in industrial settings.