Since the plate rolling machine undergoes significant stress during operation, it is prone to several faults during use. In the following section, we will discuss two common faults and their respective solutions.
Fracture and repair of main shaft of plate rolling machine
A 50×3000 plate rolling machine in a machinery factory experienced cracks on its main shaft after one year of use. Upon conducting an ultrasonic flaw detection, it was discovered that the main shaft’s structure was divided into two parts: a forged section and a cast section, which did not meet the national standard for Class II flaw detection.
To determine the cause of the damage more precisely, maintenance personnel dissected the main shaft and found that the detection results were accurate. After their analysis, it was concluded that the primary reason for the main shaft’s fracture was poor welding. The welding area was small, the process was rough, and there were welding slag inclusions, leading to low strength defects.
1.1 Repair scheme.
Based on the stress conditions of the main shaft, we utilized a butt welding technique. To achieve this, two U-shaped grooves were made at the welding location, and a pit and a boss were respectively machined at the center of the broken shaft, with a tolerance fit of H7/H7.
To ensure the coaxiality of the welding, a V-shaped sizing block and an equal diameter ring were designed as part of the configuration.
1.2 Welding materials and methods.
During the inspection of the main shaft material using inspection equipment, it was discovered that it is made of No. 45 steel. However, this steel has poor welding performance, which creates numerous challenges during welding.
Additionally, due to the large diameter of the main shaft, pre-heating is necessary before welding. The welding machine used is the XC500 carbon dioxide gas-shielded welding machine. The welding wire used is ER50-6 with a diameter of 1.2mm.
During the welding process, the voltage is maintained at around 35V, the current ranges from 220-250A, and the speed is between 15-25 cm/min.
To ensure full penetration of the main shaft, the speed must be decreased during the initial welding phase, and the straight-line strip transportation method should be employed. As the width of the groove increases, the welding movement should be changed to a sawtooth form to minimize deformation.
Furthermore, the welding should be performed by two people simultaneously, alternating between an upward and downward rotation.
1.3 Welding.
Before welding, some pre-treatment steps must be taken.
Firstly, the main shaft must be disassembled and certain machining processes, such as pits and grooves, must be performed on the main shaft as specified in the drawings. The two broken shafts must also be tested for proper assembly.
To avoid the impact of welding slag on the assembly, the area near the weld must be cleaned with a slag remover to dispose of any waste slag generated during machining.
Next, the broken shafts are placed on the T20 boring machine and aligned using a V-shaped sizing block to adjust the horizontal height difference. The two shafts are then connected using a roller and checked for coaxiality using a cutter ruler. Fine adjustments are made using a thin copper sheet to ensure that the coaxiality error does not exceed 0.05mm.
Finally, angle irons are used to reinforce the four ends.
To reduce deformation of the main shaft during welding, the method of two people welding simultaneously is used. The roller installed on the main shaft is symmetrically welded in four positions, up, down, left, and right, with the welding length gradually increasing.
After each welding session, the welding slag must be removed promptly, and any welding stress must be relieved by tapping the weld.
To ensure coaxiality, welding should be stopped when it reaches 3/5 of the groove depth and the coaxiality deviation should be checked to determine the direction of the next bend. The spindle can be straightened by properly increasing the length of the welding arc and the current.
1.4 Effect.
Statistics indicate that after this spindle repair, there have been no cracks in the spindle for the past three years.
The entire welding repair process took four days and required 15kg of welding rod. The total cost of the repair, including machining and material expenses, was 5788 yuan.
If a new spindle were to be purchased, it would cost 220000 yuan and take 35 days for transportation and installation.
In comparison, spindle repair not only saves cost but also reduces the time required and increases efficiency.
Repair of motor failure of plate rolling machine
A Italy-made Em040-160 three-roll pressure plate bending machine suddenly stopped functioning during operation.
Upon inspection, the electrical signal was found to be normal, and it was initially determined to be a mechanical issue.
The maintenance worker first removed the motor from the tail of the upper roll and manually turned the input shaft of the upper roll reduction gearbox to confirm that the reduction gearbox was functioning properly.
Upon disassembling the motor, it was discovered that the movable cover plate on the end face of the oil distribution plate at the oil inlet side of the motor was broken, and the sealing ring under the cover plate had also been damaged. The debris from the damage had entered the plunger, causing oil to channel both inside and outside the oil distribution plate, preventing the generation of working pressure.
The hydraulic motor used in this bending machine is an imported Sai brand S7b3000or five-star radial piston motor. Purchasing new motor parts from the manufacturer would be time-consuming and expensive.
Therefore, the equipment maintenance department decided to repair the motor in-house, based on the production task and progress of the factory.
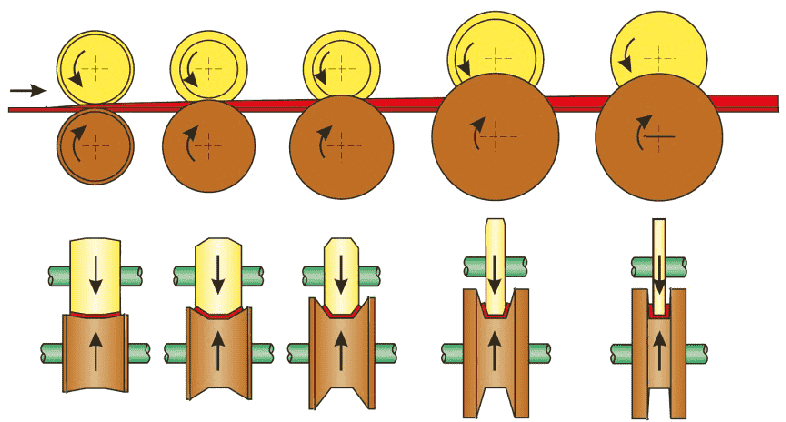
A new movable cover plate was machined to the size of the oil distribution plate, and a sealing ring was obtained from an oil seal agent. The original seals were an O-ring and a circular groove ring.
However, the agent only had O-rings and plane rings, while the original sizes were 2.5 and 1.9mm, and the available sizes were 2.5 and 1.4mm, which were not suitable for use.
As a solution, a 3mm retaining ring was used instead of the 1.9mm retaining ring. Since the oil distribution plate oil seal groove was 3.6mm deep and 3.2mm wide, the 3.0 O-ring had a slight gap in the groove for compression, and the 1.4 plane retaining ring could be securely placed in the groove.
The motor was assembled and the machine was reset, allowing the upper roll to rotate freely. After being in operation for one month, the motor was still functioning normally.