Table of Contents
CNC press brakes have transformed metal fabrication across various industries, providing unmatched precision, efficiency, and versatility in bending operations. Let's delve deeper into some successful application cases and the valuable lessons learned from CNC press brake usage in automotive manufacturing, aerospace, and construction sectors.
How CNC Press Brakes Transform Various Industries
Automotive Manufacturing
Within the automotive sector, CNC machines are indispensable for producing precision components crucial for vehicle assembly. From chassis components to intricate body panels, they empower manufacturers to bend and shape metal parts with exceptional accuracy and consistency.
An exemplary application case lies in the fabrication of vehicle frame components. CNC press brakes are employed to bend and form steel and aluminum sheets into complex geometries essential for frame structures. Leveraging the advanced programmable controls of machines, automotive manufacturers attain tight tolerances and high-quality finishes, ensuring both the structural integrity and aesthetic appeal of vehicle frames.
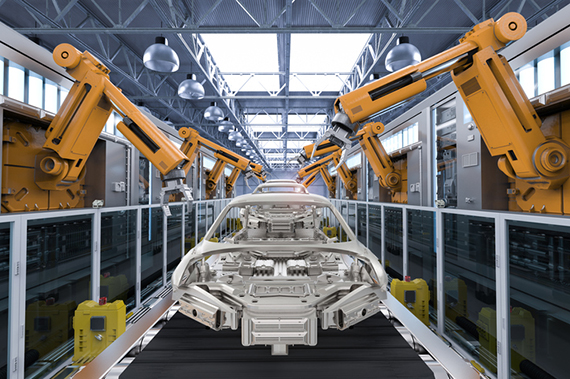
Lessons Learned:
Precision Tooling: Employing precision tooling and leveraging the advanced software features of CNC machies enable the achievement of intricate bends and contours required for automotive components.
Material Handling: Implementing efficient material handling systems streamlines workflow and minimizes downtime during production runs, optimizing overall efficiency.
Quality Assurance: Implementing rigorous quality control measures ensures that bent components meet stringent automotive industry standards for strength, durability, and dimensional accuracy, enhancing overall product quality and customer satisfaction.
Aerospace
In the aerospace industry, CNC technology play a pivotal role in fabricating aircraft components, including fuselage panels, wing structures, and landing gear components. The capability of CNC press brakes to bend and shape a wide range of materials, including aluminum, titanium, and composites, makes them indispensable in aerospace manufacturing.
A notable application case is in the production of aircraft fuselage sections. CNC press brakes are utilized to precisely bend aluminum and composite panels into complex shapes essential for fuselage construction. With precise control over bend angles and dimensions, aerospace manufacturers achieve optimal aerodynamic efficiency and structural integrity in aircraft design.
Lessons Learned:
Material Compatibility: Understanding the unique properties of aerospace materials and optimizing bending parameters accordingly is crucial to prevent material distortion or stress concentration, ensuring component quality and performance.
Compliance Standards: Adhering to stringent aerospace industry standards and regulations for component quality, traceability, and certification is imperative to ensure compliance and airworthiness.
Collaborative Design: Fostering collaboration between design engineers and manufacturing teams facilitates the optimization of component designs for manufacturability, cost-effectiveness, and performance, streamlining the production process.
Construction
In the construction sector, CNC press brakes are employed for fabricating structural components, architectural elements, and building facades. From steel beams to decorative cladding panels, CNC press brakes enable construction firms to achieve precise bends and profiles required for diverse construction projects.
A noteworthy application case is in the fabrication of architectural metalwork for commercial buildings. CNC press brakes are utilized to bend stainless steel, aluminum, and glass-reinforced concrete panels into custom shapes and profiles specified by architects and designers. By harnessing the versatility of CNC press brakes, construction firms enhance the visual appeal and structural integrity of building exteriors.
Lessons Learned:
Design Flexibility: Leveraging the design flexibility of CNC press brakes allows for the accommodation of custom architectural elements and intricate details in building facades, catering to unique project requirements and architectural visions.
On-Site Fabrication: Exploring portable CNC press brake solutions for on-site fabrication of structural components minimizes transportation costs and lead times, enhancing project efficiency and flexibility.
Surface Finish: Paying attention to surface finish requirements and implementing post-bending processes such as polishing or coating enhances the aesthetics and durability of architectural metalwork, ensuring long-lasting performance and visual appeal.
Conclusion
In conclusion, CNC press brakes are indispensable tools in metal fabrication, offering unparalleled precision, efficiency, and versatility across diverse industries. By sharing industry application cases and the valuable lessons learned, manufacturers and fabricators can harness the full potential of CNC press brakes to meet the evolving demands of modern manufacturing and construction sectors.