In the ever-evolving landscape of metal fabrication, CNC press brakes continue to play a pivotal role in shaping the industry. As technology advances and market demands evolve, it's crucial to explore the current trends and future prospects of CNC press brakes to stay ahead of the curve. Let's delve into the key trends shaping the industry and the promising outlook for CNC press brakes:
Advanced Automation
One of the most significant trends in CNC machines is the integration of advanced automation technologies. Manufacturers are increasingly adopting robotic systems and artificial intelligence (AI) for tasks such as tool changing, material handling, and part sorting. These automation solutions enhance productivity, reduce labor costs, and improve overall efficiency in metal fabrication processes.
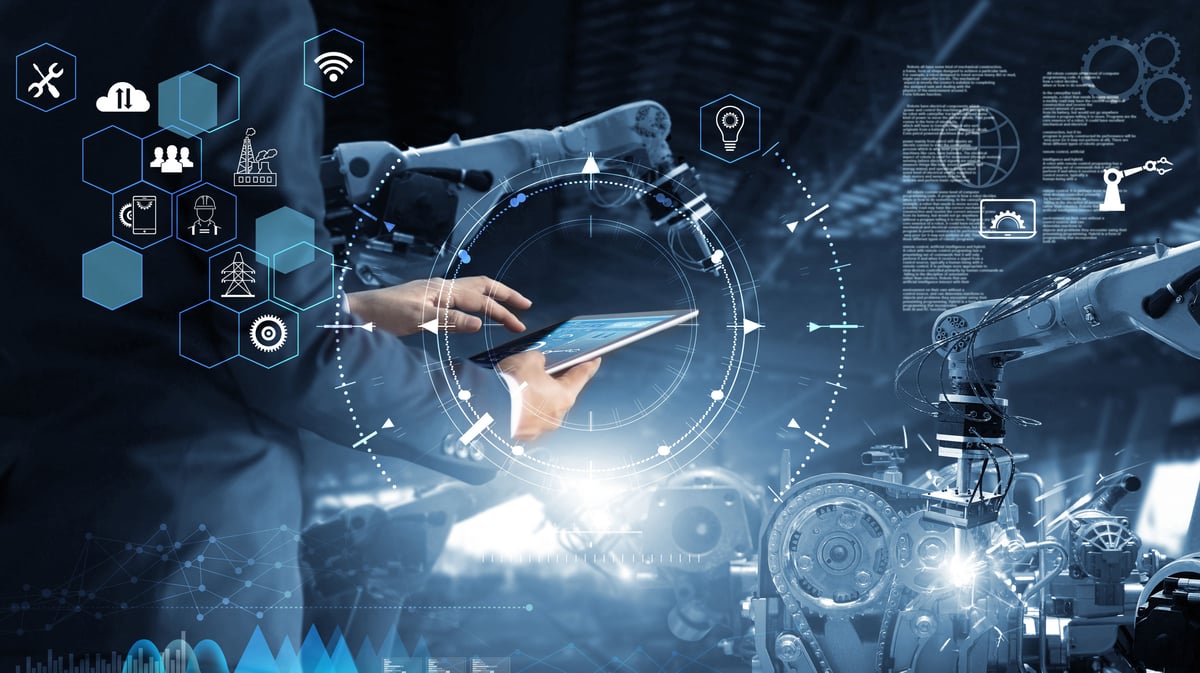
Digitalization and Connectivity
Digitalization is revolutionizing the way CNC machines operate and communicate within manufacturing ecosystems. With the advent of Industrial Internet of Things (IIoT) technologies, CNC press brakes are becoming more connected and data-driven. Real-time monitoring, predictive maintenance, and remote diagnostics enable proactive decision-making and optimize machine performance. Additionally, seamless integration with enterprise resource planning (ERP) systems streamlines production planning, inventory management, and order tracking, enhancing operational efficiency and agility.
Precision and Accuracy
As customer demands for precision and quality continue to rise, CNC press brakes are evolving to deliver higher levels of accuracy and repeatability. Advancements in servo-electric and hybrid drive systems, coupled with sophisticated control algorithms, enable precise control over bending parameters such as angle, length, and force. Additionally, innovations in tooling technologies, such as dynamic crowning and adaptive bending, enhance bending accuracy and compensate for material variations and springback effects.
Sustainability and Environmental Responsibility
With increasing focus on sustainability and environmental responsibility, CNC press brake manufacturers are prioritizing energy efficiency and eco-friendly practices. Energy-efficient servo-driven hydraulic systems, regenerative braking systems, and intelligent power management strategies help minimize energy consumption and reduce carbon footprint. Furthermore, the adoption of recyclable materials, waste reduction initiatives, and eco-conscious manufacturing processes align with sustainability goals and support a greener future for metal fabrication.
Customization and Personalization
In today's market, customization and personalization are driving forces behind consumer preferences. CNC press brakes are adapting to meet these demands by offering greater flexibility and versatility in bending capabilities. Multi-axis control systems, versatile tooling options, and adaptive bending technologies enable the production of highly customized parts with intricate geometries and complex profiles. Whether it's automotive components, aerospace structures, or architectural elements, CNC press brakes empower manufacturers to deliver tailor-made solutions that meet the unique needs of their customers.
Conclusion:Advancing Metal Fabrication,CNC Press Brake Automation and Innovation
Looking ahead, the future prospects of CNC press brakes are bright, with continued innovation and technological advancements driving growth and competitiveness in the metal fabrication industry. By embracing these trends and leveraging the capabilities of CNC press brakes, manufacturers can stay agile, responsive, and ahead of the curve in meeting the evolving demands of the market.