Table of Contents
Investing in a CNC press brake is a significant decision for any metal fabrication business. To ensure you make the right choice, consider the following factors when evaluating options and making a purchase:
Key Factors to Consider For Buying A CNC Press Brake
Bending Capacity
When determining the maximum bending length and thickness required for your typical projects, it's essential to assess the range of parts you'll be producing and the materials you'll be working with. Consider the diversity of your product portfolio and the specific geometries and dimensions involved in each component. Evaluate past projects and forecast future demands to establish a comprehensive understanding of your bending requirements.
For bending length, take into account the longest parts you anticipate fabricating and ensure that the CNC press brake you choose can accommodate those dimensions comfortably. Factor in any additional space needed for tooling setup, backgauge extensions, and material handling considerations.
Similarly, when considering bending thickness, analyze the range of materials you'll be bending, including their varying thicknesses and material properties. Select a CNC press brake with sufficient tonnage capacity to handle the thickest material you expect to bend, accounting for factors such as material type, grain direction, and bend radius.
It's also prudent to plan for future growth and expansion in your metal fabrication business. Anticipate changes in customer demands, market trends, and technological advancements that may impact your bending requirements. Investing in a CNC press brake with ample capacity and flexibility ensures that your equipment can adapt to evolving production needs and scale with your business over time.
Bending Accuracy
Firstly, pay close attention to the machine's crowning system, which plays a crucial role in compensating for deflection and ensuring uniform bending along the entire length of the workpiece. Opt for CNC press brakes equipped with dynamic crowning systems that automatically adjust the bed's curvature to counteract any deformation caused by bending forces. This feature helps maintain consistent bend angles and dimensions across various parts and material thicknesses, even for long and narrow workpieces.
Furthermore, consider the backgauge options available on the CNC press brake, as they contribute to precise positioning and alignment of the workpiece during bending operations. Look for CNC press brakes with multi-axis CNC backgauges that offer versatility and flexibility in positioning the material accurately for each bend. Additionally, choose backgauge systems with advanced features such as automatic height adjustment, pneumatic clamping, and programmable positioning to streamline setup and enhance bending efficiency.
It's also essential to evaluate the overall rigidity and stability of the CNC press brake's frame and structure, as these factors directly impact bending accuracy and repeatability. Select machines constructed from high-quality materials and engineered for minimal deflection under bending loads. Robust frame designs and reinforced components ensure stable and precise bending performance, especially when working with heavy-duty materials or performing complex bending operations.
Automation Features
Evaluate the level of automation offered by different CNC press brake models. Features such as automatic tool changing, material handling, and part sorting can enhance productivity and reduce labor costs. Choose automation options that align with your production requirements and budget.
Brand Reputation and Support
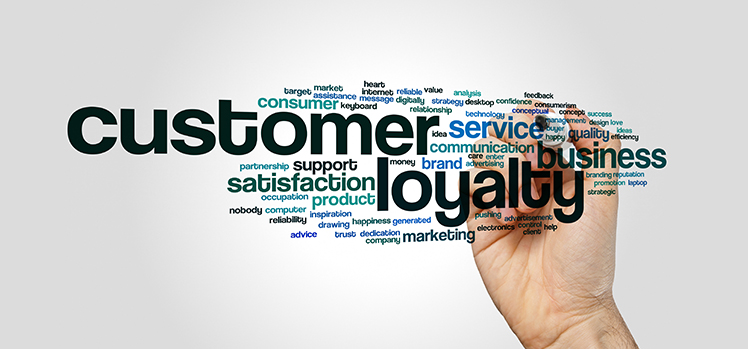
Research reputable CNC press brake manufacturers known for quality craftsmanship and reliable customer support. Read customer reviews, testimonials, and case studies to gauge user satisfaction and reliability. Consider factors such as warranty coverage, spare parts availability, and technical support services when selecting a brand.
Price Budgeting
Establish a realistic budget based on your available funds and expected return on investment. Compare prices from multiple manufacturers and consider total cost of ownership, including installation, training, maintenance, and operational expenses. Balance upfront costs with long-term benefits and savings to make a cost-effective decision.
User-Friendly Interface
Choose a CNC press brake with an intuitive and user-friendly control interface that simplifies programming, setup, and operation. Look for features such as graphical touchscreens, offline programming software, and error diagnostics to enhance operator efficiency and reduce downtime.
Customization Options
Consider your specific application requirements and inquire about customization options available from CNC press brake manufacturers. Customizable features such as tooling configurations, bending sequences, and safety enhancements can tailor the machine to suit your unique production needs.
Conclusion
By carefully considering these key parameters and comparing options from reputable brands, you can make an informed decision when purchasing a CNC press brake for your metal fabrication business. Remember to prioritize functionality, reliability, and long-term value to maximize the benefits of your investment.