In the world of manufacturing, precision and efficiency are paramount. For companies working with sheet metal, having the right equipment is essential to meet the demands of modern production. One such indispensable tool is the press brake sheet metal machine. In this comprehensive guide, we'll explore everything you need to know about press brake sheet metal fabrication, from its definition to its applications and advantages.
Understanding Press Brake Sheet Metal Fabrication
Press brake sheet metal fabrication is a fundamental process in modern manufacturing, serving as a cornerstone for a wide range of industries. With its ability to precisely bend and shape sheet metal to desired specifications, press brake technology plays a crucial role in the production of components and structures used in automotive, aerospace, construction, and electronics applications.
In the automotive industry, press brake sheet metal fabrication is utilized for manufacturing various components such as chassis frames, body panels, brackets, and structural reinforcements. These components require precise bending and shaping to meet stringent safety and performance standards. Press brake machines enable manufacturers to produce these parts with accuracy and consistency, contributing to the overall quality and reliability of vehicles.
In aerospace engineering, press brake sheet metal fabrication is indispensable for producing aircraft components and structures. From fuselage panels to wing ribs, these components demand precise bending to exact specifications to ensure aerodynamic efficiency and structural integrity. Press brake machines enable aerospace manufacturers to achieve the intricate geometries and tight tolerances required for safe and reliable aircraft operation.
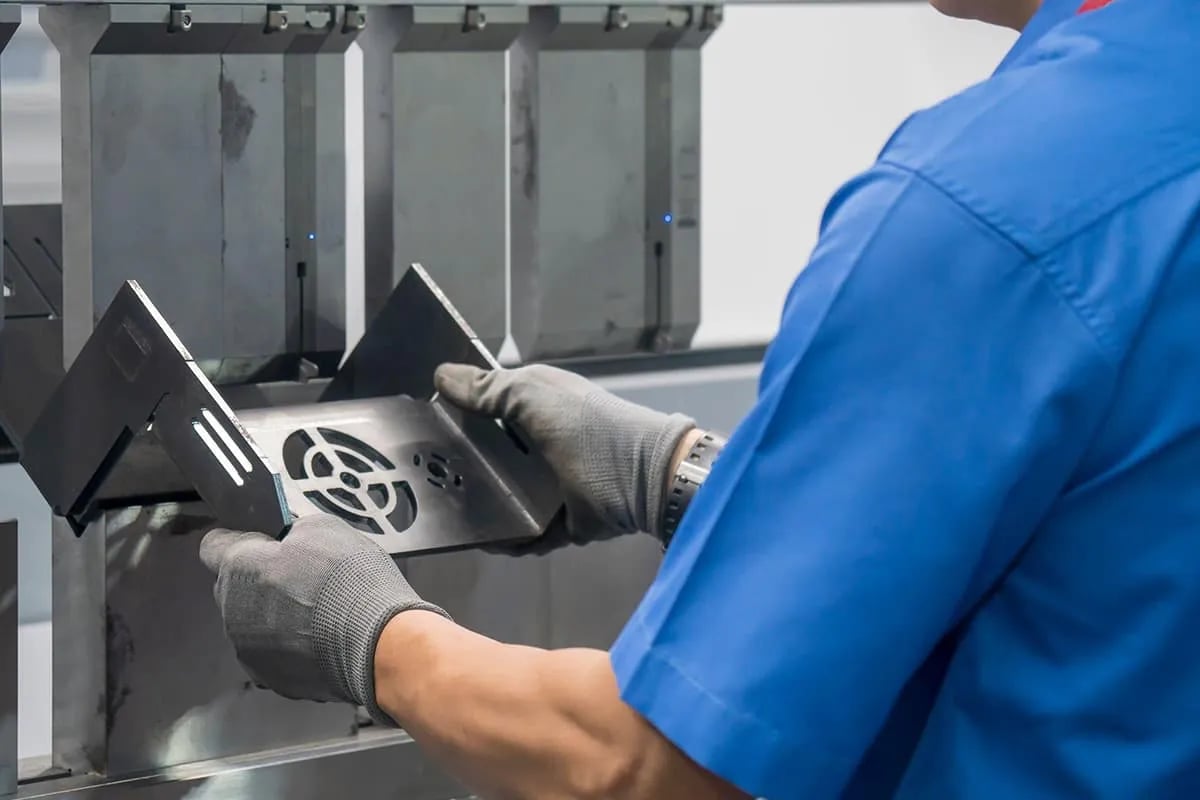
In the construction industry, press brake sheet metal fabrication is employed for manufacturing architectural components, building fixtures, and structural elements. These components include facade panels, roofing materials, staircases, and beams, among others. Press brake technology allows construction companies to fabricate these parts with precision and efficiency, contributing to the aesthetic appeal, durability, and functionality of buildings and infrastructure projects.
In the electronics sector, press brake sheet metal fabrication is used for producing enclosures, chassis, brackets, and other components for electronic devices and appliances. These components require precise bending to accommodate circuitry, connectors, and other internal components while ensuring proper ventilation and heat dissipation. Press brake machines enable electronics manufacturers to fabricate these parts with accuracy and reliability, meeting the performance and safety standards of modern electronic devices.
Components of a Press Brake Machine
The Bed
The bed is the foundation of the press brake machine, providing a stable platform for the workpiece during bending operations.
Constructed from heavy-duty materials such as cast iron or steel, the bed ensures rigidity and stability, essential for achieving accurate and consistent bends.
The bed may feature T-slots or grooves to accommodate tooling and accessories for holding and clamping the workpiece securely in place.
The Ram
The ram is the moving component of the press brake machine responsible for applying the bending force to the workpiece.
Connected to the hydraulic or mechanical system of the machine, the ram moves vertically or horizontally, exerting pressure on the workpiece to create the desired bend.
The ram may be equipped with tooling such as punches and dies, which come in various shapes and sizes to accommodate different bending requirements.
The Back Gauge
The back gauge is a positioning device located at the rear of the press brake machine, opposite the ram.
It consists of a series of adjustable fingers or stops that help position the workpiece accurately relative to the bending tooling.
By precisely controlling the position of the back gauge, operators can ensure consistent bend angles and dimensions across multiple workpieces, improving overall accuracy and efficiency.
The Control Panel
The control panel is the interface through which operators interact with the press brake machine.
It allows operators to input bending parameters such as bend angle, bend length, and material thickness.
The control panel may feature a touchscreen display or a combination of buttons, switches, and knobs for adjusting settings and monitoring the bending process.
Advanced press brake machines may be equipped with computer numerical control (CNC) systems, allowing for programmable bending sequences and automated operation.
Working Principles of Press Brake Sheet Metal Fabrication
The bending process in a press brake machine is a critical step in sheet metal fabrication, where precision and accuracy are paramount. Let's delve deeper into each aspect of the bending process:
Insertion of Sheet Metal
Before bending can occur, the sheet metal workpiece is carefully positioned between the ram and the bed of the press brake machine.
Operators must ensure that the sheet metal is aligned properly and securely held in place to prevent shifting or misalignment during the bending operation.
Application of Bending Force
Once the sheet metal is in position, the ram of the press brake machine begins to descend, applying force to the workpiece.
The force exerted by the ram causes the sheet metal to bend along the predetermined bend line, creating the desired angle or shape.
The amount of force applied by the ram is carefully controlled to achieve consistent and accurate bends, taking into account factors such as material thickness and bend radius.
Role of the Back Gauge
While the bending process is underway, the back gauge of the press brake machine plays a crucial role in ensuring precise positioning of the workpiece.
The back gauge consists of adjustable fingers or stops that are positioned behind the workpiece to establish the correct bend line.
By accurately positioning the back gauge, operators can achieve uniform bend angles and dimensions across multiple workpieces, improving overall consistency and quality.
Adjustment of Bending Parameters
The control panel of the press brake machine provides operators with the ability to adjust various parameters to control the bending process.
Operators can input parameters such as bend angle, bend length, and bend radius, tailoring the bending operation to the specific requirements of the workpiece.
Advanced press brake machines may feature computer numerical control (CNC) systems, allowing for precise programming of bending sequences and automation of repetitive tasks.
Advantages of Press Brake Sheet Metal Fabrication
Press brake sheet metal fabrication offers numerous advantages over other bending methods. It allows for high precision, enabling manufacturers to achieve tight tolerances and intricate designs. It's also highly versatile, capable of bending a wide range of materials and thicknesses. Additionally, press brake machines are efficient, allowing for rapid production and quick setup times.
Applications of Press Brake Sheet Metal Fabrication
Press brake sheet metal fabrication is used in a variety of industries and applications. In automotive manufacturing, it's used to create chassis components and body panels. In aerospace, it's used to fabricate aircraft parts and structures. In construction, it's used to produce architectural components and building fixtures. And in electronics, it's used to manufacture enclosures and housings for electronic devices.
Conclusion
Press brake sheet metal fabrication is a vital process in modern manufacturing, enabling companies to produce high-quality parts and components with precision and efficiency. By understanding the principles and advantages of press brake technology, manufacturers can optimize their production processes and stay ahead in today's competitive market.