Navigating the choice between NC and CNC press brakes can be a pivotal decision for metal fabrication businesses. Each option offers distinct advantages and considerations, influencing the efficiency, precision, and cost-effectiveness of your bending operations. To make an informed decision, it's essential to understand the differences between NC and CNC press brakes and how they align with your specific production needs and objectives. Let's delve into these distinctions and explore how to determine which option is the best fit for your requirements.
Table of Contents
Exploring CNC Press Brake
The CNC Press Brake stands as a pinnacle of contemporary metal fabrication technology, leveraging sophisticated computer numerical control to elevate precision, speed, and flexibility in bending sheet metal. This state-of-the-art machine relies on precise programming and real-time feedback systems to automate bending processes, greatly enhancing production efficiency and accuracy.
Key Components of CNC Press Brake
The effectiveness of the CNC press brake is underpinned by its intricate components, each fulfilling a vital role:
- CNC Controller: Serving as the central hub, the CNC controller interprets and executes programmed instructions, orchestrating the entire bending operation.
- Backgauge: This precision positioning system ensures accurate placement of the metal sheet, optimizing bending outcomes.
- Ram: The ram is responsible for descending and exerting controlled force, facilitating the bending process.
- Punch and Die: These customizable tools physically shape the metal, generating the desired bend configuration.
- Safety Systems: Integrated safety features such as light curtains and laser systems uphold operator safety throughout operation.
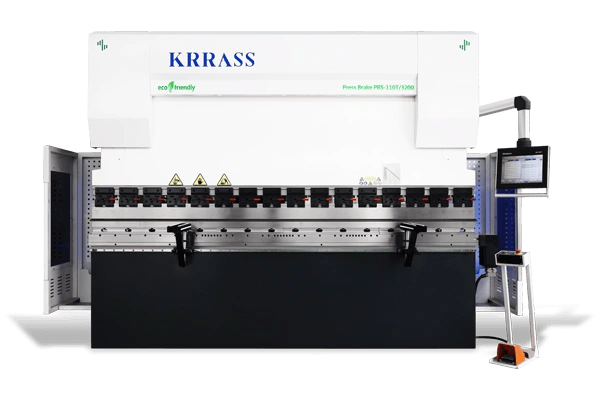
Operational Mechanism of CNC Press Brakes
The operational workflow of CNC press brakes exemplifies the seamless integration of advanced technology in manufacturing:
- Programming: Elaborate instructions, encompassing bend angles and sequences, are meticulously programmed into the CNC controller.
- Setup: Leveraging the input, the machine autonomously adjusts the backgauge and selects optimal tools for the task at hand.
- Bending Process: The ram executes precise downward motion, applying controlled force to mold the metal sheet against the die. Real-time feedback mechanisms ensure accuracy and consistency.
- Quality Assurance: Continuous monitoring safeguards against deviations, ensuring each bend aligns with programmed specifications. Adjustments are made in real-time to maintain precision throughout production.
Delving into NC Press Brake
An NC Press Brake serves as a vital intermediary between manual bending techniques and fully automated CNC press brake systems. Employing numerical control systems, NC press brakes execute bending operations, providing a cost-effective alternative for less intricate tasks. While they may lack the complete automation and precision of CNC models, NC press brakes still present a substantial improvement over manual processes, enhancing production efficiency and consistency in operations that do not demand intricate programming or real-time feedback.
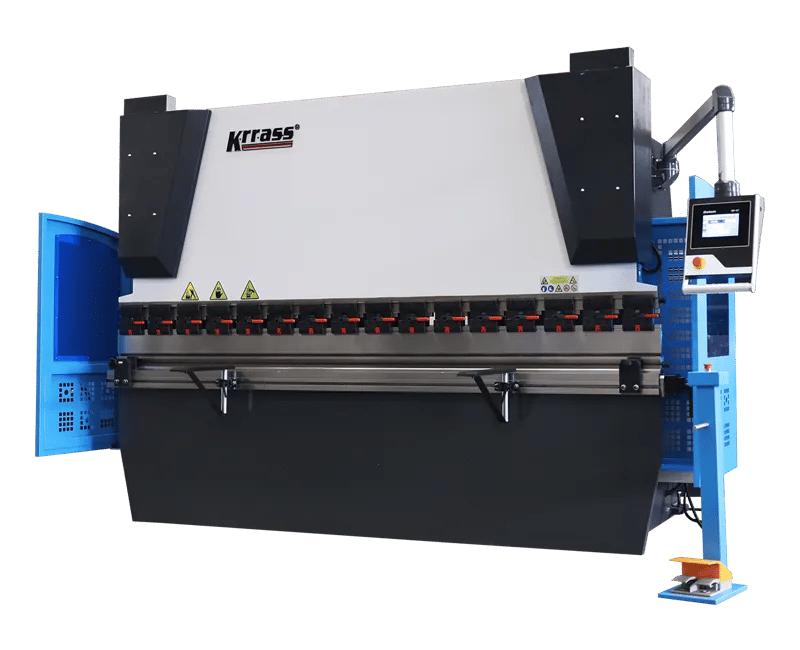
Core Components of NC Press Brake
The functionality of NC press brakes relies on several fundamental components:
- NC Controller: A simplified version compared to CNC controllers, it enables basic programming of bending operations.
- Backgauge: Mechanically positions the workpiece, albeit with less precision than CNC models.
- Ram: Executes the bending action by moving the punch towards the die.
- Punch and Die: Essential tools that collaborate to bend the metal sheet effectively.
Operation of NC Press Brakes
The operational workflow of NC press brakes can be summarized as follows:
- Programming: Operators input bending parameters, including bend angles, sequence, and backgauge positions, into the NC controller.
- Setup: Based on the inputted data, operators manually configure the machine, adjusting the backgauge and installing the appropriate punch and die combination.
- Bending Operation: Operators initiate the bending process, with the ram moving the punch to press the workpiece into the die, creating the desired bend. The backgauge positions the workpiece for each bend.
- Manual Adjustments: Unlike CNC press brakes, operators may need to make manual adjustments between bends to ensure accuracy.
NC press brakes, characterized by their simpler operation and lower cost, remain a viable option for numerous fabrication tasks. They are particularly suitable for projects where the extensive automation and flexibility of CNC press brakes are unnecessary. By combining numerical control with mechanical precision, NC press brakes offer a well-rounded solution for achieving consistent, accurate bends across various metalworking applications.
NC vs CNC Press Brakes: Pros and Cons; Comparion
Each type of press brake possesses distinct strengths and weaknesses, influencing their suitability for diverse manufacturing environments.
Advantages of CNC Press Brakes:
- Enhanced Precision and Consistency: Advanced control systems enable CNC press brakes to achieve superior bending accuracy and repeatability.
- Increased Productivity: Automation and quicker setup times contribute to higher throughput, making CNC press brakes ideal for high-volume production.
- Versatility: Programmable settings and seamless job-switching capabilities allow CNC press brakes to handle a wide range of bending tasks, including complex shapes and materials.
- Waste Reduction: The precision and real-time feedback of CNC press brakes minimize material waste, leading to cost savings and improved sustainability.
Disadvantages of CNC Press Brakes:
- Higher Initial Cost: The advanced technology of CNC press brakes results in a higher purchase price, making them a substantial investment.
- Complexity and Maintenance: The intricate nature of CNC machines can lead to higher maintenance costs and necessitate specialized technicians for upkeep.
- Training Requirements: Operators must undergo training to effectively utilize the sophisticated software and controls, adding to operational costs.
Advantages of NC Press Brakes:
- Lower Initial Investment: NC press brakes typically have a lower purchase cost than CNC models, making them accessible to smaller operations or those with budget constraints.
- Simplicity: With fewer complex features, NC press brakes are easier to maintain and operate, requiring less specialized training.
- Reliability: The mechanical simplicity of NC press brakes can result in robust performance and durability with proper maintenance.
Disadvantages of NC Press Brakes:
- Limited Flexibility: Lack of advanced programmable features may render NC press brakes unsuitable for tasks requiring high precision or complex bending sequences.
- Lower Productivity: Manual adjustments and setups can diminish the efficiency of NC press brakes, particularly for large-scale or intricate production runs.
- Dependence on Operator Skill: Consistent results with NC press brakes hinge heavily on the operator's experience and skill level.
CNC and NC Press Brakes: Accuracy and Speed Comparison
Both have their unique advantages, but they differ significantly in terms of accuracy, speed, and overall efficiency. Understanding these differences is crucial for manufacturers to choose the right equipment for their specific needs.
Accuracy
- CNC Press Brakes: These machines offer superior accuracy thanks to their advanced control systems. CNC press brakes utilize precise, programmable parameters and real-time feedback mechanisms to ensure each bend is executed with exact precision. This is particularly important for complex shapes or where tight tolerances are required.
- NC Press Brakes: While NC press brakes can achieve a high degree of accuracy, they lack the real-time adjustment capabilities of CNC models. The operator sets the parameters before the job, and adjustments during bending are manual and less precise, potentially leading to slight variations in the finished product.
Speed
- CNC Press Brakes: Speed is one of the major advantages of CNC press brakes. The automated nature of these machines, combined with their ability to quickly adjust to different bending parameters, allows for faster production times. This is enhanced by features such as automatic tool changing and rapid ram movement.
- NC Press Brakes: NC press brakes generally operate at slower speeds compared to their CNC counterparts. The manual setup and adjustments required for each job can lead to increased cycle times, particularly for complex bending operations or when switching between different types of bends.
Customization and Flexibility Comparison
In today’s dynamic manufacturing environment, the ability to adapt to custom jobs and various projects is essential. Both CNC and NC press brakes offer different levels of customization and flexibility, catering to the diverse needs of the metal fabrication industry.
CNC Press Brakes
- High Customization: CNC press brakes excel in customization due to their programmable nature. The ability to store and recall numerous programs allows for quick setup changes between jobs, making it easier to handle custom or complex bending tasks.
- Superior Flexibility: The advanced control systems of CNC press brakes enable them to adapt to a wide range of materials, thicknesses, and bending angles with precision. This flexibility is crucial for workshops that work on varied projects requiring high levels of detail and customization.
- Automated Tool Changing: Many CNC press brakes feature automated tool changing systems, further enhancing their adaptability by reducing setup times for different jobs.
NC Press Brakes
- Moderate Customization: While NC press brakes can be set up for custom jobs, the process is generally more manual and time-consuming than with CNC models. The lack of programmable controls means adjustments between different projects can slow down production.
- Basic Flexibility: NC press brakes provide a level of flexibility suitable for straightforward bending tasks. However, their manual setup process and limited control options can restrict their use in projects requiring high precision or varied bending operations.
- Tool Changing: Changes in tooling on NC press brakes require manual intervention, which can extend setup times and reduce overall flexibility in switching between different types of jobs.
How to Choose Between CNC and NC Press Brakes
Choosing between CNC and NC press brakes requires careful consideration of several factors tailored to your specific production needs, budget, and long-term objectives. Here's a breakdown of key decision-making criteria:
Production Volume and Complexity:
For high-volume production with intricate bending requirements, CNC press brakes offer superior precision, speed, and flexibility. Conversely, if your tasks are simpler and lower in volume, an NC press brake may suffice.
Precision Requirements:
CNC press brakes excel in achieving tight tolerances and high repeatability, making them suitable for projects demanding precision. However, if your work does not require such exactness, an NC press brake could be a more cost-effective choice.
Material Handling:
Consider the range of materials and thicknesses you'll be working with. CNC press brakes can handle a broader variety of materials efficiently and with less waste compared to NC models.
Operator Skill Level:
CNC press brakes are designed to be user-friendly and require less operator skill due to their automated features and programmable controls. On the other hand, NC press brakes may require a more experienced operator to achieve optimal results.
Flexibility and Future Needs:
If you anticipate diversifying your projects or scaling up production, the adaptability of CNC press brakes makes them a worthwhile investment. However, if your business maintains a steady output of similar products, an NC press brake may suffice.
Budget Constraints:
CNC press brakes typically entail a higher initial investment compared to NC models. Assess your budget and weigh the potential return on investment, considering efficiency gains and the ability to undertake more complex jobs with a CNC press brake.
Maintenance and Operating Costs:
While CNC press brakes may incur higher maintenance and operating costs due to their complexity and software updates, their efficiency and reduced waste can offset these expenses over time. NC press brakes generally have lower initial maintenance costs but may lack the same efficiency benefits.
Conclusion
Choosing between a CNC and an NC press brake involves a careful assessment of your specific needs, the nature of your work, and your long-term objectives.
CNC press brakes offer unparalleled precision, flexibility, and efficiency for high-volume or complex bending operations.
NC press brakes can be a cost-effective solution for simpler tasks and smaller-scale operations.
Regardless of the choice, both CNC and NC press brakes play vital roles in the metal fabrication industry, each offering unique benefits to suit different manufacturing environments. Ultimately, the decision should be guided by a balanced consideration of production requirements, budget constraints, and future growth prospects to ensure that you select the right machine for your business’s needs.