In precision manufacturing, laser cutting represents the epitome of accuracy and efficiency. This guide delves into a fundamental aspect of laser cutting: the kerf. Appreciating the intricacies of laser cutting kerf not only refines cut accuracy but also maximizes material utilization and cost-effectiveness. Within this discussion, we'll elucidate the concept of laser cutting kerf, underscore its significance, and analyze its effects on different materials and laser variants.
What Is Laser Cutting Kerf
The term ‘kerf’ refers to the amount of material that is removed by the laser beam during the cutting process. In the context of laser cutting, the kerf width is pivotal for achieving precision. It’s not just a cut line; it’s the difference between a perfect fit and a failed project. The kerf’s width varies based on multiple factors including the laser type, material properties, and cutting settings, making it a crucial element in laser manufacturing.
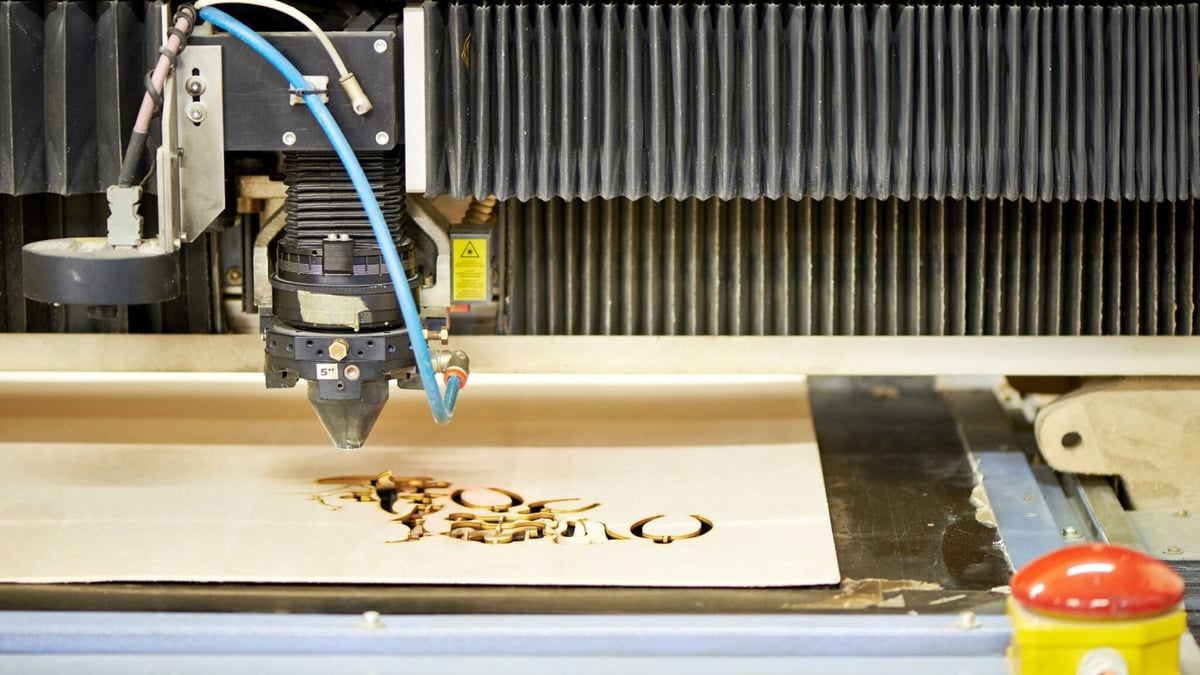
What Does laser Kerf Mean
The laser burns away a portion of material when it cuts through. This is known as the laser kerf and ranges from 0.08mm – 1mm depending on the material type and other conditional factors. Although above ~0.45mm is only experienced when cutting thicker foams. Any areas in your design where cut lines come closer than 0.5mm together could burn away entirely. Any details narrower than 1mm are likely to be very fragile and in some cases can cause the material to warp whilst cutting.
As a benchmark, we recommend that minimum cut widths be no smaller than the corresponding thickness of the material. For example, if cutting from 3mm acrylic, it’s best not to allow any widths less than 3mm. We can go smaller (see the cut width image on the material pages) but this can make your pieces very fragile which might not be suitable for your application. We will advise if your drawing has cutting tolerances that are too small, but we can’t be held responsible if your components do not hold together sufficiently.
Kerf is determined by material properties and thickness. But other factors also have an impact on how much the laser takes away. The focal length of the lens, pressure of compressed air both have an impact. Kerf widths can vary even on the same material sheet, whether cutting a straight line or a curve line or from laser cutting in the x or Y dimension. The manufacturing tolerance of the material can also impact the kerf.
For a fee, we can help you with offsetting the kerf to ensure that your project cuts and fits together accurately, if you would like our help with this, let us know and we can work with you to make sure your drawing is correct.
Incorporating Laser Kerf Considerations into Drawings
For some applications (for example a slot together product), you will need to account for the kerf within your drawing by adding or subtracting the kerf width from your component dimensions. The following table gives an overview of the average measurement the laser will take away when cutting on the most commonly cut materials and thicknesses. Please bear in mind that these measurements are to be treated as guidelines only, use them as a starting point. We always recommend prototyping a portion of your design taking into account the kerf and tweaking if necessary.
MATERIALS | THICKNESS | AVERAGE KERF |
---|---|---|
Acrylic | 1mm-3mm | 0.18mm |
Acrylic | 5mm-8mm | 0.21mm |
Acrylic | 10mm-15mm | 0.30mm |
Acrylic | 20mm | 0.32mm |
HIPS, PETG, Styrene | 1mm-3mm | 0.45mm |
Birch plywood | 0.8mm | 0.08mm |
Birch plywood | 1.5mm | 0.16mm |
Birch plywood | 3mm | 0.20mm |
Birch plywood | 6mm | 0.22mm |
Birch plywood | 12mm | 0.3mm |
MDF | 3mm | 0.16mm |
MDF | 6mm | 0.2mm |
MDF | 12mm | 0.28mm |
Veneered MDF | 6mm | 0.17mm |
Greyboard | 1200microns | 0.08mm |
Greyboard | 2400microns | 0.12mm |
Paper | 90 – 350 gsm | 0.08mm |