When precision cutting is essential, one common question is, "How thick can 3000W fiber laser cut?" This cutting-edge technology has transformed the manufacturing industry with its exceptional accuracy and efficiency. Knowing the maximum cutting thickness of a 3000W fiber laser is vital for maximizing its effectiveness across various applications. In this article, we examine the upper limits of thickness achievable with a 3000W fiber laser, investigate the factors that impact its performance, and offer practical advice for users.
Table of Contents
Introduction
Brief Overview of Fiber Laser Cutting Technology
Fiber laser cutting technology has emerged as a game-changer in the manufacturing industry due to its precision, speed, and efficiency. Unlike traditional cutting methods, fiber lasers use a high-powered beam of light generated by diodes and transmitted through a flexible optical fiber. This beam is focused onto the material, melting, burning, or vaporizing it to achieve precise cuts. The technology is widely used in various industries, including automotive, aerospace, electronics, and metal fabrication, owing to its ability to cut complex shapes with high accuracy and minimal waste.
Importance of Understanding the Cutting Limits of a 3000W Fiber Laser
Understanding the cutting limits of a 3000W fiber laser is essential for optimizing its performance and ensuring its efficient use in different applications. Knowing how thick a 3000W fiber laser can cut helps in selecting the appropriate materials and adjusting the cutting parameters to achieve the desired results. This knowledge is crucial for manufacturers to maximize productivity, reduce material costs, and maintain high-quality standards in their production processes. Additionally, it allows for better planning and decision-making when investing in fiber laser cutting technology, ensuring that the chosen equipment meets the specific needs of the operation.
Understanding Fiber Laser Technology
How Does Fiber Lasers Work
Fiber lasers operate by generating a high-powered beam of light through the amplification of light in a fiber optic cable doped with rare-earth elements like ytterbium. The light is produced by diodes and then channeled through the optical fiber, which is designed to amplify the light without losing its coherence. This highly focused and intense beam is directed at the material to be cut, where it heats the material to its melting point, allowing for precise cuts. The beam's focus and intensity can be finely controlled, enabling intricate designs and detailed work with minimal distortion or thermal damage to the surrounding material.
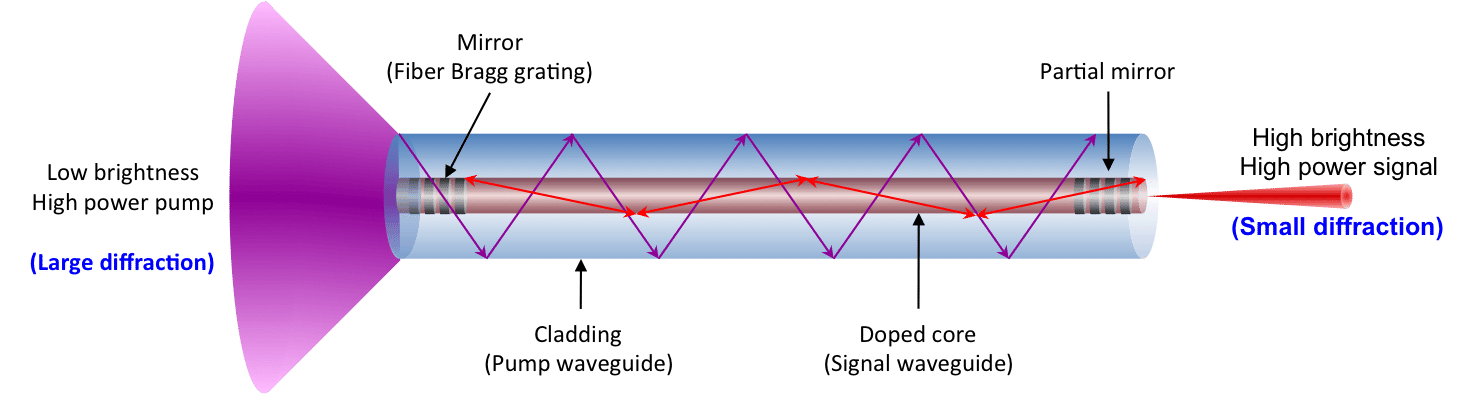
CO2 Laser Vs. Fiber Laser: Which One Is Better For Cutting Metal?
CO2 Lasers:
- Versatility: CO2 lasers are highly versatile and can cut a wide range of materials beyond metals, including plastics, wood, and ceramics.
- Thicker Materials: They are effective for cutting thicker metals, such as mild steel and stainless steel up to 25mm thick, due to their ability to maintain stable beam quality over longer distances.
- Smooth Edges: CO2 lasers can produce smoother edges on thicker materials, which is advantageous for applications requiring a high-quality finish.
- Initial Cost: Generally, CO2 laser machines tend to have a lower initial investment cost compared to fiber lasers, making them more accessible for some businesses.
Fiber Lasers:
- Speed and Efficiency: Fiber lasers are renowned for their high cutting speeds and energy efficiency, making them ideal for high-volume production environments.
- Precision: They offer excellent precision and accuracy, making them suitable for intricate designs and fine detailing, even on thinner materials.
- Maintenance: Fiber lasers typically require less maintenance due to their solid-state design and fewer moving parts, resulting in lower operational costs over time.
- Reflective Materials: Fiber lasers are particularly effective for cutting reflective materials like copper, brass, and aluminum, which can be challenging for CO2 lasers due to their wavelength absorption characteristics.
Choosing the Right Technology:
- Production Volume: For high-volume production requiring speed and efficiency, fiber lasers are often preferred.
- Material Type: If your cutting needs include a variety of materials beyond metals, CO2 lasers offer greater versatility.
- Thickness and Precision: For thick metals and applications demanding precise cutting, CO2 lasers excel, whereas fiber lasers shine in tasks requiring intricate detailing and high-speed cutting of thin to medium-thick metals.
Advantages of Fiber Lasers Over Other Cutting Methods
Fiber lasers stand out in the manufacturing industry due to their numerous advantages over traditional cutting methods and other laser technologies:
Precision and Accuracy
Fiber lasers excel in providing precise cuts with narrow kerf widths, significantly reducing material waste. This precision allows for intricate designs and complex geometries that are crucial in industries like aerospace and electronics. Studies have shown that fiber lasers can achieve positioning accuracies of up to ±0.05 mm, ensuring consistent quality and dimensional accuracy in every cut.
High Efficiency
Compared to CO2 lasers, fiber lasers demonstrate superior efficiency, leading to lower operational costs and reduced energy consumption. Research indicates that fiber lasers can convert over 30% of input electrical energy into usable laser power, whereas CO2 lasers typically convert around 10-20%. This efficiency not only lowers production costs but also contributes to sustainable manufacturing practices by minimizing energy usage and carbon footprint.
Speed
One of the most significant advantages of fiber lasers is their high cutting speed. They can cut materials at speeds up to 3 times faster than CO2 lasers. For example, a 3000W fiber laser can cut thin sheets of steel at speeds exceeding 30 meters per minute, significantly enhancing productivity and reducing lead times in manufacturing processes.
Versatility
Fiber lasers are versatile and capable of cutting a wide range of materials with varying thicknesses. They can process metals such as steel (up to 25 mm), aluminum (up to 15 mm), and copper (up to 12 mm), as well as non-metals like plastics and composites. This versatility makes fiber lasers suitable for diverse applications across multiple industries, from automotive and medical device manufacturing to architectural and jewelry industries.
Low Maintenance
With fewer moving parts and a sealed fiber optic path, fiber lasers require minimal maintenance compared to CO2 lasers and mechanical cutting systems. Studies show that fiber lasers can operate continuously for thousands of hours before requiring servicing, reducing downtime and maintenance costs associated with traditional laser systems.
Quality of Cuts
The high beam quality of fiber lasers ensures clean, smooth edges without burrs or thermal distortion, eliminating the need for secondary finishing processes. This superior cut quality is crucial for achieving tight tolerances and meeting stringent quality standards in manufacturing operations.
Environmental Impact
Fiber lasers are recognized for their environmental benefits due to their high energy efficiency and minimal emissions. Research indicates that fiber lasers consume up to 70% less energy than CO2 lasers for the same cutting tasks, contributing to lower greenhouse gas emissions and reducing the overall environmental impact of manufacturing processes.
In conclusion, fiber lasers represent a technological advancement that not only enhances manufacturing capabilities but also promotes sustainability and cost-effectiveness in industrial operations. Their precision, efficiency, speed, versatility, low maintenance requirements, superior cut quality, and environmental advantages position them as a preferred choice for modern manufacturing applications.
Three Factors Influencing Cutting Thickness
Achieving optimal cutting thickness with a fiber laser involves a nuanced understanding of several critical factors that impact its performance and capabilities:
Material Type
Different materials react differently to laser cutting due to their composition and properties:
- Steel: Fiber lasers can effectively cut mild steel up to 25 mm thick and stainless steel up to 20 mm thick, depending on the specific alloy composition and grade.
- Aluminum: With its lower density but higher thermal conductivity compared to steel, aluminum can be cut up to approximately 15 mm thick using fiber lasers.
- Copper and Brass: These materials are more challenging to cut due to their high reflectivity to infrared wavelengths. Fiber lasers typically limit cutting thickness for copper and brass to around 12 mm.
Material Properties
Various material properties significantly influence cutting capabilities:
- Density: Higher density materials require more laser power to achieve deeper cuts. For instance, cutting thicker sections of high-density materials like steel may necessitate higher power settings.
- Thermal Conductivity: Materials with high thermal conductivity, such as copper, dissipate heat rapidly. This characteristic can affect the cutting process, requiring adjustments in laser parameters to maintain efficiency and quality.
- Reflectivity: Reflective materials like aluminum and copper may require optimization of laser parameters to enhance cutting efficiency. Managing reflectivity is crucial for achieving clean cuts without compromising speed or quality.
Cutting Speed and Quality Requirements
Balancing cutting speed with quality considerations is crucial for achieving optimal results:
- Speed: Fiber lasers are capable of high cutting speeds, exceeding 30 meters per minute for thin materials. However, cutting thicker sections may require slower speeds to maintain precision and avoid thermal distortion.
- Quality Requirements: Meeting stringent quality standards involves adjusting cutting parameters such as power, focus, and speed. Fine-tuning these parameters ensures clean edges, minimal burrs, and dimensional accuracy, especially for applications requiring tight tolerances.
Understanding these factors empowers operators to optimize cutting processes, select suitable materials, and adjust parameters effectively with fiber laser technology. This comprehensive approach ensures efficient operation and high-quality results across a range of industrial applications.
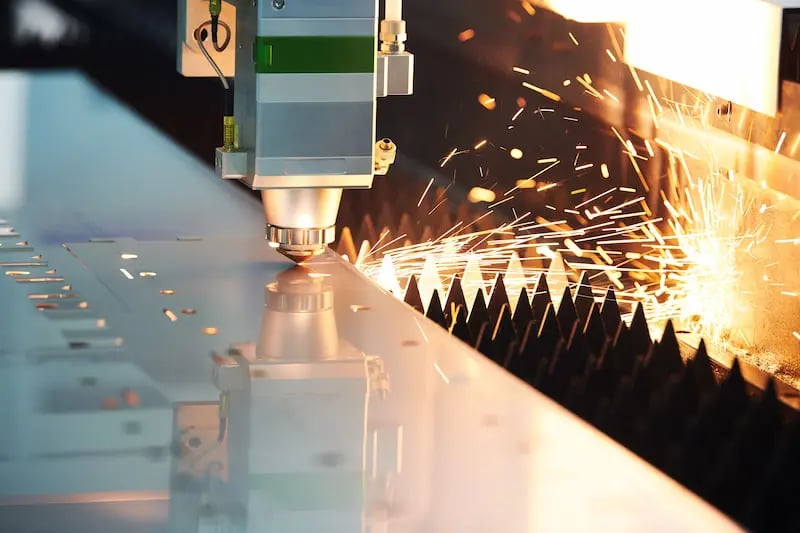
Maximum Cutting Thickness for Different Materials
Meta fiber laser cutting machines are primarily used to cut a variety of metal materials, including stainless steel, carbon steel, alloy steel, aluminum, silver, copper, titanium, and other metals. The key advantages of these machines become evident in their practical applications. The cutting capacity of a fiber laser cutting machine depends on factors such as the machine's quality, the type of laser used, the cutting environment, cutting speed, and the use of auxiliary gases, which can enhance cutting capabilities. Consequently, there is no absolute standard for judging cutting thickness. Generally, thicker metal plates pose greater challenges for cutting. When purchasing laser cutters, users must carefully consider their specific needs and select the appropriate laser configuration accordingly.
So, what thicknesses can various power fiber laser cutting machines effectively cut through metal plates?
How Thick Can 500W to 2000W Fiber Laser Cut?
1. The maximum cutting thickness of different materials of 500W metal laser cutting machine: the maximum thickness of carbon steel is 6mm; The maximum thickness of stainless steel is 3mm; The maximum thickness of aluminum plate is 2mm; The maximum thickness of copper plate is 2mm;
2. The maximum thickness of different materials cut by 1000W metal laser cutting machine: the maximum thickness of carbon steel is 10mm; The maximum thickness of stainless steel is 5mm; The maximum thickness of aluminum plate is 3mm; The maximum thickness of copper plate is 3mm;
3. The maximum thickness of different materials cut by 2000W metal laser cutting machine: the maximum thickness of carbon steel is 16mm; The maximum thickness of stainless steel is 8mm; The maximum thickness of aluminum plate is 5mm; The maximum thickness of copper plate is 5mm;
How Thick Can 3000W Fiber Laser Cut?
The maximum thickness of different materials cut by 3000W metal laser cutting machine: the maximum thickness of carbon steel is 20mm; The maximum thickness of stainless steel is 10mm; The maximum thickness of aluminum plate is 8mm; The maximum thickness of copper plate is 8mm;
How Thick Can 4000W Fiber Laser Cut?
4000W laser cutting stainless steel is 16mm at most, but the quality of the cutting surface above 12mm is not guaranteed, and the cutting surface below 12mm is definitely bright. The cutting capacity of 6000W will be better, but the price is also higher.
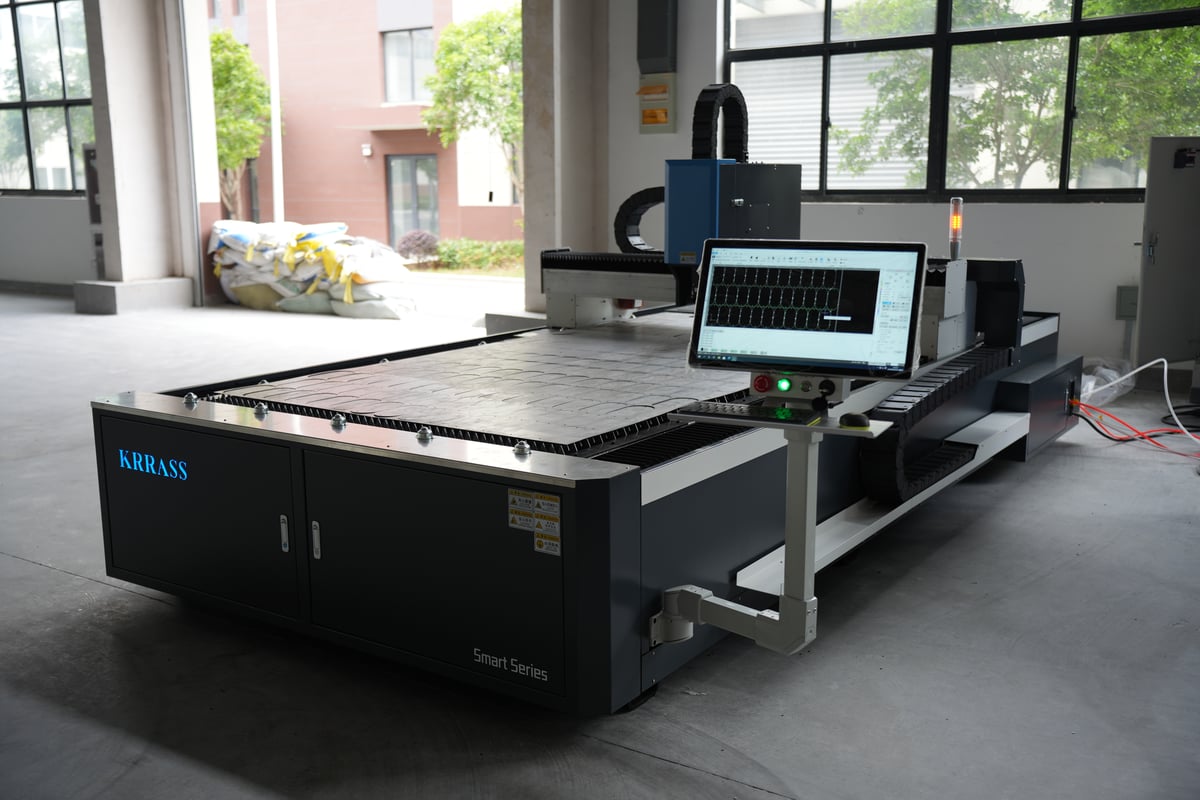
Evolution of Laser Cutting Power: Pushing the Limits of Possibility
From 6000W to 8000W, and now to the once unimaginable 10,000W laser cutting machines, the power of these machines has advanced step by step, surpassing our expectations. Previously, fiber laser cutting was limited to cutting carbon steel plates up to 20mm thick and stainless steel up to 12mm. However, with 10,000W laser cutting machines like the Dada model, aluminum alloy plates up to 40mm thick and stainless steel plates up to 50mm thick can now be effectively cut.
Enhanced Cutting Capabilities
For stainless steel plates ranging from 3mm to 10mm thick, a 10,000W laser cutting machine operates at more than double the speed of a 6000W machine. In carbon steel applications, this machine achieves rapid bright surface cutting at speeds of 18 to 20mm per second, twice the standard cutting speed. Additionally, using compressed air or nitrogen for cutting carbon steel up to 12mm thick increases efficiency six to seven times compared to oxygen cutting.
Recent data highlights substantial speed increases with higher laser power: cutting 8mm stainless steel is nearly 400% faster with a 6kW machine compared to a 3kW model. Moreover, for 20mm thick stainless steel, a 12kW laser operates 114% faster than a 10kW machine.
From an economic standpoint, the cost of a 10,000W laser cutting machine is only marginally higher than a 6kW model, yet it offers more than double the output efficiency. This efficiency not only saves on labor and space but also garners favor among laser processing enterprise owners, underscoring its cost-effectiveness and productivity advantages.
Key Tips for Maximizing Performance of Fiber Laser
Material Preparation and Selection
Choosing suitable materials for fiber laser cutting involves considering their composition and thickness compatibility. Different materials, such as stainless steel, carbon steel, aluminum, and various alloys, respond differently to laser cutting due to their thermal conductivity, reflectivity, and chemical composition. It's crucial to select materials that align with the laser cutter's capabilities and are within its specified cutting thickness range.
Additionally, ensuring materials are clean and free of contaminants is essential to prevent issues during cutting. Contaminants like oil, grease, or rust can interfere with the laser beam's effectiveness, leading to inconsistent cuts, increased heat absorption, or even damage to the cutting equipment. Proper preparation of materials, including thorough cleaning and surface treatment as needed, helps maintain cutting precision and quality throughout the production process. These practices not only optimize cutting performance but also contribute to the longevity of the fiber laser cutting machine and the quality of the finished products.
Optimizing Cutting Parameters
Power: Tailor laser power settings to suit the material's characteristics and thickness, optimizing both cutting speed and quality. This adjustment ensures the laser provides adequate energy for clean and accurate cuts without excessive heat or material distortion.
Speed: Control cutting speed meticulously to strike a balance between efficiency and precision. Adjusting speed allows for smooth cuts while maintaining accuracy, crucial for achieving high-quality results in manufacturing processes.
Focus: Regularly monitor and fine-tune the laser focus to uphold consistent cutting depth and edge quality. Proper focus adjustment ensures the laser beam maintains optimal intensity throughout the cutting process, essential for achieving precise cuts across different material thicknesses.
Environmental Control
Proper Ventilation: Adequate ventilation is essential to remove smoke, fumes, and particles generated during the cutting process. Efficient ventilation not only improves air quality in the workspace but also prevents the accumulation of debris that could obstruct the laser beam or contaminate the material surface.
Humidity Management: Maintaining optimal humidity levels helps to stabilize material properties and prevent variations in cutting performance. Excess humidity can lead to condensation on optics and reduce beam quality, affecting cutting precision. Conversely, overly dry conditions can increase static electricity, potentially causing discharge issues.
Temperature Control: Controlling ambient temperature helps to minimize thermal expansion and contraction of materials, which can affect dimensional accuracy during cutting. Stable temperatures also contribute to consistent laser beam performance and prevent thermal stress on machine components.
Cleanliness: Keeping the work area clean and organized is essential. Dust, dirt, and debris can interfere with laser optics and lead to inconsistent cutting results. Regular cleaning of machine components, including lenses, mirrors, and cutting heads, ensures optimal performance and extends equipment lifespan.
Safety Measures: Implementing safety protocols, such as proper machine grounding, fire prevention measures, and personal protective equipment (PPE) for operators, ensures a safe working environment during laser cutting operations.
Regular Maintenance and Calibration
To maintain peak performance of fiber laser cutting machines, it's essential to adhere to regular maintenance practices that encompass cleaning, calibration, and lubrication.
Cleaning Optics, Lenses, and Cutting Heads: Routine cleaning of optics, lenses, and cutting heads is crucial to remove accumulated debris and contaminants. Dust and residue can impair the quality of the laser beam, leading to uneven cuts or reduced precision. Using recommended cleaning solutions and methods ensures that these components remain clear and functional, optimizing cutting efficiency and quality.
Periodic Calibration: Scheduled calibration sessions are necessary to verify and adjust the alignment of the laser system components. This process ensures that the laser beam remains accurately focused and aligned with the cutting path. By maintaining precise alignment, operators can consistently achieve desired cutting results across various materials and thicknesses, reducing the likelihood of errors and maximizing operational efficiency.
Lubrication of Moving Parts: Applying appropriate lubricants to the moving parts of the laser cutting machine helps minimize friction and wear. This preventive measure not only extends the operational lifespan of critical components but also ensures smoother operation and reduces the risk of mechanical failures. Regular lubrication according to manufacturer guidelines maintains the machine's reliability and performance consistency over time.
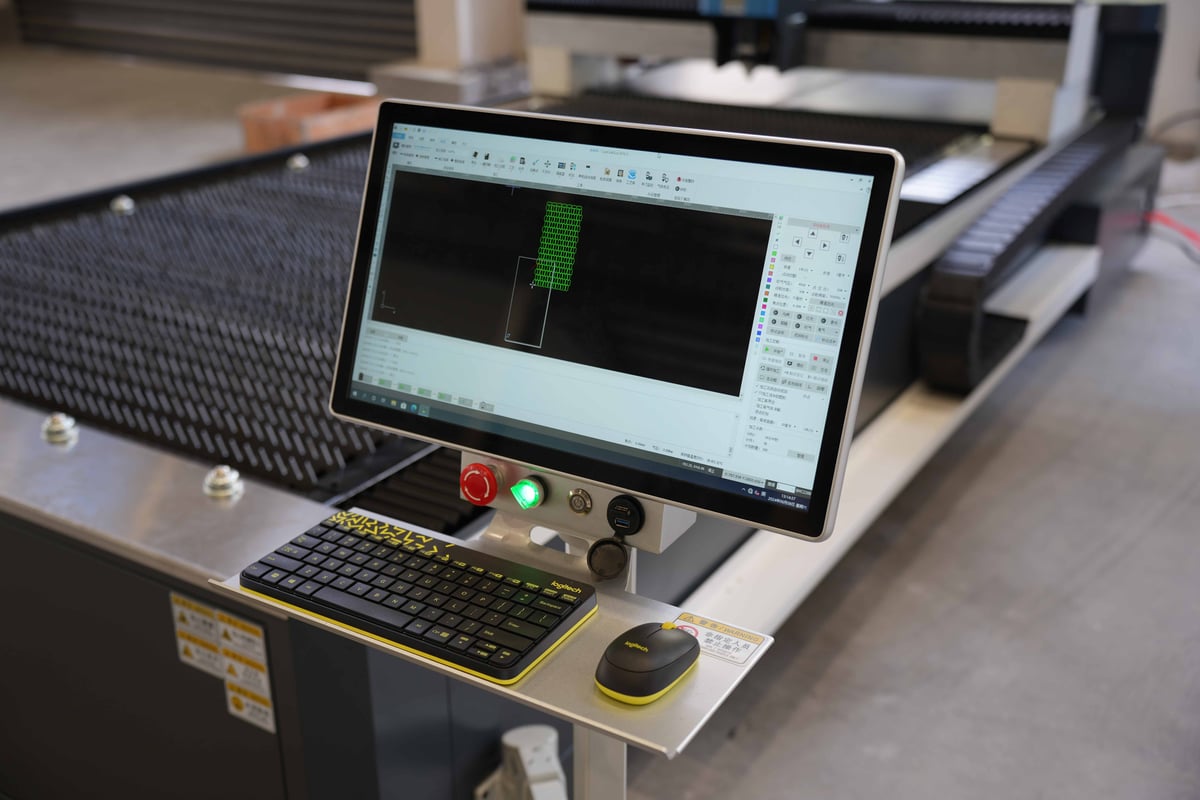
Utilization of Auxiliary Gases
Compressed Air: When used as an auxiliary gas, compressed air helps to blow away molten metal and debris from the cutting zone. This action prevents the accumulation of materials on the cutting surface, reducing the risk of re-solidification and improving the overall cleanliness of the cut. Compressed air also assists in cooling the material during cutting, which can enhance cutting speed and efficiency, especially for thinner materials.
Nitrogen: Nitrogen is widely favored for its non-reactive properties and ability to provide a clean cutting edge. When used as a cutting gas, nitrogen displaces oxygen from the cutting zone, reducing oxidation on the cut edge. This results in a smoother, oxide-free surface finish, particularly beneficial for materials sensitive to oxidation, such as stainless steel and aluminum. Nitrogen also helps maintain stable cutting conditions and can improve the overall quality of the cut, including edge smoothness and dimensional accuracy.
Oxygen and Other Gases: Oxygen is another commonly used auxiliary gas, particularly for cutting mild steel. It enhances the exothermic reaction with the metal, thereby increasing cutting speed and efficiency. However, oxygen may not be suitable for materials prone to oxidation, as it can lead to rougher cut edges and potential heat-affected zones.
Optimizing Gas Usage: The choice of auxiliary gas depends on the material being cut and the desired cutting results. Proper gas selection and optimization can significantly impact cutting speed, edge quality, and overall process efficiency. Operators should experiment with different gas types and pressures to determine the optimal settings for specific materials and thicknesses, ensuring the best possible cutting performance.
How To Choose Best Power For Idea Cutting Effect
The power of a laser cutting machine is a critical factor to consider when purchasing equipment for metal cutting operations. It directly influences the energy output of the laser head, impacting both the quality of processing and the speed of operation. Higher power levels enable superior cutting quality and efficiency, reducing production times significantly.
In the sheet metal industry, laser machines typically start with a minimum power of 500W for thin materials. However, more commonly used cutting powers range from 3 kW to 20 kW, selected based on production requirements and the desired operational advantages. In recent advancements, fiber laser cutting technologies have even reached power levels as high as 40 kW, catering to industrial demands for faster processing speeds and enhanced cutting capabilities.
Choosing the appropriate laser power ensures that manufacturers can achieve optimal results in terms of precision, productivity, and cost-effectiveness. Higher power systems not only improve cutting speed and quality but also offer greater versatility in handling a wide range of material thicknesses and types. As technology continues to advance, the scalability and efficiency of laser cutting machines continue to evolve, meeting the evolving needs of modern manufacturing industries.
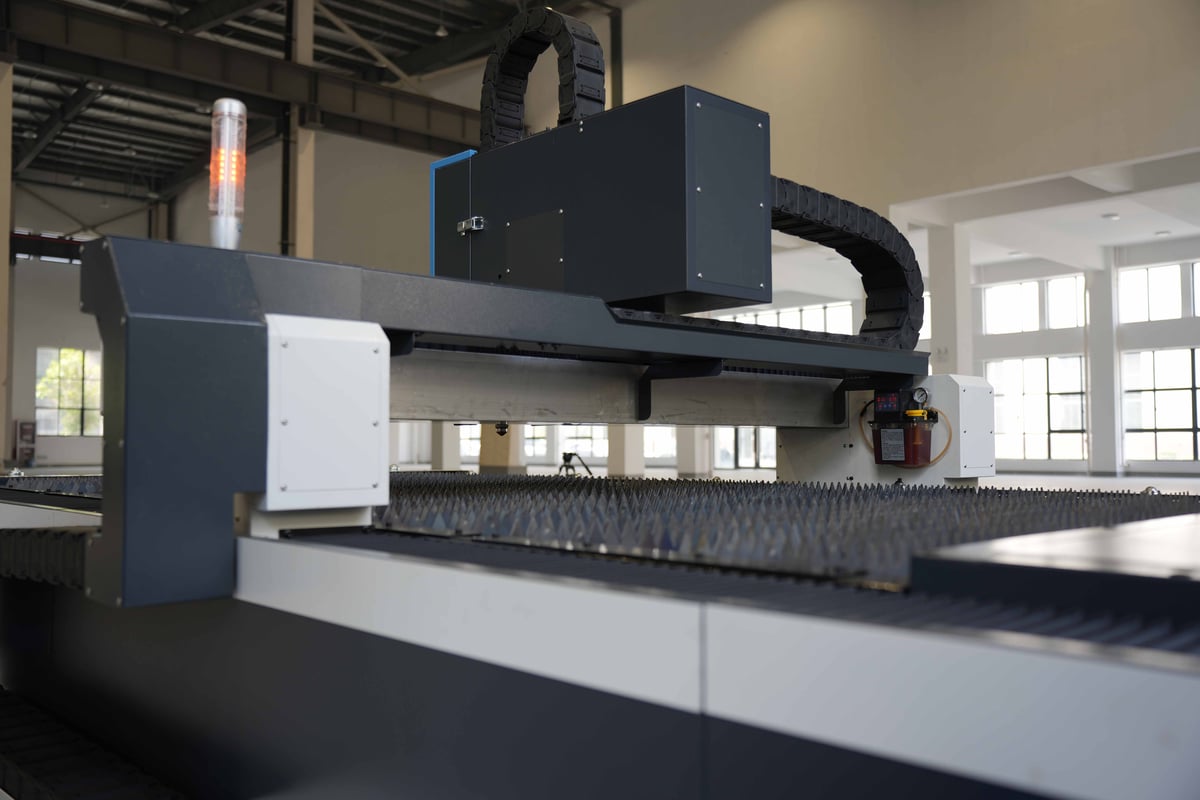
Tips for Choose Proper Power For Metal Cutting
Material Type and Thickness: Different metals require varying laser powers for efficient cutting. For instance, thicker materials like stainless steel or aluminum may necessitate higher power levels to achieve clean cuts.
Cutting Speed and Precision Requirements: Higher laser powers generally allow for faster cutting speeds while maintaining precision. Consider the desired balance between speed and accuracy based on your production needs.
Machine Capability and Technology: Evaluate the capabilities of available laser cutting machines. Modern advancements in fiber laser technology offer a wide range of power options, from lower powers suitable for thin materials to higher powers for thick and high-speed cutting.
Cost and Operational Efficiency: Higher power lasers may offer faster cutting speeds and improved quality, but they also come with increased operational costs. Assess the cost-effectiveness of investing in higher power based on your production volume and requirements.
Application Specifics: Consider the specific applications and industries you serve. Some applications may require specialized cutting capabilities that only higher power lasers can provide.
Does Higher Laser Power Always Translate to Better Cutting Performance?
Not necessarily. While higher laser power generally allows for faster cutting speeds, especially advantageous for thicker metal materials, the actual cutting performance hinges on various factors beyond power alone:
- Material and Thickness Variability: Different metals and thicknesses require specific laser power levels for optimal results. For example, cutting thin materials with excessively high power can lead to over-melting or a wider heat-affected zone, compromising precision and edge quality.
- Precision and Detailing Needs: Cutting intricate designs or detailed patterns demands a balance between power and precision. Excessive power might accelerate cutting speed but could sacrifice fine detailing and accuracy, crucial in industries like electronics or jewelry making.
- Surface Quality and Finish: Even with high power, the quality of the cut largely depends on factors such as beam quality, focal point accuracy, and cutting head design. Improper settings can result in rough edges or material distortion, impacting the final product's quality.
Case Studies and Data Analysis:
- Case 1: In automotive manufacturing, a study comparing 6kW and 12kW fiber lasers showed that while the 12kW laser achieved higher cutting speeds for 10mm stainless steel plates, the 6kW laser produced smoother edges and less material distortion due to better control over the heat-affected zone.
- Case 2: Data from a fabrication workshop demonstrated that for 8mm aluminum sheets, increasing from a 3kW to a 6kW laser improved cutting speed by 40%, but the scrap rate increased due to more frequent burring and rougher cuts at the higher power level.
- Research Insights: Research conducted by laser technology institutes highlights that optimal cutting performance often involves balancing power with beam quality and cutting parameters. Higher power can boost productivity but may require meticulous adjustments to maintain cutting precision and minimize material waste.
In conclusion, while higher laser power can enhance cutting efficiency and speed, achieving the best cutting performance requires a nuanced approach. It involves optimizing parameters like power, speed, and beam quality based on specific material characteristics, application requirements, and desired output quality. Balancing these factors ensures that manufacturers achieve not only faster production but also superior cutting accuracy and surface finish.
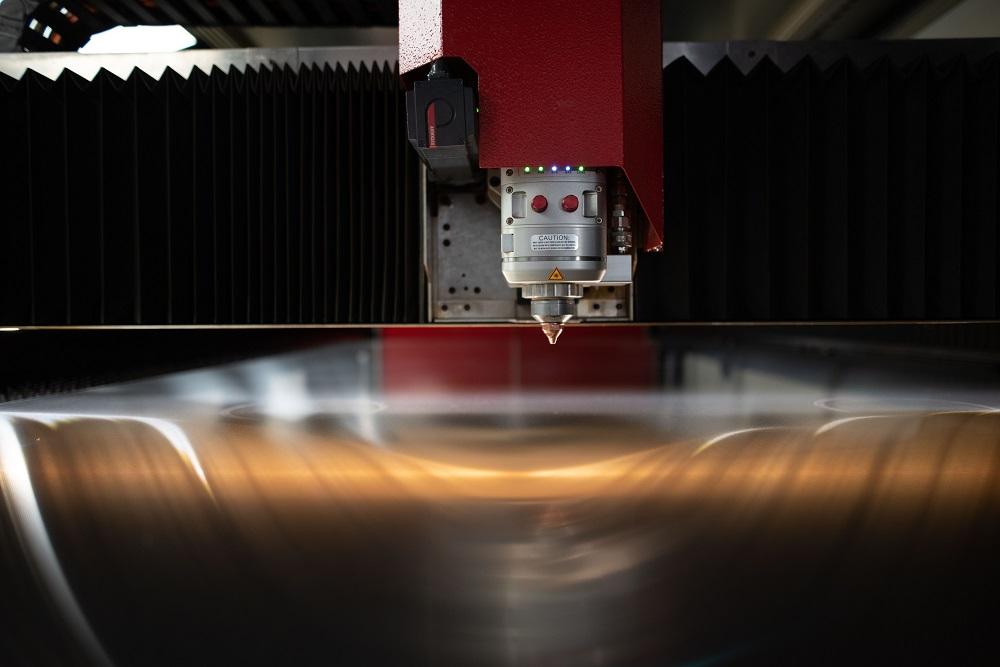
Summary:Unlock Your Laser Cutting Potential with Krrass Laser
Looking for a laser cutter tailored to your specific material cutting needs? Wanna know how thick can 3000W fiber laser cut? At Krrass Laser, we specialize in cutting-edge technology designed to handle a wide range of materials with precision and efficiency. Whether you're working with metals, plastics, ceramics, or other materials, our laser cutting solutions ensure superior quality results for your projects.
Don’t settle for anything less than precision in your projects. Contact Krrass Laser today for expert advice, competitive quotes, and to discover how our advanced laser cutting technology can elevate your manufacturing processes.
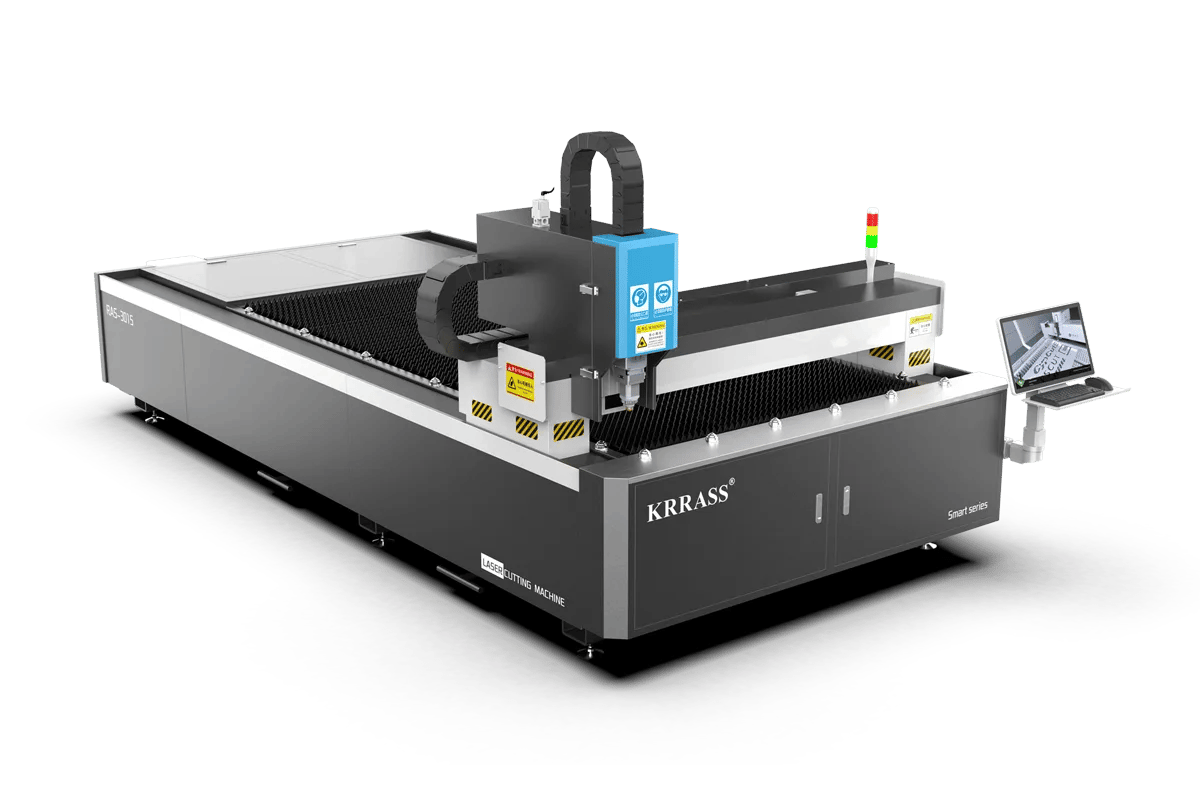