When it comes to metalworking and fabrication, few tools are as versatile and essential as the horizontal press brake. This powerful machine is capable of bending and shaping metal sheets with precision, making it an invaluable asset in a wide range of industries. In this guide, we’ll delve into the workings of a horizontal press brake, explore its various applications, and discuss some crucial considerations for choosing and operating one effectively.
Table of Contents
Types of Press Brake Machine
Press brakes are essential tools in metalworking for bending and forming metal sheets and plates. Each type has distinct features suited for various applications. Here’s an overview of the main types:
1. Hydraulic Press Brakes
- Description: Hydraulic press brakes use hydraulic cylinders filled with oil to apply force to the ram, bending the metal. They are known for their high power and precision.
- Advantages:
- High Force: Capable of handling thick and heavy materials due to the powerful hydraulic system.
- Precision: Advanced CNC systems enable precise control over bending operations.
- Versatility: Suitable for a wide range of bending tasks and materials.
- Applications:
- Heavy-duty metal bending in industries such as aerospace, automotive, and construction.
2. Mechanical Press Brakes
- Description: Mechanical press brakes use a mechanical clutch and flywheel system to deliver force to the ram. They operate with a rotating crankshaft and are driven by a motor.
- Advantages:
- High Speed: Fast operation due to the mechanical drive system.
- Simplicity: Fewer moving parts compared to hydraulic systems, leading to lower maintenance requirements.
- Applications:
- Suitable for high-speed production environments with lighter materials and simpler bending tasks.
3. Electric Press Brakes
- Description: Electric press brakes use servo motors and electric actuators to move the ram. They are known for their energy efficiency and precision.
- Advantages:
- Energy Efficiency: Lower energy consumption compared to hydraulic systems.
- Precision and Control: Offers high precision with programmable controls for detailed bending operations.
- Reduced Maintenance: Fewer hydraulic components reduce maintenance needs.
- Applications:
- Ideal for precision metalworking and applications requiring high accuracy, such as electronics and precision engineering.
4. Hybrid Press Brakes
- Description: Hybrid press brakes combine hydraulic and electric systems. They use hydraulic pressure for force and electric motors for positioning and control.
- Advantages:
- Energy Efficiency: Combines the power of hydraulic systems with the efficiency of electric drives.
- Flexibility: Offers the benefits of both hydraulic and electric press brakes, providing versatility in operation.
- Applications:
- Suitable for a wide range of applications where both high power and precision are required.
5. CNC Press Brakes
- Description: CNC (Computer Numerical Control) press brakes are equipped with computerized controls that automate the bending process. They can be hydraulic, electric, or hybrid.
- Advantages:
- Automation: Automates complex bending tasks, increasing productivity and consistency.
- Precision: High precision with programmable controls, allowing for complex and repeatable bending operations.
- Flexibility: Capable of handling various materials and shapes with ease.
- Applications:
- Used in manufacturing environments where automation and high precision are critical, such as aerospace, automotive, and heavy machinery.
6. Manual Press Brakes
- Description: Manual press brakes require operators to manually adjust the ram and bending die. They are less automated compared to CNC or hydraulic systems.
- Advantages:
- Cost-Effective: Generally less expensive due to the lack of automated systems.
- Simplicity: Simple design with fewer components, making them easier to maintain.
- Applications:
- Suitable for small-scale or hobbyist metalworking, where automation is not a priority.
7. Horizontal Press Brakes
- Description: Horizontal press brakes operate with the ram moving side-to-side rather than up-and-down. They can be hydraulic or electric and are designed to handle long and heavy workpieces.
- Advantages:
- Ease of Handling: Simplifies the handling of long and heavy workpieces, reducing operator fatigue.
- Versatility: Can perform various operations, including bending, punching, shearing, forming, and straightening.
- Safety: Improved safety due to easier material positioning and handling.
- Applications:
- Ideal for manufacturing environments where handling large and heavy materials is common, such as in construction, automotive, and heavy machinery industries.
Definition of Horizontal Press Brake
Horizontal press brakes are sheet metal bending machines which are designed to bend sheet metal from 20 to 100 tonnes. They are generally used for production of large components such as auto bodies, roofs, and truck cabs. The horizontal press brake is a machine that presses the sheet metal into a desired shape by applying pressure on the material with a movable anvil. The machine is operated by two hydraulic cylinders that move the anvil either up or down. This movement causes the pressure on the material to increase or decrease, respectively.
The horizontal press brake is generally used for production of large components such as auto bodies, roofs, and truck cabs. .The material is mounted between the two jaws of the anvil which are attached to a fixed part. The movable cylinder moves up and down the fixed part, and this movement causes the pressure on the material to increase or decrease, respectively. The jaws of anvil are generally made in one piece but some machines have anvils that are made in two pieces
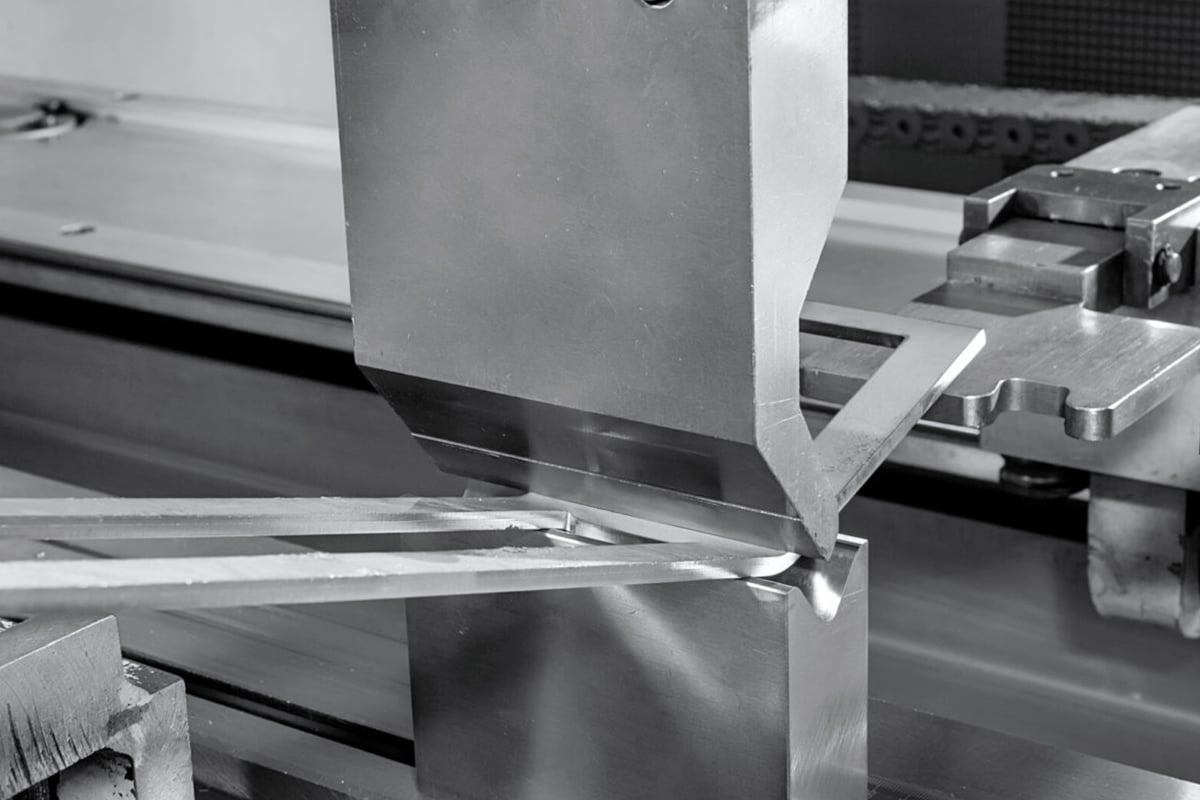
How Does Horizontal Press Brake Works
Components of a Horizontal Press Brake
Frame: The sturdy structure that supports the machine and absorbs the forces generated during operation.
Hydraulic or Electric System: Provides the power needed to move the ram and apply pressure to the workpiece.
Ram: The moving part that exerts force on the workpiece, driven by hydraulic cylinders or an electric actuator.
Die and Punch: Tools used to shape the metal. The die is stationary, and the punch moves with the ram.
Control System: Manages the operation of the machine, often using CNC (Computer Numerical Control) for precise movements and repeatability.
Working Principle
Setup:
The operator places the workpiece (sheet metal) on the machine bed.
The appropriate die and punch are selected and installed based on the desired bend or operation.
Positioning:
The workpiece is positioned between the die and punch. Accurate positioning is crucial for achieving the desired results.
CNC systems can automatically position the workpiece and control the movement of the ram for precision.
Bending Process:
The hydraulic or electric system activates, driving the ram horizontally towards the workpiece.
As the punch presses into the workpiece, it forces the metal into the die, creating a bend or other desired shape.
Control and Precision:
The control system, especially in CNC horizontal press brakes, ensures that the ram moves precisely according to the programmed instructions.
Sensors and feedback mechanisms help maintain accuracy and repeatability, adjusting the force and position as needed.
Completion:
Once the desired operation is completed, the ram retracts, and the operator can remove the formed workpiece.
The machine can then be set up for the next operation.
Horizontal press brakes offer precise and reliable bending capabilities, making them essential tools in the metal fabrication industry. Their efficiency and accuracy make them ideal for a wide range of applications, from small-scale projects to large-scale production. By understanding how a horizontal press brake works, professionals and beginners can make informed decisions when choosing the right machine for their specific needs.
Advantages
Horizontal press brakes offer several advantages over vertical press brakes. One of the key advantages is their efficiency in handling large and heavy workpieces. The horizontal orientation allows for easy manipulation and maneuverability of the material, reducing the risk of damage and increasing productivity.
Another advantage is the improved visibility and accessibility of the workpiece. With the horizontal press brake, operators have a clear line of sight to monitor the bending process, ensuring precise and consistent results. Additionally, the horizontal design allows for better access to the workpiece, making it easier to adjust and fine-tune the bending parameters.
Horizontal press brakes find applications in various industries, including automotive, aerospace, construction, and more. They are commonly used for producing components such as brackets, panels, enclosures, and frames. The ability to create accurate and repeatable bends makes horizontal press brakes a valuable tool in the metal fabrication process.
A horizontal press brake is a versatile machine used in the metal fabrication industry for bending and shaping sheet metal. Its horizontal orientation, efficient handling of large workpieces, improved visibility, and accessibility make it a preferred choice for many professionals in the industry.
Benefits of Owning a Horizontal Press Brake
When it comes to metal fabrication, a horizontal press brake is a valuable tool that offers a range of features and benefits. Here are some key aspects to consider when choosing a horizontal press brake for your specific needs:
1. Versatility: One of the major advantages of a horizontal press brake is its versatility. These machines are designed to bend and shape sheet metal with precision and accuracy. With their adjustable backgauges and various tooling options, horizontal press brakes can handle a wide range of applications, from simple bends to complex shapes.
2. Efficient Handling of Large Workpieces: Horizontal press brakes are specifically designed to handle large workpieces. Unlike vertical press brakes, which have limitations on the size of the material they can handle, horizontal press brakes offer a wider working area and can accommodate larger and heavier sheets of metal. This makes them ideal for projects that require bending or shaping large-size workpieces.
3. Improved Visibility and Accessibility: Another advantage of a horizontal press brake is its design, which provides improved visibility and accessibility. The horizontal orientation allows the operator to have a clear view of the bending process, ensuring precise and accurate results. Additionally, the operator can easily access the machine from all sides, making it easier to load and unload the workpiece and adjust the tooling.
4. Enhanced Productivity and Efficiency: Horizontal press brakes are known for their high productivity and efficiency. These machines are equipped with advanced features such as CNC controls, automatic bending sequences, and programmable backgauges, which streamline the bending process and reduce setup times. This not only increases productivity but also ensures consistent and repeatable results.
5. Wide Range of Applications: Horizontal press brakes find applications in various industries, including automotive, aerospace, construction, and manufacturing. They are used to fabricate a wide range of products, such as enclosures, brackets, frames, and components for machinery and equipment. The versatility and precision of horizontal press brakes make them an essential tool in the metal fabrication process.
A horizontal press brake offers a range of features and benefits that make it a valuable asset in the metal fabrication industry. From its versatility and efficient handling of large workpieces to improved visibility and accessibility, these machines contribute to enhanced productivity and a wide range of applications. When choosing a horizontal press brake, consider these factors to ensure that you select the right machine for your specific needs.
Applications of Horizontal Press Brakes
Bending
Horizontal press brakes are extensively used for various bending operations, including forming angles, channels, and other shapes. They are particularly suitable for handling long and heavy workpieces that can be challenging to manage with a vertical press brake. These machines are employed in manufacturing metal brackets, frames, and structural components, and are widely used in the automotive, aerospace, and construction industries for forming various parts.
Punching and Shearing
Equipped with the appropriate tools, horizontal press brakes can also perform punching (creating holes) and shearing (cutting) operations. This versatility in handling different tasks makes them valuable in workshops and manufacturing plants. Applications include creating holes (punching) for installation or assembly purposes and cutting metal sheets (shearing) to desired sizes and shapes.
Forming and Straightening
Horizontal press brakes are also used for forming complex shapes and straightening bent parts. They are essential for maintenance and repair tasks where precision and flexibility are required. Applications include straightening bent or damaged parts in repair shops and specific forming operations during manufacturing, such as creating complex metal shapes or curves.
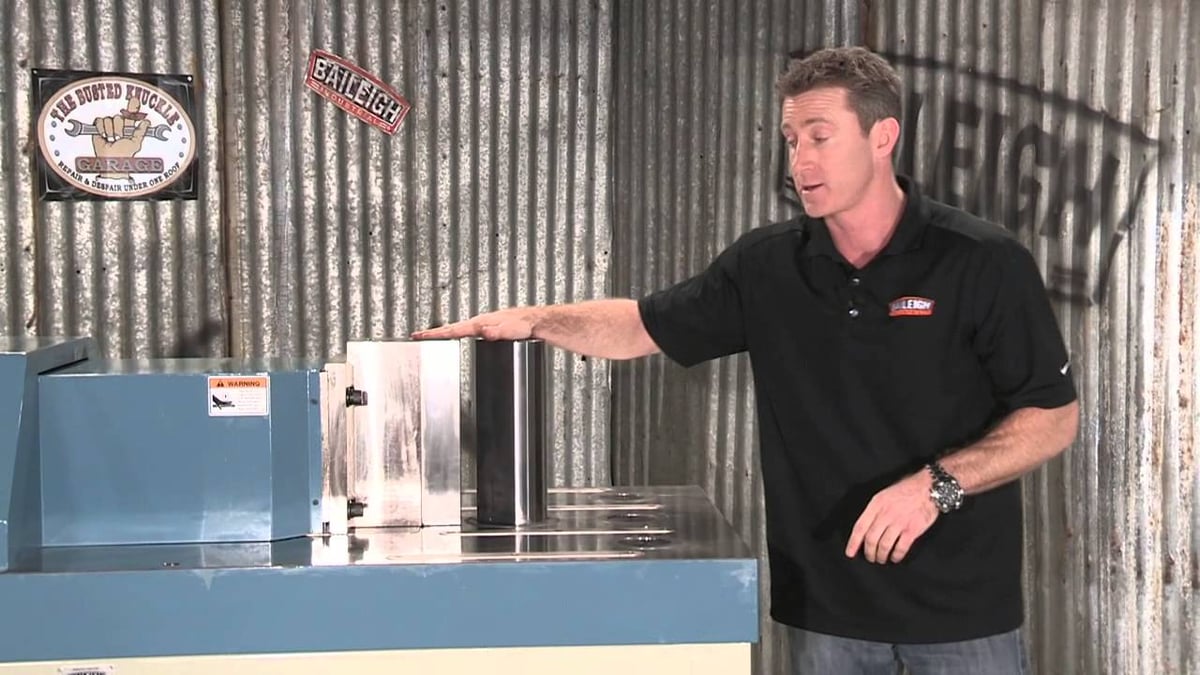
Hydraulic vs Horizontal Press Brake: Differences Analysis
Why do some industries prefer hydraulic press brakes, while others opt for horizontal press brake machines? The choice often boils down to the distinct advantages each offers in terms of precision, efficiency, and versatility. Let's explores the key differences between hydraulic press brakes and folding machines, helping you understand their unique applications and benefits. By the end, you’ll know which machine suits your needs and why.
1. Operating Mechanism
Hydraulic Press Brake
- Mechanism: Hydraulic press brakes use hydraulic cylinders filled with oil to apply force to the ram. When the hydraulic pump activates, it pushes the oil into the cylinders, creating pressure that moves the ram. This force is then transferred to the metal workpiece, bending it into the desired shape.
- Power Source: The hydraulic system relies on pumps and motors to generate the necessary pressure. The hydraulic fluid, usually oil, transmits power throughout the system. This setup ensures a consistent and powerful force, making hydraulic press brakes ideal for heavy-duty applications.
- Movement: Typically, hydraulic press brakes operate in a vertical direction, with the ram moving up and down. This vertical movement allows for precise control over the bending process, ensuring high accuracy and repeatability. The vertical design also facilitates the handling of a wide range of workpiece sizes and shapes.
Horizontal Press Brake
- Mechanism: Horizontal press brakes utilize either hydraulic or electric systems to apply force to the ram. In hydraulic versions, similar to vertical hydraulic press brakes, oil pressure drives the movement. Electric versions use motors and actuators to achieve the same effect. The choice between hydraulic and electric systems depends on the specific application requirements, with each offering unique benefits in terms of power, speed, and control.
- Power Source: The power source for horizontal press brakes can be either hydraulic or electric. Hydraulic systems provide high force and are suitable for heavy-duty applications, while electric systems offer precise control and energy efficiency. This flexibility allows horizontal press brakes to be adapted to various tasks and industries, making them highly versatile.
- Movement: Horizontal press brakes operate with the ram moving side-to-side, rather than up and down. This horizontal movement is particularly advantageous for handling long and heavy workpieces, which can be cumbersome to manipulate in a vertical press brake. The horizontal design simplifies the positioning and processing of large materials, reducing operator fatigue and improving safety.
2. Applications
Hydraulic Press Brake
- Bending: Hydraulic press brakes excel in standard bending operations, making them ideal for forming various shapes including angles, channels, and complex contours. The hydraulic system's ability to provide high force allows for precise and reliable bending of thick and rigid materials.
- Punching and Shearing: While hydraulic press brakes can be equipped with additional tools for punching (creating holes) and shearing (cutting), these functions are less common compared to their primary bending application. The integration of punching and shearing tools can be advantageous for tasks that require multifunctional capabilities, but hydraulic press brakes are predominantly known for their bending prowess.
- Heavy-Duty Work: Hydraulic press brakes are particularly suited for heavy-duty and high-force applications due to their robust hydraulic systems. The powerful hydraulic pressure can handle substantial workpieces and demanding tasks, making them ideal for industries that require significant force and durability.
Horizontal Press Brake
- Bending: Horizontal press brakes are designed to handle bending operations efficiently, particularly for long and heavy workpieces. The horizontal movement of the ram simplifies the handling of large materials that would be challenging to manage with a vertical press brake. This design is advantageous for applications requiring the processing of large and cumbersome components.
- Punching and Shearing: Horizontal press brakes offer greater versatility in performing punching and shearing tasks. The ability to integrate various tools allows them to handle a wider range of operations beyond just bending. This makes horizontal press brakes valuable in workshops and manufacturing plants where multiple tasks need to be accomplished with a single machine.
- Forming and Straightening: In addition to bending and cutting, horizontal press brakes are frequently used for forming complex shapes and straightening bent parts. This makes them particularly useful in maintenance and repair applications, where precision and flexibility are crucial. Their ability to handle diverse tasks contributes to their effectiveness in both manufacturing and repair settings.
3. Precision and Control
Hydraulic Press Brake
- Precision: Hydraulic press brakes offer high precision, especially when equipped with advanced CNC (Computer Numerical Control) systems. These systems enable accurate control over the bending process, ensuring that complex shapes and fine details are achieved with minimal deviation.
- Control: The hydraulic system provides good control over both force and movement, making it suitable for detailed work. The ability to fine-tune pressure and movement allows for consistent and reliable bending results, even for intricate designs.
Horizontal Press Brake
- Precision: Horizontal press brakes are equally precise when equipped with CNC systems. The horizontal design benefits certain tasks, such as handling long workpieces and providing stability during bending, which can enhance overall precision.
- Control: Offers excellent control, particularly for tasks that require horizontal force application. The horizontal movement allows for precise alignment and manipulation of workpieces, improving accuracy and efficiency in handling complex operations.
4. Ease of Operation
Hydraulic Press Brake
- Ease of Handling: The vertical design of hydraulic press brakes can make handling large and heavy workpieces challenging. The upward and downward movement requires careful positioning of materials, which may complicate the handling process.
- Operator Fatigue: The vertical setup can contribute to greater operator fatigue, especially when dealing with heavy or cumbersome materials. Frequent adjustments and handling of large pieces may lead to increased physical strain.
Horizontal Press Brake
- Ease of Handling: The horizontal design simplifies the handling of long and heavy workpieces, as materials are positioned horizontally rather than vertically. This design reduces operator fatigue and facilitates easier material positioning.
- Safety: Improved safety is a notable advantage of the horizontal design. The ability to handle materials with less manual lifting and positioning minimizes the risk of accidents and enhances overall workplace safety.
5. Versatility
Hydraulic Press Brake
- Versatility: Hydraulic press brakes are highly versatile for bending operations, capable of handling a range of shapes and sizes. However, they are less versatile in tasks like punching and shearing, which may require additional tooling and setups.
- Tooling: Requires specific tooling for different tasks, which can add complexity and time to switch between various functions. This necessity for specialized tools can impact operational efficiency and flexibility.
Horizontal Press Brake
- Versatility: Horizontal press brakes offer greater versatility across multiple operations, including bending, punching, shearing, forming, and straightening. This adaptability makes them suitable for a wide range of tasks within manufacturing and repair environments.
- Tooling: Easier to switch between different tools for various tasks, enhancing operational flexibility and efficiency. The design accommodates quick changes in tooling, allowing for a more streamlined workflow.
6. Cost and Maintenance
Hydraulic Press Brake
- Cost: Generally more expensive due to the complexity of the hydraulic system and its components. The high initial cost reflects the advanced technology and power capabilities of hydraulic press brakes.
- Maintenance: Requires regular maintenance of hydraulic components, such as oil changes and seal replacements. Routine upkeep is essential to ensure optimal performance and longevity of the equipment.
Horizontal Press Brake
- Cost: Can be less expensive, particularly if powered by electric systems rather than hydraulic. The lower cost of electric models contributes to reduced initial investment and operational expenses.
- Maintenance: Maintenance is simpler for electric-powered horizontal press brakes, with fewer components requiring regular attention. Hydraulic versions still need periodic maintenance, but overall upkeep tends to be less complex compared to hydraulic systems.
Summary
Hydraulic Press Brakes Offer high precision and control for bending operations but may present challenges in handling large workpieces and can lead to operator fatigue. They are highly versatile for bending but less so for other tasks and tend to be more expensive with higher maintenance requirements. Horizontal Press Brakes: Provide excellent ease of operation, especially for handling long and heavy workpieces, with improved safety and reduced operator fatigue. They offer greater versatility across multiple tasks and are generally less expensive with simpler maintenance if electric-powered.
Top Manufacturers of Horizontal Press Brakes
When it comes to choosing a horizontal press brake, it’s important to consider the reputation and reliability of the manufacturer. Here are some of the top manufacturers in the industry:
- Amada – Amada is a well-known name in the metal fabrication industry, offering a wide range of high-quality press brakes. Known for their precision and durability, Amada press brakes are trusted by professionals worldwide.
- Trumpf – Trumpf is another reputable manufacturer that produces top-of-the-line horizontal press brakes. With advanced technology and innovative features, Trumpf press brakes deliver exceptional performance and accuracy.
- Bystronic – Bystronic is a global leader in the manufacturing of metal fabrication machinery, including horizontal press brakes. Their machines are known for their efficiency, versatility, and cutting-edge technology.
- LVD – LVD is a trusted brand that has been producing reliable press brakes for decades. Their machines are known for their robust construction, ease of use, and high bending accuracy.
- Durma – Durma is a leading manufacturer of press brakes, offering a wide range of models to suit different bending requirements. Their machines are known for their solid build, precision, and user-friendly interface.
Each of these manufacturers has a strong track record of producing high-quality horizontal press brakes that meet the demands of the metal fabrication industry. When considering which manufacturer to choose, it’s important to evaluate factors such as machine capabilities, technological advancements, customer support, and overall reputation. By selecting a press brake from one of these top manufacturers, you can have confidence in the performance and reliability of your machine.
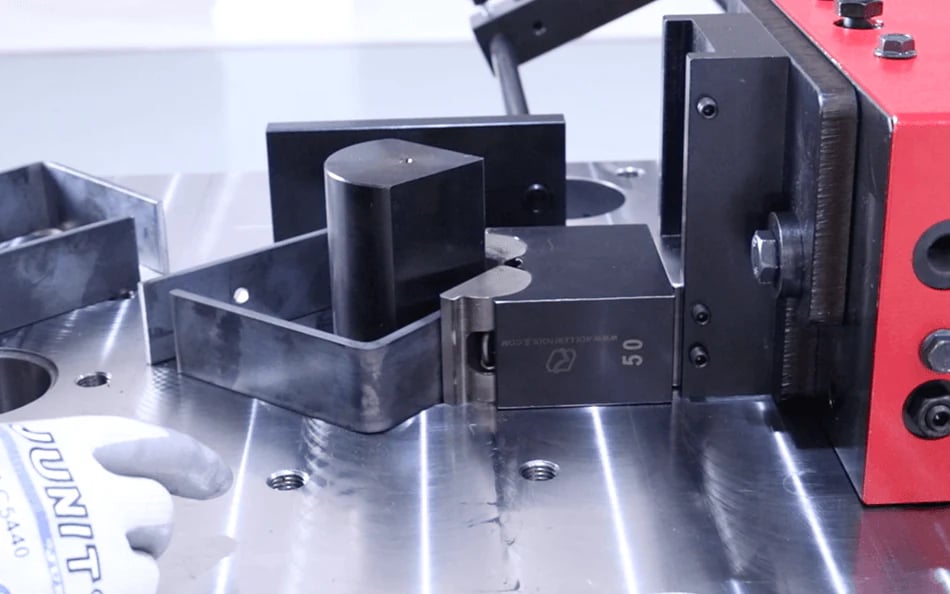
Conclusion
A horizontal press brake is an essential tool in the metal fabrication industry. Its precision and reliability make it a valuable asset for bending sheet metal with accuracy and efficiency. By following the steps outlined in this article, including clamping the sheet metal, selecting the appropriate bending tool, and using a back gauge system, operators can achieve precise bends to meet their specific requirements.
When choosing a horizontal press brake, it is crucial to consider several factors. Bending capacity, tonnage, accuracy and precision, tooling options, and ease of use and safety features are all important considerations. Additionally, it is vital to select a reputable manufacturer known for producing high-quality machines. Manufacturers such as Amada, Trumpf, Bystronic, LVD, and Durma have established themselves as leaders in the industry, offering reliable and durable press brakes.
By understanding the workings of a horizontal press brake and considering the key factors in choosing the right machine, metal fabricators can optimize their operations and achieve superior results. Whether it’s bending simple parts or complex components, a horizontal press brake is an indispensable tool for any metal fabrication workshop.