When it comes to metal fabrication, a stainless steel bending machine is an essential tool for shaping and forming stainless steel into precise, custom designs. Whether you're working with thin sheets or thick plates, these machines allow fabricators to achieve accurate bends, which are crucial for a wide range of applications, from industrial equipment to architectural elements. Understanding the capabilities, features, and best practices for using a stainless steel bending machine is key to ensuring high-quality results and improving production efficiency. In this guide, we’ll explore the fundamentals of stainless steel bending, key considerations when selecting the right machine, and tips for optimizing your bending processes in metal fabrication.
What Is Sheet Metal Bending?
Sheet metal bending involves using machines and tools to form metal into a specific shape. This can be achieved through the use of a press brake, punching machine, ironworker, or other machinery.
These machines utilize a power system to drive the tooling and apply pressure on the metal sheet, causing it to deform. To ensure accurate results in sheet metal bending, several parameters must be determined before the process begins.
These parameters include the material thickness, bending radius, bending allowance, bending deduction, K factor, and others. It is important to keep in mind that different materials have varying properties such as tensile strength and ductility.
Different machines may use different bending methods to produce the same profile from a metal sheet. Therefore, it's crucial to choose the right machine and approach based on the specific requirements and parameters of the project.
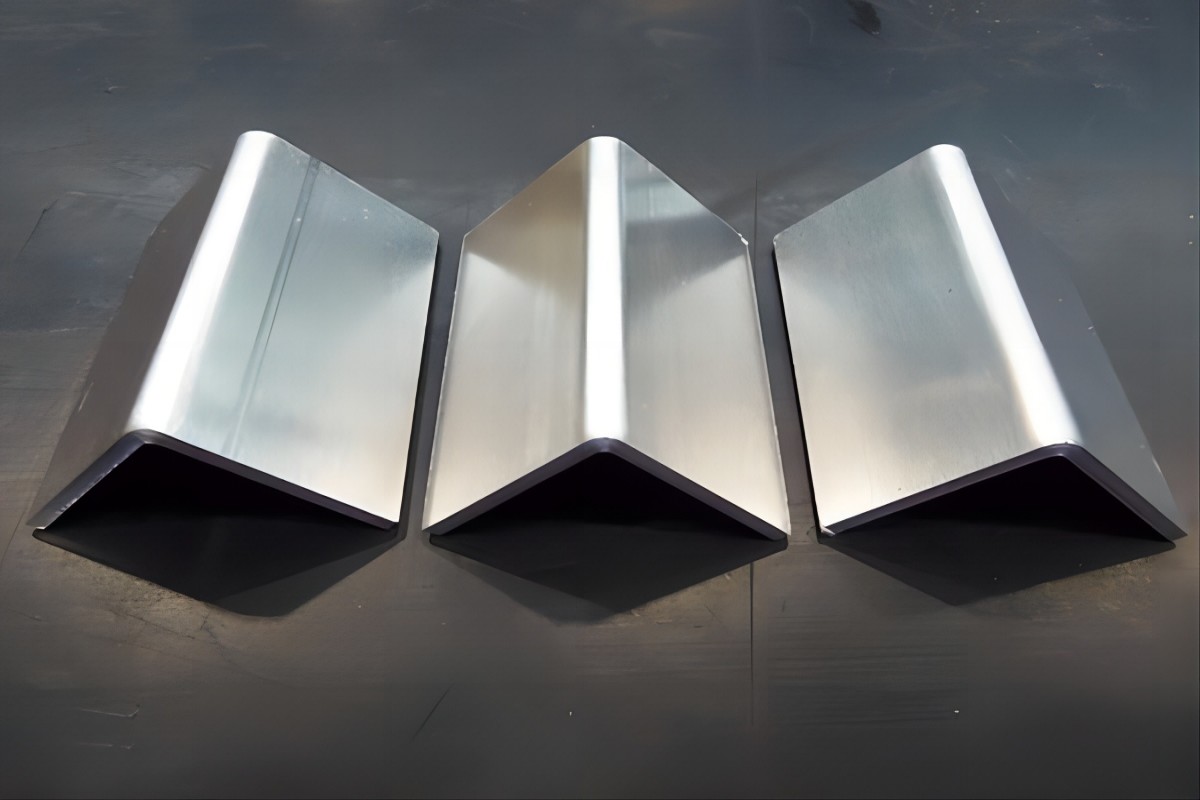
What Are the Methods of Sheet Metal Bending?
The sheet metal bending process results in different bending shapes based on the angle and radius of the bend. To ensure precision in the bending process, standard bending methods are employed. These methods vary, but they all aim to produce uniform standards in the final profiles.
Let's take a look at some of the main bending methods in sheet metal bending:
V Bending - This is the most common bending process and is named so because of the V-shaped punch and die used in the process. The punch presses the metal sheet into the lower die, resulting in a V-shaped workpiece.
Roll Bending - This process is used for bending workpieces with large curls and involves the use of three rolls driven by a hydraulic system to bend the sheet.
U-Bending - This method involves using a U-shaped die to bend the workpiece. The punch is powered by a system to press the metal sheet into the U-shaped die, resulting in U-shaped profiles.
Rotary Bending - This method can bend sheet metal with a degree of more than 90. The final profile is similar to a V-bend, but the profile surface is smoother.
Edge Bending - This method is used in panel bending and involves the use of upper and lower molds that move up and down for bending. It's usually used for shorter metal sheets to reduce sharpness and prevent damage to the bending edge.
Wipe Bending - This method is similar to edge bending. The metal sheet is placed on the lower die and pressure is applied to the protruding metal by a pressure pad and punch, resulting in bending.
What Materials Are Fit for Sheet Metal Bending?
The choice of material for bending is crucial for achieving desired bending results in sheet metal fabrication. Some materials may not be suitable for bending and could result in fracture or damage to the tooling. Materials with low ductility can be heated to reduce the risk of fracture.
When selecting materials for bending, it's important to consider their characteristics. Here are some common materials used in sheet metal bending and their properties:
- Carbon steel: This material is strong and flexible with good ductility, and is an environmentally friendly option that can be recycled.
- Mild steel: Mild steel has excellent ductility, which allows it to bend smoothly without heating.
- Stainless steel: This material is strong, corrosion-resistant, and has high tensile and yield strength, making it a popular choice for bending.
- Titanium: Titanium has a high tensile strength but can be prone to damage the tooling if not used properly. When bending titanium, it is necessary to increase the internal bending radius to prevent cracking and to overbend the material to achieve the desired shape.
- Aluminum: Aluminum is prone to cracking when bent, so it's important to anneal it to prevent cracking. When bending aluminum, it's important to avoid over-bending to reduce the risk of cracking.
- Copper: Copper has high ductility, making it a great choice for bending, and is cost-effective. It is widely used in the sheet metal processing industry.
Stainless Steel Metal Bending
Features of Stainless Steel
Steel is a combination of materials, including small amounts of carbon, manganese, silicon, copper, phosphorus, sulfur, and oxygen. It is classified based on the carbon content as high, medium, low, and ultra-low carbon steel.
Steel can be bent easily as the tools used for bending steel plates are also made of steel. However, bending stainless steel requires a relatively larger force due to its high yield strength, hardness, and poor ductility.
Additionally, stainless steel's springback after bending is significant, requiring a larger bending radius to avoid cracking the workpiece.
2. Considerations for Bending Stainless Sheet
Plate Thickness and Bending Tonnage Before bending stainless steel, it is essential to determine the thickness of the stainless steel. Thicker plates require a larger bending machine.
Bending Angle and Bending Radius
The bending angle and radius are crucial to consider in the metal manufacturing industry. A larger bending radius may result in excessive springback, while a smaller radius may cause cracking.
Generally, the bending radius is around 0.2. For materials like high-carbon steel, a larger inner radius is necessary to prevent cracking. Stainless steel has high resilience, and the bending angle and radius cannot be too small.
Bending Springback
The springback of a metal plate is proportional to the material's yield strength and inversely proportional to its elastic modulus. Low-carbon steel has less springback and is ideal for high-precision workpieces, while high-carbon steel and stainless steel have significant springback.
The larger the bending radius, the greater the springback. Smaller bending radii result in higher accuracy.
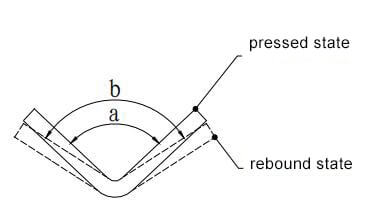
Calculating the Bending Allowance
The bending allowance, which is the expansion of the outer side of the sheet, can be calculated with the knowledge of the sheet thickness, bending angle, and inner radius.
This calculation determines the required length of the sheet for bending. The formula for calculating the bending allowance is: BA=(π/180) x B x (IR+K x MT), or use a bending allowance gauge.
Bending with Machines
Finally, a machine like a press brake can be used for bending processing. If the metal sheet is prone to cracking, it can be hot-formed or annealed.
Annealing improves the ductility of metals by softening them, and hot bending involves heating the metal to a red state and then bending it.
How to Bend Stainless Steel Sheet Metal Without a Brake?
First, gather the necessary materials including stainless steel plates, hammers, vises, rulers, protractors, and markers. Use the ruler to measure the plate's thickness, calculate the K factor and inner radius, and then determine the bend allowance using the formula BA=(π/180) x B x (IR+K x MT).
Use the protractor and marker to mark the bending line and radius on the plate. Cut the stainless steel plate to the appropriate size, and use the vise to bend the plate to the desired angle.
Ensure an even bend by striking the metal with a wooden hammer. Check the bend angle and bend allowance for accuracy. If necessary, you can assist the bend by heating the metal.
4. How to Calculate Bend Allowance?
Remember that bending the metal under pressure will result in internal compression and external stretching. When calculating the bend dimension, be sure to take into account the bend allowance which is dependent on the sheet thickness, inner radius, K factor, and bending angle.
The formula to calculate the bend allowance is BA=(π/180) x B x (IR+K x MT), where K is the K factor, B is the bending angle, IR is the internal radius, and MT is the plate thickness.
Stainless Steel Bending Grades
The most common grades used for stainless steel tube bending include 304 stainless steel and 316 stainless steel. The material grade you choose determines the type of bending process used along with the radius that can be achieved without damaging the tube.
304 Stainless Steel
304 stainless steel is one of the most common SS grades due to its versatility, corrosion resistance, and non-magnetic properties. However, its toughness may present challenges for tube bending without the proper tooling and equipment. 304 stainless steel can be used to create machining equipment, food processing equipment, aerospace components, hospital and medical devices, and more.
316 Stainless Steel
316 stainless steel contains added molybdenum for enhanced corrosion resistance and superior strength at high temperatures. While 316 is also very tough, it is ideal for use in corrosive, harsh environments, such as marine applications, chemical processing, pharmaceutical and medical applications, and more.
The stainless steel grade you choose depends on the requirements of your application. Triad also provides other stainless steel grades as specified by the customer. Contact us for help determining the best material grade for your application.
Stainless Steel Bending Machine Bending Thickness Explained
1. Thin Sheets (< 3mm)
1) Characteristics and Challenges
Thin stainless steel sheets, those less than 3mm thick, are relatively easy to bend but come with their own set of challenges. The primary concern is avoiding over-bending, which can lead to cracking or other deformities.
2) Best Practices
- Bend Radius: For thin sheets, a bend radius of at least 1x the material thickness is recommended to prevent cracking.
- Springback: While thin sheets exhibit minimal springback, it is still essential to account for it. Slight over-bending can help achieve the desired angle.
- Tool Selection: Utilize smaller V-die openings and lower bending forces. Precision is key, and the right tools can make all the difference.
2. Medium Thickness Sheets (3mm - 6mm)
1) Characteristics and Challenges
Medium thickness sheets, ranging from 3mm to 6mm, require more force and careful handling. The risk of springback is more pronounced, necessitating precise adjustments.
2) Best Practices
- Bend Radius: A bend radius of 1.5x to 2x the material thickness is advisable to avoid material stress and cracking.
- Springback: Medium thickness sheets have a noticeable springback effect. Over-bending by a calculated amount can help counteract this.
- Tool Selection: Use medium-sized V-die openings and appropriate bending forces. Ensuring the press brake is correctly calibrated is crucial for accuracy.
3. Thick Sheets (> 6mm)
1) Characteristics and Challenges
Thick stainless steel sheets, those over 6mm, present significant challenges due to their rigidity and the high forces required to bend them. The risk of material cracking and significant springback must be managed carefully.
2) Best Practices
- Bend Radius: For thick sheets, a bend radius of 2x to 3x the material thickness is necessary to prevent cracking and ensure a smooth bend.
- Springback: Thick sheets exhibit substantial springback. Accurate over-bending and multiple hits may be required to achieve the correct angle.
- Tool Selection: Large V-die openings and high bending forces are essential. Heavy-duty press brakes with advanced control systems are recommended to handle the increased demands.
4. Types of Stainless Steel
1) 304 Stainless Steel
Characteristics
304 stainless steel is the most commonly used type, known for its excellent corrosion resistance and good formability.
Bending Considerations
- Springback: 304 stainless steel has a moderate springback effect. Over-bending slightly can help achieve the desired angle.
- Tool Selection: Standard V-dies and punches are typically sufficient, but ensuring the press brake is well-calibrated is essential.
2) 316 Stainless Steel
Characteristics
316 stainless steel contains molybdenum, providing superior corrosion resistance, especially in marine and chemical environments.
Bending Considerations
- Springback: 316 stainless steel is stronger and harder, resulting in a higher springback effect. Precise over-bending is necessary.
- Tool Selection: Higher forces and larger bend radii are required. Specialized tools may be needed to handle the increased strength.
3) High Carbon Stainless Steel
Characteristics
High-carbon stainless steel offers increased strength and hardness but reduced ductility, making it more prone to cracking.
Bending Considerations
- Springback: Significant springback requires careful over-bending and multiple hits.
- Tool Selection: Larger V-die openings and higher forces are necessary. Preheating the material can reduce the risk of cracking.
4) Low Carbon Stainless Steel
Characteristics
Low carbon stainless steel is more ductile and easier to bend, making it suitable for complex shapes and tight bends.
Bending Considerations
- Springback: Minimal springback makes it easier to achieve precise bends.
- Tool Selection: Standard tools and lower forces are typically sufficient.
How to Choose The Right Stainless Steel Bending Machine?
Choosing the right stainless steel bending machine for your needs depends on several factors, including the specific type of stainless steel you work with, the complexity of your projects, production volume, and your budget. Here are key considerations to help you select the best stainless steel bending machine:
1. Determine Your Bending Requirements
- Type of Bending: Are you looking to perform simple bends, or more complex ones such as box or channel bending? Some machines are designed for specific bending types (e.g., angle, U-bending, or round tube bending).
- Bending Angle: Determine the maximum angle of bend required for your workpieces. Some machines have adjustable bending angles while others have fixed ones.
- Material Thickness: Stainless steel comes in various thicknesses, so you need to choose a machine that can handle the thickness you work with regularly. Be sure to check the machine’s rated capacity for bending different thicknesses of stainless steel.
2. Consider the Type of Machine
There are several types of machines you can choose from depending on your application:
- Press Brake (Mechanical or Hydraulic): Ideal for bending thick sheets of stainless steel. Hydraulic press brakes offer more flexibility in terms of bending force and are better for more complex tasks, while mechanical press brakes are typically faster and better for high-volume, less intricate bending.
- Roll Benders: Great for bending large diameter pipes or round shapes. Suitable for cylindrical or conical bends.
- Mandrel Benders: Often used for more complex or precise bending requirements, especially in applications like exhaust systems or tubes where maintaining the internal diameter is important.
- Plate Benders: These are typically used for larger plates of stainless steel and are great for creating uniform bends.
3. Bending Capacity (Force and Length)
- Bending Force: The machine should have the required tonnage to bend your stainless steel sheet or plate. This is determined by the thickness, length, and material hardness.
- Bending Length: Check the length of the material the machine can handle. Some machines have adjustable beds to accommodate longer pieces, while others are fixed.
4. Precision and Accuracy
For high-precision bending, look for a machine with advanced controls and the ability to adjust for precise bending angles. CNC (Computer Numerical Control) bending machines allow you to set up and control complex bends with high precision.
5. Control System
- Manual vs. CNC: If your operation involves complex or varied bending tasks, a CNC-controlled bending machine can improve precision and efficiency. Manual machines are typically simpler but require more operator skill.
- Programming Flexibility: Consider whether you need to program multiple bend sequences. CNC machines allow you to input programs and automate processes, which reduces setup time for multiple bends and increases production efficiency.
6. Machine Build Quality and Durability
Stainless steel bending can be tough on equipment, so choose a machine made from high-quality materials (e.g., high-strength steel) to ensure long-term durability and stability. Look for a machine with solid construction and proven reliability in high-demand applications.
7. Hydraulic vs. Mechanical Systems
- Hydraulic Bending Machines: These offer more flexibility and power for bending thicker materials or for making deeper bends. Hydraulic press brakes are often preferred for complex or high-volume operations.
- Mechanical Bending Machines: These are generally faster and less expensive than hydraulic models, but they may not offer the same force or precision for thick or intricate bends.
8. Safety Features
Safety is crucial, especially when working with heavy stainless steel sheets. Look for machines with built-in safety features like light curtains, safety mats, and emergency stop functions. Ensure the machine complies with the relevant safety standards in your region.
9. Operator-Friendly Features
Consider a machine with easy-to-use controls, especially if you're not experienced in metalworking. Features like digital readouts, automatic back gauges, and programmable controls can simplify the setup process.
10. Space and Budget Constraints
- Machine Size: Make sure the machine fits your workshop or production area. Consider the machine's footprint and ensure you have adequate space for installation, operation, and maintenance.
- Budget: Your budget will play a key role in your decision. CNC machines tend to be more expensive upfront, but they can offer greater precision, speed, and automation. Weigh the upfront cost against long-term productivity gains.
11. After-Sales Support and Service
Choose a manufacturer or dealer who provides good after-sales support, including training, maintenance, and access to spare parts. Check reviews or ask for references from other users to ensure the machine’s reliability and the manufacturer's reputation.
12. Energy Efficiency
In today’s environment, energy-efficient machines are a priority for many companies. Check the machine’s energy consumption and consider investing in energy-efficient models if long-term operating costs are a concern.
13. Brand and Manufacturer Reputation
Established brands tend to offer better quality and after-sales support. Research different brands and models to compare performance, features, and user feedback.
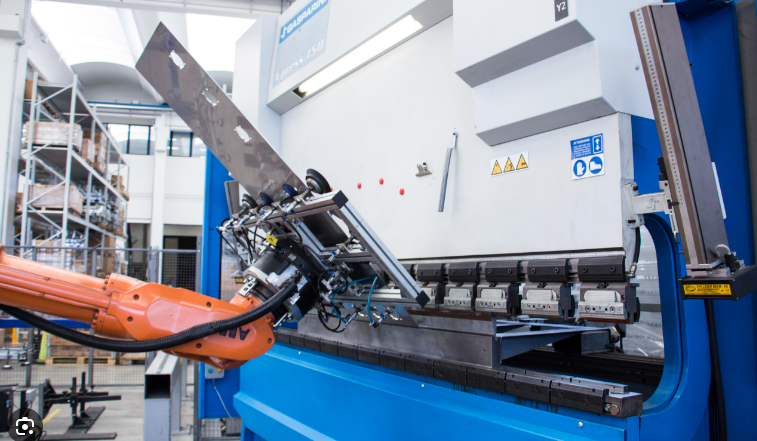
Considerations to Keep in Mind for Your Custom Steel Tubing Project
When starting a custom steel tubing project, there are several critical factors to consider:
- Bend Radius: Tight radius bends often require specialized bending methods, such as rotary draw or roll bending. To prevent wall collapse, a mandrel can be used for support during the bending process.
- Yield Strength: Stainless steel’s high yield strength increases the likelihood of springback. It's essential to account for this potential distortion when calculating the amount of strain during the bending process.
- Material Thickness: The thickness of the tube directly affects the bending force required. Thicker tubes demand more force, while thinner ones are more prone to collapsing. This factor is crucial in determining the right tooling setup.
- Welded vs. Extruded: Both welded and extruded tubing can be bent, but they each have specific advantages. Seamless (extruded) tubing is ideal for tight radius bends, while welded tubing is more suitable for larger diameters or less intricate bending requirements.
Stainless Steel Tube Bending Methods
Stainless steel can be bent using a variety of different methods. The best method for your process will depend on the shape and radius you want to achieve. Common stainless steel tube bending methods include:
Rotary Draw Bending
Rotary draw bending involves clamping the exterior of a stainless steel tube or pipe and forming it around a die until the desired bend radius is achieved. This process is ideal for high precision components and tight radius bends.
Three Roll Bending
In roll bending, three rollers are used to gradually bend a stainless steel pipe or tube by applying pressure at specific points as the material is fed through the machine. Three roll bending is typically used to achieve large radius bends.
Mandrel Bending
Mandrel bending is similar to rotary draw bending, but instead uses a mandrel to provide internal support while the tube is bent around the die. Mandrel bending is used to maintain the roundness of the tube and prevent collapse.
Compression Bending
Compression bending involves clamping the stainless steel tube around a stationary die and then pulling the material around it to form the bend. This process is fast, but should not be used when tight radius bends are a priority.
Ram Bending
Ram bending uses a hydraulic ram to bend stainless steel tubing in multiple locations as it is braced against a pivot block or roller. This process is easy and cost-effective, but is not ideal for applications that require a tight tolerance.
Summary
In this blog post, we've covered the fundamentals of sheet metal bending, with a particular emphasis on key considerations when bending stainless steel. Whether you're performing simple bends or more complex operations, a variety of machines—such as stainless steel bending machines and press brakes—can help achieve precise results. For basic bending tasks, even a vise can serve as a cost-effective solution.
KRRASS is a trusted manufacturer with over 20 years of experience in the sheet metal processing industry. If you're looking for a stainless steel bending machine or other metalworking machinery, don't hesitate to contact one of our sales representatives for more details about our products and pricing.