Press Brakes Explained
أ مكابح الضغط is a machine tool used in metalworking and manufacturing processes to bend and shape sheet metal. Its primary purpose is to apply a force to a workpiece, typically a sheet of metal, in order to bend or form it into a desired shape. The press brake operates by using a punch and die to exert force on the material, causing it to deform.
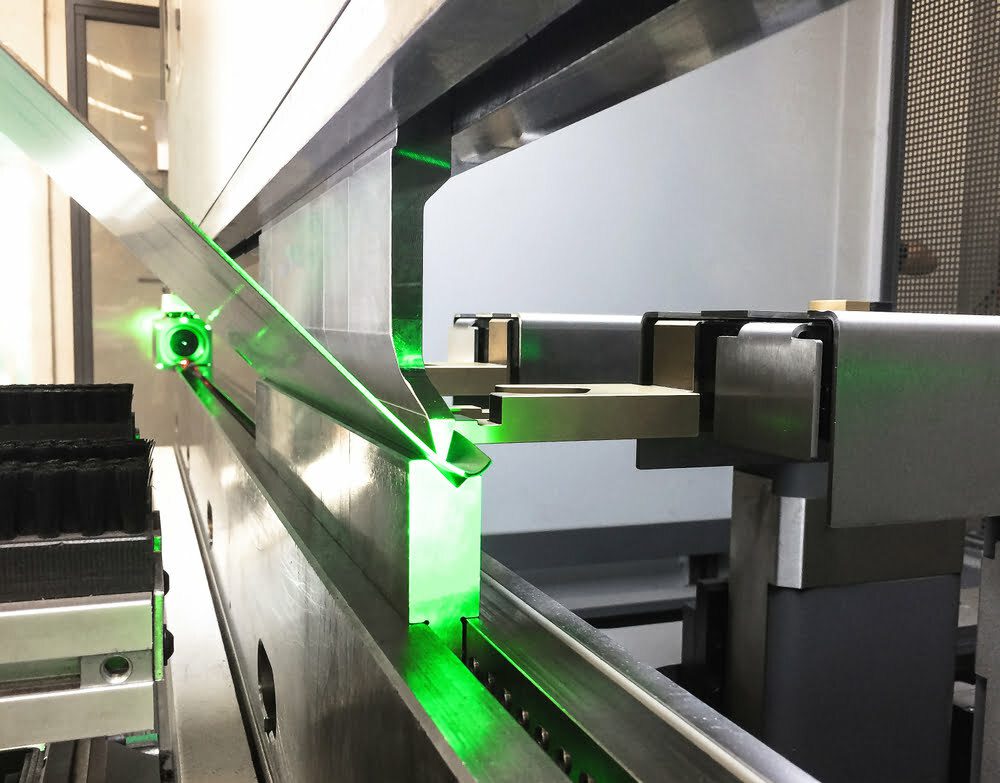
WHAT IS A PRESS BRAKE, AND WHAT DOES IT DO?
Key purposes and functions of a press brake include:
Bending: The primary function is to bend sheet metal to create various shapes and angles. This is crucial in the fabrication of components for a wide range of industries, including automotive, aerospace, construction, and more.
Precision: Press brakes are known for their accuracy and repeatability, allowing manufacturers to produce consistent and high-quality parts with precise dimensions.
التنوع: Press brakes can handle a variety of materials, including different types of metals and alloys. They can be used for a range of applications, from simple bends to complex forms.
Sheet Metal Forming: Besides bending, press brakes are also used for other sheet metal forming processes, such as blanking, coining, and embossing.
Automation: Many modern press brakes are equipped with computer numerical control (CNC) systems, allowing for automated and programmable operations. This enhances efficiency and reduces the potential for human error.
Efficiency and Productivity: Press brakes are essential for mass production as they enable the quick and efficient shaping of metal components. CNC-controlled press brakes can increase productivity by allowing for batch processing and rapid tool changes.
Cost-Effective: By enabling precise control over the bending process, press brakes help minimize material waste, making them a cost-effective solution for metal fabrication.
press brakes play a crucial role in the manufacturing industry by providing a versatile and efficient means of shaping sheet metal into the desired forms for various applications.
CHOOSING THE BEST PRESS BRAKE FOR YOUR APPLICATION
Choosing the best press brake for your application involves considering several factors to ensure that the machine meets your specific requirements. Here are key considerations to help you make an informed decision:
Material and Thickness:
Consider the type of material you’ll be working with (e.g., steel, aluminum, stainless steel) and the thickness of the sheets. Ensure that the press brake you choose has the capacity to handle the materials and thicknesses you commonly work with.
Bending Length:
Determine the required bending length, which is the maximum distance between the center of the tooling. Choose a press brake with a bending length that accommodates the size of the parts you’ll be producing.
Tonnage:
Tonnage refers to the force the press brake can exert on the material. Select a press brake with sufficient tonnage to handle your typical bending applications. The material type and thickness will influence the required tonnage.
Tooling Compatibility:
Check the availability and compatibility of tooling options for the press brake. Ensure that the machine can accommodate the specific tooling you need for your applications, including punches and dies.
الدقة والضبط:
Look for press brakes that offer high precision and accuracy, especially if your applications require tight tolerances. CNC-controlled press brakes with advanced backgauge systems can enhance accuracy and repeatability.
Speed and Productivity:
Consider the production volume and speed requirements of your application. Some press brakes come with features like fast ram speeds, quick tool changes, and automated backgauges to improve overall productivity.
Flexibility and Versatility:
Assess the flexibility of the press brake in handling various bending tasks. A versatile machine can adapt to different materials and part geometries, providing you with more manufacturing capabilities.
CNC Control:
Opt for a press brake with a user-friendly CNC control system if precision and programmability are essential for your applications. CNC controls allow for automation, ease of operation, and the creation of complex part geometries.
Tool Change System:
Evaluate the tool change system of the press brake. Quick and easy tool changes can reduce setup time and increase overall efficiency, especially in environments where frequent tool changes are required.
Maintenance and Support:
Consider the maintenance requirements of the press brake and the availability of support from the manufacturer. A reliable after-sales service and support network can be crucial for minimizing downtime and addressing any issues that may arise.
By carefully considering these factors, you can choose a press brake that aligns with your specific application needs, providing optimal performance and efficiency in your metal fabrication processes.
WHY TONNAGE AND LENGTH ARE IMPORTANT
Press brake tonnage and length are crucial factors in determining the capabilities and suitability of a press brake for specific metal bending applications. Here’s why these two aspects are important:
Press Brake Tonnage:
Bending Force : Tonnage refers to the force that the press brake can exert on the material during the bending process. It is typically measured in tons. The tonnage required depends on the material type, thickness, and the desired bend angle.
Material Strength: Different materials have varying strengths, and higher tonnage is often needed for bending stronger materials like high-strength steel. Insufficient tonnage may result in incomplete or inaccurate bends.
Avoiding Deflection: Adequate tonnage helps prevent the machine from deflecting under the load. Deflection can lead to inaccuracies in the bend angle and affect the overall quality of the formed part.
Bending Length:
Part Size and Geometry: Bending length, also known as the bed length or working length, is the distance between the center of the tooling. It determines the maximum size of the parts that can be bent on the press brake. Choosing the right bending length ensures that the machine can handle the size and geometry of the parts you intend to produce.
Flexibility in Part Design: A longer bending length allows for the bending of larger and more complex parts. If your applications involve producing longer or wider components, a press brake with an appropriate bending length is essential for flexibility in part design.
Tooling Compatibility: The bending length is closely related to the tooling used. Ensure that the press brake can accommodate the required tooling for your specific applications, including the necessary punch and die sizes.
In summary, press brake tonnage and length are critical because they directly impact the machine’s ability to handle different materials, part sizes, and geometries. Selecting the right tonnage and bending length ensures that the press brake can provide the necessary force to bend materials accurately and accommodate the size and complexity of the parts you need to manufacture. Failure to consider these factors may lead to suboptimal bending results, increased wear on the machine, and potential issues with part quality and precision.
HOW KRRASS MACHINE TOOLS CAN HELP
KRRASS Machine Tools is a company known for manufacturing and supplying a range of sheet metal fabrication machinery, including press brakes. While specific details about the company’s products and services may have changed since then, I can provide general information on how a reputable machine tools manufacturer like KRRASS may assist in your metal fabrication needs:
Quality Machinery:
KRRASS Machine Tools is known for producing high-quality press brakes and other sheet metal fabrication machinery. Their machines may be designed with advanced features, precision controls, and durable construction, contributing to reliable and efficient metal bending operations.
Product Range:
KRRASS may offer a variety of press brake models with different tonnage capacities, bending lengths, and features. This allows you to choose a machine that best suits your specific application requirements.
Customization Options:
Reputable machine tool manufacturers often provide customization options to meet the unique needs of their customers. KRRASS may offer choices in terms of tooling, CNC controls, and other features to tailor the press brake to your specific manufacturing needs.
Technical Support:
A reliable manufacturer typically provides technical support, including documentation, manuals, and assistance with machine setup and operation. KRRASS may offer training programs or resources to help users maximize the capabilities of their machinery.
After-Sales Service:
After-sales service is crucial in the machinery industry. KRRASS may offer maintenance and repair services, ensuring that your press brake operates at its best over the long term. Timely support and readily available spare parts can minimize downtime.
Global Presence:
If KRRASS has a global presence, it may provide distribution, support, and service in various regions. This can be beneficial for customers with international operations or those looking for a reliable partner with a wide reach.
Innovation and Technology:
Reputable manufacturers often invest in research and development to incorporate the latest technologies and innovations into their machines. KRRASS may offer press brakes with advanced features, automation capabilities, and user-friendly interfaces.
Customer Reviews and Reputation:
Research customer reviews and testimonials to gauge the reputation of KRRASS Machine Tools. Positive feedback from other users can provide insights into the quality and performance of their machinery.
Before making a purchase, it’s advisable to directly contact KRRASS Machine Tools or their authorized dealers to get the most up-to-date and specific information about their products, services, and support offerings.