Press brake crowning is a technique used in metalworking, particularly in the bending process, to ensure consistent and accurate results when bending metal sheets or plates. When a metal sheet is bent using a press brake, it tends to deform in a predictable manner due to factors like material elasticity and thickness variations. However, these deformations can sometimes lead to inaccuracies in the final bend angles, especially across the width of the sheet.
Crowning involves modifying the shape of the bed or the tooling of the press brake to compensate for these predictable deformations. Typically, the bed or tooling is shaped slightly to form a convex curve across its length. This curvature is designed to counteract the anticipated deflection of the metal sheet during bending, resulting in more uniform bending angles across the entire width of the sheet.
The amount of crowning required depends on factors such as the material type, thickness, and length of the metal sheet being bent. Crowning can be adjusted manually or automatically based on the specific requirements of each bending job.
By employing crowning, manufacturers can achieve more precise and consistent bending results, reducing scrap, improving overall product quality, and minimizing the need for secondary operations to correct inaccuracies in the bent parts.
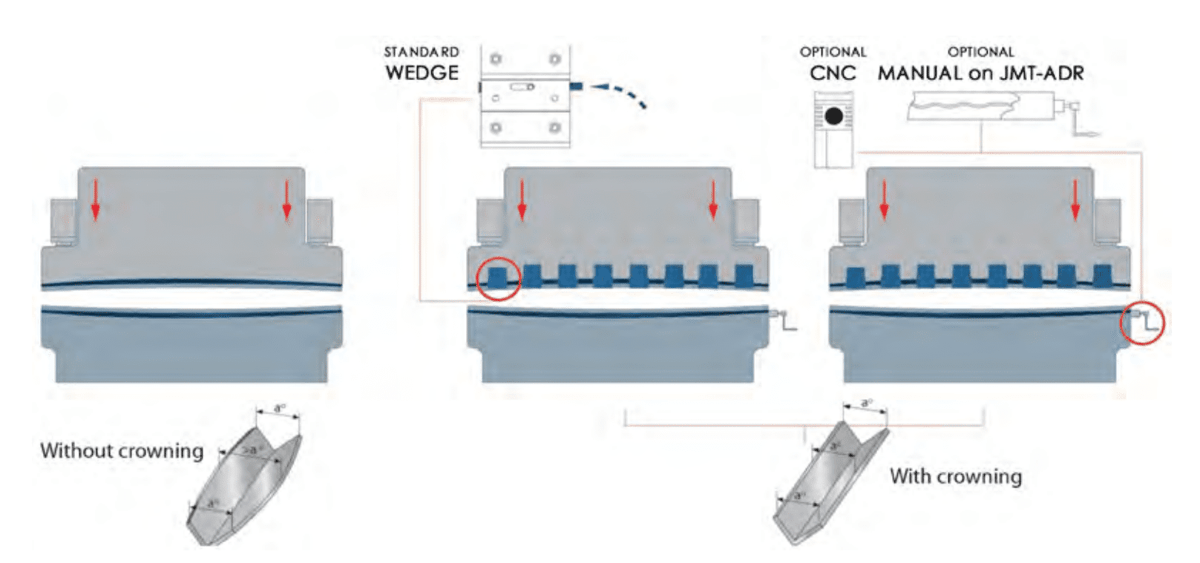
What Is Crowning in Press Brakes?
In the context of مكابح الضغط, crowning refers to the intentional curvature or adjustment made to the bed or tooling of the press brake machine. This adjustment is made to compensate for the natural deflection that occurs when large or thick sheets of metal are bent.
When a metal sheet is bent on a press brake, the force applied by the press brake’s ram can cause the bed of the machine to flex slightly. This flexing can result in an uneven bend across the length of the sheet, with the center experiencing less bending than the edges. This inconsistency can lead to inaccuracies in the final bent part.
To counteract this effect, crowning is used. By adjusting the curvature of the bed or tooling, typically in a convex shape, the press brake operator can compensate for the anticipated deflection. This ensures that the force applied during bending is distributed more evenly across the width of the sheet, resulting in more consistent bend angles throughout the part.
Crowning is particularly important when working with longer or thicker sheets of metal, where deflection can have a more significant impact on bending accuracy. It helps to minimize scrap, improve product quality, and reduce the need for manual correction of bent parts. Modern press brakes often feature automated crowning systems that can adjust the curvature dynamically based on factors such as material thickness and bending parameters.
Can Crowning Be Prevented?
While it’s nearly impossible to completely eliminate crowning, especially in long pieces of sheet metal, methods do exist to mitigate its effects. These include various compensation techniques that adjust for the deformation that crowning causes, ensuring accurate bends despite the inherent flexing of the machine.
Ways To Compensate for press brake Crowning
There are several ways to compensate for press brake crowning to ensure accurate and consistent bending results:
Manual Adjustment: Press brake operators can manually adjust the crowning by shimming the dies or bed of the press brake. This involves adding or removing shims to change the curvature of the tooling or bed, compensating for deflection.
Hydraulic Crowning Systems: Many modern press brakes are equipped with hydraulic crowning systems. These systems use hydraulic actuators to adjust the curvature of the bed or tooling automatically. They can be programmed to compensate for variations in material thickness and bending parameters.
Mechanical Compensation: Some press brakes use mechanical mechanisms to compensate for crowning. This may involve adjustable wedges or bolts that can be tightened or loosened to change the curvature of the bed or tooling.
Software Compensation: Advanced press brake control systems may incorporate software-based compensation algorithms. These algorithms analyze factors such as material properties, bend length, and bending force to calculate the required crowning adjustment automatically.
Die Selection: Choosing the appropriate die shape and size can also help compensate for crowning. Certain die designs, such as segmented or variable-radius dies, can distribute bending forces more evenly across the width of the sheet, reducing the need for crowning adjustments.
Material Pre-Bending: Pre-bending the material slightly before the actual bending operation can help compensate for crowning effects. This involves bending the material in the opposite direction of the final bend to counteract any inherent curvature or deflection.
Material Thickness Compensation: Adjusting the bending parameters, such as the tonnage and bend radius, based on the material thickness can help compensate for crowning. Thicker materials tend to deflect more, so applying additional force or using larger bend radii can help mitigate this effect.
Maintaining Your Crowning System
By employing these compensation techniques, press brake operators can ensure that crowning does not negatively impact the accuracy or consistency of their bending operations, resulting in high-quality finished parts.
Maintaining your crowning system is crucial to ensuring its continued performance and longevity. Regular maintenance includes frequent inspection and—in wedge-type crowning systems—wedge lubrication to keep them operating smoothly and effectively.
Understanding press brake crowning and the various ways to compensate for it is key to achieving precise bends in all your press brake operations. Remember to maintain your crowning system regularly to ensure optimal performance and extended equipment life.