مقدمة:
آلات ثني الصفائح CNC تعتبر الآلات الثني ثلاثية الأسطوانات ورباعية الأسطوانات جزءًا لا يتجزأ من الصناعات المختلفة، حيث توفر القدرة على ثني الألواح غير المعدنية إلى أشكال متنوعة. ضمن هذه الفئة، تخدم آلات ثني الألواح ثلاثية الأسطوانات ورباعية الأسطوانات أغراضًا فريدة، ولكل منها مزايا مميزة. تتعمق هذه المقالة في الاختلافات بين هذه الآلات، مع التركيز على بنائها ومبادئ عملها ووظائفها المحددة.
ماكينة ثني الألواح ذات 3 لفات مقابل 4 لفات
1. حركة الأسطوانة ومبادئ العمل:
- آلة ثني الصفائح ذات الثلاث أسطوانات:
- يتم وضع الأسطوانة العلوية بشكل متماثل بين الأسطوانتين السفليتين، ويسهل الزيت الهيدروليكي حركات الرفع والخفض الرأسية.
- يقوم الترس النهائي للمخفض الرئيسي بتحريك تروس الأسطوانات السفلية، مما يخلق حركة متدحرجة ويوفر عزم الدوران للانحناء.
- آلة ثني الصفائح ذات الأربع أسطوانات:
- تعمل الأسطوانة العلوية كمحرك رئيسي، متصلة من خلال مخفض ومشبك منزلق متقاطع لتوفير عزم الدوران للتدحرج.
- تتحرك الأسطوانة السفلية عموديًا، وتثبت اللوحة بمحرك ميكانيكي، بينما تتحرك الأسطوانات الجانبية على كلا الجانبين وترتفع لمزيد من التحكم.
- تستخدم أربع بكرات عمل محامل دوارة لتحسين الاستقرار.
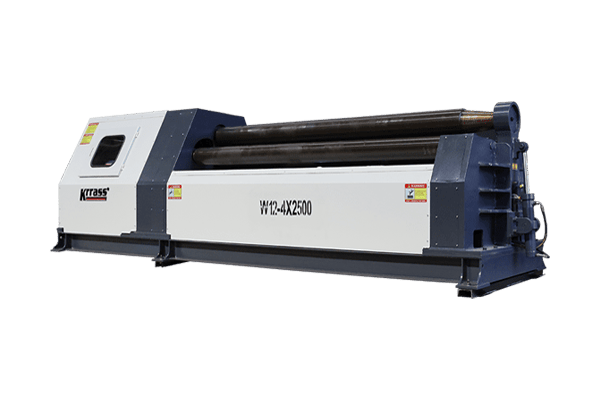
2. هيكل الآلة والتشغيل:
- آلة ثني الصفائح ذات الثلاث أسطوانات:
- تصميم غير متماثل مع الأسطوانة العلوية كمحرك رئيسي والأسطوانة السفلية تتحرك عموديًا لتثبيت اللوحة.
- يوفر تفاعل التروس بين الأسطوانات العلوية والسفلية وظيفة مزدوجة للثني المسبق والدحرجة.
- هيكل مدمج يضمن سهولة التشغيل والصيانة.
- آلة ثني الصفائح ذات الأربع أسطوانات:
- تثبيت موضع الأسطوانة العلوية، مع تحريك الأسطوانة السفلية إلى الأعلى لتثبيت اللوحة.
- تقوم الأسطوانات الجانبية بتعديل موضعها إما بشكل خطي أو على شكل قوس، مما يوفر المرونة في تعديل نصف قطر الانحناء.
- انحناء مسبق متفوق للحواف المستقيمة والاستدارة مقارنة بنظيراتها ذات الثلاث بكرات.
3. الأداء والنتائج النهائية:
- آلة ثني الصفائح ذات الثلاث أسطوانات:
- يقوم بكفاءة بتدوير قطع العمل الدائرية والمقوسة والمخروطية ضمن نطاق محدد.
- آلة ثني الصفائح ذات الأربع أسطوانات:
- يقوم بإجراء الثني المسبق في نهايات الصفائح، مما يؤدي إلى الحصول على حواف مستقيمة متبقية أصغر حجمًا وكفاءة عمل عالية.
- مثالي لتسوية الصفائح المعدنية بشكل تقريبي، مما يضمن الدقة والجودة.
4. عملية التشغيل:
- آلة ثني الصفائح ذات الأربع أسطوانات:
- تحتوي على أربع بكرات مع موضع ثابت للأسطوانة العلوية وأسطوانات هيدروليكية تعمل على تحريك الأسطوانة السفلية إلى الأعلى.
- مسافة قابلة للتعديل بين الأسطوانة الجانبية والأسطوانة العلوية لتناسب متطلبات الانحناء المتنوعة.
- تسمح الحركات المتسلسلة للأسطوانات السفلية والجانبية بتكوين أشكال أسطوانية بكفاءة.
خاتمة:
فهم الاختلافات بين 3 لفة و آلة ثني الألواح ذات 4 لفاتتعتبر هذه التقنية بالغة الأهمية للصناعات التي تعتمد على تقنية التحكم الرقمي بالكمبيوتر. وفي حين يلتزم كلاهما بمبدأ تحديد الدائرة ذات النقاط الثلاث، فإن النسخة ذات الأربع بكرات تتميز بقدراتها الفائقة على الانحناء المسبق وضبط الانحناء الدقيق، مما يوفر كفاءة وجودة محسّنتين في معالجة الصفائح المعدنية. يعتمد اختيار الآلة المناسبة على متطلبات المشروع المحددة والنتائج المرجوة.