Understanding how does a hydraulic press brake work is crucial for anyone involved in the manufacturing and metalworking industries. Hydraulic press brakes are essential machines used to bend and shape metal sheets with precision and efficiency. By leveraging hydraulic power, these machines convert hydraulic pressure into mechanical force, enabling them to perform complex bending operations. Knowing how these machines operate can significantly enhance the productivity and quality of manufacturing processes. The purpose of this article is to explain the working mechanism of hydraulic press brakes, providing a detailed overview of their components, the bending process, and the advantages they offer over other types of press brakes.
جدول المحتويات
What Is A Hydraulic Press Brake
أ مكابس هيدروليكية is a sophisticated machine tool designed for shaping sheet metal and metal plates by clamping the workpiece using hydraulic pressure between a matching top tool (punch) and a bottom die, thereby achieving precise bends. Understanding how does a hydraulic press brake work involves recognizing the key components and their functions:
- Hydraulic System: This is the heart of the machine, generating the necessary pressure to move the ram. The hydraulic system consists of pumps, valves, and a reservoir filled with hydraulic fluid, which together create and control the pressure required for the bending process.
- Ram: The ram is a crucial component that moves up and down, pressing the punch into the workpiece. It converts the hydraulic pressure into mechanical force, enabling precise and powerful bending.
- Bed: The bed is the stationary part of the machine that holds the die. It provides a solid foundation and supports the workpiece during the bending process.
- Back Gauge: The back gauge is a device that ensures exact positioning of each workpiece, guaranteeing consistent and accurate bending. It can be adjusted to accommodate different bend lengths and angles.
- Control Unit: Most modern hydraulic press brakes are equipped with a CNC (Computer Numerical Control) system. The control unit allows operators to input precise commands and control the machine accurately, enhancing the efficiency and repeatability of the bending process.
When a hydraulic press brake operates, the process begins with the hydraulic system generating pressure. This pressure forces the ram down, pushing the punch into the workpiece, which is positioned on the lower die. By adjusting the pressure and positioning of the tools, various angles and shapes can be achieved, making hydraulic press brakes highly versatile compared to mechanical or pneumatic brakes. This versatility allows for the creation of complex bends and shapes, catering to a wide range of manufacturing needs.
Types of Hydraulic Press Brake
Hydraulic press brakes come in various types, each designed to meet specific bending needs and operational requirements. Here are the main types:
1. Conventional Hydraulic Press Brakes
- Description: Conventional hydraulic press brakes are the traditional type, using hydraulic pressure to bend metal. They operate with a straightforward mechanical system, where the hydraulic system generates pressure to move the ram and apply force to the metal.
- التطبيقات: Suitable for general metal bending tasks in various industries, including metal fabrication and construction.
2. CNC Hydraulic Press Brakes
- Description: Computer Numerical Control (CNC) hydraulic press brakes are equipped with advanced computer systems that automate and control the bending process. Operators input parameters such as bend angle, depth, and material thickness into the CNC system, which manages the machine’s operation with high precision.
- التطبيقات: Ideal for complex and precise bending tasks, including automotive, aerospace, and high-volume manufacturing.
3. Hybrid Hydraulic Press Brakes
- Description: Hybrid hydraulic press brakes combine hydraulic and electric drive technologies. They use hydraulic pressure for bending while incorporating electric drives for improved control and energy efficiency. This hybrid approach aims to offer the best of both hydraulic and electric systems.
- التطبيقات: Suitable for applications requiring high precision and energy efficiency, often used in industries that prioritize both performance and cost-effectiveness.
4. Servo-Electric Press Brakes
- Description: Servo-electric press brakes use electric motors to drive the ram, offering precise control and high efficiency. While not purely hydraulic, they use hydraulic pressure to achieve the bending force. These machines are known for their energy efficiency and low noise levels.
- التطبيقات: Ideal for high-precision bending tasks where energy savings and low maintenance are important, such as in the automotive and aerospace industries.
5. Tandem Press Brakes
- Description: Tandem press brakes consist of two or more hydraulic press brakes arranged in a series. This setup allows for the handling of larger and longer metal sheets by dividing the bending process across multiple machines.
- التطبيقات: Suitable for manufacturing large or long metal components, commonly used in industries like construction and heavy machinery.
6. Box & Pan Press Brakes
- Description: Box and pan press brakes are designed to handle specific bending tasks, particularly for creating box-shaped and pan-shaped metal parts. They feature specialized dies that allow for forming complex shapes with multiple bends.
- التطبيقات: Commonly used in custom fabrication shops and industries that require the production of complex metal parts, such as aerospace and automotive.
7. Automatic Press Brakes
- Description: Automatic press brakes are designed for high-volume production, featuring automated loading, bending, and unloading processes. They are equipped with advanced automation systems to improve efficiency and reduce manual labor.
- التطبيقات: Ideal for high-volume manufacturing environments where speed and automation are critical, such as in mass production industries.
Each type of hydraulic press brake is tailored to meet specific operational needs and industry requirements, offering various features and capabilities to handle diverse metal bending tasks.
How Does A Hydraulic Press Brake Work
A hydraulic press brake is a vital machine in metal fabrication, designed to precisely bend and shape sheet metal. It uses hydraulic force to apply pressure to the metal, enabling it to bend at specific angles. The key components of a hydraulic press brake include the frame, ram, bed, hydraulic system, control panel, and back gauge.
The frame serves as the structural backbone of the machine, providing stability and support throughout the bending process. The ram is the component that exerts the bending force on the sheet metal. The bed acts as the base where the sheet metal is positioned for the bending operation.
النظام الهيدروليكي
The hydraulic system is the core driving force behind a press brake’s operation, consisting of a hydraulic pump, cylinders, valves, and an oil reservoir. When the bending process begins, the hydraulic pump generates pressure by channeling hydraulic fluid into the cylinders. This fluid pushes the ram downward, applying the necessary force to bend the sheet metal. Valves regulate the flow of hydraulic fluid, allowing for precise adjustments in bending speed and pressure.
Control Mechanisms
Hydraulic press brakes feature advanced control mechanisms to ensure accurate and consistent bending. The control panel allows operators to set bending parameters such as angle, depth, and back gauge position. The back gauge, equipped with sensors or meters, precisely positions the sheet metal, ensuring uniform bends across multiple parts. Some press brakes use computer numerical control (CNC) technology, which enables automated and programmable operations for enhanced efficiency.
عملية الانحناء
The bending process involves several stages. First, the operator inputs the desired parameters into the control panel. The back gauge then positions the sheet metal accurately to ensure consistent bends. When the operator initiates the bending cycle, the hydraulic system activates, causing the ram to descend and exert force on the metal. This force exceeds the sheet metal’s yield strength, creating the desired bend at the specified angle. The back gauge and control panel work together to maintain precision and repeatability throughout the bending process.
Safety Measures
Safety is crucial when operating a hydraulic press brake. These machines are equipped with various safety features, including emergency stop buttons, safety curtains, and two-handed controls. Operators must receive thorough training on machine operation, safety protocols, and proper sheet metal handling. Following safety guidelines is essential for creating a secure working environment and minimizing the risk of accidents.
Advantages and Applications
Hydraulic press brakes offer numerous benefits, making them a popular choice in metal fabrication. Their ability to generate high bending forces allows for precise bending of thick and heavy-duty materials. The hydraulic system facilitates easy control and adjustment, resulting in consistent and accurate bends. Additionally, hydraulic press brakes operate with lower noise levels and reduced vibrations compared to mechanical press brakes. These machines are used in various industries, including automotive, aerospace, construction, and manufacturing, where precise sheet metal bending is critical.
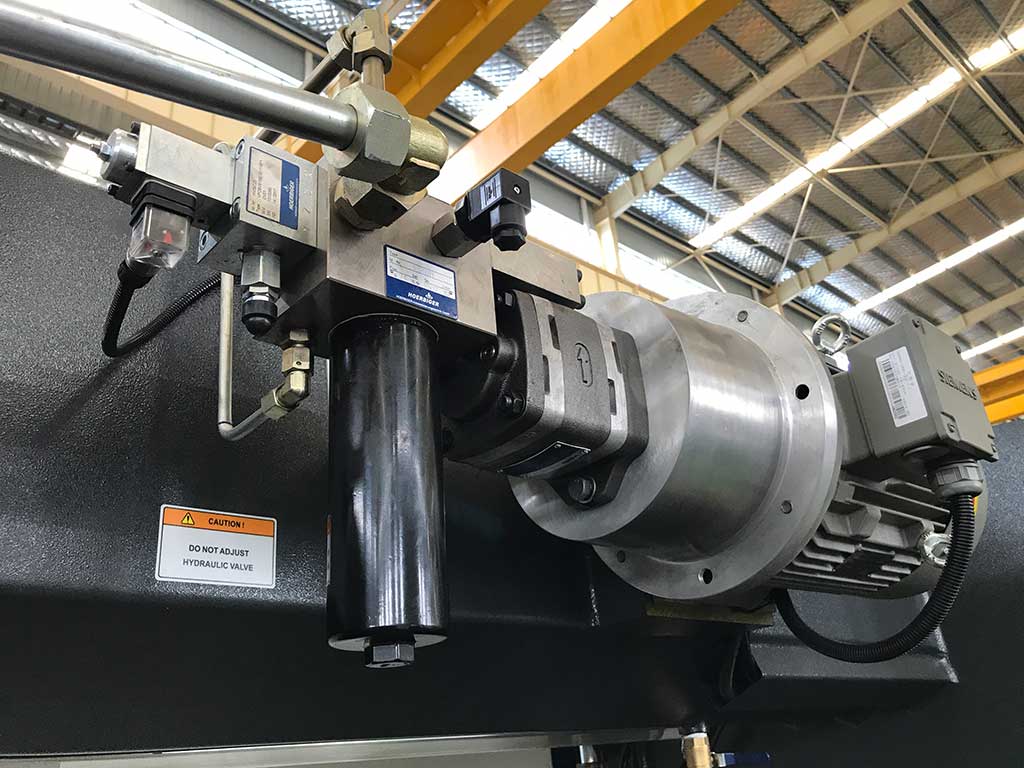
How to Use A Hydraulic Press Brake
The operation of a hydraulic press brake typically involves the following stages:
Setup: The operator prepares the press brake for bending by selecting the appropriate die, adjusting the back gauge for material positioning, and setting the bending parameters such as bend angle, bend radius, and material thickness on the control system.
Material loading: The operator places the sheet metal or plate material to be bent onto the bed of the press brake and aligns it against the back gauge for accurate bending.
Bending cycle initiation: The operator starts the bending cycle by activating the hydraulic system, which applies pressure to the hydraulic cylinders to move the ram downward and exert force on the material.
Bending process: As the ram presses the material against the die, it begins to bend along the desired line. The operator monitors the bending process to ensure it meets the specified parameters and makes adjustments if needed.
Release: Once the material has been bent to the desired angle, the hydraulic system releases pressure, allowing the ram to retract and the bent material to be removed from the press brake.
Unloading: The operator removes the bent material from the press brake and may repeat the bending process for additional bends or parts if necessary.
Maintenance and cleanup: After the bending operations are complete, the operator performs any required maintenance tasks on the press brake and cleans up the work area for the next job.
These stages outline the typical sequence of operations involved in using a hydraulic press brake to bend sheet metal or plate material.
Advantages of Hydraulic Press Brake
Enhanced Precision
Hydraulic press brakes excel in delivering superior precision during bending operations. The machine’s control system allows operators to accurately manage the ram’s motion, speed, and applied force. This results in highly precise bend angles and consistent output. Advanced sensors and feedback systems further enhance accuracy, ensuring that each bend adheres closely to the specified parameters and reducing the likelihood of defects.
تحسين السلامة
Safety is a major benefit of hydraulic press brakes. The integration of sophisticated computer controls allows for precise operation, minimizing the risk of human error. These machines are also equipped with a variety of safety features such as light curtains, emergency stop buttons, and safety guards, which collectively enhance operator protection and prevent accidents. Additionally, automatic shut-off mechanisms and pressure monitoring further contribute to a safer working environment.
التنوع
Hydraulic press brakes are known for their versatility. They can handle a wide range of metals, different tonnages, and varying sheet thicknesses. Capable of forming diverse shapes, including complex geometries, these machines are adaptable to many industrial applications. This flexibility makes them invaluable in sectors such as automotive, aerospace, construction, and manufacturing, where a wide variety of bending tasks are required.
كفاءة الطاقة
Modern hydraulic press brakes are designed with energy efficiency in mind. They utilize hydraulic systems that optimize power consumption, reducing overall energy usage compared to older models or other types of press brakes. This efficiency not only lowers operational costs but also contributes to a more sustainable manufacturing process.
صيانة مخفضة
Hydraulic press brakes often require less maintenance than their mechanical counterparts. The hydraulic system’s design minimizes wear and tear on components, leading to fewer breakdowns and reduced maintenance needs. This results in lower long-term operating costs and increased machine uptime.
Higher Throughput
The efficient operation and precise control of hydraulic press brakes enable faster bending cycles. This increased throughput allows for higher production rates and the ability to handle larger volumes of work within shorter timeframes, improving overall productivity.
Consistent Quality
The precise control and uniform bending capabilities of hydraulic press brakes ensure consistent quality across all parts produced. This consistency helps in maintaining high standards in manufacturing and reduces the need for rework or quality checks, thus enhancing overall production efficiency.
How Hydraulic Press Brake Fit Manufacturing
Hydraulic press brakes are versatile machines employed across a range of industries for the precise bending of sheet metal and plate materials. Their applications span several key sectors:
Metal Fabrication: In metal fabrication shops and manufacturing facilities, hydraulic press brakes play a crucial role in bending sheet metal and plate materials. They are used to create a variety of components and products essential to the industry.
Automotive Industry: Hydraulic press brakes are integral to the automotive sector, where they are used to bend metal parts for vehicle bodies, chassis, and interior components, ensuring precision and durability in automotive design and manufacturing.
صناعة الطيران والفضاء: The aerospace industry relies on hydraulic press brakes for forming sheet metal components used in aircraft structures, engines, and other aerospace applications. These machines ensure the high precision required for critical aerospace components.
Construction Industry: In construction, hydraulic press brakes are employed to bend metal components used in building structures, architectural elements, and infrastructure projects. They help in crafting structural supports, beams, and custom metal features.
Electronics Industry: Hydraulic press brakes are also utilized in the electronics sector for producing electronic enclosures, components, and devices made from sheet metal. Their precision helps in manufacturing components that meet strict design and functional requirements.
Furniture Manufacturing: The furniture industry benefits from hydraulic press brakes in bending metal parts for furniture frames, structures, and decorative elements. This application ensures the creation of sturdy and aesthetically pleasing furniture components.
Agricultural Equipment: Hydraulic press brakes are used in the fabrication of agricultural machinery and equipment, such as tractor components and farm machinery parts. Their ability to handle heavy-duty materials is crucial for the robust demands of agricultural applications.
In summary, hydraulic press brakes are essential across various industries, providing the precision and versatility needed for manufacturing a wide range of products and components from sheet metal and plate materials.
Cases Studies of Hydraulic Press Brakes in Action
Hydraulic press brakes are widely utilized machines for metal processing in mechanical manufacturing, aerospace manufacturing and car production among other fields. Primarily employed to bend, form and shape metal sheets precisely and efficiently while producing sheets in different shapes and sizes.
Hydraulic Press Brakes Can Be Found Used Widely.
- Process for Bending: Bending involves the precise bending of metal sheets at specific angles and radii, to fulfill design specifications. A hydraulic press brake uses massive pressure generated by its hydraulic device to keep a sheet between lower and upper dies until bending is complete. By changing worktable angle and clamp force settings, this device allows precise control over bend angle and curvature control ensuring an efficient bending process.
- Curving Methods: Curving is the practice of bending metal sheets at a specific radius to create the ideal shape. A hydraulic press brake, by changing the positions and force of clamping can control curvature angle and degree that allow exact curving of metal sheets – this method is often employed when producing fittings, pipes, and slot plates with required exact curvatures.
- Forming Methods: Forming involves shaping sheets of metal into specific dimensions and shapes for specific uses and functions. A hydraulic press brake equipped with different-shaped dies can shape sheets of metal into various forms – U-shaped dies can make metal sheet bend into U-shape while V-shaped tools create V-shape bends. By choosing wisely when choosing dies for hydraulic presses, forming processes can be established on metal sheets of various sizes and shapes.
- Cold Bending: Cold bending refers to the process of bending metal sheets at room temperature without using heat as a heat source. A hydraulic press brake can be used for this, with its lower and upper dies adjustable as well as its clamping force changing to control angle of bending and curvature of sheet allowing cold bending to take place. This method is frequently employed by thin sheet suppliers looking to minimize stress, thermal deformation, and retain their materials’ characteristics while still producing desired shapes.
Hydraulic press brakes are essential metal processing tools with numerous uses. Capable of curving, bending and forming sheets of metal in various ways to meet diverse processing requirements for various shapes and sizes of sheets of metal sheets, they have become essential pieces of industrial manufacturing equipment to increase production efficiency while improving quality control standards.
Hydraulic Press Brake Comparison
In the highly competitive field in the field of CNC press brakes and hydraulic press brakes, it is the Hydraulic Press Brake Servo emerges as a shining example of advancement. Its three key advantages–High Precision, Comprehensive Functionality, and User-Friendliness–make it a compelling choice.
- Advanced Precision With electronic signals analysis the CNC press brake that comes with Hydraulic Servo ensures unbeatable precision, which makes it an ideal choice for specifications with intricate details.
- Complete Functions: Cost considerations often are a factor in the selection of CNC press brakes. It is the Hydraulic Servo Brake with its entire functionality, easily makes its case, proving superior to conventional counterparts.
- Friendly for Users: Clarity, simplicity and user-friendliness are the main characteristics of the Hydraulic Press Brake Servo. Even the most novice users can manage the functions efficiently, while reducing the possibility of errors and failures.
Feature | مكبس الفرامل الهيدروليكي | Traditional Press Brake |
---|---|---|
مصدر الطاقة | Hydraulic system | Mechanical (usually via a flywheel) |
مبدأ العمل | Uses hydraulic fluid to generate pressure for bending | Relies on mechanical force, often using a flywheel and clutch system |
المرونة | Highly flexible, adaptable to various workpieces and demands | Limited flexibility, may require changing tools for different applications |
Pressure Control | Adjustable and controllable pressure for precision | Pressure control may be less precise |
Speed and Length Control | Adjustable speed and length of the slide for dynamic options | Limited speed and length control, manual adjustments |
صيانة | Generally low maintenance, suitable for prolonged use | May require more frequent maintenance, especially for mechanical parts |
أمان | Operates in a stable manner, reducing impacts and vibrations | May produce more noise, impacts, and vibrations |
دقة | High precision, capable of maintaining extended pressure at the dead center | Precision may vary, especially over the entire stroke |
التطبيقات | Widely used in various industries for bending, folding, and shaping metal sheets | Commonly used but may be less adaptable to diverse applications |
Advancements | Evolving towards automation and intelligent features | May have fewer advancements in automation and smart technology |
How to Select A Hydraulic Press Brake
Purchasing a hydraulic press brake is a significant investment. Understanding key considerations can help ensure you select the right machine for your specific needs. Here are some of the main factors to bear in mind:
Nature of Your Applications
Consider the specific tasks that your hydraulic press brake will be used for. Different models of press brakes are designed with varying capabilities and features to suit specific applications.
- Do you need to bend thick or thin materials?
- What is the typical bending length for your projects?
- What is the complexity of the bends you need to perform?
Machine Capacity
The machine’s capacity, defined by its tonnage and bending length, is an essential factor. This determines what size and thickness of materials the machine can handle and the kind of bending it can perform.
- What is the maximum tonnage the machine can apply?
- What is the maximum bending length the machine can accommodate?
Machine Features
Hydraulic press brakes come with a variety of features, which can enhance their performance and usability. These can include things like CNC controls for precision and programmability, back gauges for accurate positioning of the workpiece, and safety features.
- Does the machine come with CNC controls for precision and ease of use?
- Does it have a back gauge to assist with positioning the workpiece?
- What safety features does the machine have?
Budget
The cost of the machine is, of course, a key consideration. It’s important to weigh the cost of the machine against its capabilities and features. A higher price may be justified by increased productivity, improved accuracy, or reduced operating costs in the long term.
- How does the cost of the machine compare to its features and capabilities?
- Will the machine provide a return on investment through increased productivity or reduced operating costs?
Operating and Maintenance Costs
In addition to the purchase price, consider the ongoing costs of operating and maintaining the machine. These can include energy costs, maintenance costs, and the cost of replacement parts.
- What are the typical energy consumption costs?
- How often will the machine need maintenance, and what will this cost?
- How easy is it to obtain replacement parts, and what do they typically cost?
Vendor Support and Warranty
Finally, consider the level of support and warranty provided by the vendor. A good vendor will provide comprehensive after-sales support, including installation, training, and maintenance. A robust warranty can also provide peace of mind.
- What level of support does the vendor provide after the sale?
- Does the machine come with a warranty, and what does it cover?
What’s the Cost of Hydraulic Press Brake
The cost of a hydraulic press brake can vary widely depending on several factors, including its size, tonnage capacity, features, and brand. Here’s a general overview:
- Entry-Level Models:
- Price Range: $10,000 to $30,000
- سمات: Basic controls, limited tonnage (often up to 50 tons), and simpler configurations. These are suitable for smaller workshops or light-duty applications.
- Mid-Range Models:
- Price Range: $30,000 to $100,000
- سمات: Includes more advanced controls (possibly CNC), higher tonnage capacities (up to 150 tons), and additional features like improved back gauges and hydraulic systems. These are ideal for medium-sized shops or more complex tasks.
- High-End Models:
- Price Range: $100,000 to $300,000+
- سمات: High tonnage capacities (150 tons and above), advanced CNC controls, precise back gauges, automation features, and robust construction. These are designed for large-scale production and high-precision tasks.
- Custom and Specialized Models:
- Price Range: $300,000 to $1,000,000+
- سمات: Tailored to specific needs, such as large bending capacities, specialized dies, or automated systems. These models are often used in industries requiring very high precision and heavy-duty applications.
Additional Cost Considerations:
- Installation and Training: Some manufacturers charge extra for installation, training, and setup.
- Maintenance and Parts: Ongoing maintenance and replacement parts should be factored into the overall cost.
- Shipping: Delivery charges can vary based on the machine’s size and weight.
For a precise quote, it’s best to contact manufacturers or distributors directly. Brands like KRRASS, Amada, Trumpf, and Accurpress offer various models and configurations, so contacting them for detailed pricing based on your specific needs will provide the most accurate cost information.
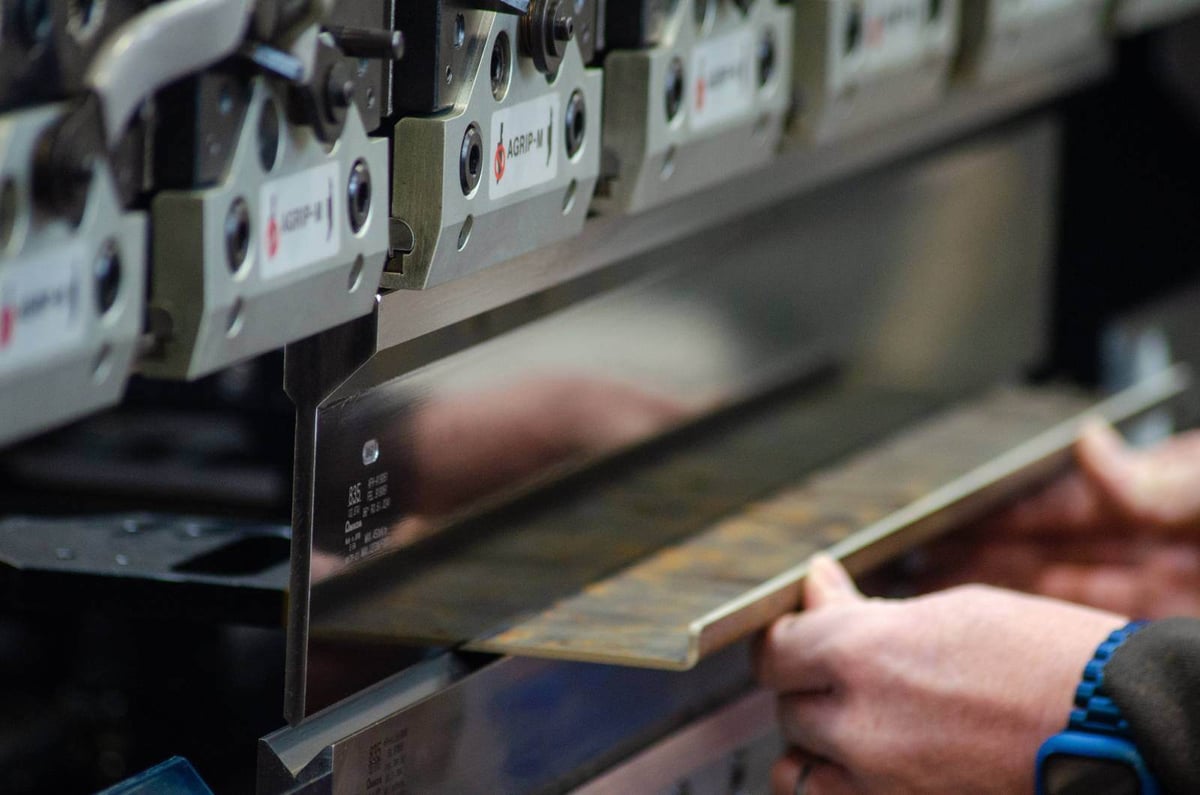
KRRASS Hydraulic Press Brakes: Leading Innovation and Precision
كرااس is a prominent name in the hydraulic press brake industry, renowned for its commitment to quality and innovative solutions. Our CNC hydraulic press brakes are designed with versatility in mind, offering a wide range of customizable sizes and configurations to meet the diverse needs of our clients.
As one of the top hydraulic press brake manufacturers, KRRASS delivers unmatched power, productivity, and adaptability with each machine. Our dedication to cutting-edge technology and superior craftsmanship ensures that every press brake operates with precision and reliability, making them a preferred choice across various industries.
خاتمة
Hydraulic press brakes, with their capacity for precise bending, versatility, and enhanced safety features, have transformed numerous sectors, including automotive, aerospace, and general manufacturing. To fully leverage these machines, it is essential to understand their operation, maintenance requirements, and associated costs.
By choosing KRRASS, you invest in a hydraulic press brake that combines advanced features with robust performance, ensuring long-term efficiency and productivity. With a clear understanding of their capabilities and proper care, these machines will continue to be invaluable assets in your manufacturing processes for years to come.