When it comes to metal fabrication, laser cutting aluminum is an efficient and precise method favored across various industries. Aluminum’s lightweight and reflective properties can pose challenges during the laser cutting process, but with advancements in fiber laser technology, cutting through aluminum has become much easier and more cost-effective. From aerospace components to architectural designs, laser cutting aluminum offers unmatched accuracy, faster production times, and superior edge quality, making it an essential choice for modern manufacturing.
مقدمة
Aluminum is a lightweight and pliable material that offers corrosion resistance and extreme flexibility. It is also non-ferrous and has high thermal conductivity. These unique properties make it the perfect material for the manufacturing industry.
However, although aluminum is soft and lightweight, laser cutting it is not easy. Many manufacturers avoid cutting it through laser cutters because of this. Yet, with the right process and tools, the laser can cut aluminum effectively!
So today, we will examine everything you need to know about laser cutting aluminum. This will help you understand the process behind cutting aluminum and how to get the best results.
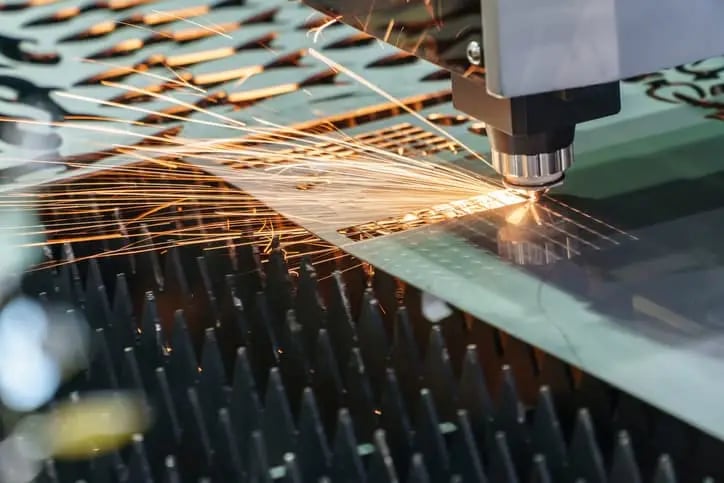
How Laser Cutting Works on Aluminum
1. The Principles of Laser Cutting
Laser cutting operates by focusing a high-powered laser beam onto a material, which heats, melts, and vaporizes the material along a designated path. This method offers incredible precision, enabling intricate cuts with minimal waste. When applied to aluminum, the laser’s energy interacts with the material, allowing for quick, clean cuts. Assist gases such as nitrogen or oxygen are often used to remove molten material and enhance cutting speed and edge quality. The process is highly controlled, making it suitable for a variety of aluminum thicknesses.
2. Differences Between CO2 and Fiber Lasers for Cutting Aluminum
CO2 and fiber lasers are the two main types of lasers used for cutting aluminum, each offering different advantages:
- CO2 Lasers: These lasers work by electrically stimulating a gas mixture (typically carbon dioxide) to produce the laser beam. While CO2 lasers are capable of cutting aluminum, they are less efficient due to aluminum’s reflective surface, which can deflect the laser beam and cause energy loss. Additionally, CO2 lasers require more maintenance and higher operating costs.
- Fiber Lasers: These lasers use optical fibers doped with rare earth elements to generate the laser beam. Fiber lasers are highly efficient for cutting aluminum, especially with advancements in anti-reflective technology. They offer faster cutting speeds, higher precision, and lower operating costs compared to CO2 lasers. Fiber lasers are better suited for handling the reflective nature of aluminum, making them the preferred choice for most modern applications.
Aluminum is widely used in the manufacturing industry to make many things, including cans, foils, airplane parts, and window frames.
Benefits of Laser Cutting Aluminum
So much usage means a big market for cutting aluminum sheets into the desired shapes. There are many tools for cutting aluminum. For instance, people use metal shears, jigsaws, circular saws, CNC machines, and laser cutters.
Laser-cutting remains the most suitable and beneficial of all these different tools and methods.
So without wasting time, let’s look at some of the benefits of cutting aluminum with laser cutting machines:
Precision Cutting
The first benefit of laser cutting aluminum is that it allows for precision cutting. A standard laser-cutting machine utilizes a laser beam to cut through the aluminum sheets. Thus, it can make small holes, sharp cuts, and high-quality edge quality.
When comparing it with alternative cutting processes, it becomes evident that those processes can’t come anywhere near the preciseness of a laser cutter. De facto, these machines hit an accuracy of is ± 0.0005 inches.
Moreover, the mirrors and optical path Lose beam quality and cause significant power drop-off (Around 1/4th of the width of a human’s hair).
Less Expensive
Compared with other cutting processes, such as chemical etching, a laser cutting process is more affordable for aluminum sheets.
Furthermore, the tools are not worn down since they are a no-contact process and use a laser beam. And this is yet another aspect through which a laser-cutting machine can be cost-effective in the long run.
Custom Jobs
Cutting aluminum plates through laser cutting machines allows for highly customized jobs without tooling charges or up-front costs. All you need is to add the laser cutting file to the machine containing the details of the cutting/engraving. The machine does the rest, no matter how complex the design or shape is!
On the contrary, other cutting processes are not designed to handle custom jobs and usually require up-front costs and additional tools.
Fast & Repeatable
Metal shears, Circular Saws, or any other cutting tool can’t compete with the speed of laser cutters. So an additional benefit of relying on laser cutting services is that it can get the job done quickly, within seconds.
In addition, the entire process is also highly repeatable. All you need is to add the cutting file and adjust your laser cutting machine settings. Then, it will cut your desired number of aluminum designs/shapes with minimum human input.
Speed
Given the non-contact nature of the process, laser cutting is typically faster than traditional cutting techniques, especially for thin aluminum.
المرونة
From prototypes to large batch production, laser cutting meets various needs, effectively handling simple to complex designs.
Process of Laser Cutting Aluminum : Difficulty Analysis
Reflective Material
Aluminum is a reflective metal, so the laser beam can reflect from its surface. This reflection can be dangerous since it can enter the laser head and damage the machine parts.
However, this problem can be easily solved by covering the aluminum surface with masking tape or paint. This will remove the reflection of the aluminum sheets and thus make it possible to cut easily.
Another way to deal with this problem is to mix aluminum with other elements such as zinc, magnesium, etc. These are known as alloy elements and can reduce aluminum’s reflectiveness, making it safe for use in the cutting process.
However, the easiest way to solve this problem is to use a fiber laser cutting machine. Fiber laser machines are devised to cut aluminum, brass, and copper! As such, their laser beam is not reflected and is more readily absorbed.
Thermal Conductivity
A laser beam cuts through a material by vaporizing it. However, this can be problematic if the material has high thermal conductivity.
Aluminum is one of those materials that is good at absorbing heat and thus can dissipate heat. So, when the laser beam touches the aluminum surface, it cools off quickly. As a result, the laser cutter fails to reach the high temperature necessary for melting and vaporizing.
A simple solution to this problem is a high-speed laser cutting machine such as a fiber laser cutter. Roughly speaking, a fiber laser machine is five times faster than a typical CO2 laser cutter.
In fiber laser cutting, the laser touches the aluminum surface quickly so that it can melt quickly rather than dissipate into the surroundings.
Upfront Costs
Cutting aluminum with a seamless, high-quality finish and precision requires a high-powered fiber laser cutter or a CO2 one. This means that you will need to incur high upfront costs. However, over the long run, This can help you save money. That’s because these machines offer fast cutting with high precision.
Laser cutting would require post-treatment aluminum parts to obtain a smooth and seamless cutting edge.
How to Get the Best Results When Laser Cutting Aluminum Parts
Laser Power
One of the key factors when cutting aluminum is the laser power of your machine. Low-power lasers are suitable only for thin aluminum sheets, while high-power lasers are capable of cutting through thicker sheets with ease.
It’s important to remember that aluminum is a reflective material, which can cause issues with lower-powered lasers, leading to inefficient cuts. Therefore, opting for a machine with higher laser power is crucial. For instance, fiber lasers with a power rating of 500W or more can easily cut aluminum sheets up to around 3mm in thickness. A pulsed laser with a 500W power supply can also handle aluminum, but it operates at a slower pace compared to fiber lasers.
سرعة القطع
Cutting speed is another essential factor that directly affects the quality of the cut and the smoothness of the edge. A faster cutting speed is always preferable for aluminum, but it should be combined with the appropriate laser power to ensure the best results.
The cutting speed must also be adjusted based on the thickness of the aluminum. Additionally, different lasers, such as CO2 and fiber lasers, have varying optimal speeds for cutting aluminum. Low-speed cuts can lead to cracks, while excessively high speeds can produce rough edges, so striking the right balance is critical.
Auxiliary Gas
Using an auxiliary gas in laser cutting helps to remove molten material and prevent overheating of the cutting head. Various gases like oxygen, air, argon, and nitrogen are commonly used. However, not all are suitable for aluminum. For example, using oxygen can cause oxidation, leading to discolored or rough edges.
Air can reduce oxidation while improving cutting speed, but nitrogen is generally the best option when working with aluminum. It prevents oxidation entirely and ensures smooth, clean edges.
Reflection Detector
The reflective nature of aluminum can be problematic, as it can send the laser beam back toward the machine, potentially damaging the laser module. Fiber lasers are designed to handle this reflectivity better, but for those using CO2 or ND
lasers, it’s essential to use a machine with a reflection detector.
Modern laser cutters typically include this feature, which monitors the amount of reflected laser beam and automatically shuts down the machine if too much reflection occurs. This prevents overheating or damage to the equipment, ensuring safe and efficient operation.
Laser Technology
Several laser cutting technologies are available, including CO2, fiber, and ND
lasers. Among these, fiber lasers are the most effective for cutting or engraving aluminum. They can handle both ferrous and non-ferrous metals with high efficiency and speed, making them the preferred choice for working with aluminum.
Applications of Laser Cutting Aluminum
1. Aerospace and Automotive Industries Laser cutting aluminum plays a crucial role in the aerospace and automotive sectors due to its precision and ability to handle complex designs. In aerospace, aluminum is widely used for its lightweight and high strength-to-weight ratio. Laser cutting allows manufacturers to create intricate components for aircraft, such as brackets, fuselage parts, and wing structures, with minimal material waste and tight tolerances. In the automotive industry, laser cutting is essential for producing aluminum parts like body panels, frames, and battery enclosures for electric vehicles, providing a quick and efficient method for high-quality fabrication.
2. Architecture and Construction In architecture and construction, laser cutting aluminum is commonly used for decorative elements, facades, and structural components. Its ability to deliver clean, precise cuts makes it ideal for creating custom architectural features like intricate designs in panels, railings, and building exteriors. Additionally, aluminum’s resistance to corrosion and lightweight properties make it a popular choice for structural frameworks and exterior cladding, especially in modern building designs where aesthetics and durability are key.
3. Consumer Products and Electronics Laser cutting is increasingly used in the production of consumer goods and electronics, where aluminum’s versatility, durability, and lightweight nature are highly valued. Aluminum is frequently used in the design of smartphone bodies, laptop casings, and other electronic enclosures. The precision of laser cutting ensures that the aluminum components have a seamless finish and meet exact specifications. This technology is also used to create parts for household appliances, kitchenware, and even furniture, offering manufacturers flexibility and high-quality results.
Comparison of Aluminum with Other Metals in Laser Cutting
1. Steel vs. Aluminum
- Steel is denser and stronger than aluminum, making it more resilient for heavy-duty applications. However, it also requires higher laser power for cutting due to its toughness. Steel’s lower reflectivity makes it easier to cut with both CO2 and fiber lasers compared to aluminum.
- Aluminum, while lighter and more malleable, is highly reflective, which can create challenges during laser cutting, especially with CO2 lasers. Fiber lasers are more suited for aluminum cutting due to their ability to handle reflectivity. Additionally, aluminum tends to dissipate heat more quickly, which can reduce the risk of warping, but it requires higher precision to avoid cutting defects.
2. Copper vs. Aluminum
- نحاس is another highly reflective material like aluminum, which makes laser cutting difficult without specialized equipment. Fiber lasers are generally used for cutting copper, just as they are for aluminum. However, copper’s thermal conductivity is much higher, meaning it absorbs heat more effectively and requires more laser power than aluminum to cut efficiently.
- Aluminum, on the other hand, is lighter and less dense, making it easier to cut with lasers than copper, particularly for thicker materials. Although both metals pose reflective challenges, aluminum is typically more widely used in industries like aerospace and automotive due to its favorable strength-to-weight ratio.
3. Stainless Steel vs. Aluminum
- Stainless steel is stronger and more corrosion-resistant than aluminum, making it ideal for demanding applications where durability is key. It is relatively easy to cut with lasers, as its reflective properties are lower than aluminum. Laser cutting stainless steel produces clean edges and is highly effective for both thin and thick sheets.
- Aluminum, while not as strong as stainless steel, is much lighter and easier to form. Its reflective nature requires careful attention during laser cutting, but when done correctly, aluminum offers faster cutting speeds than stainless steel, especially when using fiber lasers. Aluminum is preferred in applications where weight reduction is a priority, such as in the automotive and aerospace industries.
This comparison highlights the unique properties of each metal and the considerations involved when using laser cutting technology to process them.
How to Choose a Suitable Laser Cutting Machine
When selecting a laser cutting machine, factors like material type, cost, speed, and available space are crucial. Here’s a breakdown of each factor to guide your decision:
1. Type of Material
For cutting various materials, regular CO2 laser cutters are a popular and straightforward choice. These machines can effectively cut wood, paper, plastic, metals, leather, and rubber with the right power.
However, if you plan to cut reflective materials like aluminum, stainless steel, carbon steel, brass, copper, or titanium, a fiber laser cutter is the better option. While it’s possible to cut reflective materials with a CO2 laser, using a workaround—such as applying a coat of paint to the surface—can improve results when working with aluminum.
2. Price
The cost of laser cutters varies significantly based on their capabilities. High-power and advanced laser cutters generally come at a higher price point, while lower-powered models are more affordable.
While low- or medium-powered lasers can be easier on the budget, they may require more time to cut and have limitations when it comes to handling thicker materials. Typically, CO2 lasers are less expensive than fiber lasers, but the latter provides faster cutting speeds and better performance with reflective materials, making them a worthwhile investment.
3. Material Thickness
The thickness of the material you plan to cut is another critical consideration. A high-power laser cutter is ideal for handling thicker materials efficiently, providing faster cuts and better results.
Conversely, if your focus is on cutting thin materials, a low-powered CO2 laser cutter may suffice, as it is more economical and easier to manage for such tasks.
4. Available Space
Consider your available workspace when selecting a laser cutter. If you need a machine for industrial purposes, be prepared for larger, high-powered machines that occupy more space. These machines are designed to handle substantial workloads and can accommodate various materials.
In contrast, smaller setups for small business operations may require compact machines. Evaluating your business requirements and the physical space available is essential for finding a suitable laser cutter that meets your needs without overcrowding your workspace.
خاتمة
In conclusion, utilizing advanced laser technologies for aluminum laser cutting is crucial for achieving precision, efficiency, and high-quality results in various applications. As aluminum continues to gain popularity across industries due to its lightweight, durability, and versatility, the adoption of suitable laser cutting machines is essential for manufacturers aiming to optimize their fabrication processes.
For industries considering laser cutting for aluminum fabrication, it is recommended to:
- Invest in Fiber Lasers: These machines are specifically designed to handle reflective materials like aluminum, offering superior cutting speeds and precision compared to traditional CO2 lasers.
- Evaluate Material Thickness: Choose a laser cutter that matches the thickness of the aluminum materials you work with to ensure optimal performance and quality cuts.
- Consider Auxiliary Gas Usage: Utilizing nitrogen as an assist gas can enhance cutting quality and minimize oxidation, further improving the overall results.
- Stay Updated with Technology: Keep abreast of the latest advancements in laser cutting technologies to leverage innovative features that can enhance productivity and reduce operational costs.
By focusing on these recommendations, industries can effectively harness the capabilities of advanced laser cutting technologies, paving the way for enhanced efficiency and improved product quality in aluminum fabrication.