آلة الثني الدقة هي عامل رئيسي في ضمان تلبية حجم المنتج وشكل وزواياه لمواصفات التصميم. إذا لم تكن دقة الانحناء عالية بما يكفي، فقد تكون هناك حاجة إلى معالجة ثانوية لتصحيح الانحرافات البعدية أو مشاكل الشكل. وهذا يزيد من تكاليف التصنيع ووقت دورة الإنتاج، ومن خلال تحسين دقة الانحناء، يمكن تجنب خطوة المعالجة الثانوية الإضافية هذه أو تقليلها. يمكن أن تضمن دقة الانحناء العالية إنتاج منتجات تلبي معايير الجودة، وتقليل المنتجات المعيبة ومعدلات الخردة الناجمة عن الانحرافات البعدية، وتقليل هدر المواد الخام وتكاليف الإنتاج، وهو ما يعود بالنفع على الفوائد الاقتصادية والتنمية طويلة الأجل للمؤسسة. فيما يلي بعض الطرق لتحسين دقة آلة الانحناء الخاصة بك:
الصيانة الدورية والمعايرة
من أجل ضمان استقرار ودقة آلة الثني بالإضافة إلى دقة الثني، فإن أعمال الصيانة والمعايرة المنتظمة لا غنى عنها. يمكن للصيانة المنتظمة أن تطيل عمر خدمة آلة الثني بشكل فعال. من خلال التنظيف والتزييت واستبدال الأجزاء البالية، يمكنك تقليل التآكل والتلف في المكونات الميكانيكية والإلكترونية وزيادة متانة المعدات. في الوقت نفسه، يمكن الحفاظ على الاستقرار والدقة. يؤثر استقرار ودقة آلة الثني بشكل مباشر على جودة المنتج النهائي. يمكن للفحص والتعديل المنتظم لهيكل أداة الماكينة ونظام التشحيم والقالب والمكونات الأخرى ضمان استقرار آلة الثني أثناء التشغيل، وتحسين دقة الانحناء، وتجنب اختلافات جودة المنتج الناجمة عن مشاكل المعدات. إذن كيف يتم إجراء الصيانة والمعايرة المنتظمة؟
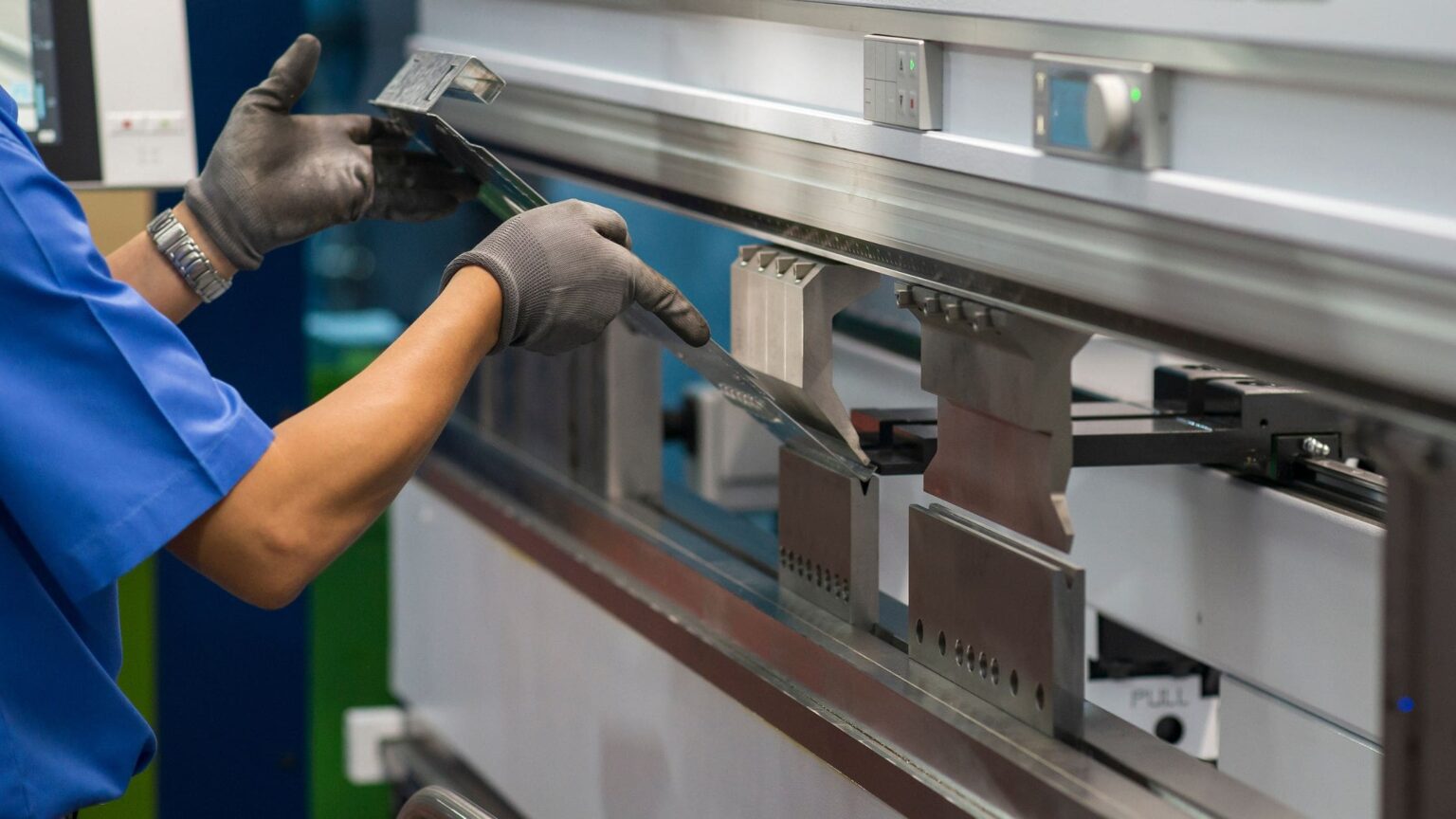
التنظيف والتزييت بشكل منتظم
يعد الحفاظ على نظافة ماكينة الثني أساس الصيانة. قد يؤثر تراكم الغبار ونشارة المعدن على التشغيل الطبيعي للمكونات الميكانيكية. قم بتنظيف سطح الماكينة وقضبان التوجيه والشرائح بانتظام لضمان حرية حركة جميع الأجزاء. في الوقت نفسه، تحقق من نظام التزييت لضمان وجود كمية كافية من مادة التشحيم لمنع التآكل والاحتكاك.
التحقق من هيكل الماكينة
افحص بعناية هيكل أداة الماكينة الخاصة بآلة الثني، بما في ذلك القاعدة والدعامة والجسم. تأكد من عدم وجود شقوق أو تشوهات في هيكل أداة الماكينة، مما قد يؤثر على استقرار مكابح الضغط. إذا وجدت مشاكل، قم بإصلاح أو استبدال الأجزاء التالفة على الفور.
فحص واستبدال قوالب القطع والقوالب
تعتبر القوالب والأجزاء من المكونات الرئيسية لآلة ثني القوالب. افحص بانتظام درجة تآكل القالب والأجزاء. إذا تم العثور على تآكل أو تشوه واضح، فيجب استبدالها في الوقت المناسب لضمان الدقة والجودة أثناء عملية الثني.
فحص النظام الكهربائي
يحتاج النظام الكهربائي لآلة الثني أيضًا إلى فحص منتظم. افحص الكابلات والمستشعرات والمفاتيح ولوحات التحكم للتأكد من أن التوصيلات محكمة وغير تالفة أو بها ماس كهربائي. قم بإصلاح الأعطال الكهربائية على الفور لتجنب التوقف عن العمل وانقطاع الإنتاج.
اختيار المواد وتحسين التسخين المسبق
يعد اختيار المواد أمرًا بالغ الأهمية لدقة الانحناء. تتمتع المواد المختلفة بخصائص ميكانيكية وخصائص تشوه مختلفة. عند اختيار المواد، يجب مراعاة متطلبات الاستخدام والتصميم للمنتج بعناية، ويجب اختيار نوع المعدن وسمكه المناسبين لتقليل احتمالية التشوه. بالإضافة إلى ذلك، يمكن أن يؤدي التسخين المسبق المعتدل للمادة قبل الانحناء إلى تقليل صلابة المادة وتقليل الإجهاد الداخلي، وبالتالي تقليل خطر التشوه وتحسين دقة الانحناء.
تأكد أولاً من أن المادة التي تختارها مناسبة للتسخين المسبق. عادةً، بالنسبة لبعض المواد المعدنية، مثل سبائك الألومنيوم والفولاذ المقاوم للصدأ وما إلى ذلك، يكون تأثير التسخين المسبق أكثر أهمية. يمكننا وضع المادة المراد معالجتها في معدات التسخين وفقًا للشكل والحجم المنحنيين. تأكد من تسخين المقطع العرضي بالكامل للمادة بالتساوي، وتحكم أيضًا في وقت التسخين المسبق لضمان وصول المادة بالكامل إلى درجة الحرارة المطلوبة. يعتمد طول وقت التسخين أيضًا على نوع وسمك المادة، بالإضافة إلى أداء معدات التسخين المسبق. بمجرد وصول المادة إلى درجة حرارة التسخين المسبق واستقرارها، يمكن إجراء عملية الانحناء. أثناء عملية الانحناء، مع أن تصبح المادة أكثر ليونة، يمكن تحقيق شكل الانحناء المطلوب بسهولة أكبر، مما يقلل من خطر الإجهاد الداخلي والتشوه، وبالتالي تحسين دقة الانحناء.
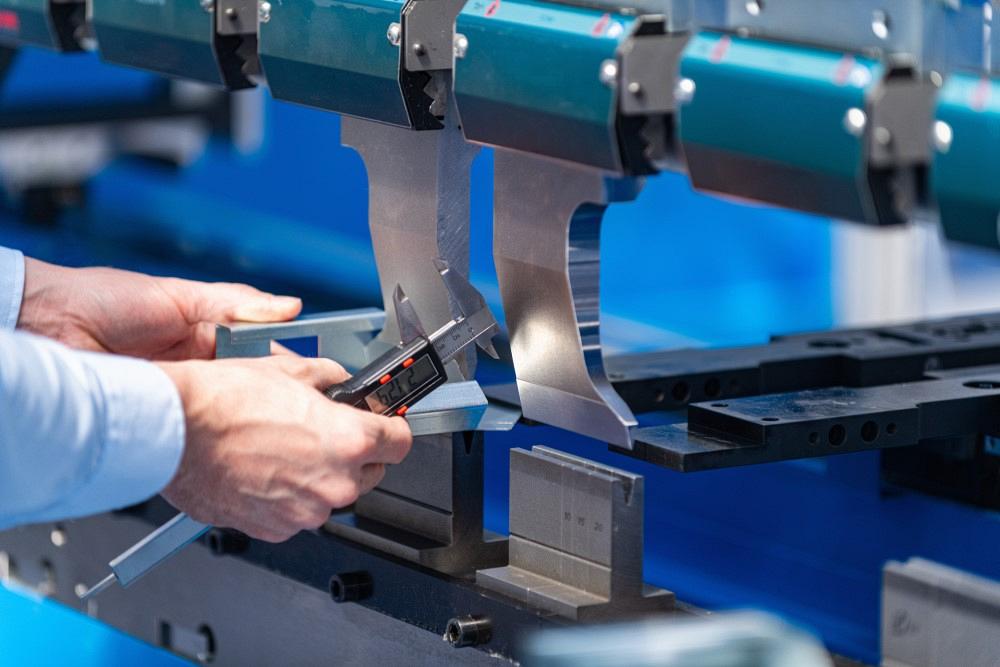
استخدم الدعامات والمشابك عند استخدام آلة الثني
إن استخدام الدعامات والمشابك هو طريقة فعالة لتقليل الأخطاء أثناء عملية الانحناء وتحسين دقة الانحناء. يتضمن هذا المبدأ استخدام دعامات وثباتات إضافية أثناء عملية الانحناء لتثبيت وتقييد قطعة العمل، وبالتالي تقليل التشوه وتحسين دقة التصنيع. أثناء عملية الانحناء، يمكن أن يوفر استخدام الدعامات والمشابك المزيد من نقاط الارتكاز والاستقرار ومنع الحركة غير الضرورية أو تشوه قطعة العمل أثناء عملية الانحناء. يساعد هذا في ضمان بقاء قطعة العمل في وضع ثابت على آلة الانحناء ويقلل من التغييرات غير المنضبطة. بالإضافة إلى ذلك، قد تتأثر قطعة العمل بالانحراف والتشوه أثناء الانحناء، وخاصة أثناء عمليات الانحناء الكبيرة أو المعقدة. باستخدام الدعامات والمشابك، يمكن تقليل انحراف وتشوه قطعة العمل بشكل فعال لضمان ثني قطعة العمل بعد الانحناء. تلبي هندسة قطعة العمل متطلبات التصميم. علاوة على ذلك، يساعد استخدام الدعامات والتثبيتات على توزيع الضغط الواقع على قطعة العمل بشكل أكثر توازناً أثناء عملية الانحناء، مما يساعد على تقليل التشوه المحلي وتركيز الإجهاد، ويحسن الاستقرار العام لقطعة العمل، ويقلل من خطر التشوه.
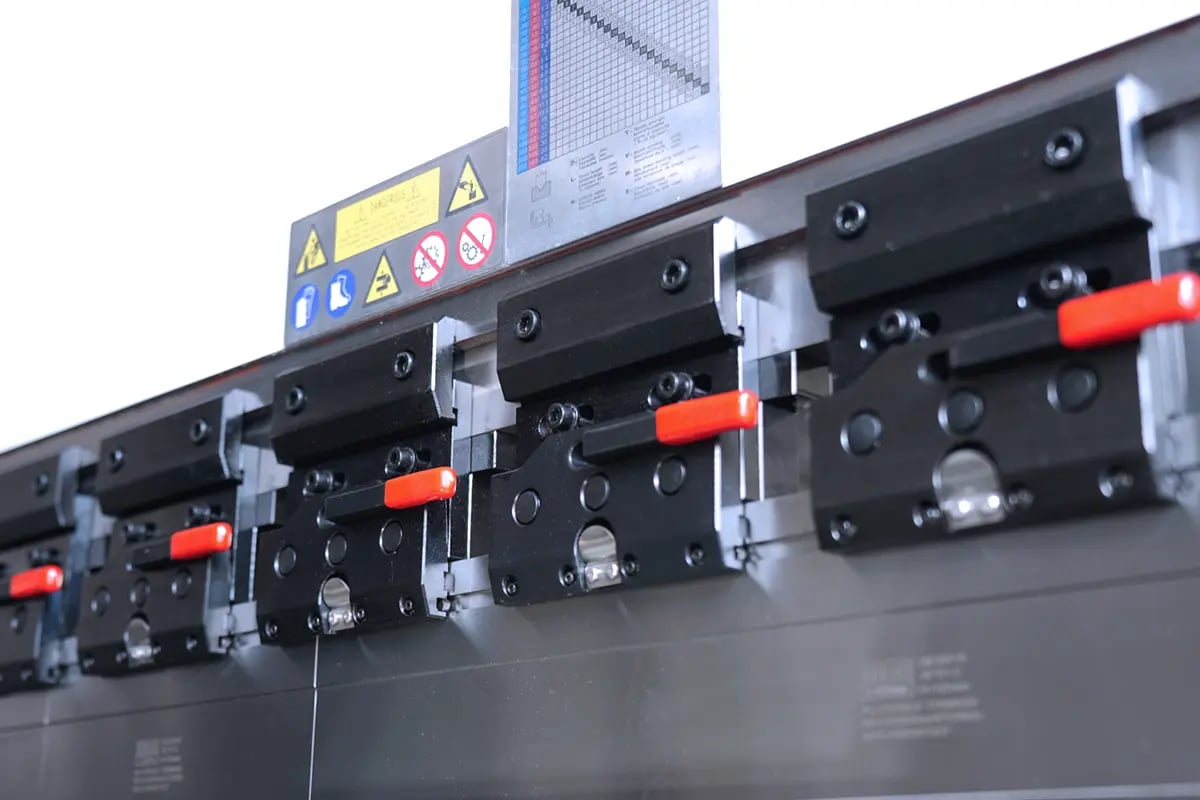
استخدم أنظمة CNC عالية الدقة
يمكن لنظام CNC التحكم بدقة في كل محور من محاور آلة الانحناء، بما في ذلك حركة القوالب العلوية والسفلية المشاركة في الانحناء، وتغذية المواد، وما إلى ذلك. يضمن التحكم في الحركة عالي الدقة دقة وتناسق كل عملية انحناء.
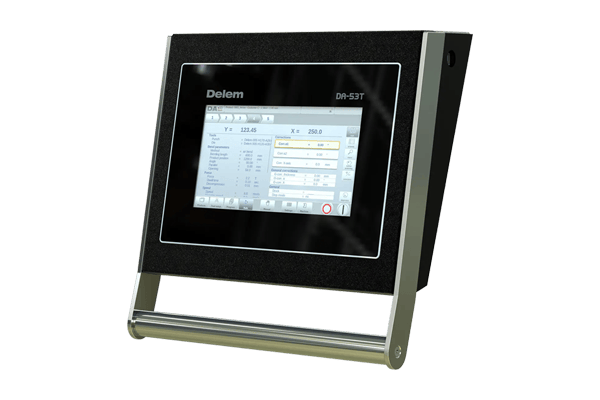
يدعم نظام CNC التحكم متعدد المحاور، والذي يمكنه التحكم في الحركات في اتجاهات مختلفة في نفس الوقت، مما يجعل آلة الانحناء أكثر مرونة في العمليات المعقدة. يمكن للتحكم متعدد المحاور تحقيق عمليات ثني أكثر تعقيدًا وتحسين القدرة على التكيف ودقة آلة الانحناء. يمكن لطريقة التحكم بلغة البرمجة الرقمية (مثل G-code) تحقيق تعديل مفصل لعملية الانحناء من خلال تقنية البرمجة المتقدمة، مما يسمح للمشغلين بتحديد مسار الانحناء والسرعة والقوة والمعلمات الأخرى بدقة. بالإضافة إلى ذلك، عادةً ما تكون أنظمة CNC مجهزة بأجهزة استشعار عالية الدقة لمراقبة المعلمات المختلفة في الوقت الفعلي أثناء عملية الانحناء، مثل موضع المادة وقوة الانحناء وما إلى ذلك. يمكن استخدام هذه البيانات لضبط تعليمات التحكم في الوقت المناسب من خلال نظام التغذية الراجعة، مما يجعل عملية الانحناء أكثر دقة. بشكل عام، يوفر نظام CNC درجة عالية من قدرات التحكم والتعديل لعملية الانحناء من خلال التحكم الدقيق في الحركة والتحكم متعدد المحاور وأجهزة الاستشعار عالية الدقة وأنظمة التغذية الراجعة وتصحيح الانحراف في الوقت الفعلي والوظائف الأخرى، وبالتالي تحسين دقة الانحناء بشكل كبير. كما أنه من المهم أيضًا سبب لماذا آلة ثني CNC تحظى بشعبية كبيرة.