جدول المحتويات
Regular maintenance is crucial for keeping your مكابس الضغط CNC in top condition and ensuring its longevity. As with any precision machinery, proactive care and attention to detail are key to maintaining optimal performance and minimizing downtime. By implementing a comprehensive maintenance program, you can maximize the efficiency and reliability of your مكابس الضغط CNC, ultimately leading to improved productivity and profitability in your metal fabrication operations.
Now, let's delve into the essential aspects of CNC press brake maintenance to help you keep your machine operating smoothly and effectively.
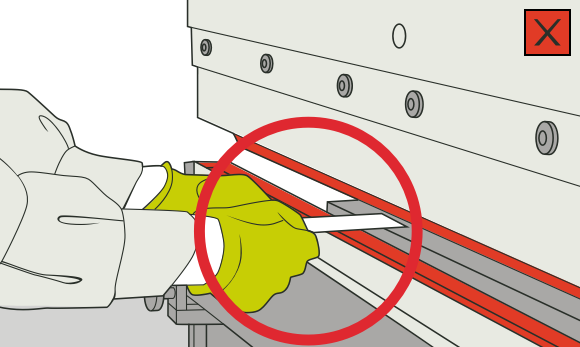
Maintenance Guide for CNC Press Brake
تشحيم
Implement a regular lubrication schedule for all moving parts, including the hydraulic system, ball screws, guide rails, and bearings. Proper lubrication reduces friction, minimizes wear, and extends the lifespan of critical components.
Use high-quality lubricants recommended by the manufacturer and apply them according to specified intervals and quantities. Be sure to clean any excess lubricant to prevent buildup and contamination.
تنظيف
Regularly clean the CNC press brake to remove dust, debris, and metal shavings that can accumulate during operation. Use compressed air or a vacuum cleaner to reach inaccessible areas and ensure thorough cleaning.
Wipe down machine surfaces, control panels, and safety guards with a damp cloth and mild detergent to remove dirt and grease. Regular cleaning helps maintain a safe working environment and prevents corrosion.
تقتيش
Conduct routine inspections of all machine components to identify signs of wear, damage, or misalignment. Focus on critical parts such as the bending beam, tooling, backgauge, and hydraulic system.
Check hydraulic hoses, fittings, and seals for leaks, cracks, or deterioration. Replace any damaged or worn-out components promptly to prevent hydraulic system failures and ensure reliable operation.
Inspect electrical connections, wiring, and safety features such as emergency stop buttons and light curtains to ensure they are functioning correctly and comply with safety standards.
Calibration and Adjustment
Regularly calibrate and adjust the CNC press brake to maintain bending accuracy and repeatability. Use precision measurement tools to verify the alignment of the bending tools and backgauge.
Check and adjust hydraulic pressure, synchronization, and crowning system settings as needed to optimize bending performance. Proper calibration ensures consistent and precise bending results, reducing scrap and rework.
تدريب المشغل
Provide thorough training to operators on proper machine operation, maintenance procedures, and safety protocols. Ensure that operators understand the importance of regular maintenance and adhere to prescribed schedules.
Encourage operators to report any abnormal machine behavior, unusual noises, or signs of wear promptly for inspection and resolution. Operator vigilance plays a crucial role in identifying potential issues before they escalate into major problems.
خاتمة
By following these maintenance practices diligently, you can ensure that your CNC press brake operates smoothly, reliably, and efficiently, leading to improved productivity and reduced downtime in your metal fabrication operations. Regular maintenance not only prolongs the lifespan of your equipment but also enhances safety and quality in the workplace.