Industrial Press brakes play a critical role in various manufacturing processes; shaping metal sheets and plates to precise specifications. To ensure the longevity and efficiency of these essential machines, proper maintenance is a must. Neglecting maintenance can lead to costly downtime and reduced productivity. In this blog, we will explore the key aspects of maintaining industrial press brakes to keep them in optimal working condition.
Industrial Press Brake Cleaning And Lubrication
Just like any other piece of machinery, industrial press brakes require regular cleaning and lubrication to prevent the accumulation of dirt, dust, and debris. Cleaning the machine components, especially the hydraulic system, is important to prevent contamination, which leads to reduced performance and damage over time. Press brakes also require the lubrication of moving parts to minimize friction and wear. We recommend referring to the manufacturer’s recommendations for the appropriate lubricants and cleaning procedures.
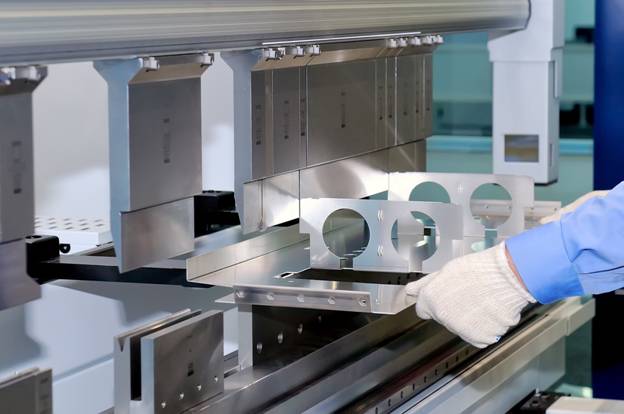
Hydraulic System Maintenance
The hydraulic system is the heart of a hydraulic press brake. To keep the brake performing at optimal levels it is crucial to keep it in prime condition. Here are some key hydraulic system maintenance tips:
a. Check for Leaks: Regularly inspect the hydraulic lines, hoses, and fittings for any signs of leakage. Leaks can lead to reduced hydraulic pressure and inefficient operation.
b. Change Hydraulic Fluid: Change the hydraulic fluid at the recommended intervals to maintain its viscosity and performance. Use the manufacturer’s recommended hydraulic oil.
c. Filter Replacement: Regularly replace hydraulic filters to ensure clean oil circulation and prevent contamination.
Our in-stock press brakes come standard with servo-hydraulic valves. These press brakes allow for increased working speeds and precision while saving on energy costs. Our servo-hydraulic system also makes for easier maintenance and a quieter standby operating volume.
Die and Punch Maintenance
The press brake punches and dies are crucial components that shape the materials. Regularly inspect and maintain them to ensure precise bending and reduce the risk of defects in the finished products.
a. Check for Wear: Examine the dies and punches for signs of wear or damage. If they are no longer in good condition, replace them promptly to maintain the quality of the products.
b. Alignment: Ensure that the dies and punches are properly aligned. Misalignment can lead to uneven bending and poor product quality.
c. Cleaning: Keep the dies and punches clean to prevent material buildup, which can affect bending accuracy and damage the tools.
Backgauge and Positioning System
The backgauge and positioning system in an industrial press brake are critical for achieving accurate and consistent bends. Regularly calibrate and maintain these components to ensure precise results.
a. Inspection: Regularly inspect the backgauge and positioning system for alignment, wear, and damage. Make necessary adjustments and replacements as needed.
b. Lubrication: Ensure that the backgauge and positioning system is well-lubricated to maintain smooth and precise movement.
Electrical and Control System
The electrical and control system of an industrial press brake is responsible for its automation and accuracy. Regularly inspect the electrical components and connections to prevent malfunctions.
a. Check Wiring: Inspect the electrical wiring and connections to ensure they are secure and free from damage.
b. Software Updates: Keep the control system’s software up-to-date to benefit from any enhancements or bug fixes provided by the manufacturer.
Safety Measures
We all know how important safety is in any industrial setting. Ensure that safety features, such as guards, interlocks, and emergency stop buttons are regularly inspected and maintained. Additionally, employees operating the press brake should be well-trained in safety procedures and operation of these safety features.
How Often Should You Maintain Your Press Brake?
The frequency of maintenance for an industrial press brake can vary depending on several factors, including its usage, environmental conditions, and the manufacturer’s recommendations. However, here are some general guidelines on how often you should maintain your press brake:
Daily Maintenance:
Clean the machine and surrounding area daily to remove dust, debris, and swarf.
Check for any loose or damaged parts and tighten or replace them as needed.
Verify that safety features, such as guards and emergency stop buttons, are functioning correctly.
Weekly Maintenance:
Lubricate moving parts, including guides and ball screws, on a weekly basis.
Inspect hydraulic hoses, fittings, and connections for leaks or damage.
Check the condition of the backgauge and positioning system, including alignment and calibration.
Monthly Maintenance:
Inspect the dies and punches for wear and damage. Replace them if necessary.
Examine the hydraulic system for signs of contamination or abnormal noise.
Verify the alignment of the machine’s components.
Quarterly Maintenance:
Change the hydraulic fluid and filters as recommended by the manufacturer.
Inspect the electrical components and connections for any issues.
Review and adjust the hydraulic pressure as necessary to match the material being processed.
Annual or Biannual Maintenance:
Conduct a thorough inspection of the machine’s overall condition.
Perform more in-depth maintenance tasks, such as calibrating the machine and performing any required alignments.
Review and update the control system software if updates are available.
It’s important to note that these are general guidelines, and your specific press brake may have different maintenance requirements. Always consult the manufacturer’s maintenance manual or guidelines for your particular machine, as they will provide the most accurate and detailed information regarding maintenance schedules and procedures. Additionally, if your press brake sees heavy or continuous use, you may need to increase the frequency of maintenance to ensure its optimal performance and longevity.
خاتمة
Proper maintenance of industrial press brakes is crucial for ensuring their long-term reliability, precision, and safety. By following these quick tips listed above, you can ensure your press brake operates for many years to come at high efficiency. However, if your press brake requires servicing beyond your capabilities, Krrass Machine Tools can help you; even if you didn’t buy your machine from us. Our service technicians are U.S.-based and have minimum response times. We offer service to a wide variety of press brake manufacturers including Trumpf, Amada, Accurpress, Bystronic, and Cincinnati. Reach out today to see what our service technicians can do for you.