أ مكابح الضغط المعدنية آلة أساسية تستخدم في تصنيع المعادن لثني وتشكيل الصفائح والألواح المعدنية بدقة. تتوفر بأنواع مختلفة، بما في ذلك النماذج الهيدروليكية والميكانيكية والنماذج ذات التحكم الرقمي بالحاسوب، حيث يوفر كل نوع فوائد فريدة تناسب احتياجات الإنتاج المختلفة. سواء تم استخدامها في ورش عمل صغيرة أو تصنيع واسع النطاق، توفر مكابس الثني المعدنية التنوع والكفاءة المطلوبة لتلبية متطلبات الثني المعقدة في الصناعة.
ما هي مكبس الكبح المعدني؟
أ مكابح الضغط المعدنية آلة قوية مصممة لمهام تشغيل المعادن، تستخدم في المقام الأول لثني وتشكيل صفائح المعادن بدقة وإتقان. وهي مزودة بنظام هيدروليكي أو ميكانيكي، وتمارس قوة هائلة على المعدن، مما يتيح ثنيه بزوايا وأشكال محددة.
تتميز مكابس الثني بتعدد استخداماتها ويمكنها التعامل مع مجموعة واسعة من تطبيقات الانحناء، مما يجعلها لا غنى عنها في الصناعات مثل صناعة السيارات والفضاء والبناء والتصنيع. تُستخدم عادةً لإنشاء أجزاء للآلات والمركبات والأجهزة والهياكل المعمارية.
تتضمن عملية مكبس الثني المعدني تثبيت الصفيحة المعدنية بين المثقب والقالب، واللذين يتم وضعهما بدقة لتحقيق زاوية الانحناء المطلوبة. يطبق المثقب قوة على المعدن، مما يتسبب في تشوهه وانحناءه على طول القالب. تضمن هذه الدقة أن يكون كل انحناء متسقًا ويلتزم بالمواصفات اللازمة.
تتمثل إحدى الفوائد الرئيسية لاستخدام مكابس الثني المعدنية في قدرتها على إنتاج انحناءات وأشكال معقدة مع إمكانية تكرار عالية، مما يجعلها مثالية لتصنيع كميات كبيرة من الأجزاء المتطابقة بجودة ثابتة. بالإضافة إلى ذلك، يمكن برمجة مكابس الثني لتنفيذ انحناءات متعددة في عملية واحدة، مما يعزز الكفاءة والإنتاجية.
بالإضافة إلى الثني، فإن بعض مكابس الثني مجهزة لأداء مهام إضافية مثل التشكيل والقص والثقب. هذه القدرة على التكيف تجعل مكابس الثني أداة قيمة في تصنيع المعادن، وقادرة على التعامل مع مجموعة واسعة من المهام باستخدام آلة واحدة فقط.
باختصار، تعد مكبسات الثني المعدنية آلة موثوقة وفعالة توفر إمكانيات ثني دقيقة. كما أن تنوعها وقدرتها على تلبية احتياجات الثني المتنوعة تجعلها من الأصول المهمة في عمليات تشغيل المعادن.
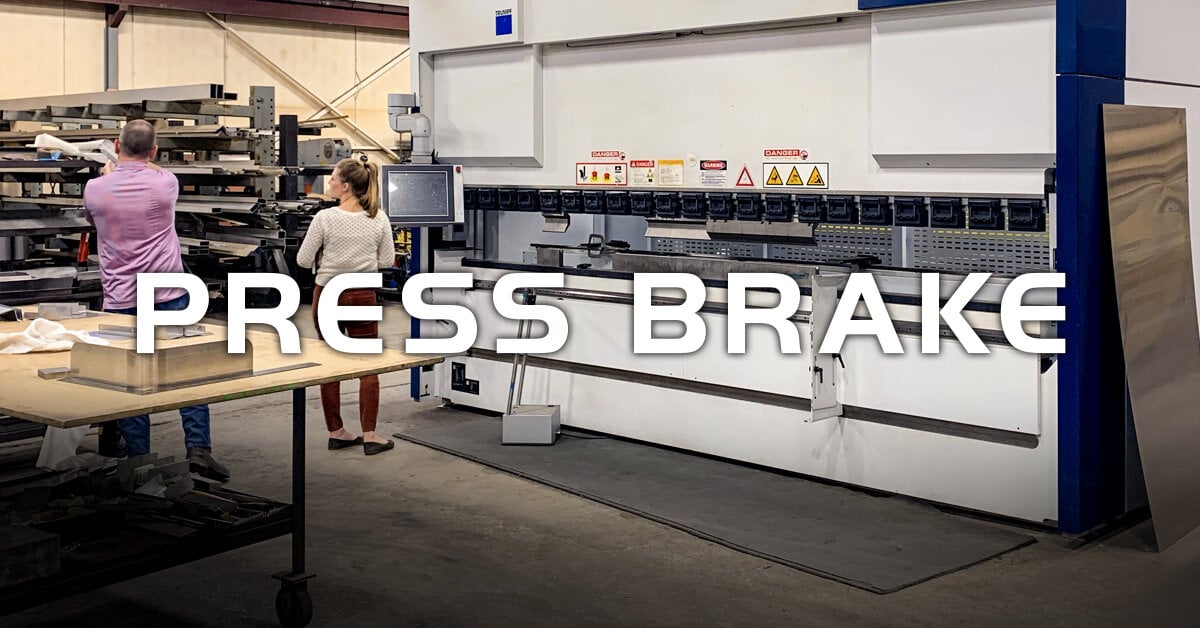
المكونات والوظائف الرئيسية
الإطار والسرير هما العنصران الأساسيان لآلة ثني الثني. وهما مصنوعان من الفولاذ الثقيل ويتحملان القوة الناتجة عن عملية الثني. والسرير هو سطح أفقي توضع عليه قطعة العمل. والإطار يدعم المكبس والقالب.
يعد الكبش والقالب من الأجزاء الأساسية في مكبس الثني المعدني. الكبش هو جزء يتحرك رأسيًا، ويترك ضغطًا على قطعة العمل ويجعلها تنحني حول القالب. القالب هو أداة قابلة للتغيير مصممة لضمان زاوية ومعامِلات مكبس الثني.
يعد المقياس الخلفي أيضًا جزءًا مهمًا من مكبس الثني، والذي يضمن الموقع الدقيق لقطعة العمل المراد ثنيها. وهو يتألف من العديد من أصابع التوقف المحاذية للخطوط المنحنية ويوجه قطعة العمل إلى الموقع الصحيح. يمكن تعديل المقياس الخلفي يدويًا أو آليًا لاستيعاب أحجام الانحناء المختلفة.
تتضمن الوظيفة الرئيسية لوحدة التحكم معلمات الانحناء ومراقبة الضغط والتأكد من تشغيل الماكينة ضمن مواصفاتها.
الأنواع الرئيسية من مكابس الثني المعدنية
مكابس الكبح الميكانيكية
تعتبر مكبسات الثني الميكانيكية من أكثر الأنواع استخدامًا. تعمل من خلال نظام يعمل بمحركات كهربائية، والتي توفر الطاقة لعجلة الموازنة التي تدور بسرعة. يتحكم المشغل في عجلة الموازنة من خلال آلية القابض. تشتهر مكبسات الثني الميكانيكية ببساطتها، وخاصة فيما يتعلق بالمكونات الإلكترونية، وهي سهلة التشغيل والصيانة. ومع ذلك، بمجرد تشغيل الكبش، يجب إكمال الدورة الكاملة، وإذا كانت الشوط طويلًا جدًا، فقد تقفل الآلة، مما يشكل مخاطر محتملة على السلامة.
- الايجابيات:تكلفة منخفضة، عملية بسيطة
- سلبيات:دقة وقوة وتحكم محدودين
مكبس الفرامل الهيدروليكي
تستخدم مكابس الثني الهيدروليكية أنظمة هيدروليكية لدفع الكبش للأسفل، مما يوفر تحكمًا ودقة أكبر مقارنة بالنماذج الميكانيكية. مع وجود أسطوانات متعددة، يمكن للمشغلين إدارة الانحناءات الأكثر تعقيدًا، مما يجعل هذا النوع من مكابس الثني مثاليًا للعمليات المخصصة والدقيقة. يمكنها التكيف بسهولة مع سماكات المعادن المختلفة، مما يسمح بالانحناء المعقد والسلس. على الرغم من أنها أكثر تكلفة عادةً، إلا أن مكابس الثني الهيدروليكية مفضلة لتعدد استخداماتها وأدائها المحسن.
- الايجابيات:دقة أعلى، وتحكم، وقوة؛ تستوعب مواد مختلفة
- سلبيات:تكلفة أعلى، عملية أكثر تعقيدًا، محدودة بالوزن المقدر لها
مكابس الضغط CNC
إن مكابس الثني ذات التحكم الرقمي بالكمبيوتر هي آلات متطورة يتم التحكم فيها بواسطة تكنولوجيا الكمبيوتر، وتوفر إمكانية التخصيص والدقة الاستثنائية. يقوم المشغلون بإدخال البيانات الرئيسية، مثل زاوية الانحناء وسمك الورقة وعرضها، في وحدة التحكم من أجل تشغيل عالي الكفاءة والدقة. هذا النوع مثالي للأشكال والزوايا المعقدة، حيث يوفر مستويات عالية من الدقة مع سهولة الاستخدام.
- الايجابيات:دقة عالية، وسهولة التشغيل، والتعامل مع مجموعة متنوعة من الأشكال والزوايا
- سلبيات:التكلفة العالية والقيود المفروضة على المواد شديدة الانعكاس أو الهشة
فوائد مكابح الضغط المعدنية
تتميز مكابس الضغط بالعديد من المزايا، مما يجعلها لا غنى عنها لصناعة الصفائح المعدنية. وتلعب دورًا محوريًا في صناعة الصفائح المعدنية.
تشغيل سهل: تعتبر آلة ثني الثني واحدة من أبسط الأجهزة. وبالمقارنة بالآلات الأخرى، فهي لا تتطلب مشغلين ذوي مهارات عالية.
دقة عالية: الدقة هي مفتاح التعامل مع المعادن. يمكن لآلة ثني المعادن أن توفر دقة أعلى مقارنة بآلات ثني المعادن الأخرى لأنها تستخدم لكمة وقوالب لتشكيل المعدن، مما يحقق ثني المعدن بزاوية دقيقة.
أكثر مرونة:بالمقارنة بالآلات الأخرى، يمكن لآلة ثني المعادن ثني مكونات صغيرة وكتل كبيرة من المعادن. وتتميز بمرونة كبيرة في تطبيقات مختلفة بسبب توافقها مع أحجام متعددة من الصفائح المعدنية.
تحسين الإنتاجية: تعتبر آلة ثني المعادن أكثر كفاءة من الطرق الأخرى لثني المعادن. فهي قادرة على ثني العديد من المعادن في وقت واحد، وبالتالي تحسين الإنتاجية.
تقليل نفايات المواد: بالمقارنة مع الأجهزة الأخرى، توفر مكبس الثني دقة عالية. وهذا يعني تقليل هدر المواد، مما يجعلها أكثر كفاءة وفعالية من حيث التكلفة.
تكلفة منخفضة: تكلفة القالب المستخدم بواسطة مكابح الضغط منخفضة نسبيًا، ولكنها تتمتع بعمر طويل، مما يزيد من إمكانية الوصول الاقتصادي في عملية تشكيل الصفائح المعدنية وثنيها.
تحسين الأمان: إن آلة ثني المعادن أكثر أمانًا من طرق ثني المعادن الأخرى. وذلك لأنه لا توجد حاجة لتسخين المعدن قبل الثني، وبالتالي تقليل خطر الإصابة. إن آلة ثني المعادن الحديثة مجهزة بالعديد من التدابير الوقائية، مثل أجهزة استشعار الليزر. وعندما يتعرض العامل للإصابة، فإن أجهزة الاستشعار ستوقف عملية تشغيل المعدن.
التنوع: يمكن لآلة الثني الحديثة التعامل مع العديد من أشكال الكوع. علاوة على ذلك، يمكنها ثني سماكات مختلفة من الصفائح المعدنية.
يستخدم للنماذج الأولية: الميزة الرئيسية لآلات ثني الثني هي سهولة إعدادها وتغيير الأدوات، مما يسمح بالتبديل السريع واختبار التصميمات والأشكال المختلفة أثناء النماذج الأولية.
التكنولوجيا الذكية: توفر آلة ثني الضغط CNC حلول حل أوتوماتيكية متقدمة لثني المعادن، مما يجعل آلة ثني الضغط الحديثة تقنية ذكية للغاية.
تتويج: عند ثني قطعة عمل طويلة، قد يكون هناك انحراف ملحوظ بين زوايا التشكيل في المنتصف والجوانب، مما يتسبب في زوايا انحناء غير متساوية. ومع ذلك، تتميز مكبس الثني بوظيفة التتويج لضبط كل موقع من الزاوية، مما يضمن ثني الخط وتقليل متطلبات التعديل اليدوي والصيانة.
عيوب آلات مكابح الضغط
التكلفة الأولية العالية:يتطلب الاستثمار في مكبس الثني رأس مال أولي كبير بسبب سعر الشراء والصيانة المستمرة. كما تزيد المعدات المتخصصة وتدريب المشغل من تكاليف الإعداد الأولية. كما تستهلك مكبس الثني قدرًا كبيرًا من الطاقة، مما يزيد من تكاليف التشغيل. بالنسبة للشركات الصغيرة، قد تكون الطرز المتطورة المزودة بميزات الأتمتة باهظة الثمن بشكل لا يطاق.
يتطلب ضغطًا عاليًا:تعمل مكابس الضغط تحت ضغط مرتفع، مما يجعلها غير مناسبة للمواد الرقيقة، حيث أن القوة المفرطة قد تسبب تشوهًا. بالإضافة إلى ذلك، فإن بيئة الضغط العالي تشكل مخاطر تتعلق بالسلامة، ويجب على المشغلين المدربين فقط التعامل مع الماكينة للتخفيف من المخاطر المحتملة.
يقتصر على الهندسة البسيطة:في حين أن مكابس الضغط قادرة على إنتاج انحناءات بسيطة بكفاءة، إلا أنها محدودة عندما يتعلق الأمر بإنشاء أشكال أكثر تعقيدًا مثل المنحنيات أو اللوالب. أما بالنسبة للأشكال الهندسية الأكثر تعقيدًا، فإن هناك حاجة إلى طرق بديلة مثل الختم أو التشكيل الهيدروليكي.
يتطلب تدريبًا احترافيًا:يعد التدريب المناسب أمرًا ضروريًا لتشغيل مكبس الثني بأمان وفعالية. يجب أن يفهم المشغلون مبادئ عمل الماكينة، وكيفية وضع المواد بشكل صحيح، والمخاطر المرتبطة بالعمليات ذات الضغط العالي. تساعد هذه المعرفة في تقليل احتمالية وقوع الحوادث أو الإصابات.
متطلبات المساحة:بسبب حجمها الكبير، تتطلب مكابح الضغط كمية كبيرة من مساحة ورشة العمل للتركيب والتشغيل المناسبين.
الضوضاء والاهتزاز:قد تولد مكابس الضغط ضوضاء كبيرة أثناء التشغيل، مما يتطلب من المشغلين استخدام واقيات الأذن. وقد تتسبب الماكينة أيضًا في حدوث اهتزازات تؤثر على بيئة العمل.
صيانة:الصيانة الدورية ضرورية للحفاظ على مكبس الثني في حالة جيدة والحفاظ على جودة المنتج. يجب تنظيف الماكينة وصيانتها بشكل روتيني لضمان الأداء الأمثل.
خطر كسر المواد:أثناء عملية الانحناء، قد تتكون نتوءات أو طبقات أكسيد على طول حواف وزوايا المادة، مما يزيد من خطر حدوث الشقوق أو الكسور. وهذا شائع بشكل خاص في المواد التي تتعرض لضغط مرتفع أثناء الانحناء.
كيف تعمل مكبس الفرامل المعدنية؟
إن مكبس الثني المعدني عبارة عن آلة قوية ومتعددة الاستخدامات تستخدم في عمليات تشغيل المعادن لثني وتشكيل الصفائح المعدنية بدقة وإتقان. ولكن كيف تعمل بالضبط؟
تتضمن عملية مكبس الثني المعدني عدة مكونات وخطوات رئيسية:
- تثبيت الصفائح المعدنية:الخطوة الأولى هي تأمين الصفيحة المعدنية بين المثقب والقالب. المثقب هو الأداة العلوية التي تطبق القوة على الصفيحة، بينما القالب هو الأداة السفلية التي توفر الدعم وتحدد شكل الانحناء.
- تطبيق القوة:بمجرد تثبيت الصفيحة المعدنية، تطبق مكبس الثني قوة هائلة على الصفيحة من خلال المثقب. تتسبب هذه القوة في ثني المعدن واتخاذه الشكل المطلوب.
- التحكم في زاوية الانحناء:يمكن للمشغل التحكم في زاوية الانحناء عن طريق ضبط موضع المثقب والقالب. وهذا يسمح بالانحناء الدقيق والمتقن وفقًا لمواصفات المشروع.
- قابلية التكرار:تتمثل إحدى المزايا الرئيسية لآلة ثني المعادن في قدرتها على إنتاج انحناءات متسقة وقابلة للتكرار. ويتحقق ذلك من خلال استخدام أنظمة هيدروليكية أو ميكانيكية دقيقة تضمن تطبيق نفس مقدار القوة على كل انحناء.
- العمليات الإضافية:تتميز بعض مكابس الثني بخصائص إضافية تسمح بعمليات أخرى مثل التشكيل والقص والثقب. وهذا التنوع يجعل مكابس الثني من الأصول القيمة في أي عملية تشغيل للمعادن.
بشكل عام، تعمل مكبسات الثني المعدنية عن طريق تثبيت الصفيحة المعدنية بين المثقب والقالب، وتطبيق القوة لثني الصفيحة، والسماح بالتحكم الدقيق في زاوية الانحناء. إن قدرتها على إنتاج انحناءات متسقة وقابلة للتكرار تجعلها أداة لا غنى عنها في صناعة تشغيل المعادن.
العوامل التي يجب مراعاتها عند اختيار مكبس الثني المعدني
اختيار الحق مكابح الضغط المعدنية يتطلب الأمر تقييمًا دقيقًا للعديد من العوامل الرئيسية. فيما يلي بعض الجوانب المهمة التي يجب وضعها في الاعتبار عند اتخاذ قرارك:
- نوع المعدن:إن النوع المحدد من المعدن الذي تخطط للعمل به أمر ضروري لتحديد مكبس الثني المناسب. فالمعادن المختلفة لها مستويات صلابة مختلفة وتتطلب قوى ثني محددة. تأكد من أن مكبس الثني الذي تختاره قادر على التعامل مع المادة التي ستقوم بمعالجتها.
- سمك المعدن:يلعب سمك الصفائح المعدنية دورًا رئيسيًا في عملية الاختيار. تتمتع كل مكبس ثني بقدرة ثني مختلفة، لذا من المهم اختيار واحدة يمكنها استيعاب سمك الصفائح المعدنية لديك. إذا كان عملك يتضمن مجموعة من السماكات، فاختر مكبس ثني بإعدادات قابلة للتعديل لتوفير المرونة.
- دقة الانحناء:الدقة أمر أساسي في أعمال المعادن، وخاصة لمهام الثني. ضع في اعتبارك مستوى الدقة المطلوب لمشاريعك واختر مكبسًا يلبي متطلبات الدقة الخاصة بك. للحصول على دقة عالية وإمكانية تكرار، مكابس الضغط CNC يعد خيارًا شائعًا.
- حجم الإنتاج:يعد حجم الإنتاج عاملاً مهمًا آخر. إذا كنت بحاجة إلى التعامل مع أحجام كبيرة، فابحث عن مكبس ثني بأوقات دورة أسرع وخيارات أتمتة لتحسين الإنتاجية. بالنسبة للإنتاج على نطاق أصغر، قد يكون استخدام مكبس ثني يدوي أو شبه آلي أكثر فعالية من حيث التكلفة.
- مميزات اضافية:اعتمادًا على احتياجاتك المحددة، قد ترغب في استكشاف مكابس الثني التي توفر ميزات إضافية مثل مقاييس الظهر، أو مجموعة متنوعة من خيارات الأدوات، أو آليات الأمان المحسنة. يمكن لهذه العناصر الإضافية تحسين كفاءة الماكينة وضمان عمليات تشغيل المعادن بسلاسة.
من خلال تقييم هذه العوامل، يمكنك اختيار مكابح الضغط المعدنية ما يناسب متطلباتك الفريدة على أفضل وجه. خذ الوقت الكافي لتقييم احتياجاتك المحددة واطلب المشورة من الخبراء عند الضرورة لاتخاذ الاختيار الأكثر استنارة لمشاريعك المتعلقة بمعالجة المعادن.
خاتمة
أ مكابح الضغط المعدنية تُعد هذه المادة حجر الأساس في عالم تصنيع المعادن، حيث توفر تنوعًا ودقة وكفاءة لا مثيل لها لصناعات مثل صناعة السيارات والفضاء والبناء والتصنيع. تضمن قدرتها على ثني مواد وسمك مختلفين بدقة عالية نتائج موحدة ومتسقة تعمل على تبسيط عمليات الإنتاج.
بالإضافة إلى تقليل العمالة والوقت المرتبطين عادةً بالثني اليدوي، أثبتت مكبسات الثني أنها حل فعال من حيث التكلفة، خاصة عند النظر في قدرتها على أداء مهام إضافية مثل التشكيل والقص والثقب. تجعلها هذه الوظائف المتعددة أداة لا تقدر بثمن لمجموعة واسعة من احتياجات تشغيل المعادن.
يتطلب اختيار مكبس الثني المعدني المناسب دراسة متأنية لعوامل رئيسية، بما في ذلك نوع وسمك المادة، ودقة الانحناء المطلوبة، وحجم الإنتاج. من خلال تقييم هذه الجوانب بدقة -والاستعانة بإرشادات الخبراء عند الحاجة- يمكنك ضمان أن مكبس الثني الذي تختاره سيلبي احتياجاتك المحددة.
إن الاستثمار في مكبس ثني المعادن من شأنه أن يرفع من مستوى عمليات تشغيل المعادن لديك، مما يتيح لك إنتاج ثنيات دقيقة وعالية الجودة بسهولة وكفاءة. ونظراً لمزاياها العديدة، فإن مكبس ثني المعادن يعد أداة أساسية حقاً لأي محترف أو شركة تعمل في مجال تشغيل المعادن.