Metal fabrication is an ideal candidate for automation, as many processes are repetitive and require a high degree of precision—conditions that are perfectly suited for industrial robots. Automated laser cutting, in particular, can greatly benefit from the introduction of automation, leading to significant efficiency improvements.
However, despite its advantages, factory automation requires thorough planning. The primary obstacles to automation often revolve around costs. Robotics come with high upfront expenses and typically need time to generate a return on investment. To maximize the benefits of these investments, careful implementation is essential.
Follow these five steps to successfully incorporate automated laser cutting into your processes.
1. Automate front-end tasks.
One challenge machinists often run into after implementing automation is new, unintentional bottlenecks. Automated laser-cutting systems can produce two to four times more parts in the same time as manual processes. If the rest of your workflow does not likewise accelerate, the differences in speed will restrict your overall productivity.
The solution here is to automate front-end tasks like data entry and processing through robotic process automation (RPA.) Employing software robots will ensure your order management can keep pace with the rest of your factory automation. Consequently, you’ll prevent bottlenecks from occurring around your laser-cutting processes and improve your total efficiency.
Implementing RPA in addition to laser-cutting robots will mean higher upfront costs and potentially more disruption before employees get used to new workflows. At the same time, it will lead to more dramatic efficiency improvements, generating a positive ROI sooner. That way, you get all you can out of your robotics investments.
2. Program for material efficiency.
Automation alone will not necessarily lead to remarkable productivity improvements. The efficiency of your automated laser-cutting system largely depends on how you program it. When the time comes to program your robots, aim for higher material efficiency, requiring pre-set material yields wherever possible.
Many machines can be programmed to use a stated percentage of the materials for each sheet of metal. Doing this will ensure you create more parts per sheet, minimizing waste and eventually leading to reduced material costs. While this programming may not speed up your metal fabrication process, it will increase profits by lowering expenses.
Another step to raise your laser-cutting efficiency is to combine orders based on like materials and thicknesses. Remember, though, that metal thickness determines cutting speed, so if you combine multiple orders on a thick sheet, it will slow down the process. Plan your production schedule accordingly to accommodate your machine’s varying cutting speeds when stacking orders.
3. Purchase equipment in stages.
Another thing to consider when automating metal fabrication processes is how you can offset the costs. One of the most effective cost mitigation strategies with factory automation is to automate in stages instead of all at once. While it may be tempting to apply automation everywhere from the start, this will incur high costs and likely will disrupt your workflows.
Many automated laser-cutting systems are modular, allowing you to automate one part of the process at a time. Start with the area with the highest potential for savings, then slowly automate other, lower-priority tasks. As you automate further, remember to use worker feedback to scale up more effectively.
A 2020 survey found that 65% of successful automation initiatives used people’s feedback to train automation solutions, compared to just 24% of unsuccessful operations. Embracing a slow, modular approach to automation while using workers’ experience to guide you will mitigate costs and lead to higher ROIs.
4. Automate loading and unloading.
As you automate, remember to consider more than just the cutting process itself. Just as front-end bottlenecks can limit laser cutting automation’s efficiency, so can later processes like unloading. Loading and unloading may not seem like time-consuming tasks, but they’re easy to automate, and small changes can lead to considerable improvements over time.
You may be able to automate loading and unloading with little more than a conveyor belt. Even more delicate operations likely will not need more than a robotic arm and some sensors to guide it. These motions are simple and repetitive, making them ideal for automation. Automating them will ensure the entire line can match the laser cutter’s efficiency.
While they may seem like minor tasks, loading and unloading are common points of inefficiency. Automating them can take your beam-on time up to 80% or more, while average times linger around 30% to 40%. If you don’t automate loading and unloading, you’re not using your laser cutting automation to its fullest extent.
5. Monitor key performance indicators.
One of the most common mistakes in factory automation is overlooking the importance of KPIs. Many shops will automate without measuring their performance before or after, hindering the efficacy of these investments. If you hope to make wise automation decisions, you must thoroughly monitor the processes under consideration.
Before automating, gather data on your metal fabrication KPIs to establish a baseline for comparison. After introducing any type of automation capability, continue to monitor those KPIs, looking for both positive and negative changes. Any differences will reveal the extent to which your automation was effective, guiding your future automation decisions.
Without benchmarking data, it will be difficult to understand how automation improved your processes. If you don’t have quantifiable data to reference, you’ll end up relying primarily on guesswork when trying to replicate past successes or avoid making the same failures. As such, it is essential that you monitor KPIs before and after automating.
6. Proper planning maximizes automation’s potential.
Metal fabrication may be an ideal application for automation, but these benefits will not come automatically. Effective factory automation relies on thorough planning and careful implementation. If you follow these steps, you can use maximize the value and performance of laser cutting automation – and mitigate any related challenges.
Automation can be expensive and intimidating, but with the right approach, it does not have to cause much disruption. These guidelines will help you see how to implement automation most effectively, minimizing upfront costs and accelerating ROIs. You can then be sure your investment will deliver all it can.
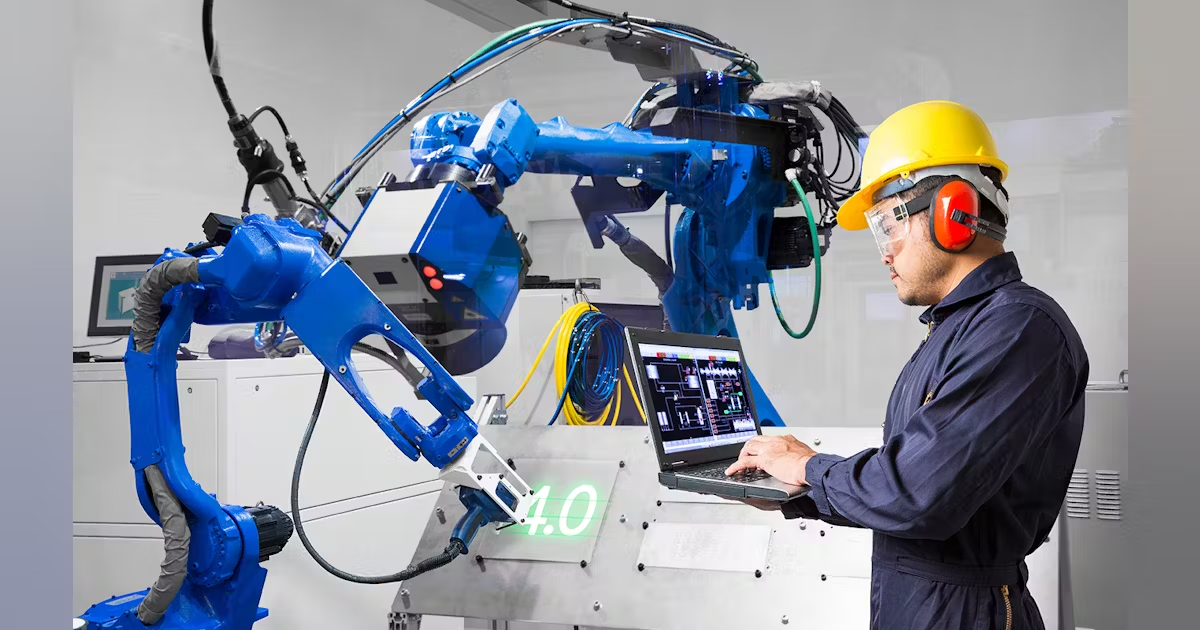
Top 5 Advantages of Implementing Automated Laser Cutting Technology
In today’s competitive manufacturing landscape, automation is transforming industries by delivering significant improvements in efficiency, precision, and cost management. One of the key areas benefiting from this technological shift is laser cutting. Automated laser cutting technology combines advanced robotics and laser precision to revolutionize metal fabrication processes. Let’s explore the top five advantages of integrating automated laser cutting into your operations.
1. Increased Precision and Accuracy
One of the most notable benefits of automated laser cutting technology is the remarkable precision it offers. Traditional cutting methods often involve manual processes, which are susceptible to human error and inconsistencies. However, automated laser cutting systems are governed by computer-controlled software that ensures every cut is executed with pinpoint accuracy.
These systems can produce highly intricate and detailed designs with minimal tolerance variations, which is critical in industries that demand exacting standards. Whether you’re working with thin metals or thick plates, the automated process guarantees consistency, reducing the likelihood of costly mistakes and rework. This level of precision is especially valuable for high-volume production, where even small discrepancies can lead to significant material waste or product defects.
2. Enhanced Production Speed
Automation is synonymous with speed, and automated laser cutting is no exception. By streamlining the cutting process, these systems drastically reduce production time compared to manual methods. Automated laser cutters can work continuously without the need for breaks or interruptions, maximizing productivity and meeting tight deadlines with ease.
Moreover, because the machines can operate 24/7, downtime between shifts is eliminated. This is especially beneficial for industries with high production demands, as it allows for greater throughput while maintaining consistent quality. The integration of automation also reduces setup times, allowing for faster changeovers between projects and a more efficient use of resources.
3. Cost Savings Over Time
While the initial investment in automated laser cutting technology may seem substantial, the long-term financial benefits far outweigh the upfront costs. One of the key drivers of cost savings is the reduction in material waste. With greater precision and accuracy, automated laser cutters use materials more efficiently, minimizing scrap and optimizing the use of raw materials.
Labor costs are another area where automation shines. Automated systems require less manual intervention, allowing operators to focus on other high-value tasks, such as programming, maintenance, or quality control. This shift not only reduces labor costs but also improves overall operational efficiency. Additionally, because automated systems produce consistent and accurate results, the need for rework is minimized, saving both time and resources.
Over time, these cumulative savings lead to a faster return on investment (ROI), making automated laser cutting a cost-effective solution for businesses looking to scale production and improve profitability.
4. Greater Flexibility in Operations
Flexibility is key in modern manufacturing, and automated laser cutting systems provide exactly that. Traditional cutting processes often require manual adjustments and lengthy setup times when switching between different tasks or materials. With automation, these transitions are seamless, allowing operators to quickly adapt to different job specifications without halting production.
Automated laser cutting machines can handle a wide range of materials, from various metals to plastics, making them versatile tools for any fabrication shop. Additionally, the systems can be programmed to perform different types of cuts—whether straight lines, curves, or complex geometries—with ease. This ability to switch between jobs with minimal downtime improves overall productivity and helps businesses meet diverse customer needs efficiently.
5. Improved Workplace Safety
Safety is always a priority in industrial environments, and automated laser cutting systems offer significant advantages in this regard. Manual laser cutting or metalworking processes can expose workers to potential hazards, including intense heat, sharp edges, and harmful fumes. By automating these processes, employees are removed from direct exposure to these risks, creating a safer working environment.
Moreover, modern automated systems are equipped with advanced safety features, such as sensors, emergency stop mechanisms, and protective enclosures. These features not only ensure the safe operation of the machinery but also protect workers from accidents, reducing workplace injuries and the associated costs of downtime or compensation claims.
Conclusion: A Strategic Investment for the Future
Implementing automated laser cutting technology in your manufacturing operations is more than just a technological upgrade—it’s a strategic investment that enhances efficiency, boosts productivity, and delivers long-term cost savings. By embracing automation, you can improve the precision and speed of your production processes, while also creating a safer and more flexible work environment.
As the manufacturing industry continues to evolve, adopting automated laser cutting systems can give you a competitive edge, positioning your business for growth and success in the years to come.
Automated Laser Cutting Softwares
1. Adobe Illustrator
Adobe Illustrator (AI) is a well respected vector-based software which has been considered an industry leader for decades. If you are in graphic or industrial design, you will be well aware of AI.
This software is an excellent choice for laser-cutting design given its robust features, stable nature, and support from one of the world’s biggest software companies, Adobe. Plugins are available to take the designs and turn them into the g-code needed to run the laser.
For hobbyists and small businesses, it can be on the expensive side. To use AI you need to pay a subscription fee, rather than purchasing a single license. This cost is hard to justify unless you are creating new designs regularly and generating income from them.
In saying that, most professional designers use Illustrator as their choice of vector design software.
To learn more about using Illustrator to design for laser cutting, check out these resources.
2. Inkscape
Inkscape is a free, open-source version of Adobe Illustrator. There’s nothing you can do in Illustrator that you can’t do in Inkscape, it may just be a little more complicated. Millions and millions of dollars have gone into fine-tuning and adjusting the user interface and experience of Adobe Illustrator, whereas Inkscape has had to rely solely on developers and volunteer feedback.
The major advantage of Inkscape is that it’s free. But there are other reasons to use it. For example, there’s a large community involved in using the tool, where you can get help and tutorials. The community has also developed plugins to turn Inkscape designs into g-code files.
Professional designers are usually going to use Illustrator rather than Inkscape, but that isn’t universal. There are many professionals who operate solely on open-source platforms.
To learn more about using Inkscape to design for laser cutting, check out these resources.
3. LightBurn
Lightburn is an extremely popular software for laser cutting. It’s great for beginners with lasers at home and many businesses that use laser cutters. Many CO2 lasers ship with a license for LightBurn. The design side of LightBurn can be somewhat basic compared to the other options here, but if it’s enough to get you what you need, LightBurn is an excellent option. LightBurn can import files to turn into g-code if you have another software you prefer to design in.
4. LaserGRBL
Built specifically to control lasers, LaserGRBL is a free laser control software for Windows. It’s a much simpler interface, but has a limited feature set. What makes it different from the others listed here is that it is meant to control a laser directly. Rather than exporting a g-code file for your laser, LaserGRBL runs on a computer that is connected directly to the laser.
5. Fusion 360
Unlike LightBurn, the design side of Fusion 360 is excellent, allowing full 3D modeling, sheet metal tools and much more. Fusion 360 has built-in manufacturing tools that will let you take your designs and create the g-code files needed by your machine directly in one package. As a bonus, Fusion 360 can also handle milling, turning, plasma cutting, water jet cutting, laser cutting and more. If you do a lot of fabrication and want one software that can do it all, check out Fusion 360. If you want to send your files out to be laser cut, Fusion 360 can export the appropriate file formats too.
Things to Consider to Choose a Automated Laser Cutting Software
- Workflow – How you want to use software is important to consider. Do you want one software to design and create g-code or do you like to design in something you’re already familiar with and just need something to create g-code?
- Cost – There are some free options available for laser cutting software. They may trade stability or ease of use for that cost, however.
- Time – Sometimes what you get when you spend more for software is time savings. In a production environment where time is money, this could be a big factor to consider.
- Projects – The types of projects you want to create could factor into your decision. Will you only be laser cutting or would it be convenient to have a full CAM capable software?
What is the Best Laser Cutting Software for Beginners?
Try to leverage what you already know. If you have experience with something like Illustrator, look into the plugins that will allow you to turn your designs into g-code from there. For users with CAD experience, something like Fusion 360 might be a good choice.
For those of you just getting started with no experience to rely on, you might want to try out a few different options to see which you like. We’d advise you to not get stuck on just one option though. Sometimes it’s easy to stick with something because you’re familiar with it and miss out on a better option. Look for options with available tutorials and resources you can lean on if you need help.
Conclusion
Automated laser cutting is not just a technological upgrade; it’s a game-changer for production efficiency. By offering unmatched precision, faster production cycles, reduced material waste, and lower labor costs, it significantly streamlines operations. As manufacturing continues to move towards Industry 4.0, businesses that embrace automation will be better equipped to meet growing demands, improve their bottom line, and remain competitive in an evolving market.
Incorporating automated laser cutting into your production process is a key step toward achieving greater efficiency, scalability, and long-term success.