In the ever-evolving landscape of metalworking, the introduction of automatic panel bending machines marks a significant leap forward in technology and efficiency. These advanced machines are designed to automate the panel bending process, delivering unparalleled precision and consistency while reducing labor costs and production times. As industries seek to improve their manufacturing capabilities and stay competitive, understanding the benefits and functionalities of automatic panel bending machines is crucial. This article delves into the innovative features, applications, and future potential of these machines, providing a comprehensive overview for manufacturers and metalworking professionals.
Table of Contents
Understanding Automatic Panel Bending Machines
Automatic panel bending machines represent a transformative leap in modern metalworking, enhancing precision, efficiency, and flexibility in sheet metal bending processes. This section delves deeper into their definition, operational principles, key components, and cutting-edge technologies driving their functionality.
Definition
Automatic panel bending machines are advanced manufacturing tools designed to automate the intricate process of bending sheet metal. They replace traditional manual methods with sophisticated automation, ensuring consistent and precise bending results across various metal thicknesses and complexities. These machines are pivotal in industries requiring high-volume production of metal components with stringent quality standards.
Mechanism of Automatic Panel Bending Machine
When we think of traditional bending machines,we usually think of those where the force is impressed by the downward movement of a punch against the fixed part of the press, known as the die.
However, in panel benders,the bending work is performed by the blades, while the blank holder holds the sheet still during bending. The blades are thus able to perform different types of folds, upwards or downwards,beginning with the outermost bends of one side, before then automatically performing the bend sequence towards the innermost bend. All of these movements are controlled by electric servo drives that guarantee maximum positioning accuracy in the bending trajectory, thus ensuring an optimal result.
An automatic panel bending machine operates by clamping a sheet of metal between an upper and lower beam. The machine then uses a combination of upward and downward movements of these beams to bend the metal along predetermined lines. The bending process is controlled by sophisticated software that ensures precision and consistency.
The core components of a panel bender include the clamping beams, bending blades, and a control unit. The clamping beams hold the metal sheet in place, while the bending blades move to create the bends. The control unit allows the operator to program specific bending patterns and angles, ensuring each piece is manufactured to exact specifications.
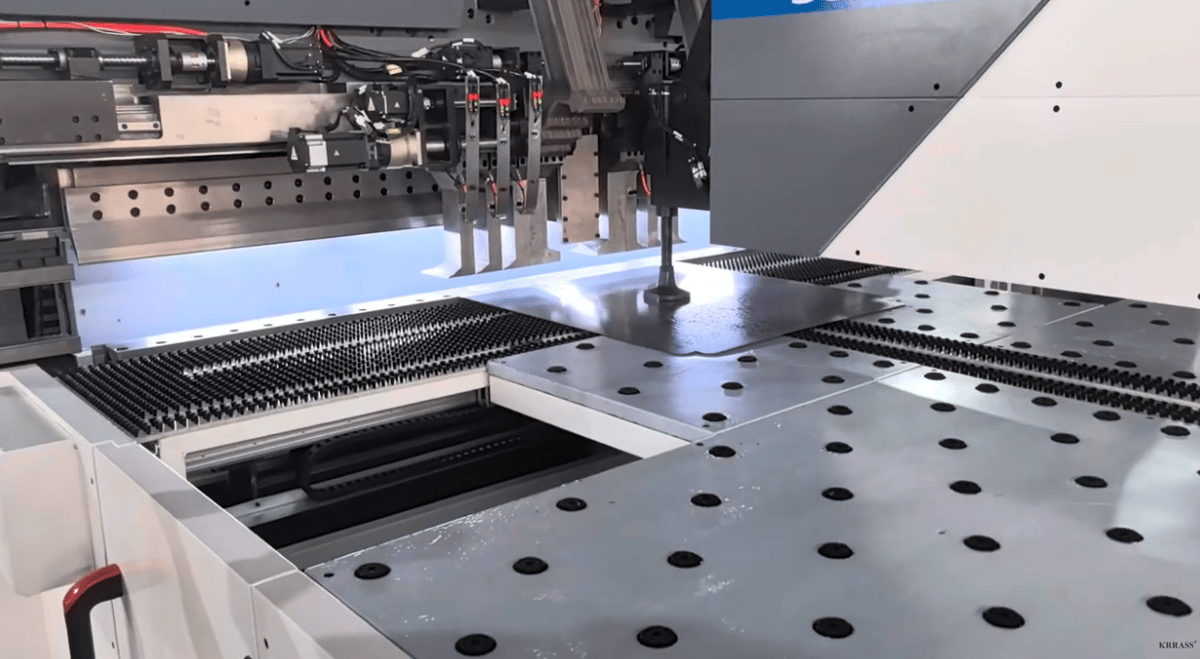
Key Components and Technologies
Bending Beam: Central to the machine, the bending beam applies controlled force to the metal sheet, ensuring uniformity and precision in bending operations.
Back Gauge System: Essential for accurate positioning of the metal sheet relative to bending tools. This system enhances repeatability and ensures consistent bend placements across production runs.
Tooling Systems: Include a variety of punches, dies, and tool changers tailored to different bending requirements. These components enable the machine to handle diverse geometries and materials with ease.
Control and Software Integration: Advanced control panels and software interfaces empower operators to manage and optimize bending processes. Features such as automatic angle correction, material thickness detection, and predictive maintenance algorithms enhance operational efficiency and minimize downtime.
Safety Features: Robust safety mechanisms, such as light curtains, interlocks, and emergency stop functionalities, safeguard operators and prevent accidents during machine operation.
Features and Applications
Automatic panel bending machines offer numerous advantages, including:
- Enhanced Precision: Achieve precise bend angles and dimensional accuracy consistently.
- Increased Efficiency: Reduce setup times and material waste, optimizing production throughput.
- Versatility: Handle complex geometries and various metal types, from aluminum to stainless steel.
- Cost-effectiveness: Lower labor costs and operational expenses through automation and streamlined workflows.
In industrial settings, these machines find applications across sectors such as automotive, aerospace, electronics, and construction, where high-quality metal components are essential for product performance and durability.
Automatic Panel Bender: Pros & Cons Explained
Advantages
Advanced Automation and Precision
Panel benders are specialized machines designed for efficient sheet metal bending, distinguished by their automatic tool changers that significantly reduce setup times. These machines boast a comprehensive tool set capable of handling intricate bends across various workpieces. Their tools interact minimally with the metal surface, resulting in fewer scratches and reduced tool wear due to minimal friction. Moreover, panel benders operate autonomously, minimizing the need for extensive human intervention and optimizing resource utilization.
Simplified Tooling and Versatility
Unlike traditional press brakes, panel benders achieve bending angles through the movement of upper and lower blades, simplifying tool complexity. Fully automated panel benders feature rapid tool changers that swiftly adapt to different bending tasks, ensuring efficient production across diverse applications. This capability makes them ideal for manufacturing large workpieces with complex flanges, and when equipped with automatic blank holders, they streamline operations, requiring only minimal operator oversight.
Ideal for Complex Bending Applications
The bending method employed by panel benders exerts pressure solely through upper and lower blades, minimizing metal plate deformation and spring-back. This technique facilitates the bending of entire box sides in one operation, making it particularly suitable for producing boxes, covers, and similar components with precise dimensional accuracy. Unlike modern press brakes, which may pose safety challenges when handling smaller parts, panel benders offer enhanced safety features and flexibility, accommodating even the production of smaller profiles through efficient clamping mechanisms or manual adjustments.
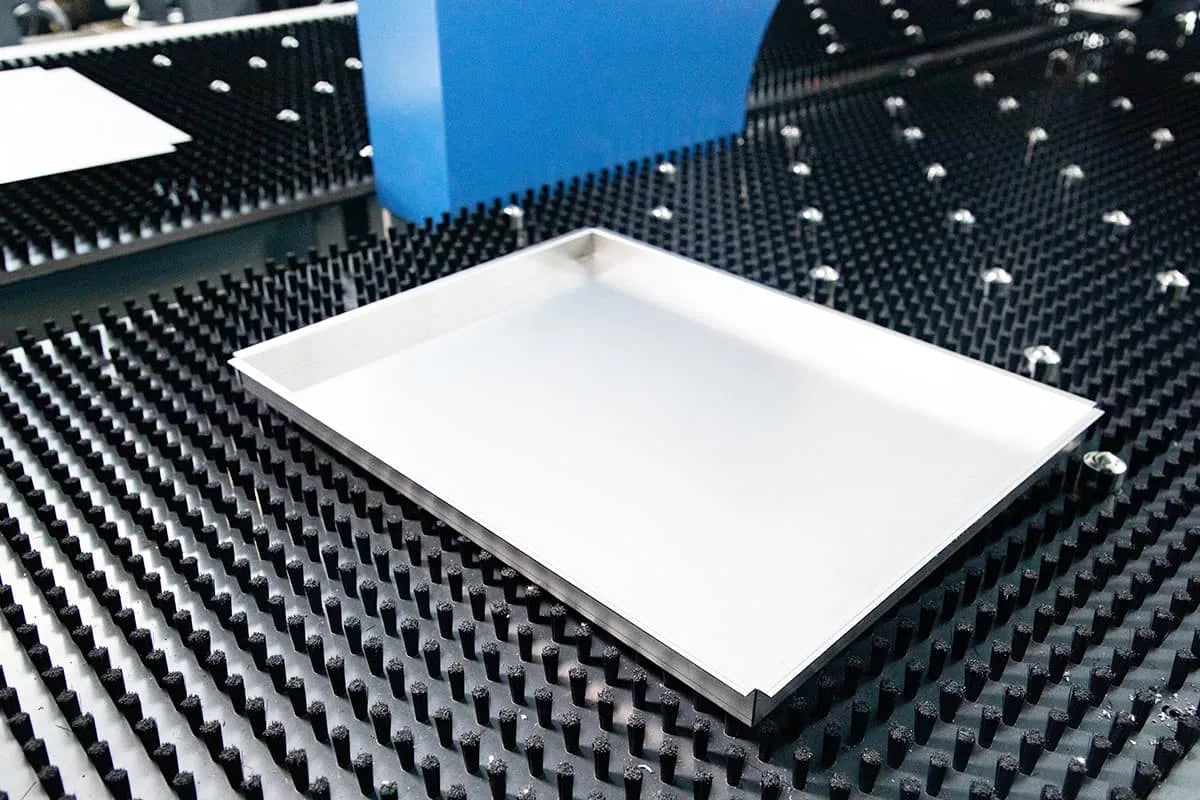
Limitations
Size and Material Constraints
Size Limitation: Panel benders excel in processing small to medium-sized metal sheets. However, their capability diminishes when handling extra-large or extra-thick sheets, requiring larger hydraulic bending machines or specialized equipment for such tasks.
Material Limitation: While suitable for softer metals like aluminum and stainless steel, panel benders may struggle with harder materials such as steel plates. This limitation can result in increased tool wear and potential compromises in bending precision and accuracy.
Shape and Batch Processing Challenges
Shape Limitation: Panel benders are adept at bending flat sheet materials but face challenges with complex three-dimensional curved structures. Such shapes often necessitate supplementary manufacturing processes like welding for completion.
Batch Limitation: Despite automation advantages, panel benders may not optimize processing efficiency for small-batch, multi-variety orders. Adjusting processes and changing molds can incur additional time and costs, diminishing their practicality in certain production scenarios.
Additional Considerations
Structural Constraints: The design of panel benders, with limited throat depth and opening height, makes them more suitable for producing smaller flanges. Internal bending operations pose challenges due to the positioning of clamping tools and bending blades.
Noise and Cost Factors: Operating at high speeds, panel benders can generate considerable noise levels, impacting both the factory environment and operator comfort. Addressing noise issues requires investments in sound insulation and noise reduction measures. Moreover, panel benders tend to be more costly compared to traditional bending machines, influencing their adoption in specific industrial applications.
Highlights of Automatic Panel Bending Machine
Handling large-scale panels
Krrass’s automatic panel bender models address diverse production needs in a wide range of applications, offering high precision production of panels including cabinet components, architectural building panels, photo-voltaic components, trailer side panels, lighting, shelving, industrial equipment, elevators, steel furniture, fire doors and clean rooms.
Full automation for high productivity
The fully servo-driven system provides precise control over the bending process, providing high repeatability and high productivity. It includes automatic sheet feeding, tool setting, servo bending, clamping, feeding, sheet rotation and positioning and gauging. Unloading and stacking are available as an option.
Cost-effective machine
The standard models keep the cost of the machine competitive and can be further customized for maximum performance. The servo-driven design requires low service and is almost maintenance-free. At fixed intervals all the moving parts are lubricated via a centralized lubrication system.
Multiple-stack loading
An automatic pick-and-place system allows to load from multiple stack locations onto the auto-feed. The ability to vary sizes and thicknesses provides greater flexibility.
User-friendly parametric programming interface
Programming can be done offline – by entering the bend parameters and loading the program - or directly on the machine, even during bending. Speeds are automatically calculated based on the sheet dimensions.
One set of tools for a variety of profiles
With a universal set of servo-operated up-and-down folding blades, Krrass panel benders can process a wide range of profiles and various types of bends. The majority of the profiles can be bent with just one set of universal bending tools.
Bends include:
- positive and negative bends
- open and closed hemming
- up and down hemming
- offset bends
- radius bends
- closed bends
Panel bender plate thickness range
Aluminum plate: up to 3.5mm
Carbon steel: up to 2mm
Stainless steel: up to 1.5mm
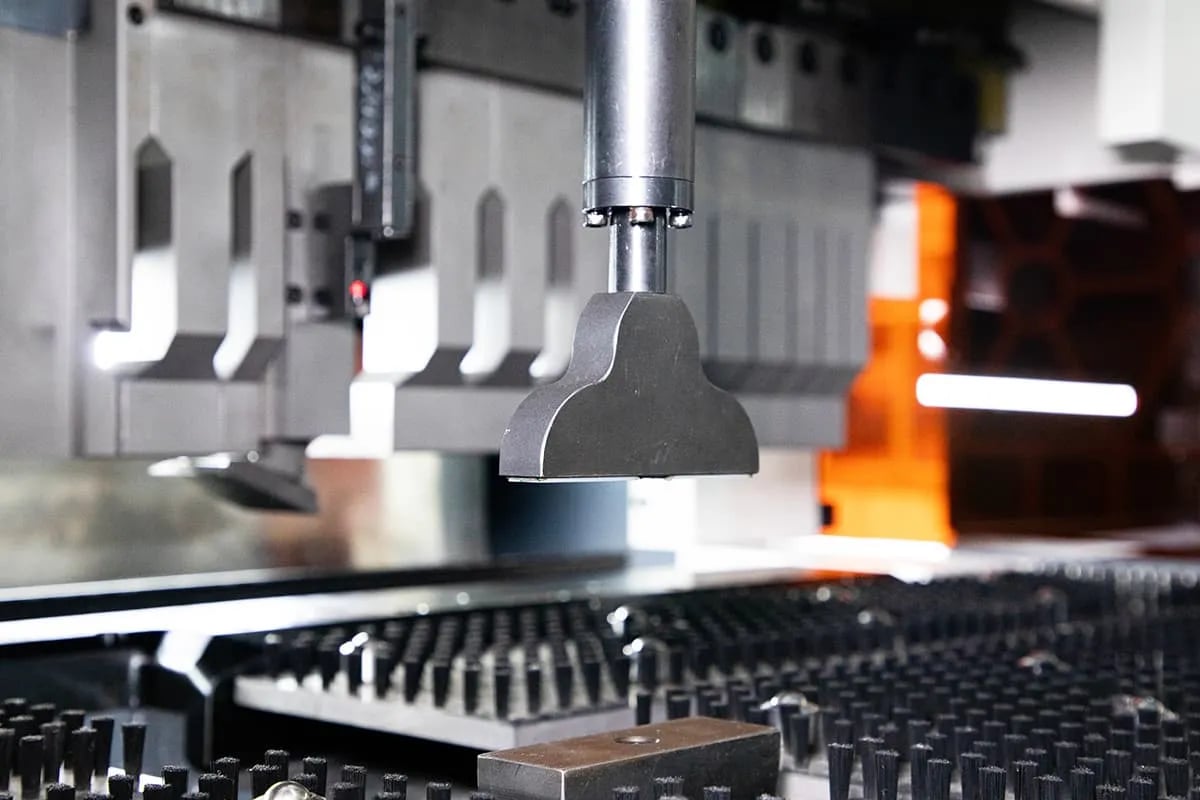
RFQ Guide
Can panel benders handle different types of metal sheets?
Yes, panel benders are designed to handle various types of metal sheets, including steel, aluminum, and stainless steel. The machine's settings and tooling can be adjusted to accommodate different materials and thicknesses.
Is it difficult to operate a panel bender?
While there is a learning curve, modern panel benders are designed to be user-friendly. Training and practice will help operators become proficient in using the machine and taking full advantage of its capabilities.
Can panel benders create complex forms and shapes?
Yes, panel benders are capable of creating complex forms and shapes by using customized tooling. This makes them suitable for applications that require intricate and precisely formed sheet metal components.
Has the panel bender resulted in cost savings in terms of labour costs and material wastage?
While there isn't a direct material saving with the panel bender, we can capitalize on short periods during which it can operate autonomously. This enables our operators to concurrently manage other machines, enhancing their efficiency. The benefits of this aspect will become even clearer as soon as all our staff become familiarized with the panel bender.
Are panel benders suitable for small-scale fabrication?
Yes, panel benders are suitable for both large-scale industrial production and smaller-scale fabrication. They offer flexibility and efficiency, making them applicable to a wide range of manufacturing scenarios.
Conclusion
Even though a panel bender offers many advantages, there are certain parts that fall outside its criteria and are better suited for fabrication using a press brake. When it comes to high-quality metal fabrication, both the panel bender and press brake have their place. The decision as to which to use will depend on the type and size of the project.
Here at KRRASS Machinery, we offer our best solutions and services to customers. If you are looking for a third party to outsource your projects or have issues that require expertise, we are always ready to deliver. All you need to do is contact us!
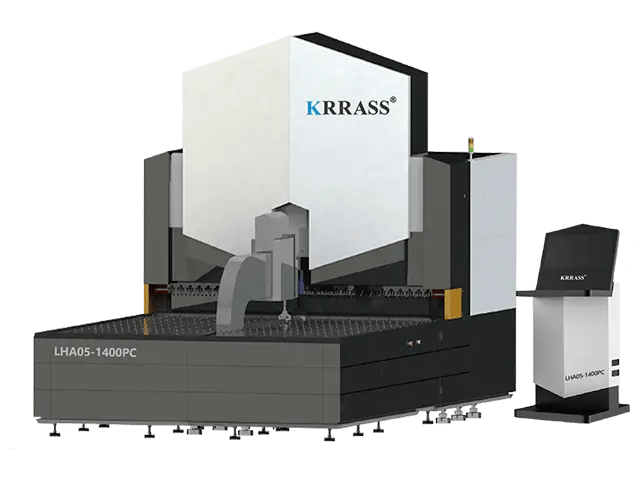