The CNC plasma cutting machine operates on the principle of utilizing plasma, a state of matter consisting of charged gas particles including electrons and ions, to cut through metal materials. This cutting technology harnesses the immense heat, energy, and velocity of plasma to achieve precise cuts. Plasma, with temperatures soaring into tens of thousands of degrees Celsius and boasting an exceptionally high energy density, swiftly elevates metal materials beyond their melting point. This rapid heating causes the metal to liquefy, forming an oxide layer, which is then blown away, facilitating the cutting process.
Plasma Generation
Plasma is a gaseous state in a high-energy state with properties such as ionization, conductance, and radiation. In a plasma, electrons of gas atoms collide with ions, releasing energy and ionizing the gas atoms into positively charged ions and negatively charged electrons. When the electrons return to the ground state of the atoms, they emit photons and heat, creating a plasma.
Application of CNC Plasma Cutting Machine
Plasma cutting machines are widely used in industrial fields such as metal cutting and welding. Its application range includes cutting and welding of stainless steel, aluminum alloy, copper, brass, steel and other materials. Plasma cutting machine can achieve precise cutting and welding, with fast cutting speed, high efficiency and good effect. Therefore, it is widely used in metal manufacturing, machinery manufacturing, automobile manufacturing, construction engineering and other industries
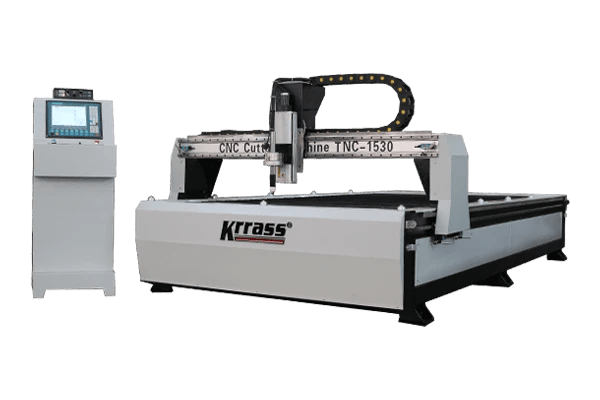
Main Steps of Plasma Cutter Principle
1) Gas introduction and arc ignition
The cnc plasma cutting machine introduces oxygen and inert gases (such as nitrogen, argon, etc.) into the cutting head through the gas introduction system, and then ionizes the gas through high-frequency arc ignition.
2) Plasma formation
After the arc is ignited, the molecules in oxygen and inert gas are decomposed into ions and free electrons to form plasma. The temperature of the plasma can reach tens of thousands of degrees, and the energy density is extremely high, which can instantly heat the metal material above the melting point.
3) Melting and oxidation
The high temperature and high energy in the plasma act on the metal material, causing it to melt and form an oxide layer. The oxide layer plays a role of heat insulation and protection, preventing the metal material from being further heated and oxidized.
4) Airflow cutting
The plasma blows away the molten metal material through a high-speed airflow to achieve cutting. The inert gas in the gas plays a protective role to prevent the molten metal material from being oxidized.
What's Advantages of CNC Plasma Cutting Machine
High Precision: CNC plasma cutting machines offer exceptional precision and accuracy in cutting various metal materials, ensuring high-quality finished products.
Versatility: These machines can efficiently cut through a wide range of materials and thicknesses, including steel, aluminum, and stainless steel, making them versatile for various applications.
Speed: CNC plasma cutting machines are known for their rapid cutting speeds, allowing for quick completion of projects and increased productivity.
Cost-Effectiveness: Compared to traditional cutting methods, CNC plasma cutting is often more cost-effective due to reduced material waste, lower energy consumption, and faster processing times.
Complex Shapes: They can effortlessly cut intricate shapes and designs with smooth edges, enabling the production of complex parts and components.
Automation and Efficiency: Integration with CNC (Computer Numerical Control) technology enables automated operation, minimizing manual intervention and maximizing efficiency.
How Thick Can A Plasma Cutter Cut
The cutting capacity of a plasma cutter is determined by its power and the type of torch it utilizes. Handheld torches typically have a cutting limit of around 1.5 inches (38 mm) for steel plates, whereas computer-controlled torches can handle up to 6 inches (150 mm) of steel. Industrial-grade plasma cutters, depending on their power rating and model, can slice through metal thicknesses ranging from 1 inch to several inches. Portable plasma cutters, on the other hand, are more suitable for thinner materials, usually up to 1/2 inch or less.
Conclusion
A plasma cutting machine is an equipment that harnesses the concentrated energy and extreme temperature of plasma to execute cutting, welding, and surface treatment tasks. Its operational principle revolves around utilizing the high energy density and instantaneous heat of plasma to liquefy metal materials, thereby facilitating cutting, welding, and related processes.
Widely employed across metal manufacturing, machinery production, automotive assembly, construction projects, and more, the plasma cutting machine offers precise cutting and welding capabilities, swift cutting speeds, heightened efficiency, and superior outcomes. However, to uphold cutting quality and prolong its service life, operators must adhere to safety protocols, regulate gas settings, select appropriate materials, and perform routine maintenance.