When we say CNC press brake axis, we always heard of Y, X, R axis, but we are often into confusion with these axes.
The key to understanding these axes is understanding how they work together to achieve specific shapes and angles of metal bending. Typically, a higher number of axes means greater flexibility and the ability to handle more complex workpieces.
For Example:
Suppose you have a 3-axis CNC press brake that can control the X, Y, and Z axes. You can control the movement of these three axes to precisely position the workpiece and tool relative to each other to achieve precise bends. However, if you have a 5-axis press brake, it may also include an R-axis and an additional rotational axis, allowing you to more freely adjust the angle of the workpiece and handle more complex bending tasks.
Taken together, understanding the these axes in a press brake involves understanding the function of each axis and how they work together to meet the requirements for bending a specific workpiece.
Here Are Some Key Concepts in A CNC Press Brake
● X-axis: The X-axis controls the horizontal movement of the back gauge, which is the device that positions the metal sheet for bending.
● Y-axis: The Y-axis controls the vertical movement of the ram, which is the device that applies the bending force to the metal sheet.
● Z-axis: The Z-axis controls the depth of penetration of the ram into the die, which determines the angle of the bend.
● R-axis: The R-axis controls the horizontal movement of the bending die, which can be used to create bends with varying radii.
● V-axis: The V-axis controls the rotation of the bending die, which can be used to create complex bends and shapes.
Overall, the various axes in a press brake machine work together to create precise and efficient bending operations, making it an essential tool in metalworking industries.
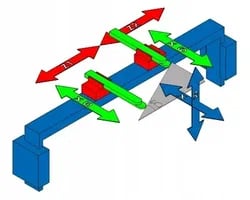
How to Select Proper Axes for Metal processing
Determine Bending Complexity:
Assess the complexity of your bending tasks. For simple bends on a single plane, a press brake with a single-axis backgauge might suffice. However, if your applications involve multiple bends, varying angles, or different planes, you'll need a press brake with multi-axis capabilities.
Material Specifications:
Consider the type and thickness of materials you'll be working with. Thicker and harder materials require more tonnage, so choose a press brake with sufficient capacity. Additionally, the length of the material influences the size of the press brake you need.
Precision and Accuracy:
Determine the level of precision your applications demand. For high-precision bending, especially when dealing with intricate designs or tight tolerances, a press brake with advanced CNC controls and high-resolution backgauge systems is essential.
Backgauge Requirements:
Evaluate the need for a backgauge system. A backgauge assists in positioning the material accurately, enabling consistent bends. Choose the appropriate number of backgauge axes based on the complexity of your bends. Common configurations include X, R, Z1, and Z2 axes.
Tooling Considerations:
Check the compatibility of the press brake with the tooling you plan to use. Different tool setups may require specific press brake models or modifications.
Automation and Software:
Consider the level of automation required. Modern press brakes often come with advanced software and CNC controls for easy programming and automation. Automation not only improves efficiency but also reduces the chance of errors.
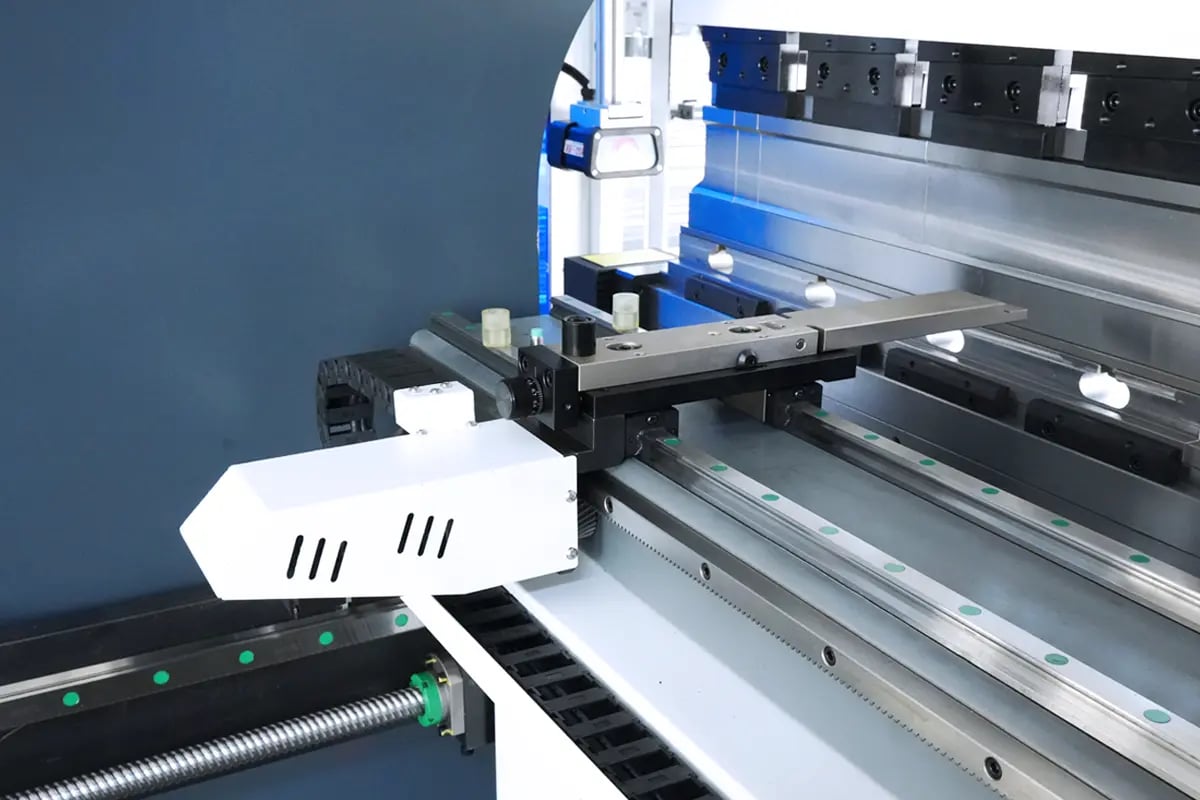
Overall, the number of axes of CNC press brake is directly related to the performance, adaptability and production efficiency of the bending machine. Proper selection and understanding of the function of the axis ensures that the press brake can meet a variety of metalworking needs.