The CNC press brake bending process is a fundamental technique in metal fabrication that utilizes computer-controlled machinery to bend sheet metal or metal plates into specific shapes and angles. Here's an introduction to the CNC press brake bending process:
7 Main CNC Press Brake Bending Processes
Material Preparation:
The process begins with the preparation of the sheet metal or metal plate, including cutting it to the required size and shape using techniques such as shearing or laser cutting.
Tooling Setup:
Next, the CNC machine is set up with the appropriate tooling, including a punch (upper tool) and a die (lower tool). These tools are selected based on factors such as material type, thickness, and desired bend angle. The CNC control system allows for precise tooling setup and adjustment.
Programming:
Before bending, the operator or programmer creates a bending program using the CNC control interface. This program specifies parameters such as bend angles, bend lengths, tooling selection, and backgauge positions.
Clamping and Alignment:
The metal workpiece is securely clamped onto the CNC press brake's bed or backgauge to ensure accurate bending. Proper alignment of the workpiece is essential to achieve precise bends.
Bending:
With the workpiece securely clamped, the machine's hydraulic ram, controlled by the CNC system, descends to apply force to the metal. The force exerted by the ram causes the metal to deform and bend around the selected die. The CNC control system precisely regulates the ram's movement to achieve the programmed bend angles and lengths.
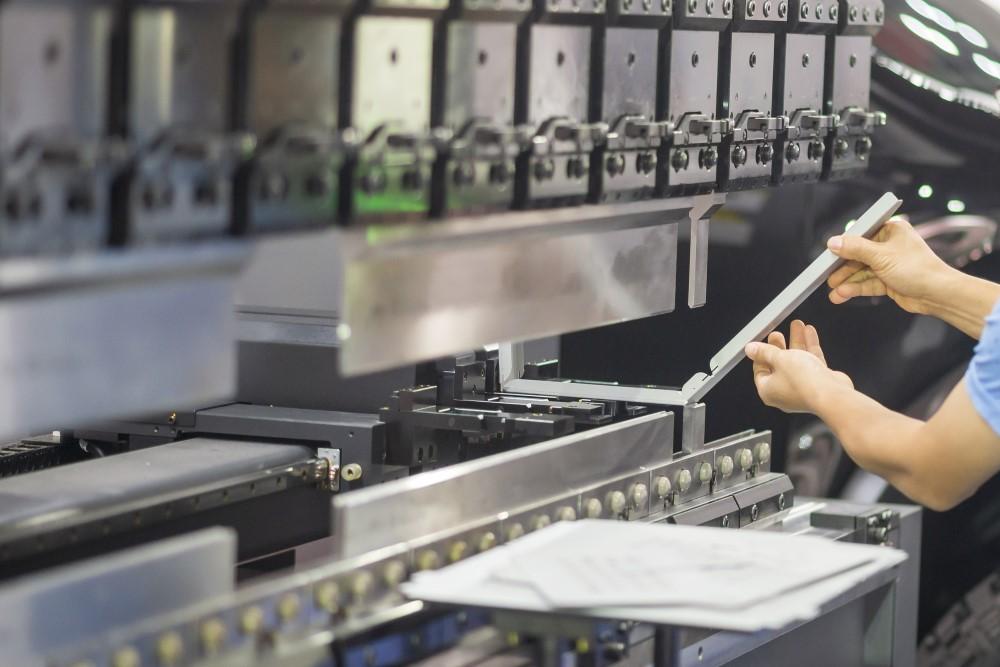
Measurement and Quality Control:
Throughout the bending process, the CNC press brake may incorporate sensors or measurement devices to monitor the bending angles, dimensions, and other parameters. This allows for real-time quality control and adjustment to ensure accurate and consistent results.
Springback Compensation:
After bending, some materials may exhibit springback, where the metal partially returns to its original shape. CNC press brakes can compensate for springback by adjusting bending parameters or applying additional bending passes.
Unloading:
Once the bending process is complete, the finished workpiece is removed from the CNC press brake. Depending on the complexity of the part and the production setup, additional operations such as secondary bending or assembly may be performed.
Overall, the CNC press brake bending process offers high precision, repeatability, and efficiency, making it suitable for a wide range of metal fabrication applications across various industries.