Introduction
In metal fabrication, selecting the right bending equipment is crucial for achieving precise results and maximizing efficiency. When considering press brakes, two primary options emerge: CNC press brakes and traditional press brakes. This comparison aims to explore the differences between these machines, helping you make an informed decision for your fabrication projects.
Comparison Between CNC Press Brake and Traditional Press Brake
Precision and Accuracy
Precision and accuracy are critical factors in metal fabrication, especially when it comes to bending operations. Let's delve deeper into how CNC press brakes and traditional press brakes differ in terms of precision and accuracy:
CNC Press Brake: CNC press brakes stand out for their ability to deliver unparalleled precision and accuracy in bending operations. This is primarily attributed to their advanced programmable controls, which allow for precise manipulation of bending parameters. With CNC press brakes, operators can program the desired bend angles, dimensions, and sequencing with high precision.
Moreover, CNC press brakes are equipped with automated adjustments and real-time feedback systems. These features ensure consistent bend angles and dimensions, even for complex parts with intricate geometries. The automated nature of CNC press brakes minimizes the margin for error, resulting in highly accurate bends with minimal deviation from the intended specifications.
Traditional Press Brake: On the other hand, traditional press brakes offer manual control over bending parameters, which may impact their precision compared to CNC counterparts. While skilled operators can achieve accurate bends with traditional press brakes, the process is inherently reliant on the operator's experience and expertise.
Operators must carefully set up the machine, adjust bending parameters, and monitor the bending process to ensure accuracy. However, variations in setup, operator technique, and material handling can introduce inconsistencies in bend angles and dimensions. Without automated feedback systems, traditional press brakes may struggle to maintain consistent precision, particularly for complex or repetitive bending tasks.
Flexibility and Versatility
Flexibility and versatility are crucial considerations when choosing between CNC press brakes and traditional press brakes. Let's explore these aspects further:
CNC Press Brake:
Material Compatibility: CNC press brakes can handle a wide variety of materials, including steel, aluminum, stainless steel, and alloys. They are capable of bending different thicknesses of materials, from thin sheets to thick plates, making them highly versatile across various industries.
Complex Bending Capabilities: One of the standout features of CNC press brakes is their ability to perform intricate and complex bends. With advanced programmable controls and tooling options, CNC machines can produce a diverse range of bends, flanges, and multiple bends in a single setup. This versatility is invaluable for fabricating components with challenging geometries.
Customization and Adaptability: CNC press brakes offer flexibility for diverse fabrication requirements. They can be programmed to produce custom parts with precision and repeatability, making them ideal for batch production, prototyping, and custom projects. Additionally, CNC machines can adapt to changing production demands and accommodate design revisions with ease.
Traditional Press Brake:
Suitable for Basic Bending Tasks: Traditional press brakes are well-suited for straightforward bending tasks and standard part geometries. While they may lack the advanced features of CNC machines, traditional presses excel in producing simple bends, angles, and flanges. They are particularly useful for repetitive bending operations with consistent requirements.
Ease of Operation: Traditional press brakes are often more straightforward to operate compared to CNC counterparts. With fewer complex controls and programming requirements, operators can quickly set up the machine and start bending parts with minimal training. This simplicity makes traditional presses accessible to smaller workshops and businesses with limited resources.
Cost-Effectiveness: In terms of upfront costs, traditional press brakes are generally more affordable than CNC machines. This cost-effectiveness makes them an attractive option for businesses with budget constraints or lower production volumes. Additionally, traditional presses may have lower maintenance and repair costs, contributing to long-term savings.
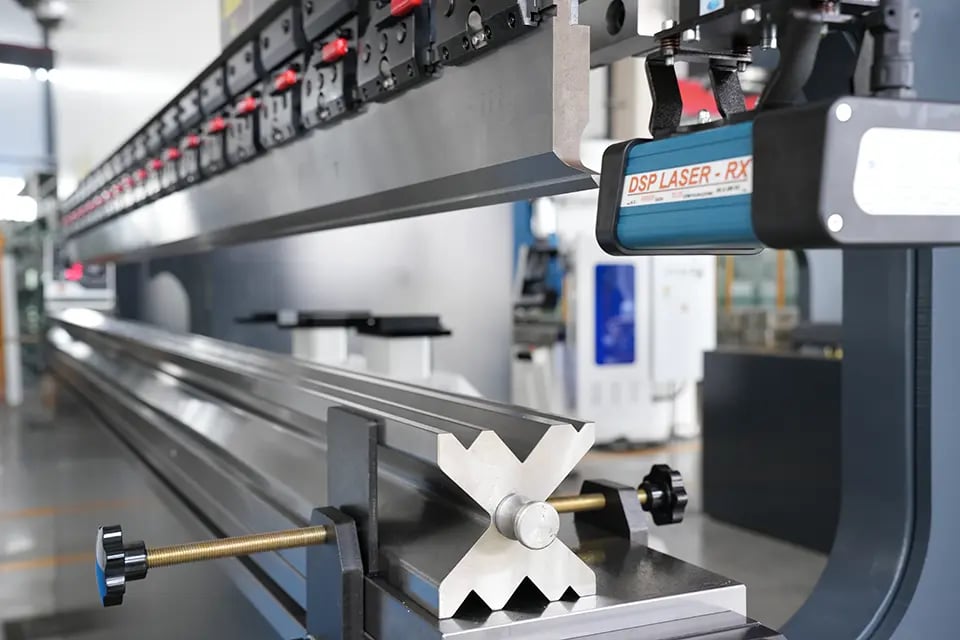
Production Efficiency
CNC Press Brake:
Automated Programming and Tool Setup: CNC press brakes leverage advanced technology for automated programming and tool setup. Operators can program bending sequences, angles, and dimensions directly into the machine's control system, eliminating the need for manual adjustments. This streamlined process reduces setup time and ensures consistent production parameters across batches.
High-Volume Production Capabilities: With their automated features and precise control systems, CNC press brakes excel in high-volume production environments. They can handle large quantities of parts with minimal downtime between setups, resulting in faster cycle times and increased throughput. This high-speed production capability is essential for meeting tight deadlines and maximizing overall efficiency.
Traditional Press Brake:
Manual Adjustments and Setup: Traditional press brakes rely on manual adjustments and setup procedures, which may require more time and labor compared to CNC counterparts. Operators need to manually adjust tooling, backgauges, and bending parameters for each new job, leading to longer setup times and potential setup errors.
Well-Suited for Low to Medium-Volume Production: While traditional press brakes may have slower cycle times compared to CNC machines, they are well-suited for low to medium-volume production and job shop applications. These machines offer cost-effective solutions for smaller-scale operations that do not require the high-speed capabilities of CNC press brakes.
Cost Considerations
CNC Press Brake:
Higher Initial Investment: The initial investment for a CNC press brake is typically higher compared to a traditional press brake. This is primarily due to the advanced technology, automation features, and precision control systems integrated into CNC machines. The upfront cost includes expenses related to the machine itself, as well as software, training, and maintenance.
Long-term Benefits: Despite the higher initial investment, CNC press brakes offer long-term benefits that can justify the upfront cost. These include increased productivity, reduced material waste, improved quality and consistency, and faster setup times. By automating repetitive tasks and minimizing operator error, CNC press brakes help fabricators maximize efficiency and profitability over time.
Traditional Press Brake:
Lower Upfront Cost: Traditional press brakes are generally more affordable upfront compared to CNC machines. These machines may have simpler mechanical designs and fewer automation features, resulting in a lower purchase price. For small businesses or startups with limited budgets, traditional press brakes offer a cost-effective entry point into metal fabrication.
Higher Labor Costs: While traditional press brakes may have a lower initial investment, they often require more manual labor to operate and set up. Operators need to manually adjust tooling, backgauges, and bending parameters for each job, which can increase labor costs over time. Additionally, the potential for human error in manual processes may lead to higher scrap rates and rework expenses.
Conclusion
Both CNC press brakes and traditional press brakes have their advantages and limitations, making them suitable for different fabrication scenarios. By carefully assessing your production requirements, budget constraints, and long-term goals, you can choose the press brake solution that best aligns with your needs and maximizes your fabrication efficiency.