What is CNC Press Brake
A CNC press brake is a machine tool utilized in metalworking to bend and shape sheet metal and plates. It employs a combination of hydraulic or mechanical force and computerized numerical control (CNC) technology to precisely manipulate metal sheets into desired configurations. CNC press brakes are commonly used in various industries, including manufacturing, construction, automotive, and aerospace, for producing components ranging from simple brackets to intricate structural parts.
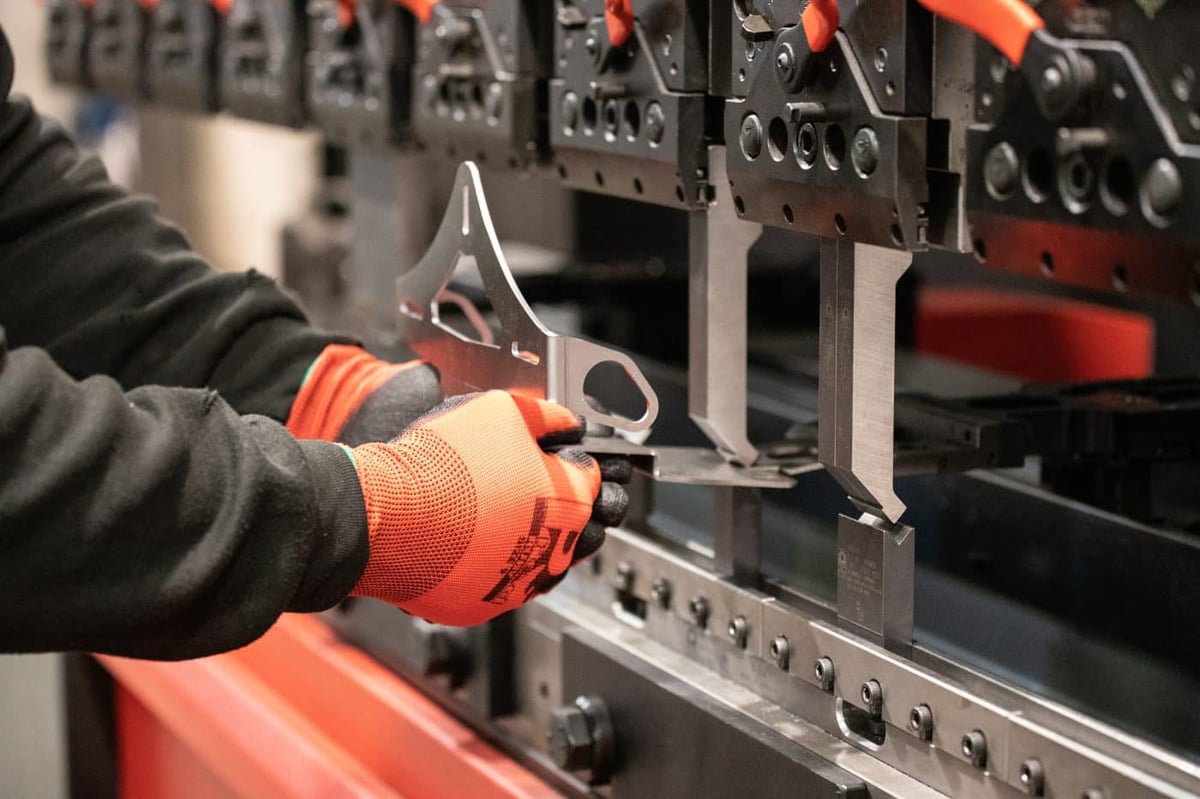
Working Principle
CNC press brake machines have transformed the metalworking industry with their precision bending capabilities and advanced technology. Understanding the fundamental working principles behind these machines is essential for optimizing their performance and efficiency. In this article, we will explore the intricate workings of the machines, focusing on key aspects such as the hydraulic system, mechanical structure, and control system.
Hydraulic System
The hydraulic system of a CNC machines is at the heart of its bending power. It consists of a hydraulic pump, cylinders, valves, and hoses working in harmony to generate and control hydraulic pressure. When a bending operation is initiated, the hydraulic pump pressurizes hydraulic fluid, which is then directed to the hydraulic cylinders. These cylinders extend or retract to exert force on the bending tool, allowing precise bending of metal sheets. By adjusting the pressure and flow rate of the hydraulic system, operators can achieve consistent and accurate bends.
Mechanical Structure
The mechanical structure of a CNC press brake provides the framework for its bending operations. It typically includes a sturdy frame, a movable ram (or upper beam), and a stationary bed (or lower beam). The bending tooling, such as punches and dies, is mounted on the ram and bed to shape the metal sheet during bending. Additionally, CNC press brakes may feature backgauges and crowning systems to enhance bending accuracy and flexibility. The mechanical components work together seamlessly to ensure precise and repeatable bending results.
Control System
The control system is the brain of the CNC press brake, governing its operation and functionality. Modern CNC press brakes are equipped with advanced control systems based on computer numerical control (CNC) technology. Operators use intuitive interfaces or touchscreen panels to input bending parameters such as bend angle, bend length, and material thickness. The control system interprets these inputs and commands the hydraulic system to execute the bending operation with precision. Advanced features such as automatic tool compensation and angle correction further optimize the bending process, ensuring consistent part quality and production efficiency.
Conclusion
In conclusion, CNC press brakes rely on a combination of hydraulic power, mechanical precision, and digital control to achieve accurate and efficient metal bending. By deciphering the working principles behind these machines, operators can harness their capabilities to produce high-quality parts with consistency and reliability. Whether in automotive manufacturing, aerospace, or general fabrication, CNC press brakes are indispensable tools for modern metalworking operations.