In the metal fabrication industry, the distinction between CNC and NC press brakes is a crucial point of consideration.
This guide aims to elucidate these differences, shedding light on their operation, applications, and the myriad factors influencing their selection. Engaging with this topic, you’ll grasp the nuances of these technologies, empowering you to make the optimal choice for your metal bending needs.
Table of Contents
What is a Press Brake?
A press brake is a foundational piece of machinery in the metalworking landscape, designed to bend sheet metal. This equipment plays a critical role in the manufacturing sector, utilizing a combination of a punch and die to form bends in metal sheets with precision.
The process is a staple in the fabrication of metal products, where accuracy and efficiency are paramount.
What is the difference between NC and CNC press brakes?
The differences between NC and CNC press brakes primarily revolve around their control systems and operational capabilities. CNC press brakes offer advanced functionalities such as real-time feedback, detailed control over bending angles, and the ability to store and recall complex programs. This makes them ideal for intricate, varied, or precision-critical projects.
On the other hand, NC press brakes provide a more cost-effective solution for straightforward bending tasks, where the complexities and flexibilities of CNC systems are not required.
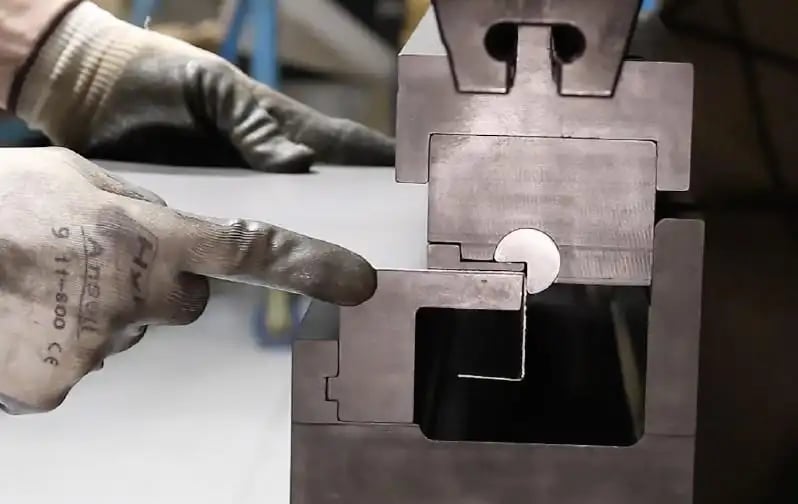
What is a CNC Press Brake?
A CNC Press Brake is a pinnacle of modern metal fabrication technology, integrating advanced computer numerical control to enhance precision, speed, and flexibility in bending sheet metal. This machine utilizes precise programming and real-time feedback systems to automate the bending process, significantly increasing production efficiency and accuracy.
What are the main Components of CNC Press Brake?
The effectiveness of a CNC press brake is attributed to its sophisticated components, each playing a crucial role:
CNC Controller: The central unit that interprets and executes the programmed instructions, controlling the entire operation.
Backgauge: A precision positioning system that accurately places the metal sheet for bending.
Ram: The component that moves the punch down to create the bend.
Punch and Die: Customizable tools that physically interact with the metal, creating the desired bend shape.
Safety Systems: Integrated features like light curtains and laser systems to ensure operator safety during operation.
How Do CNC Press Brakes Operate?
The operation of CNC press brakes is a testament to the integration of advanced technology in manufacturing:
Programming: Detailed instructions, including bend angles and sequences, are programmed into the CNC controller.
Setup: Based on the input, the machine automatically adjusts the backgauge and selects the appropriate tools.
Bending Process: The ram applies controlled force, pressing the metal sheet into the die, guided by real-time feedback for precision.
Quality Assurance: Continuous monitoring ensures each bend meets the programmed specifications, adjusting in real-time as necessary.
What is а NC Press Brake?
А NC Press Brake represents an essential bridge between manual bending operations and the fully automated CNC press brake technology. They utilize numerical control systems to perform bending operations, offering a more cost-effective solution for less complex tasks. While they lack the full automation and precision of CNC models, NC press brakes still provide a significant upgrade from manual processes, enhancing production efficiency and consistency in operations that do not require intricate programming or real-time feedback.
What are Core Components of NC Press Brake?
The functionality of NC press brakes is underpinned by several key components:
NC Controller: Simpler than a CNC controller, it allows for basic programming of bending operations.
Backgauge: Mechanically positions the workpiece, though with less precision than CNC models.
Ram: Executes the bending by moving the punch toward the die.
Punch and Die: The essential tools that work together to bend the metal sheet.
How Do NC Press Brakes Operate?
The operation process of NC press brakes can be summarized as follows:
Programming: The operator inputs the bending parameters into the NC controller. This includes data like bending angles, sequence, and backgauge positions.
Setup: Based on the inputted data, the operator manually sets up the machine, adjusting the backgauge and installing the correct punch and die combination.
Bending Operation: The operator initiates the bending process. The ram moves the punch to press the workpiece into the die, creating the bend. The backgauge positions the workpiece for each bend.
Manual Adjustments: Unlike CNC press brakes, NC press brakes may require the operator to make manual adjustments between bends to ensure accuracy.
NC press brakes, with their simpler operation and lower cost, remain a viable option for many fabrication tasks. They are especially suited for projects where the high degree of automation and flexibility of CNC press brakes is not necessary. By combining numerical control with mechanical precision, NC press brakes offer a balanced solution for achieving consistent, accurate bends in a variety of metalworking applications.
What Are the Strengths and Weaknesses of CNC and NC Press Brakes?
Each type of press brake brings its own set of strengths and weaknesses to the table, impacting their suitability for different manufacturing environments.
Advantages of CNC Press Brakes
High Precision and Consistency: Thanks to advanced control systems, CNC press brakes offer superior bending accuracy and repeatability.
Increased Productivity: Automation and faster setup times allow for higher throughput, making CNC press brakes ideal for high-volume production.
Versatility: With programmable settings and the ability to easily switch between jobs, CNC press brakes can handle a wide variety of bending tasks, including complex shapes and materials.
Reduced Waste: The precision and real-time feedback of CNC press brakes minimize material waste, contributing to cost savings and sustainability.
Disadvantages of CNC Press Brakes
Higher Initial Cost: The advanced technology of CNC press brakes comes with a higher purchase price, making them a significant investment.
Complexity and Maintenance: The complexity of CNC machines can lead to higher maintenance costs and the need for specialized technicians.
Training Requirements: Operators must be trained to use the sophisticated software and controls, which can add to operational costs.
Advantages of NC Press Brakes
Lower Initial Investment: NC press brakes are generally less expensive to purchase than CNC models, making them accessible to smaller operations or those with limited budgets.
Simplicity: With fewer complex features, NC press brakes are easier to maintain and operate, requiring less specialized training.
Reliability: The mechanical simplicity of NC press brakes can lead to robust performance and durability with proper maintenance.
Disadvantages of NC Press Brakes
Limited Flexibility: Without the advanced programmable features of CNC models, NC press brakes may not be suitable for jobs requiring high precision or complex bending sequences.
Lower Productivity: Manual adjustments and setups can make NC press brakes less efficient for large-scale or complex production runs.
Dependence on Operator Skill: Achieving consistent results with NC press brakes relies heavily on the operator’s experience and skill.
What Are the Differences in Accuracy and Speed Between CNC and NC Press Brakes?
Both have their unique advantages, but they differ significantly in terms of accuracy, speed, and overall efficiency. Understanding these differences is crucial for manufacturers to choose the right equipment for their specific needs.
Accuracy
CNC Press Brakes: These machines offer superior accuracy thanks to their advanced control systems. CNC press brakes utilize precise, programmable parameters and real-time feedback mechanisms to ensure each bend is executed with exact precision. This is particularly important for complex shapes or where tight tolerances are required.
NC Press Brakes: While NC press brakes can achieve a high degree of accuracy, they lack the real-time adjustment capabilities of CNC models. The operator sets the parameters before the job, and adjustments during bending are manual and less precise, potentially leading to slight variations in the finished product.
Speed
CNC Press Brakes: Speed is one of the major advantages of CNC press brakes. The automated nature of these machines, combined with their ability to quickly adjust to different bending parameters, allows for faster production times. This is enhanced by features such as automatic tool changing and rapid ram movement.
NC Press Brakes: NC press brakes generally operate at slower speeds compared to their CNC counterparts. The manual setup and adjustments required for each job can lead to increased cycle times, particularly for complex bending operations or when switching between different types of bends.
What Is the Impact of Material Type on the Performance of CNC and NC Press Brakes?
The type of material being bent significantly affects the performance of both CNC and NC press brakes. These machines, though versatile, have their specific strengths and limitations influenced by material properties such as thickness, strength, and ductility. Understanding how different materials impact the operation and efficiency of press brakes is essential for optimizing production processes and ensuring quality outcomes.
Impact on CNC Press Brakes
Thickness: Thicker materials require more force to bend, which can impact the speed at which CNC press brakes operate. Modern CNC press brakes are designed to handle a wide range of material thicknesses efficiently, thanks to their advanced hydraulic systems and programmable features that adjust the bending force automatically.
Material Strength: High-strength materials, such as high-strength steels, challenge the bending process by requiring precise control over bending angles and forces. CNC press brakes excel in these scenarios, as their advanced control systems can finely tune the operation to accommodate the material’s resistance.
Ductility: Materials with low ductility may crack or break if not handled correctly. CNC press brakes, with their ability to apply precise and controlled forces, can prevent damage to less ductile materials by adjusting the bending process to suit the material’s characteristics.
Impact on NC Press Brakes
Thickness: Similar to CNC press brakes, the thickness of the material affects the performance of NC press brakes. However, adjustments for material thickness in NC press brakes may require manual input, which can slow down the bending process.
Material Strength: NC press brakes can bend strong materials, but the lack of real-time feedback and automatic adjustments means operators must rely on experience and trial and error to achieve the desired results. This can lead to increased setup time and potential wastage.
Ductility: Bending materials with low ductility is more challenging with NC press brakes due to the less precise control over bending forces. The operator’s skill becomes a crucial factor in preventing material damage.
What Are the Various Applications of CNC and NC Press Brakes?
CNC and NC press brakes play vital roles in metal fabrication, catering to a diverse range of applications across various industries.
Applications of CNC Press Brakes
Aerospace Components: Precision and repeatability are crucial in aerospace applications, making CNC press brakes ideal for producing parts that meet strict tolerance requirements.
Automotive Industry: From chassis components to intricate brackets, CNC press brakes support the automotive industry’s need for high-volume, precise bending operations.
Architectural Metalwork: CNC press brakes are used to create complex shapes and designs for architectural elements, offering the flexibility and precision required for custom work.
Heavy Machinery: Large, thick components used in construction and agricultural machinery benefit from the high force and advanced control systems of CNC press brakes.
Electronics: The production of small, precise components for electronic devices often requires the capabilities of CNC press brakes.
Applications of NC Press Brakes
General Fabrication: NC press brakes are well-suited for straightforward bending tasks common in general metal fabrication shops.
Signage: Producing metal signs involves repetitive bending of similar materials, a task for which NC press brakes are efficiently designed.
HVAC Manufacturing: Ductwork and other components for heating, ventilation, and air conditioning systems can be effectively produced using NC press brakes.
Structural Steel: For projects that do not require the extreme precision of CNC control, NC press brakes can provide an effective solution for bending structural steel elements.
How Do Environmental and Energy Efficiency Factors Compare CNC and NC Press Brakes?
Both types of press brakes have evolved to offer improved energy efficiency and reduced environmental impact, but there are distinct differences between the two regarding how they achieve these goals.
CNC Press Brakes
Energy Efficiency: CNC press brakes are generally more energy-efficient compared to their NC counterparts. This efficiency is largely due to the use of servo-electric or hybrid systems that consume power only during the bending process, reducing idle energy consumption.
Environmental Impact: The precision of CNC press brakes contributes to less waste material since their high accuracy reduces the margin of error in bending operations. Additionally, the integration of modern hydraulic fluids with lower environmental impact and better recycling processes for metal scraps also helps in minimizing the ecological footprint.
Sustainability Aspects: CNC press brakes often come equipped with advanced energy-saving features such as automatic sleep modes and regenerative hydraulic circuits that can return energy to the power grid, further enhancing their sustainability profile.
NC Press Brakes
Energy Efficiency: Traditional NC press brakes, especially those with conventional hydraulic systems, tend to be less energy-efficient due to continuous power consumption, even when the machine is not actively bending. However, improvements in hydraulic system design have begun to reduce these inefficiencies.
Environmental Impact: NC press brakes can have a higher environmental impact due to less precise operations that may lead to increased material wastage. The reliance on older hydraulic systems may also contribute to a larger ecological footprint if not properly managed or updated.
Sustainability Aspects: The simpler technology of NC press brakes means they have fewer built-in features specifically designed to reduce energy consumption. However, the potential for retrofitting with more efficient components or systems can improve their sustainability over time.
How Do CNC and NC Press Brakes Compare in Terms of Customization and Flexibility?
In today’s dynamic manufacturing environment, the ability to adapt to custom jobs and various projects is essential. Both CNC and NC press brakes offer different levels of customization and flexibility, catering to the diverse needs of the metal fabrication industry.
CNC Press Brakes
High Customization: CNC press brakes excel in customization due to their programmable nature. The ability to store and recall numerous programs allows for quick setup changes between jobs, making it easier to handle custom or complex bending tasks.
Superior Flexibility: The advanced control systems of CNC press brakes enable them to adapt to a wide range of materials, thicknesses, and bending angles with precision. This flexibility is crucial for workshops that work on varied projects requiring high levels of detail and customization.
Automated Tool Changing: Many CNC press brakes feature automated tool changing systems, further enhancing their adaptability by reducing setup times for different jobs.
NC Press Brakes
Moderate Customization: While NC press brakes can be set up for custom jobs, the process is generally more manual and time-consuming than with CNC models. The lack of programmable controls means adjustments between different projects can slow down production.
Basic Flexibility: NC press brakes provide a level of flexibility suitable for straightforward bending tasks. However, their manual setup process and limited control options can restrict their use in projects requiring high precision or varied bending operations.
Tool Changing: Changes in tooling on NC press brakes require manual intervention, which can extend setup times and reduce overall flexibility in switching between different types of jobs.
What are the Maintenance Needs of CNC and NC Press Brakes?
Maintenance is a critical aspect of ensuring the longevity, efficiency, and safety of both CNC and NC press brakes. While both types of machinery require regular upkeep, the complexity and technology of CNC press brakes often necessitate a more nuanced approach to maintenance compared to their NC counterparts.
CNC Press Brakes
Regular Software Updates: To maintain optimal performance and take advantage of the latest features, CNC press brakes require regular software updates. These updates can enhance machine functionality and introduce new capabilities or efficiencies.
Hydraulic System Maintenance: CNC press brakes often rely on sophisticated hydraulic systems for precise control. Regular checks and maintenance of the hydraulic fluid, seals, and valves are essential to prevent leaks and maintain accuracy.
Tooling Inspection and Care: The advanced tooling used in CNC press brakes needs regular inspection for wear and damage. Proper storage and handling can extend tool life and ensure consistent bending quality.
Preventive Maintenance Programs: Many manufacturers recommend or offer preventive maintenance programs that include routine inspections, calibration, and parts replacement to prevent downtime and extend the machine’s lifespan.
NC Press Brakes
Mechanical Adjustments: NC press brakes may require more frequent mechanical adjustments due to their less sophisticated control systems. Regular checks and adjustments ensure that the machine continues to operate within its desired parameters.
Lubrication: Proper lubrication of moving parts is crucial to prevent wear and tear. NC press brakes, with their mechanical nature, often require regular manual lubrication of components like the ram, backgauge, and dies.
Hydraulic System Checks: Similar to CNC models, NC press brakes also rely on hydraulic systems for power. Regular inspection and maintenance of these systems are vital to prevent leaks and maintain operational efficiency.
Simpler Tooling Maintenance: While the tooling in NC press brakes also requires regular inspection, the process is generally less complex due to the more straightforward nature of the tooling compared to that used in CNC press brakes.
How to Choose Between CNC and NC Press Brakes?
Deciding whether to invest in a CNC or an NC press brake hinges on various factors that align with your specific production needs, budget, and long-term goals. Here are key decision-making criteria to consider:
Production Volume and Complexity:
If your operations involve high-volume production with complex bending requirements, CNC press brakes are the superior choice due to their precision, speed, and flexibility. For simpler, lower-volume tasks, an NC press brake might suffice.
Precision Requirements:
CNC press brakes offer higher accuracy and repeatability, making them ideal for projects requiring tight tolerances. If your work does not demand such precision, an NC press brake could be a more cost-effective option.
Material Handling:
Consider the types of materials you will be working with. CNC press brakes can handle a wider range of materials and thicknesses with greater efficiency and less waste.
Operator Skill Level:
CNC press brakes are user-friendly and require less operator skill due to their automated features and programmable controls. NC press brakes, while simpler in technology, often require a more experienced operator to achieve the best results.
Flexibility and Future Needs: If you anticipate a need for handling diverse projects or scaling production in the future, the adaptability of CNC press brakes makes them a worthwhile investment. For businesses with a steady output of similar products, an NC press brake may be adequate.
Budget Constraints:
CNC press brakes generally represent a higher upfront investment compared to NC models. Evaluate your budget and consider the potential return on investment, including efficiency gains and the ability to take on more complex jobs with a CNC press brake.
Maintenance and Operating Costs:
CNC press brakes may have higher maintenance and operating costs due to their complexity and the need for regular software updates. However, the increased efficiency and lower waste can offset these costs over time. NC press brakes typically have lower initial maintenance costs but might not offer the same efficiency benefits.
Conclusion
Choosing between a CNC and an NC press brake involves a careful assessment of your specific needs, the nature of your work, and your long-term objectives.
CNC press brakes offer unparalleled precision, flexibility, and efficiency for high-volume or complex bending operations.
NC press brakes can be a cost-effective solution for simpler tasks and smaller-scale operations.
Regardless of the choice, both CNC and NC press brakes play vital roles in the metal fabrication industry, each offering unique benefits to suit different manufacturing environments. Ultimately, the decision should be guided by a balanced consideration of production requirements, budget constraints, and future growth prospects to ensure that you select the right machine for your business’s needs.