Table of Contents
The Bending Machine is one of the most useful and common sheet metal machines used on a fabricating floor. Its versatility for bending a variety of materials in different thicknesses and compatibility with a wide range of different tools makes it a staple piece that can solely achieve dozens of different bends and shapes
But if you don’t know what you’re doing, then, like any other sheet metal machine, a press brake can be a dangerous machine. Today’s article will highlight four common mistakes that are made by new press brake operators.
4 Common Mistakes You Should Aviod When Using A Bending Machine
Performing pre-work checks
Something that every operator should get in the habit of doing is performing pre-work checks to ensure that all elements of the bending machine are in appropriate, functioning order. There should be a checklist that you can follow before operating the press brake each time from your supervisor.
Elements such as ensuring the die is correctly aligned and confirming that the flanges are the same measurement are crucial to an effective operation and mitigating any bending mistakes. If you are unsure about what needs to be checked – talk to your supervisor about putting an effective process in place.
Bending the flange the wrong way
Possibly the most common mistake made by operators – even seasoned ones – is bending the flange in the wrong direction. There are many reasons why this may occur, but one of the main ones relates to misreading the instructions.
For example, you may think the bend is meant to go one way because of how it’s instructed on paper – but it is actually inverted. This results in the bend going in the opposite direction. Every detail must be taken into account so a true and accurate bend can be achieved.
A handy trick is to place the metal pieces you’ll be bending down in the orientation they’re intended to be bent in. This way when you carry them across to the press brake – you won’t need to change their orientation and they’ll be ready to be placed in the correct alignment.
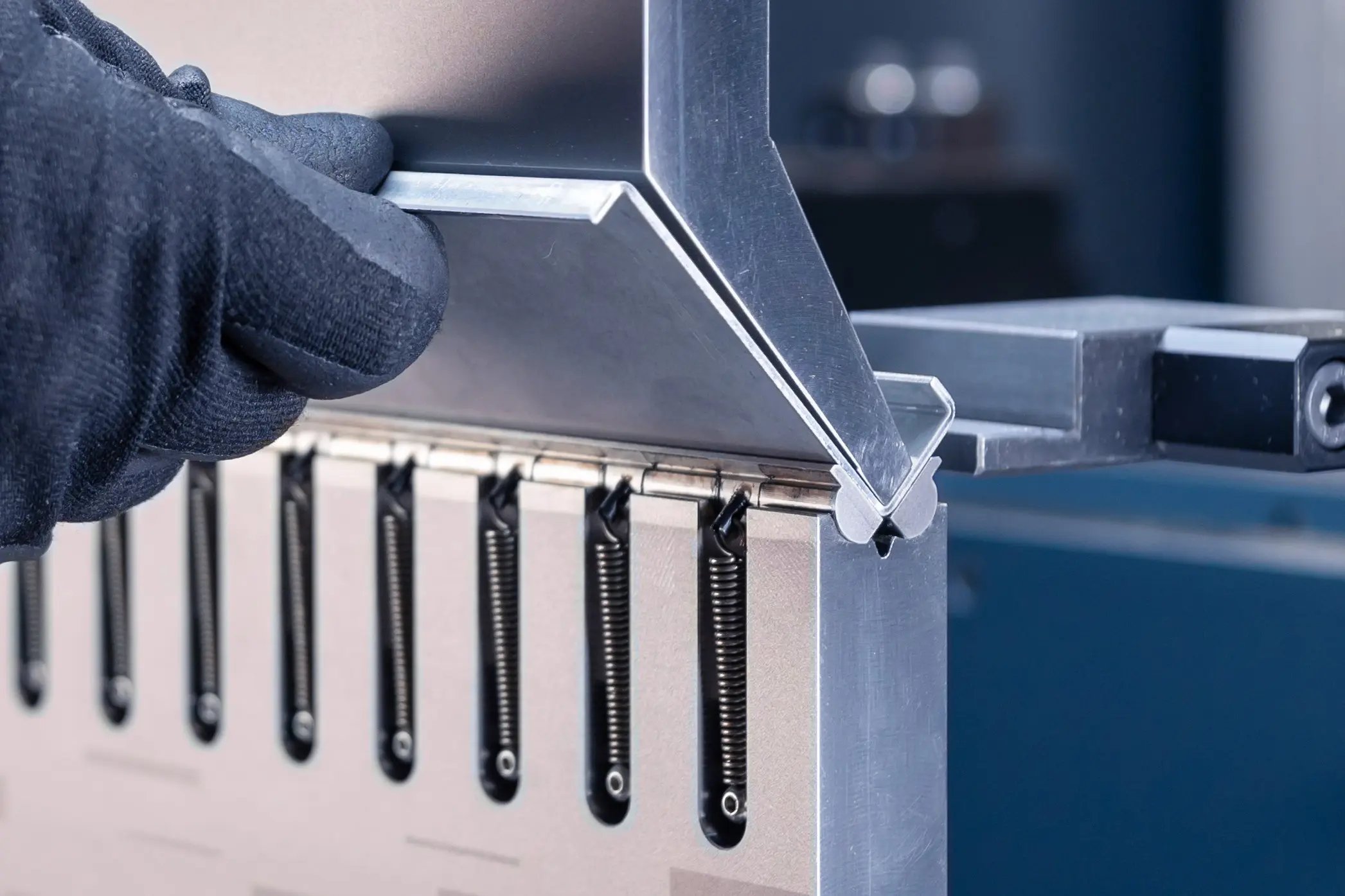
Incorrectly reading the instructions
The easiest way to ensure a successful bend is to meticulously read the instructions and guarantee that every minute detail is considered and understood. Sometimes the daftest mistakes can be made because a particular measurement was misunderstood or overlooked.
Knowing the language and process standards will help you decipher the instructions confidently and with ease as some things may be written a certain way. At least a basic understanding of mathematics will also help immensely when going over bending instructions.
Some common mistakes associated with misreading the instructions include bending in the wrong direction, misinterpreting or misreading the tolerances and overlooking special instructions. There may be particular pieces that require specialised instructions like being bent partially and then realigning some tools or calculations before continuing the bend.
This advice doesn’t only apply to press brake operators. All sheet metal machinery operators should ensure that the instructions are comprehensively and carefully read to guarantee a smooth operation.
Using the wrong tooling
Tools are an essential part of a bending machine and part of what makes it such a versatile machine. Unfortunately, it’s also the element that can cause many issues if not handled correctly. Using the wrong tool can produce disastrous results such as delaying jobs, wasting resources and sometimes even damaging the machine. Always ensure that you’re using the correct tool for the job before proceeding.
Additionally, you must know the type of bend that is required. Bottoming when you were meant to be air bending may put unnecessary strain onto the machine and ultimately ruin the bend (and y damage the machine).
In tandem with ensuring the right tools are being used, the correct tools must also be checked before every use to ensure they’re in proper condition. Worn out tools will provide subpar bends that aren’t up to the appropriate standard that the finished product should be.
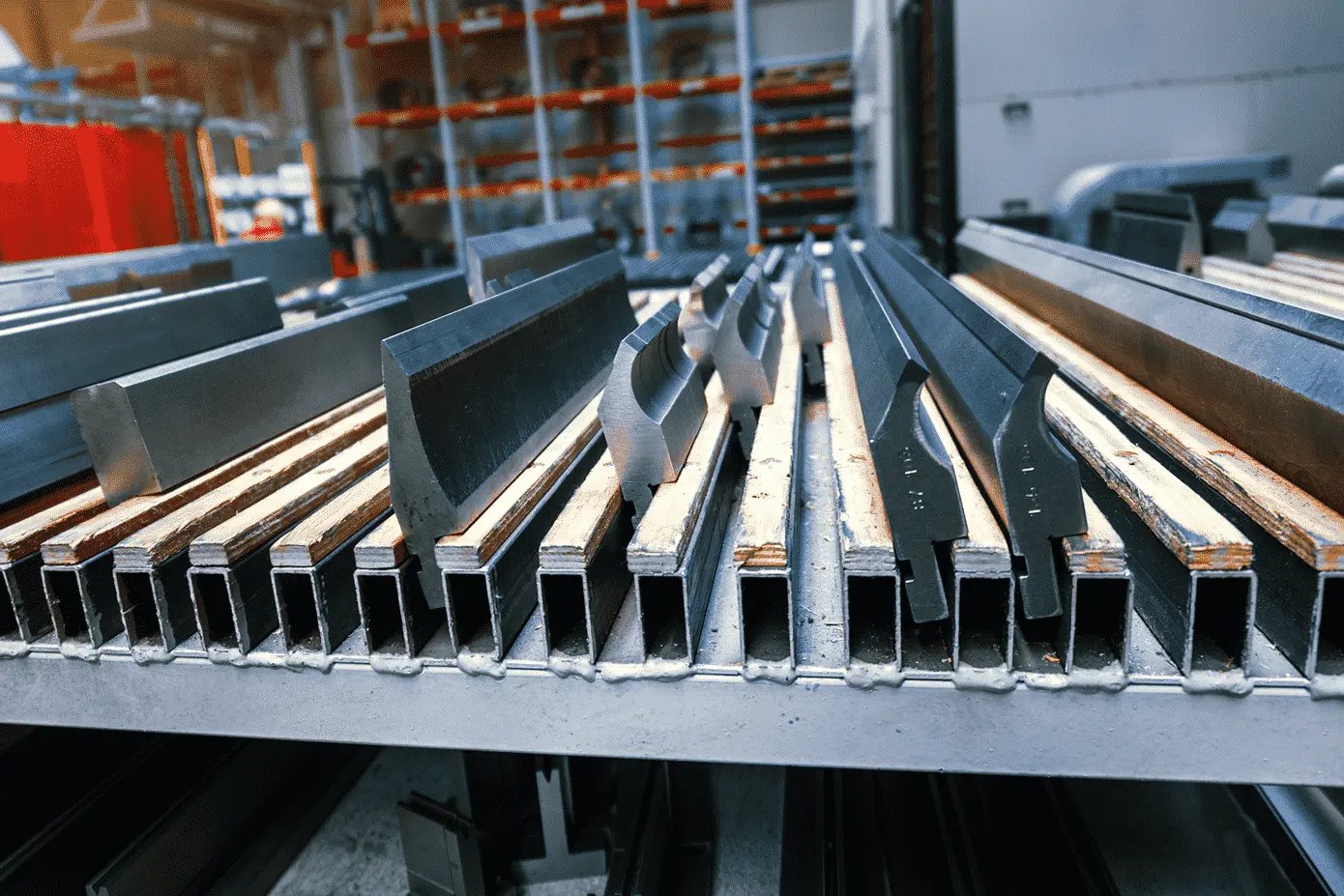