Cutting metal with laser technology is a highly advanced technique that leverages the power of concentrated laser beams to precisely cut through various types of metals. This method is celebrated for its remarkable precision, speed, and adaptability, making it the preferred choice for a wide range of industries, from automotive manufacturing to aerospace and electronics.
The laser cutting process involves directing a high-power laser at the metal, which heats, melts, or vaporizes the material along a specific path, creating clean and accurate cuts with minimal waste. This guide will explore the comprehensive aspects of cutting metal with laser, delving into its unique capabilities, the types of metals that can be cut, the advantages it offers, common applications, and key parameters that influence cutting efficiency and quality.
Can Metal Be Cut with a Laser?
Yes, metal can be cut with a laser. Laser cutting is a widely used method for cutting various metals, including steel, aluminum, stainless steel, brass, and copper. This process utilizes a highly focused laser beam that melts, burns, or vaporizes the metal, creating precise cuts with high accuracy. It's an efficient and versatile technique known for producing clean edges, reducing material waste, and achieving complex shapes that might be challenging with traditional cutting methods.
Modern laser cutting machines are capable of handling different thicknesses and metal types, making them popular in industries like automotive, aerospace, electronics, and construction.
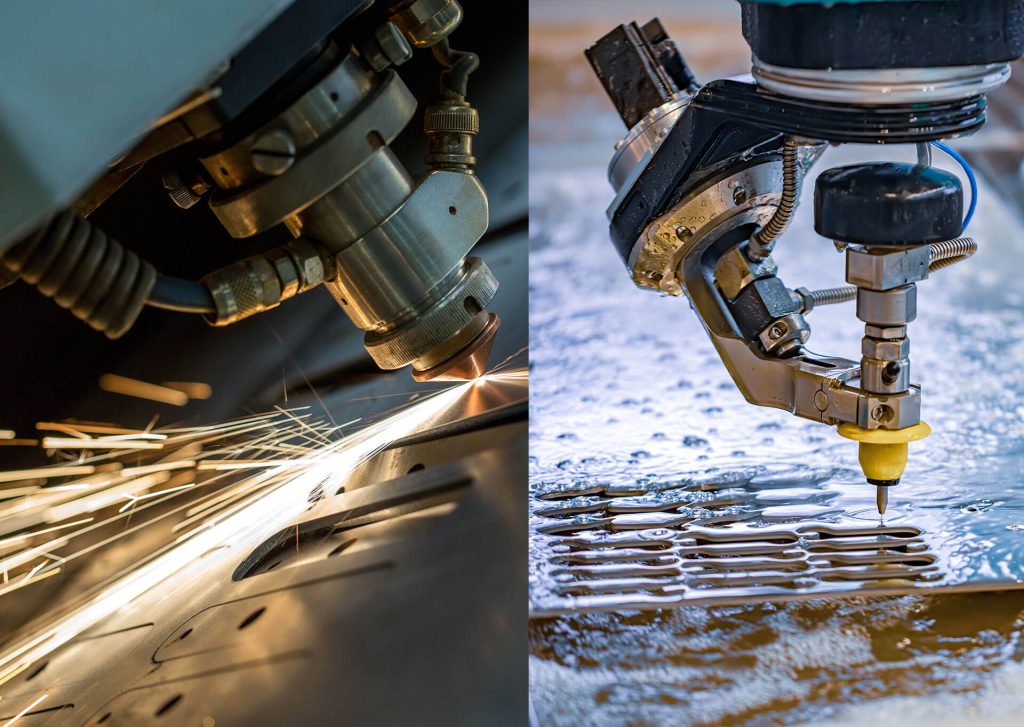
How Does Metal Laser Cutting Work?
Metal laser cutting is a sophisticated process that involves the use of a highly concentrated laser beam to slice through metal with precision. The laser’s intense heat melts, burns, or vaporizes the metal, producing sharp and clean edges. Below are the expanded stages of metal laser cutting:
1. Designing the Cutting Pattern
The first step is to create a precise design or cutting pattern using Computer-Aided Design (CAD) or other graphic software. These designs are often intricate and customized to meet specific project requirements, allowing manufacturers to visualize the final product before the cutting begins. The CAD file is then converted into a machine-readable format, such as DXF or DWG, to guide the laser cutter during the process.
2. Configuring the Laser Cutter
Once the design is ready, the laser cutter needs to be configured. The operator adjusts several key parameters based on the type of metal, its thickness, and the desired quality of the cut:
- Power Settings: Determines the laser’s energy output, which affects cutting depth and speed.
- Cutting Speed: Influences the precision and edge quality; slower speeds are used for thicker metals, while faster speeds are suitable for thinner materials.
- Focus Adjustment: Ensures that the laser beam is concentrated at the correct point on the metal surface for optimal accuracy.
Advanced laser cutters can also have automatic configuration features, reducing the need for manual adjustments and enhancing consistency.
3. Cutting the Metal
With the laser cutter configured, the machine proceeds to cut the metal by following the design pattern. The laser beam, directed by CNC (Computer Numerical Control), moves along the predefined path, melting or vaporizing the metal precisely where needed. This results in smooth and accurate cuts, even with complex shapes or detailed designs. High-power lasers, like fiber or CO2 lasers, are often used to handle different metal types and thicknesses, from thin sheets of aluminum to thick stainless steel.
4. Cooling and Post-Processing
After the metal is cut, it undergoes cooling, allowing the material to return to a stable temperature. This prevents warping or deformation due to residual heat. Any debris, slag, or dross (residue from the cutting process) is carefully removed, ensuring a clean finish. Depending on the project, additional post-processing steps may include:
- Deburring: Removing sharp edges or burrs left from the cutting process to ensure safety and a refined appearance.
- Applying Protective Coatings: In some cases, protective coatings or treatments are applied to enhance the metal's resistance to corrosion or wear.
- Quality Inspection: The final product is inspected for precision and quality, ensuring that it meets the specifications outlined in the design phase.
This detailed, step-by-step approach to metal laser cutting results in high-quality components with excellent dimensional accuracy, minimal waste, and a finish ready for immediate use or further processing.
Parameters of Cutting Metal with Laser
When cutting metal with a laser, several key parameters must be precisely controlled to ensure optimal cutting performance and quality. These parameters directly influence the efficiency, accuracy, and finish of the cut:
1. Laser Power
Laser power is a crucial parameter that determines the energy output of the laser, measured in watts (W) or kilowatts (kW). Higher laser power enables the cutting of thicker metals and increases cutting speed, but excessive power can lead to rough edges or excessive heat. The correct power level is selected based on the type and thickness of the metal being cut to achieve the best results.
2. Cutting Speed
Cutting speed refers to the rate at which the laser cutter moves across the metal surface. It has a direct impact on the quality of the cut, influencing factors like edge smoothness and precision. Slower speeds allow for finer, more precise cuts, especially with thicker materials, while faster speeds are suitable for thinner sheets and can improve overall production efficiency.
3. Pulse Frequency
Pulse frequency, or the number of laser pulses per second, affects the cutting speed, precision, and the size of the heat-affected zone (HAZ). A higher pulse frequency can enhance the cutting smoothness and reduce surface roughness, while a lower frequency is typically used for thicker materials to ensure adequate material removal without overheating.
4. Focus Spot Size
The focus spot size represents the diameter of the laser beam at its focal point on the metal surface. A smaller focus spot produces a narrower cut with greater detail and sharpness, making it ideal for intricate designs. Larger spot sizes are used for higher cutting power and are more suited to thicker metals where fine detail is less critical.
5. Assist Gas Pressure
Assist gas pressure plays a vital role in the laser cutting process by helping to remove molten material from the cutting area, cool the metal, and reduce oxidation. The pressure and type of assist gas—typically oxygen, nitrogen, or air—depend on the metal's properties and thickness:
- Oxygen is used for faster cutting speeds and thicker metals but may lead to slight oxidation.
- Nitrogen prevents oxidation and is preferred for stainless steel and aluminum to achieve clean edges.
- Air is a cost-effective alternative for less critical applications, offering moderate cutting performance.
Balancing these parameters ensures that the laser cutting process is optimized for efficiency, precision, and quality, producing clean and consistent results across various metal types and thicknesses.
Types of Laser for Cutting Metals
There are several types of laser cutters commonly used for metal cutting, each with unique features and advantages depending on the application. The primary types include:
1. Fiber Laser Cutters
Fiber laser cutters are among the most popular and advanced options for metal cutting. They use a solid-state laser source, where the laser beam is generated by a seed laser and then amplified using fiber optics. These lasers are highly efficient, offering faster cutting speeds and lower operating costs compared to other types.
Advantages:
- Excellent for cutting metals, especially reflective materials like aluminum, brass, and copper.
- High cutting speed and energy efficiency.
- Long-lasting and low maintenance due to fewer moving parts.
Applications: Ideal for industries like automotive, aerospace, and electronics, where high precision and fast production are essential.
2. CO2 Laser Cutters
CO2 laser cutters are traditional laser cutting machines that use a gas mixture (primarily carbon dioxide) to generate the laser beam. These lasers are well-known for their ability to cut non-metallic materials as well as metals.
Advantages:
- Can cut a wide range of materials, including metals, wood, plastics, and glass.
- High-quality cuts for thicker metals.
- Versatile for both cutting and engraving applications.
Applications: Commonly used in manufacturing, construction, and decorative industries, particularly for thicker or non-metallic materials.
3. Nd(Neodymium-Doped Yttrium Aluminum Garnet) Laser Cutters
Ndlasers are solid-state lasers that use a crystal as the laser medium. These lasers deliver high-intensity beams with short pulses, making them suitable for specific cutting and engraving tasks.
Advantages:
- High peak power, suitable for deep cutting and welding of metals.
- Effective for marking and engraving metals with intricate details.
- Works well with metals requiring short, intense bursts of energy.
Applications: Frequently used for specialized applications, such as welding, marking, and engraving in industries like jewelry, electronics, and medical devices.
4. Disk Laser Cutters
Disk laser cutters are a variation of solid-state lasers, similar to fiber lasers, but use a disk-shaped crystal as the gain medium. They offer a combination of high power and excellent beam quality.
Advantages:
- Stable power output and high beam quality.
- Efficient for thick metals and challenging cutting jobs.
- High energy density, enabling precise and deep cuts.
Applications: Suitable for heavy-duty industrial applications, especially when dealing with thick or hard metals.
5. Hybrid Laser Cutters
Hybrid laser cutters combine different laser technologies, such as integrating CO2 and fiber lasers, to create a versatile machine capable of cutting both metals and non-metals with high efficiency. This allows manufacturers to benefit from the strengths of each type.
Advantages:
- Offers flexibility in cutting different types of materials.
- Combines the advantages of multiple laser types, improving adaptability.
- Can handle diverse cutting and engraving projects.
Applications: Used in industries requiring both metal and non-metal cutting capabilities, such as signage, manufacturing, and custom fabrication.
6. Direct Diode Laser (DDL) Cutters
Direct Diode Lasers use diodes to generate the laser beam directly, without the need for a gain medium like in fiber or disk lasers. This results in an efficient and compact machine.
Advantages:
- High efficiency with low power consumption.
- Compact and simple design with minimal maintenance.
- Suitable for both thin and medium-thickness metals.
Applications: Commonly found in lightweight industrial applications, automotive manufacturing, and sheet metal processing.
These different types of laser cutters are selected based on factors such as material type, thickness, required precision, and specific industrial needs, ensuring the best results for each metal cutting task.
Cutting Metal with Laser: Detailed Explaination
Different types of metals have unique properties that make them suitable for laser cutting. Here’s a brief rundown of each of these metals and their physical and chemical properties:
Mild Steel (Carbon Steel)
Mild steel, also known as carbon steel, is a popular choice for laser cutting. It’s affordable, durable, and offers excellent weldability. With carbon content up to 0.3%, it’s not as brittle as higher-carbon steels.
- Melting point: 2,600 to 2,800 degrees Fahrenheit
- Tensile strength: 370-500 MPa
- Specific gravity: 7.85
Stainless Steel
Stainless steel is a corrosion-resistant alloy that’s ideal for a wide range of laser cutting stainless steel applications. It offers good strength and excellent resistance to oxidation.
- Melting point: 2,550 to 2,750 degrees Fahrenheit
- Tensile strength: 515 MPa
- Specific gravity: 7.93
Aluminum
Aluminum is a lightweight, soft, and ductile metal with excellent corrosion resistance thus making aluminum laser cutting ideal for a range of industrial applications.
- Melting point: 1,220 degrees Fahrenheit
- Tensile strength: 90-140 MPa
- Specific gravity: 2.70
Brass
Brass is an alloy of copper and zinc. It’s easy to machine, has good corrosion resistance, and is excellent for decorative purposes.
- Melting point: 1,650 to 1,720 degrees Fahrenheit
- Tensile strength: 345-470 MPa
- Specific gravity: 8.4-8.73
Copper
Copper has excellent thermal and electrical conductivity. It is tough, ductile, and can be readily welded and soldered.
- Melting point: 1,984 degrees Fahrenheit
- Tensile strength: 210-360 MPa
- Specific gravity: 8.96
Galvanized Steel
Galvanized steel is steel that has been coated with a layer of zinc to improve its corrosion resistance.
- Melting point: 2,600 to 2,800 degrees Fahrenheit
- Tensile strength: 330-505 MPa
- Specific gravity: 7.85
Titanium
Titanium is known for its strength, lightness, and corrosion resistance. It’s one of the most difficult metals to cut, but laser cutting can handle it efficiently.
- Melting point: 3,034 degrees Fahrenheit
- Tensile strength: 240-370 MPa
- Specific gravity: 4.506
Nickel Alloys
Nickel alloys are resistant to corrosion and can maintain their structural integrity at high temperatures, making them ideal for use in harsh environments.
- Melting point: Varies by alloy
- Tensile strength: Varies by alloy
- Specific gravity: Varies by alloy
Silver
Silver is a soft, white, lustrous metal that possesses the highest electrical and thermal conductivity of all metals.
- Melting point: 1,762 degrees Fahrenheit
- Tensile strength: 170 MPa
- Specific gravity: 10.49
Gold
Gold is a dense, soft, shiny metal that’s the most malleable and ductile of all known metals.
- Melting point: 1,948 degrees Fahrenheit
- Tensile strength: 120 MPa
- Specific gravity: 19.32
Platinum
Platinum is a dense, malleable, ductile, highly unreactive, precious metal with a silvery-white color.
- Melting point: 3,215 degrees Fahrenheit
- Tensile strength: 125-240 MPa
- Specific gravity: 21.45
Zinc
Zinc is a bluish-white, lustrous, diamagnetic metal. It’s somewhat less dense than iron and has a hexagonal crystal structure.
- Melting point: 787.15 degrees Fahrenheit
- Tensile strength: 110-200 MPa
- Specific gravity: 7.14
Tin
Tin is a malleable, ductile, highly crystalline, silvery-white metal. Its main use is to prevent corrosion.
- Melting point: 449.47 degrees Fahrenheit
- Tensile strength: 9-14 MPa
- Specific gravity: 7.265
Lead
Lead is a heavy metal that is denser than most common materials. It’s soft and malleable, and has a relatively low melting point.
- Melting point: 621.43 degrees Fahrenheit
- Tensile strength: 17 MPa
- Specific gravity: 11.34
Inconel
Inconel is a family of austenitic nickel-chromium-based superalloys. It’s resistant to oxidation and corrosion and performs well at high temperatures.
- Melting point: 2,350 to 2,500 degrees Fahrenheit
- Tensile strength: 690-965 MPa
- Specific gravity: 8.2
What is the best metal for laser cutting?
The best metal for laser cutting depends on the specific application and requirements. However, mild steel, stainless steel, and aluminum are among the most commonly used due to their excellent machinability and compatibility with laser cutting.
Methods Used in Laser Cutting Processes
There are various methods to cut different materials in the laser cutting process. The following introduces several common methods in laser cutting, including vaporization, melt and blow, thermal stress cracking, stealth dicing, and burning stabilized laser cutting.
Vaporization Cutting
In vaporization cutting, the focused beam heats the material’s surface to a flashpoint, creating a keyhole. The keyhole causes an abrupt rise in absorptivity, rapidly deepening the hole. As the hole deepens and the material boils, the produced vapor erodes the molten walls, blowing ejection out and growing the hole even further. This process commonly cuts non-melting materials like wood, carbon, and thermoset plastics.
Reactive Cutting/ Flame Cutting
Reactive cutting is known as “flame cutting” and “burning stabilized laser gas cutting.” Reactive cutting is similar to oxygen torch cutting, except the laser beam is the ignition source. This process is often intended for cutting carbon steel in thicknesses that exceed 1 mm. Moreover, it may be employed for cutting very thick steel plates using relatively little laser power.
Melt and Blow Cutting/ Fusion Cutting
Melt and blow cutting, also called fusion cutting, employs high-pressure gas to blow molten material away from the cutting region, lowering the power need significantly. The material is first heated to its melting point. A gas jet blows the molten material out of the kerf, eliminating the need to raise the temperature of the material anymore. Metals are often cut with this method.
Thermal Stress Cracking Cutting
Thermal stress cracking cutting exploits the feature that brittle materials are particularly susceptible to thermal fracture. A concentrated beam is directed toward the surface, resulting in localized heating and thermal expansion. This causes a crack, which may be directed by moving the beam. The crack may be moved in m/s. Thermal stress cracking is commonly used in glass cutting.
Stealth Dicing Cutting of Silicon Wafers
Stealth dicing process separates microelectronic chips in semiconductor device fabrication from silicon wafers. It employs a pulsed Nd:YAG laser whose wavelength is perfectly adapted to the electronic band gap of silicon.
Advantages and Disadvantages of Metal Laser Cutting
Metal laser cutting has revolutionized the manufacturing industry, offering precise and efficient solutions for various applications. Below are the critical advantages and disadvantages of this manufacturing technique.
Advantages of Cutting Metal with Laser
High Precision and Accuracy
Metal laser cutting is renowned for its exceptional precision and accuracy. Laser beams can achieve intricate cuts and shapes with minimal deviation, ensuring high-quality end parts. Generally, the parts can be laser cut to within a tolerance of 0.2mm. The high precision of laser cutting is particularly valuable in industries such as aerospace, electronics, and medical devices, where tolerances are critical.
Material Versatility
Laser cutting can handle various metal materials, including stainless steel, aluminum, mild steel, alloys, and exotic metals. This versatility allows manufacturers to address diverse project requirements without needing tool changes, reducing setup time and costs. It is also suitable for various thicknesses, making it a versatile option for different applications.
Cutting Flexibility
The laser cutting processes are extremely versatile and flexible. A single laser cutter can perform various cutting tasks, including simple cuts, sophisticated ones with complex details, markings, drilling, and even engravings. As a result, producers do not need to replace tooling time by time during the process.
Speed and Efficiency
Once programmed, parts may be cut in seconds, far quicker than plasma or waterjet cutting processes. High cutting speeds, rapid piercing, and kerf widths lead to shorter production cycles and increased throughput.
Low Power Consumption
Unlike other cutting devices, laser cutters don’t need to move distinct parts of the device. This enables them to cut material while spending minimal power. While laser cutters may require up to 10kW of energy, most other operations can take up to five times that amount. Meantime, the low power consumption also makes them easier on the wallet.
Contactless Process
Unlike mechanical cutting methods, laser cutting is a non-contact process. This reduces the risk of material contamination and eliminates the need for tool wear, minimizing maintenance and replacement costs.
Disadvantages of Cutting Metal with Laser
High Initial Capital Investment
Acquiring and setting up top-quality laser cutters involves a significant initial capital investment. The cost of a typical laser cutter may be twice as high as the cost of waterjet or plasma cutters. Small businesses or startups might find the upfront costs prohibitive, although the long-term benefits can outweigh the initial expenditure.
Operating Costs
While laser cutting is efficient, operational costs can accrue over time due to electricity consumption, gas supply, and maintenance requirements. Regular maintenance and servicing are essential to ensure consistent performance.
Reflective Material Limitations
While laser cutting suits a wide range of metals, certain materials, such as reflective metals like brass or polished stainless steel, can be more challenging due to their high reflectivity. Additional measures, such as using specialized gases or coatings, may be required to overcome these limitations.
Heat-Affected Zone (HAZ)
Laser cutting generates heat, creating a heat-affected zone along the cut edges. This can result in material distortion, especially in thinner materials, potentially affecting the final product’s integrity. Therefore, it can require secondary processing in some use cases.
Require Professional Operator
You may need a professional and skilled operator to run the machine during part manufacturing to get the most out of your laser cutters. This way, the operator will rapidly identify a fault or incorrect setup that could hinder manufacturing operations or the machine’s integrity.
Metal Thickness Limitations
Although laser cutting works well with a wide range of materials, it is recommended that thick metals be cut using alternative methods. Typical laser cutters are excellent for cutting aluminum sheets up to 15 mm thick and steel up to 6 mm thick.
Design Tips for the Perfect Laser Cut Metal
Here are some design tips to help you achieve the best laser cut:
- Close the Edges of Your Design. Everywhere you intend to have open or free from metal must be surrounded by a complete, closed contour. If you wish to have a circle laser cut out of a sheet of metal, for example, ensure the arc in your file is a fully connected circle.
- Mind your Metal Tabs and Notches. Getting tabs and notches right maintains the metal sheet’s or plate’s structural integrity while the product is being produced.
- Identify Line Thicknesses and Depths. Clarify and identify what each line style implies when submitting your file.
- Plan for Precise Holes and Laser Accordingly. When aiming to get holes with tight tolerances, it is recommended to employ a laser cutter to pierce and etch the designated locations for said holes. Subsequently, proceed to drill the holes straight, utilizing a drill bit.
- Decide on Rounded Metal Corner Fillets or Sharp Angles. Sharp corners are frequently observed in sheet metal parts. To enhance safety, fillets can be added to sharp corners.
- Correctly Lay out Your File for Multiple Parts or Thin Features. When cutting many parts on the same metal sheet, it’s frequently desirable to leave a distance at least the thickness of the material between them.
- Choose the Right Material. Different metals have varying levels of reflectivity and thermal conductivity, which can affect the cutting process.
- Your Details Can’t Be Smaller Than Metal Thickness. The higher the thickness, the less the laser can penetrate and cut the material.
- Remember the Kerf. Kerf refers to the material that evaporates when the laser beam hits the laser cutting material.
Conclusion
Cutting Metal with Laser is a highly effective technique for achieving precise and detailed cuts in metals, making it suitable for a broad range of materials. However, it's important to note that purchasing a laser cutter involves a significant initial investment, making outsourcing metal cutting services a practical choice for many. Alternatives to laser cutting for sheet metal include EDM, CNC milling, punching, waterjet, and plasma cutting—each offering unique benefits based on your manufacturing needs.
If you're searching for a reliable service provider for high-quality and precise metal cutting, KRRASS is the solution. We are experts in laser cutting, ensuring that the final product meets your exact specifications. Additionally, KRRASS offers a variety of prototyping services, including CNC machining, 3D printing, injection molding, and urethane casting. Don't hesitate—contact us today!