Überblick
Der 3,2 m Abkantpresse ist ein sehr gefragtes Modell, das für seine außergewöhnlichen Bearbeitungsfähigkeiten und umfangreichen Anwendungsmöglichkeiten bekannt ist. Seine Beliebtheit beruht auf seiner Fähigkeit, eine Vielzahl komplexer Metallbearbeitungsaufgaben zu bewältigen, wobei sowohl große Komponenten als auch empfindliche Teile bearbeitet werden können. Dank seiner großzügigen Tischgröße eignet es sich auch für die Bearbeitung größerer Werkstücke, was zu einer höheren Produktivität führt.
Die Abkantpresse 3200 ist noch attraktiver, weil sie über eine umfassende Palette an Funktionen und anpassbaren Konfigurationen verfügt. Diese Maschine kann mit einer Reihe von Werkzeugen und Matrizen ausgestattet werden, die verschiedene Bearbeitungsmethoden wie Biegen, Ziehen und Stanzen ermöglichen. Dank dieser Vielseitigkeit kann sie die unterschiedlichen Anforderungen verschiedener Branchen nahtlos erfüllen.
In wichtigen Branchen wie der Luft- und Raumfahrt, dem Bauwesen und der Elektronik spielt die Abkantpresse 3200 eine zentrale Rolle und bietet eine robuste Unterstützung für den Fortschritt der Metallverarbeitungsindustrie. Ihre Leistungsfähigkeit bei der Bewältigung komplexer Metallverarbeitungsaufgaben trägt wesentlich zur Entwicklung und zum Wachstum verschiedener Bereiche bei und unterstreicht ihre Bedeutung als Eckpfeiler der modernen Fertigung.
Bedeutung von 3,2 m langen Abkantpressen in der Metallverarbeitungsindustrie
Die Abkantpresse 3200 ist eine Blechbiegemaschine mit einer maximalen Biegelänge von 3200 und eignet sich für mittelgroße Metallbearbeitungsaufgaben und kann viele gängige Werkstückgrößen verarbeiten. Sie kann komplexe Metallbearbeitungsaufgaben bewältigen, egal ob für große Teile oder feine Komponenten. Ihre leistungsstarken Bearbeitungsfunktionen machen sie in so unterschiedlichen Bereichen wie Brücken, Schiffen, Motoren, Schmuck, Uhren usw. nützlich. Präzise Steuerungssysteme und hochpräzise Bearbeitungsprozesse sind außerdem unerlässlich, um Maßgenauigkeit und Bearbeitungsqualität für eine hochwertige Metallbearbeitung sicherzustellen.
Gleichzeitig bietet die Abkantpresse 3200 eine breite Palette an Funktionen und flexiblen Konfigurationen, die an unterschiedliche Verarbeitungsanforderungen angepasst und optimiert werden können. So ist sie beispielsweise je nach den unterschiedlichen Biegeanforderungen in der Produktion hochflexibel und kann mit einer Vielzahl von Werkzeugen und Formen ausgestattet werden, um eine Vielzahl von Verarbeitungsmethoden wie Biegen, Strecken, Stanzen usw. zu erreichen. Darüber hinaus sind einige Modelle mit automatischen Zuführ- und Lade-/Entladefunktionen ausgestattet, die die Produktionseffizienz weiter verbessern.
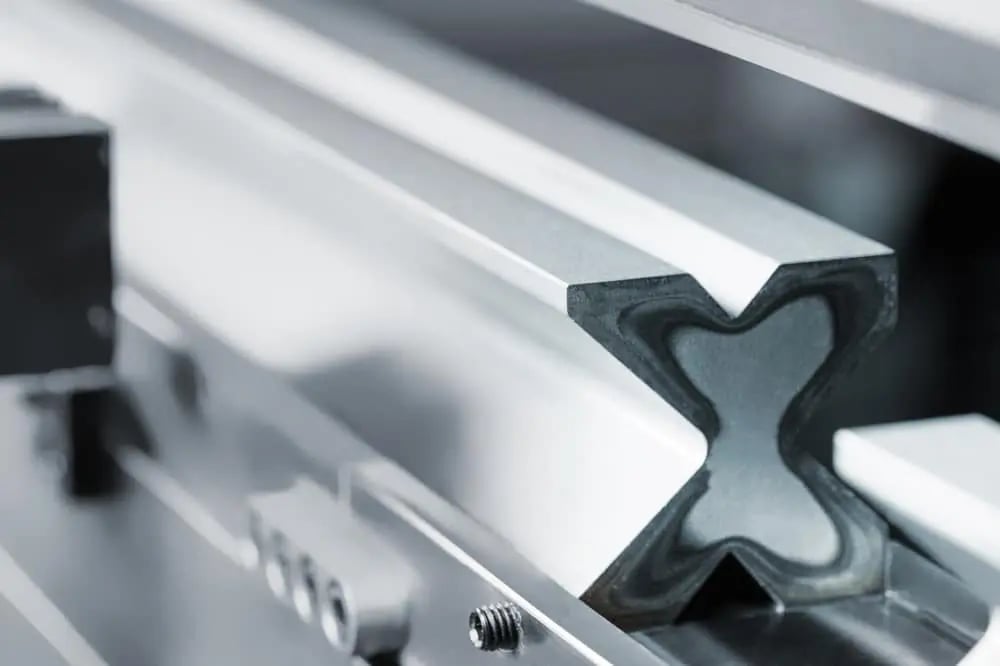
Warum Sie sich für eine 3,2 m lange Abkantpresse entscheiden sollten
Hochpräzise Stanzfähigkeit
In der modernen Fertigungslandschaft ist der Stanzprozess ein integraler Bestandteil, und die Fähigkeit zur hochpräzisen Stanzung dient als entscheidender Indikator für die Leistung der Ausrüstung. Die 3200 Abkantpresse, bekannt für seine herausragende Qualität, spielt aufgrund seiner bemerkenswerten hochpräzisen Stanzfähigkeit eine zentrale Rolle in der Fertigungsindustrie. Diese Fähigkeit, millimetergenaue Stanzergebnisse zu erzielen, ist für die Herstellung erstklassiger, qualitativ hochwertiger Produkte unabdingbar.
Die Abkantpresse 3200 zeichnet sich durch außergewöhnliche Bearbeitungsgenauigkeit beim Stanzen einer Vielzahl komplexer Teile aus. Ob es sich um große Werkstücke oder komplizierte Komponenten handelt, ihre hochpräzise Stanzfähigkeit garantiert genaue Details in jedem Prozessschritt. Dies stellt sicher, dass Bediener Teile und Produkte mit Maßgenauigkeit und gleichbleibender Qualität herstellen können.
Großformatige Stempelfunktion
Die Stanztechnologie für große Formate spielt in der modernen Fertigung eine entscheidende Rolle, insbesondere in Branchen wie der Automobil- und Luftfahrtindustrie. Diese Branchen erfordern Stanzkapazitäten für große Formate, um große Teile herzustellen, was Vorteile in Bezug auf Materialeinsparungen und niedrigere Produktionskosten bietet. Die Abkantpresse 3200 ist eine leistungsstarke Stanzmaschine für große Formate und leistet einen wichtigen Beitrag für diese Branchen.
Diese Pressentechnologie findet nicht nur Anwendung in der Automobil- und Luftfahrtindustrie, sondern auch in Bereichen wie dem Baugewerbe, der Haushaltsgeräte- und der Elektronikindustrie. Um den vielfältigen Anforderungen dieser Branchen gerecht zu werden, erfordern großformatige Stanzpressen technische Raffinesse und komplexe Konstruktionsdesigns. Die Abkantpresse 3200 ist ein Beweis für präzises Design und präzise Fertigung und bietet eine robuste Stanzleistung für ein breites Spektrum an Stanzaufgaben für großformatige Teile.
Effiziente und stabile Druckleistung
Effizienz und Stabilität der Pressleistung sind in der modernen Fertigung von entscheidender Bedeutung. Dies bedeutet, dass Genauigkeit und Stabilität bei hohen Geschwindigkeiten aufrechterhalten werden müssen, um qualitativ hochwertige Pressergebnisse zu erzielen. Darüber hinaus erfordert eine effiziente und stabile Stanzleistung robuste Fehlerbehebungs- und automatische Schutzfunktionen. Diese Funktionen stellen sicher, dass die Anlage bei Auftreten eines Problems sofort angehalten wird, wodurch potenziell erhebliche Verluste vermieden werden.
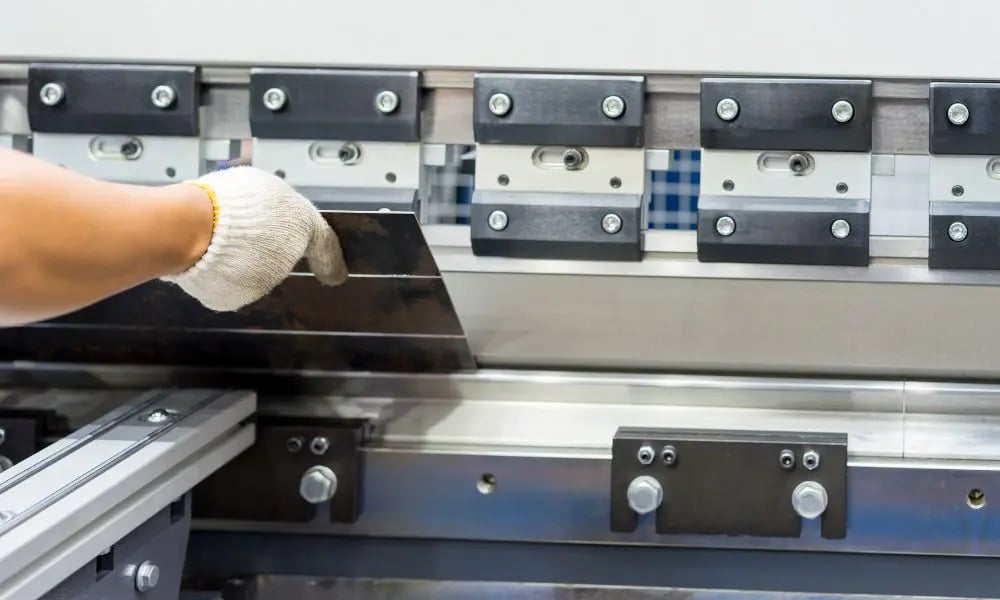
Benutzerfreundliche Bedienoberfläche
Effizienz und Stabilität sind für Hochgeschwindigkeitspressvorgänge unerlässlich. Die Abkantpresse 3200 behält ihre Genauigkeit und Stabilität bei hohen Geschwindigkeiten bei und gewährleistet so qualitativ hochwertige Ergebnisse. Automatische Schutzfunktionen erhöhen ihre Zuverlässigkeit, indem sie die Anlage bei Problemen umgehend stoppen und potenzielle Verluste verhindern.
Benutzerfreundliche Bedienoberfläche
Mit dem technologischen Fortschritt entwickelt sich die Bedienoberfläche von Stanzgeräten immer menschlicher. Eine benutzerfreundliche, humanisierte Bedienoberfläche ermöglicht es Benutzern, sich schnell mit den Betriebsabläufen vertraut zu machen, wodurch die Lernkurve verkürzt wird. Diese Oberfläche enthält umfangreiche Informationsanzeige- und Datenanalysefunktionen, die es den Bedienern ermöglichen, den Betriebsstatus der Geräte in Echtzeit zu verstehen und umgehend Anpassungen an den Produktionsstrategien vorzunehmen. Darüber hinaus sollte eine humanisierte Bedienoberfläche robuste Schutzmaßnahmen umfassen, um die Sicherheit der Bediener zu gewährleisten.
Zusammenfassend lässt sich sagen, dass die wesentlichen Merkmale moderner Stanzmaschinen hohe Präzision, große Größe, hohe Effizienz und Stabilität sowie eine benutzerfreundliche Bedienoberfläche umfassen. Geräte mit diesen Eigenschaften erfüllen nicht nur die Nachfrage nach qualitativ hochwertiger und hocheffizienter Produktion, sondern steigern auch die Wettbewerbsfähigkeit von Unternehmen. Im weiteren Kontext tragen sie zur Transformation und Modernisierung der chinesischen Fertigungsindustrie bei. Bei der Auswahl von Pressgeräten sollten Unternehmen diese Merkmale sorgfältig berücksichtigen, um sicherzustellen, dass der Erwerb hochwertiger Geräte ihren spezifischen Anforderungen entspricht.
Vier Vorteile der 3,2 m langen Abkantpresse
Verbesserte Verarbeitungskapazität
Die Abkantpresse 3200 ist mit herausragenden Verarbeitungsfunktionen und hoher Präzision ausgestattet und erweist sich als Kraftpaket für die schnelle und genaue Ausführung einer Vielzahl komplexer Stanzaufgaben. Ihre bemerkenswerte Hochgeschwindigkeitsstanzfähigkeit und schnelle Reaktionszeit auf Bewegungen steigern die Produktivität erheblich. Bediener, die diese Funktionen nutzen, können eine größere Anzahl von Verarbeitungsaufgaben in kürzerer Zeit effizient erledigen, wodurch Produktionszyklen beschleunigt und Herstellungskosten gesenkt werden.
Vielseitige Anwendungsmöglichkeiten
Die Vielseitigkeit und die anpassbaren Konfigurationen der Maschine machen sie zu einer dynamischen Lösung für eine Vielzahl von Bearbeitungsanforderungen. Ob bei der Bearbeitung von großen Bauteilen oder komplizierten Details, die Abkantpresse 3200 erweist sich als leistungsfähig. Darüber hinaus erweitert ihre Fähigkeit, mit verschiedenen Werkzeugen und Formen für unterschiedliche Verarbeitungsmethoden wie Biegen, Strecken und Stanzen ausgestattet zu werden, ihren Anwendungsbereich in verschiedenen Branchen.
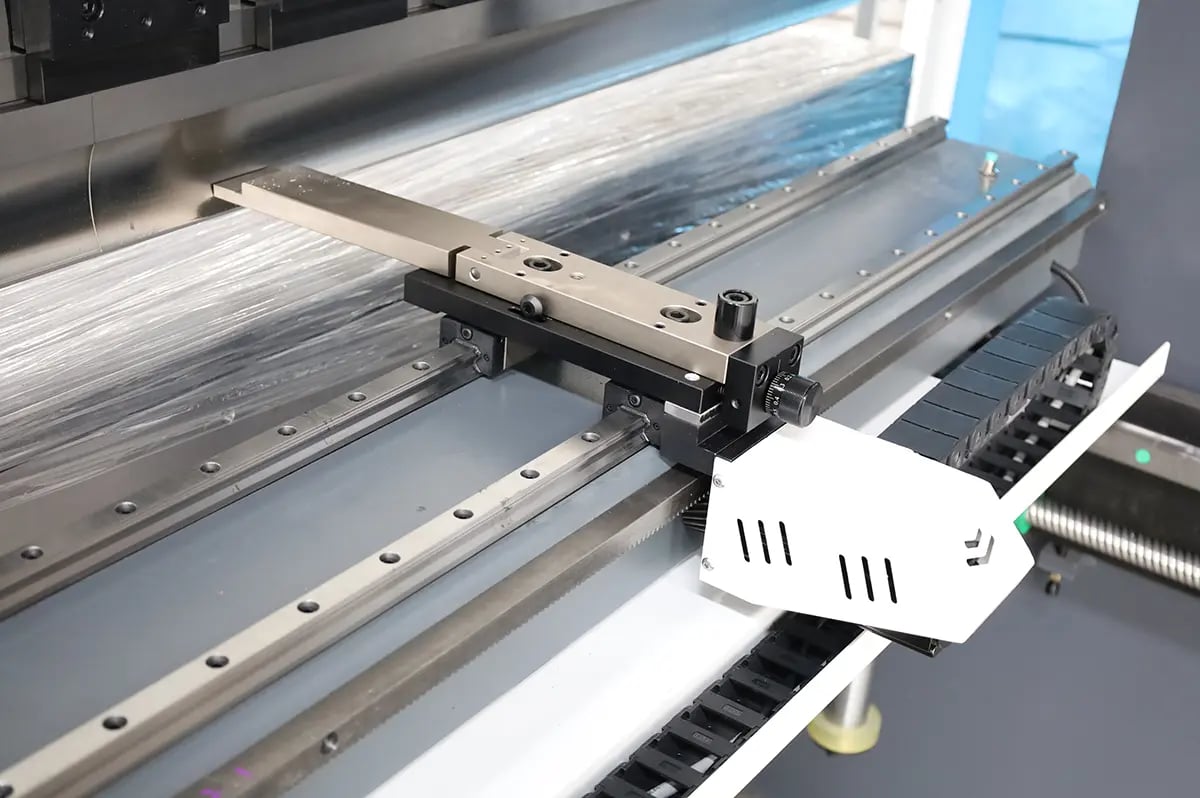
Reduzierung der Arbeitsintensität
Die Abkantpresse 3200 steigert die Betriebseffizienz erheblich, indem sie die Arbeitsintensität der Bediener verringert. Die Integration automatisierter Funktionen in Verbindung mit einer benutzerfreundlichen Bedienoberfläche rationalisiert den Betrieb. Automatisierte Lade- und Entladefunktionen sowie ein intelligentes CNC-System vereinfachen die Aufgaben der Bediener. Da die Bediener die Parameter mühelos einstellen können, führt das Gerät den Großteil der Arbeit autonom aus, wodurch die körperliche Arbeit verringert und die allgemeine Betriebseffizienz verbessert wird.
Zuverlässigkeit und Haltbarkeit
Die Abkantpresse 3200 wurde mit höchster Präzision und aus hochwertigen Materialien gefertigt und zeichnet sich durch Zuverlässigkeit und Langlebigkeit aus. Ihr stabiler Betrieb und ihre lange Lebensdauer tragen zu einem zuverlässigeren Produktionsprozess bei. Dies wiederum schafft Vertrauen bei den Bedienern und minimiert Geräteausfälle und Ausfallzeiten. Das Ergebnis ist ein höheres Maß an Stabilität und Nachhaltigkeit in der Produktionslinie, was letztlich die Gesamteffizienz der Fertigungsabläufe steigert.
Anwendungsszenarien
Verarbeitung von Autoteilen
Im Bereich des Stanzens von Automobilteilen spielt die Abkantpresse 3200 als wichtiges Stanzgerät eine zentrale Rolle. Sie eignet sich hervorragend zum Formen verschiedener Bleche in präzise Formen und Abmessungen durch robusten Druckeinsatz und sorgfältige Formkontrolle. Sie ist in der Automobilherstellung weit verbreitet und erweist sich als unverzichtbar für die Herstellung von Komponenten wie Abdeckungsteilen und Strukturelementen.
Die Abkantpresse 3200 zeichnet sich durch ihre enorme Presskraft und unerschütterliche Steifigkeit aus und gewährleistet eine beispiellose Kontrolle über die Bleche während der Verarbeitung. Diese Präzision wird durch ein fortschrittliches Form- und Vorrichtungssystem noch weiter verstärkt, das schnelle Anpassungen an die unterschiedlichen Verarbeitungsanforderungen verschiedener Automobilkomponenten ermöglicht. Dies steigert nicht nur die allgemeine Produktionseffizienz, sondern ermöglicht auch ein höheres Maß an Flexibilität als Reaktion auf dynamische Fertigungsanforderungen.
Durch den Einsatz modernster CNC-Technologie erreicht die Abkantpresse 3200 ein beispielloses Maß an hochpräziser Pressverarbeitung. Durch die präzise Steuerung der Schließhöhe und des Drucks der Form wird garantiert, dass die verarbeiteten Teile perfekt den Designspezifikationen entsprechen. Diese Präzision minimiert den Bedarf an umfangreichen Korrekturen und Anpassungen in späteren Phasen, rationalisiert den Herstellungsprozess und steigert die Effizienz.
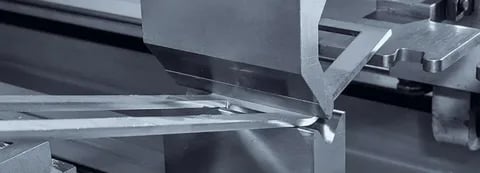
Bei der Konstruktion der Biegemaschine 3200 steht die Sicherheit im Mittelpunkt. Sie ist mit einem automatischen Erkennungssystem ausgestattet, das Anomalien an Formen und Vorrichtungen sofort erkennt und Schutzmaßnahmen auslöst, um Geräteschäden zu verhindern und das Unfallrisiko für das Personal zu verringern. Ergänzt durch eine Reihe von Sicherheitsfunktionen, darunter eine fotoelektrische Schutzvorrichtung und ein Not-Aus-Schalter, legt die Maschine Wert auf das Wohlbefinden der Bediener und sorgt für eine sichere Arbeitsumgebung.
Im Wesentlichen trägt die Abkantpresse 3200 nicht nur wesentlich zur Produktion von Automobilkomponenten bei, sondern definiert auch Industriestandards neu, indem sie Präzision, Anpassungsfähigkeit und Sicherheit vereint. Als wesentlicher Akteur im komplexen Tanz der Automobilherstellung bleibt sie ein Symbol für Innovation, Effizienz und ein unerschütterliches Engagement für das Wohlergehen derjenigen, die in ihrem Umfeld tätig sind.
Bearbeitung von Karosserieverkleidungsteilen und Strukturteilen
Die Bearbeitung von Karosserieverkleidungsteilen und Strukturteilen ist ein entscheidender Schritt in der Automobilherstellung. Die Abkantpresse 3200 spielt in diesem Prozess eine Schlüsselrolle. Diese Hochleistungsmaschine kann Bleche mit einer Dicke von bis zu 3.200 mm und mehr verarbeiten und bietet eine präzise und zuverlässige Bearbeitungslösung für die Herstellung von Karosseriekomponenten.
Mit der Abkantpresse Modell 3200 können Bediener Bleche problemlos biegen und formen, um eine große Bandbreite komplexer Formen zu erreichen. Bei Karosserieverkleidungsteilen bedeutet dies, dass Türen, Hauben, Dächer und andere Teile präzise hergestellt werden können, die den Designanforderungen entsprechen. Bei Karosseriestrukturteilen gewährleistet der hohe Druck und die Präzision der Biegemaschine Modell 3200 die Festigkeit und Stabilität von Teilen wie Karosserierahmen, Stützstrukturen und anderen wichtigen Komponenten.
Haushaltsgeräteindustrie
Stanzen von Gehäusen und Zubehör
Das Stanzen von Gehäusen und Zubehör ist ein kritischer Prozess in der Haushaltsgeräteindustrie, insbesondere in Kombination mit der Abkantpresse 3200, mit der sich höhere Produktivität und Produktqualität erzielen lassen. Diese leistungsstarke Maschine kann größere Blechgrößen verarbeiten und bietet ein breites Spektrum an Möglichkeiten für die Bearbeitung von Gehäusen und Zubehör für Haushaltsgeräte.
Verbessern Sie das Erscheinungsbild und die Leistung Ihres Produkts
In Kombination mit der Biegemaschine 3200 werden komplizierte und aufwendige Formen zum Leben erweckt. Zahlreiche Haushaltsgeräte erfordern ein unverwechselbares Design mit Kurven, Ecken und anderen speziellen Formen. Die Bedeutung der hohen Druckkapazität und der sorgfältigen Steuerung der Biegemaschine wird in diesem Zusammenhang besonders deutlich. Die Bediener erhalten die Möglichkeit, die Parameter der Maschine entsprechend den Produktdesignspezifikationen fein abzustimmen. Diese Präzision ermöglicht das Biegen von Metallblechen in unzählige komplexe Formen und erleichtert die Diversifizierung und Personalisierung des Produktaussehens mit höchster Genauigkeit.
Biegen und Formen von Blechen
In der Bauindustrie sind das Formen und Formen von Blechen integrale Prozesse. Mithilfe von Spezialmaschinen wie der Abkantpresse 3200 wird Präzision beim Biegen und Formen von Blechen unterschiedlicher Dicke und Zusammensetzung erreicht. Diese Techniken finden umfassende Anwendung bei der Herstellung wichtiger Gebäudekomponenten, darunter verschiedene Balken und Säulen sowie dekorative Außenpaneele.
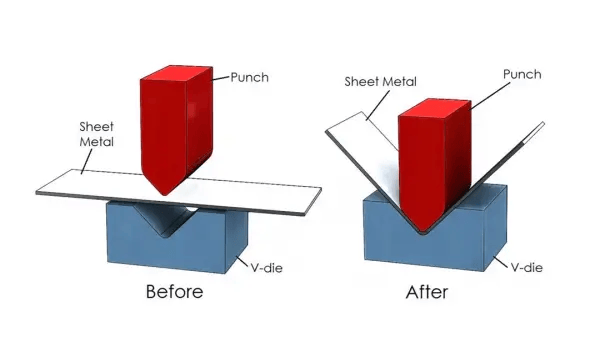
Bearbeitung von Baukonstruktionen und Dekorationsmaterialien
Im Bausektor dient Blech als vielseitiges Material zur Herstellung einer Reihe struktureller und dekorativer Elemente. Maschinen wie die Abkantpresse 3200 ermöglichen das präzise Schneiden von Blech und passen es an die spezifischen Größen- und Formanforderungen für Anwendungen wie Wandverkleidungen, Dächer, Geländer, Treppenhandläufe und mehr an. Um das gewünschte Design zu erreichen und ein hochwertiges Erscheinungsbild beizubehalten, ist eine sorgfältige Bearbeitung dieser Metallprodukte erforderlich.
Insgesamt sind das Biegen und Formen von Blechen in verschiedenen Branchen, darunter auch im Baugewerbe, zentrale Prozesse. Moderne Geräte wie die Abkantpresse 3200 verbessern die Genauigkeit und Effizienz der Blechverarbeitung erheblich und erfüllen die vielfältigen Anforderungen verschiedener Branchen.