LD (7Cr7Mo2V2Si) Kaltarbeitsstahl
LD (7Cr7Mo2V2Si) ist ein hochwertiges und robustes Material für Kaltscherenklingen, das ursprünglich für Kaltstauchwerkzeuge entwickelt wurde. Sein Code „Kaltstauchwerkzeug“ spiegelt seine Verwendung wider.
In der tatsächlichen Produktion wird LD-Stahl zur Herstellung von Kaltstauch-, Kaltfließpress- und Kaltformwerkzeugen verwendet, die eine hohe Zähigkeit erfordern. Bei Scherklingen weist er eine bessere Leistung als Cr12 und W6Mo5Cr4V2 auf.
LD-Stahl ist ein Matrix-Codeformstahl, der sich durch hohe Festigkeit und Verschleißfestigkeit, hohe Biegefestigkeit, hervorragende Kalt- und Warmverarbeitungstechnologie, minimale Wärmebehandlungsverzerrung und Vielseitigkeit auszeichnet.
Dank seiner überlegenen Festigkeit und Zähigkeit, seiner guten Verschleißfestigkeit und der Möglichkeit, daraus eine Reihe von Kaltschneidescherenklingen herzustellen, weist LD-Stahl eine mehr als zehnmal längere Lebensdauer als andere Materialien wie Cr12MoV, W18Cr4V, W6Mo5Cr4V2, Cr12, GCr15 und 9SiCr auf.
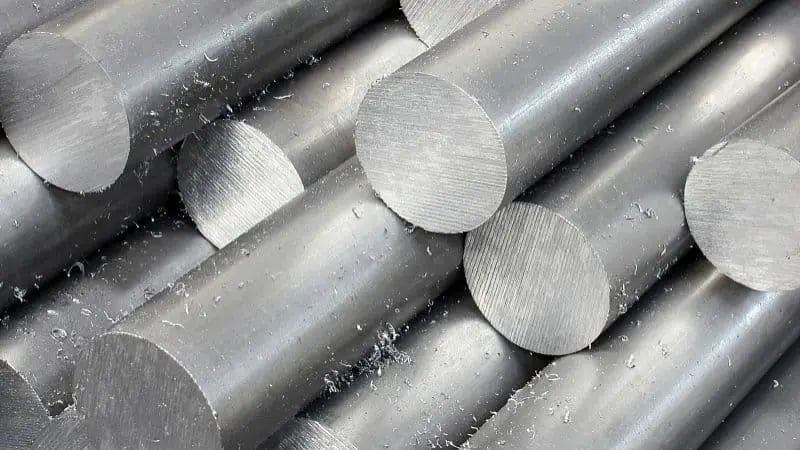
Mechanische Eigenschaften:
- Klingenhärte: HR57 ~ 63
Wärmebehandlungsspezifikationen:
- Abschrecktemperatur 1100 ~ 1150 ℃, Anlasstemperatur 530 ~ 540 ℃
H13 (4Cr5MoSiV1) Warmarbeitsstahl für Scherklingen
Funktionen und Anwendung:
H13-Stahl (4Cr5MoSiV1) ist ein hochwertiger, lufthärtender Matrizenstahl mit ausgezeichneter Zähigkeit und Beständigkeit gegen Heiß- und Kaltermüdung. Er ist nicht anfällig für thermische Ermüdungsrisse, hat starke Antihafteigenschaften und erfährt nur minimale Wechselwirkung mit geschmolzenem Metall, weshalb er häufig bei der Herstellung von Klingen für Heißstauch-, Heißextrusions- und thermische Schermaschinen verwendet wird.
In puncto Leistung ist H13-Stahl dem 4Cr5MoSiV-Stahl ähnlich, sein hoher Vanadiumgehalt verleiht ihm jedoch im Vergleich zu 4Cr5MoSiV-Stahl eine bessere Temperaturleistung (bis zu 600 Grad).
Es handelt sich um einen repräsentativen Stahl für die Verwendung in Warmarbeitsgesenken und er eignet sich zum Warmscheren von Stahlplatten bei Temperaturen unter 800 °C.
Mechanische Eigenschaften:
- Klingenhärte: HR56 ~ 58
Wärmebehandlungsspezifikation:
- Abschrecktemperatur 1050 ~ 1080 ℃, Anlasstemperatur 530 ~ 560 ℃
6CrW2Si Legierter Werkzeugstahl
Funktionen und Anwendung:
6CrW2Si ist ein hochwertiger legierter Werkzeugstahl, der durch Zugabe einer bestimmten Menge Wolfram zu Chrom-Silizium-Stahl hergestellt wird. Die Zugabe von Wolfram führt beim Abschrecken zu feineren Körnern, was zu einer erhöhten Zähigkeit unter Anlassbedingungen führt.
Im Vergleich zu 4CrW2Si-Stahl und 5CrW2Si-Stahl weist 6CrW2Si-Stahl eine höhere Abschreckhärte und eine verbesserte Hochtemperaturfestigkeit auf. Diese Stahlsorte wird häufig zur Herstellung von hydraulischen Scherklingen verwendet, die Stoßbelastungen standhalten müssen und eine hohe Verschleißfestigkeit erfordern. Sie kann zum Scheren von gewöhnlichem Stahl und Edelstahlplatten mit harter Textur verwendet werden.
Mechanische Eigenschaften:
- Klingenhärte: HRC56 ~ 60
Wärmebehandlungsspezifikation:
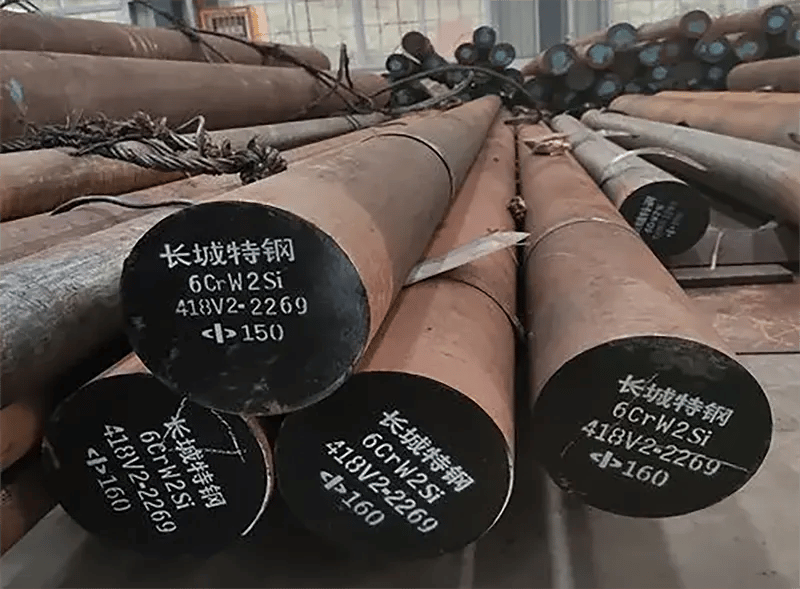
- Abschrecktemperatur 860 ~ 900 ℃, Anlasstemperatur 285 ~ 229 ℃
W6Mo5Cr4V2 Schnellarbeitsstahl
Funktionen und Anwendung:
W6Mo5Cr4V2 ist ein hochwertiger Schnellarbeitsstahl, auch bekannt als 6542, allgemein als „Schnellarbeitsstahl“ bezeichnet. Es handelt sich um einen kohlenstoffreichen, hochlegierten Werkzeugstahl, der für das Hochgeschwindigkeitsschneiden entwickelt wurde.
Die Wolfram-Molybdän-Reihe ist eine Darstellung von Schnellarbeitsstahl mit hoher Härte, Verschleißfestigkeit und thermischer Härte (auch als Rothärte bekannt). Bei Temperaturen bis zu 500 bis 600 Grad Celsius wird der SchneidwerkzeugDie Härte nimmt nicht signifikant ab.
Im Vergleich zu W18Cr4V hat W6Mo5Cr4V2 eine ähnliche Härte bei hohen Temperaturen, ist jedoch anfälliger für Oxidation und Entkohlung, daher sollte es bei der Wärmeverarbeitung und Wärmebehandlung vorsichtig behandelt werden.
Dieser Stahl kann mit höheren Geschwindigkeiten geschnitten werden als niedrig legierter Schneidwerkzeugstahl, was ihn ideal für Klingen macht, die hohe Schnittgeschwindigkeiten, schwere Lasten und hohe Arbeitstemperaturen erfordern. Er eignet sich zum Blechschneiden unter verschiedenen Bedingungen.
Mechanische Eigenschaften:
- Klingenhärte: HR62 ~ 68
Wärmebehandlungsspezifikationen:
- Abschrecktemperatur 1210 ~ 1230, Anlasstemperatur 540 ~ 560
Cr12MoV Matrizenstahl
Funktionen und Anwendung:
Cr12MoV ist ein hochwertiger Formenstahl, der eine höhere Härtbarkeit, Härte nach dem Abschrecken und Anlassen, Festigkeit und Zähigkeit als CR12 aufweist. Er kann bei Durchmessern unter 300 bis 400 mm vollständig aushärten, wobei die Verformung durch das Abschrecken minimal ist. Allerdings weist er eine schlechte Hochtemperaturplastizität auf.
Cr12MoV wird hauptsächlich zur Herstellung von Hydraulikscherenklingen mit größeren Querschnitten, komplexen Formen und hohen Arbeitslasten verwendet. Die Klinge aus Cr12MoV kann über 800.000 Mal zum Schneiden verwendet werden und eignet sich zum Schneiden von Platten mit hoher Härte wie Edelstahl und Siliziumstahlblechen.
Mechanische Eigenschaften:
- Klingenhärte: HRC56 ~ 60
Wärmebehandlungsspezifikationen:
- Abschrecktemperatur von 950 ℃ bis 1000 ℃, Anlasstemperatur von 200 ℃ bis 250 ℃
9CrSi-legierter Werkzeugstahl
Funktionen und Anwendung:
9CrSi ist ein hochwertiger, niedriglegierter Schneidstahl für langsame Schnittgeschwindigkeiten, der für seine Sprödigkeit und Härte sowie seine Tendenz zur Wärmeempfindlichkeit bekannt ist, die zu einer Verhärtung der Oberfläche und einem höheren Risiko der Rissbildung führt.
Es handelt sich um einen häufig in Mess- und Schneidwerkzeugen verwendeten niedriglegierten Werkzeugstahl, der sich durch eine hohe Abschreck- und Härtbarkeit sowie Stabilität beim Anlassen auszeichnet.
Aus 9CrSi können hydraulische Scherenklingen mit komplexer Form, minimaler Verformung, hoher Verschleißfestigkeit und niedriger Schneidgeschwindigkeit hergestellt werden.
Es ist ideal zum Schneiden gewöhnlicher A3- und Q235-Platten.
Mechanische Eigenschaften:
- Klingenhärte: HRC55 ~ 58
Wärmebehandlungsspezifikationen:
- Abschrecktemperatur 820 ~ 860 ℃, Anlasstemperatur 180 ~ 200 ℃
T10A Kohlenstoff-Werkzeugstahl
Funktionen und Anwendung:
T10A ist ein hochwertiger Kohlenstoff-Baustahl mit hoher Festigkeit und Verschleißfestigkeit, aber geringer Warmhärte, Abschreck- und Härtbarkeit sowie hoher Abschreckverformung. Er eignet sich für die Herstellung von Scherklingen unter schlechten Schnittbedingungen mit hohen Anforderungen an die Verschleißfestigkeit und ohne plötzliche und starke Vibrationen, wobei ein gewisses Maß an Zähigkeit und eine scharfe Messerschneide erforderlich sind. Er wird zum Schneiden von gewöhnlichen A3-Platten verwendet.
Mechanische Eigenschaften:
- Klingenhärte: HRC52 ~ 55
Wärmebehandlungsspezifikationen:
- Abschrecktemperatur 770 Grad, Anlasstemperatur 200 Grad
8. 45# Stahl Kohlenstoff Baustahl
Funktionen und Anwendung:
45# ist ein hochwertiger Kohlenstoff-Baustahl, der häufig im Maschinenbau verwendet wird. Er verfügt über gute Schneideigenschaften und mechanische Eigenschaften.
Als mittelkohlenstoffhaltiger Stahl weist 45# jedoch eine schlechte Abschreckleistung auf und ist nicht für die Herstellung von Klingen für Blechschneidemaschinen geeignet. Seine Wärmebehandlungshärte liegt nur zwischen HRC 42-46, daher besteht der typische Ansatz darin, eine Kombination aus Abschrecken und Anlassen sowie Hochfrequenz-Oberflächenabschrecken zu verwenden. Die Verschleißfestigkeit ist etwas schlechter als beim Aufkohlen, wodurch er zum Schneiden nichtmetallischer Bleche geeignet ist.
Mechanische Eigenschaften:
- Klingenhärte: HRC42 ~ 56
Wärmebehandlungsspezifikationen:
- Abschrecktemperatur 840 Grad, Anlasstemperatur 300 Grad