Hydraulische Abkantpressen sind unverzichtbare Maschinen in der Blechbearbeitung, bekannt für ihre Fähigkeit, Bleche mit hoher Präzision und Effizienz zu biegen. Dieser umfassende Leitfaden befasst sich mit den verschiedenen Arten von hydraulische Abkantpressen, die entscheidenden Formen, die die Form und den Winkel der Werkstücke bestimmen, und die fortschrittlichen Sicherheitssysteme, die die Sicherheit von Bediener und Ausrüstung gewährleisten. Darüber hinaus untersuchen wir optionale Funktionen, die die Funktionalität hydraulischer Abkantpressen verbessern und sie an unterschiedliche Produktionsanforderungen anpassbar machen. Egal, ob Sie in der Großserienfertigung tätig sind oder hochpräzises Biegen benötigen, das Verständnis dieser Aspekte wird Ihnen dabei helfen, die richtige hydraulische Abkantpresse für Ihren Betrieb auszuwählen und zu verwenden.
Inhaltsverzeichnis
Was ist eine hydraulische Abkantpresse?
Der hydraulische Abkantpresse ist eine Maschine, die ein hydraulisches Übertragungssystem verwendet, um Metallbleche in verschiedene Formen zu biegen. Sie wird häufig in der Blechverarbeitungsindustrie eingesetzt. Die Hauptkomponenten einer hydraulischen Abkantpresse sind Rahmen, Werkbank, Stößel, Hydrauliksystem, elektrisches Steuersystem und Werkzeuge. Durch die Steuerung der Auf- und Abbewegung des Stößels biegt die Maschine Metallbleche in die gewünschte Form und den gewünschten Winkel.
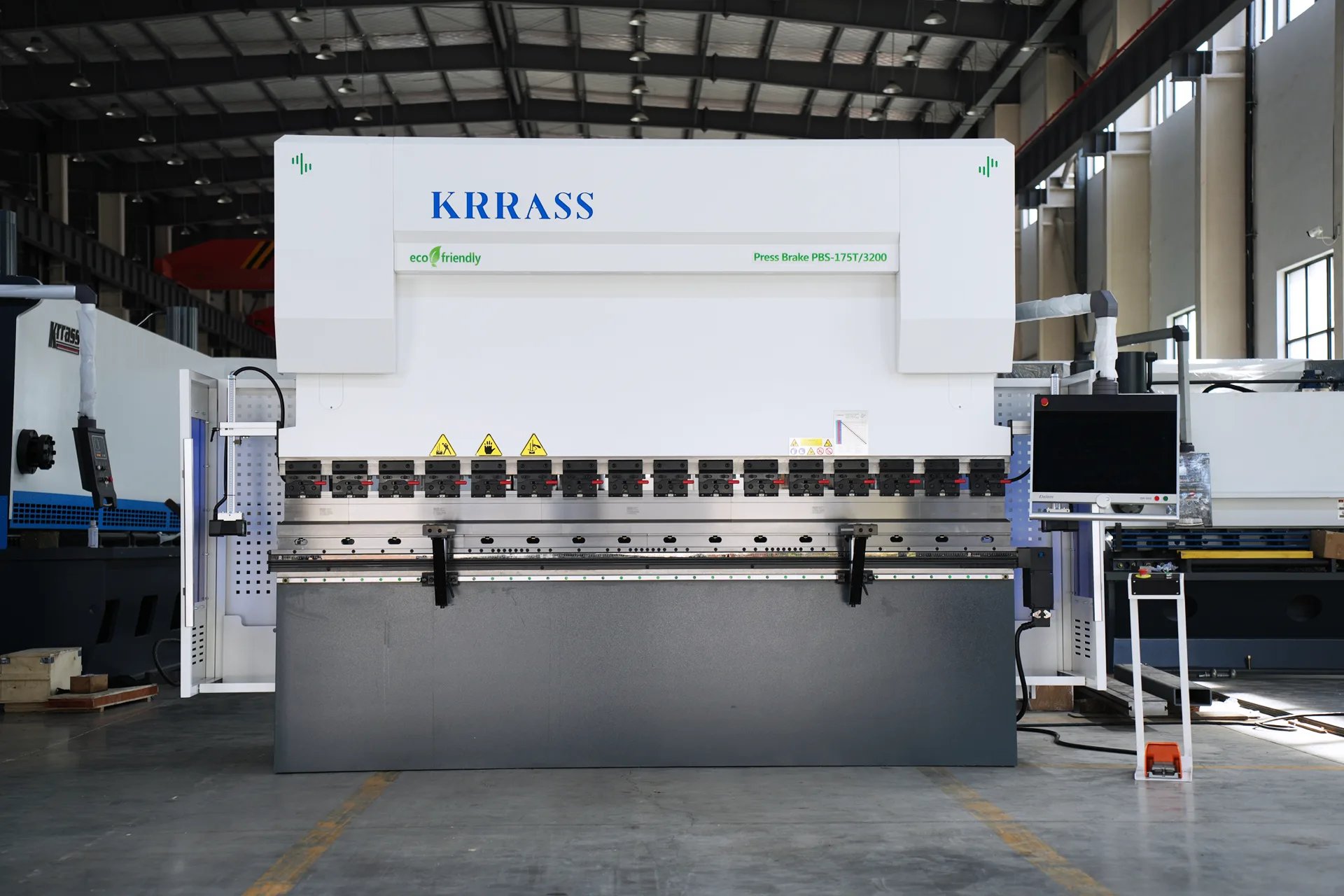
Arten von Abkantpressen
Hydraulische Abkantpressen werden anhand ihrer Steuerungssysteme und strukturellen Eigenschaften hauptsächlich in zwei Typen eingeteilt: Torsionsstab-Abkantpressen und elektrohydraulische Abkantpressen.
Torsionsstab-Abkantpressen
Die Torsionsstabbiegemaschine verwendet Torsionsstäbe, um die linken und rechten Schwingstangen zu verbinden und so einen Torsionsstab-Zwangssynchronisationsmechanismus zu bilden, der die Ölzylinder auf beiden Seiten auf und ab bewegt. Daher ist die Torsionsstabbiegemaschine ein mechanischer Zwangssynchronisationsmodus, und die Parallelität der Gleitblöcke kann nicht automatisch überprüft und eingestellt werden. Normalerweise wird die Torsionsachsenbiegemaschine auch genannt NC-Abkantpresse.
Vorteile:
- Einfache Struktur: Drehstab-Abkantpressen haben einen relativ einfachen Aufbau und sind daher leicht zu warten.
- Niedrigere Kosten: Sie sind im Vergleich zu elektrohydraulischen Abkantpressen kostengünstiger in der Herstellung und Wartung und eignen sich daher auch für kleine und mittlere Unternehmen.
- Benutzerfreundlichkeit: Diese Maschinen sind einfach zu bedienen und ideal für die Blechbearbeitung großer Stückzahlen und geringer Präzision.
Nachteile:
- Geringere Präzision: Aufgrund der mechanischen Torsionssynchronisierung ist das Erreichen einer hochpräzisen Synchronisationssteuerung eine Herausforderung.
- Eingeschränkte Flexibilität: Sie können komplexe Kurven und mehrstufige Biegeprozesse nicht automatisieren.
- Funktionale Einschränkungen: Nicht für komplexe Anforderungen in der Blechbearbeitung geeignet.
Elektrohydraulische Abkantpressen
Die elektrohydraulische Abkantpresse ist mit einem Gitterlineal auf dem Schieber oder dem Bett ausgestattet, und das numerische Steuerungssystem kann die Synchronisierung auf beiden Seiten des Schiebers jederzeit anhand der vom Gitterlineal zurückgemeldeten Informationen analysieren. Wenn ein Fehler auftritt, passt das numerische Steuerungssystem den Hub auf beiden Seiten des Schiebers über das proportionale hydraulische Servoventil an. Das numerische Steuerungssystem, der hydraulische Steuerventilsatz und das Gitterlineal bilden die Rückkopplungs-Regelung der elektrohydraulischen Abkantpresse. Normalerweise wird eine elektrohydraulische Biegemaschine auch genannt CNC-Abkantpresse.
Vorteile:
- Hohe Präzision: Elektrohydraulische Servosteuerungssysteme sorgen für eine hochpräzise Synchronisationssteuerung.
- Größere Flexibilität: Geeignet für die hochpräzise und komplexe Blechbearbeitung, geeignet für die Handhabung komplexer Kurven und mehrstufiger Biegeprozesse.
- Hohe Automatisierung: Kann eine vollständige Automatisierung erreichen, wodurch manuelle Eingriffe reduziert und die Produktionseffizienz erhöht werden.
Nachteile:
- Höhere Kosten: Höhere Herstellungs- und Wartungskosten, geeignet für große Unternehmen oder High-End-Marktanforderungen.
- Komplexe Operation: Erfordert professionelle Techniker für Betrieb und Wartung.
Steuerungen für Abkantpressen
Der Controller ist eine entscheidende Komponente einer Abkantpresse und ist für die Steuerung ihrer Bewegung und ihres Betriebs verantwortlich. Basierend auf der Steuerungsmethode können Abkantpressen-Controller in die folgenden Typen eingeteilt werden:
Mechanische Steuerungen: Mechanische Steuerungen sind traditionelle Abkantpressensteuerungen, die für ihre einfache Struktur und niedrigen Kosten bekannt sind, aber in Bezug auf Steuerungspräzision und Funktionalität eingeschränkt sind. Sie bestehen normalerweise aus Zahnrädern, Nocken und Gestängen und steuern die Bewegung der Abkantpresse durch mechanische Übertragung. Der Hauptvorteil mechanischer Steuerungen ist ihre Einfachheit und Wartungsfreundlichkeit, ihre Hauptnachteile sind jedoch eine geringe Steuerungspräzision, geringe Effizienz und die Unfähigkeit, komplexe Biegeprozesse zu handhaben.
Numerische Steuerung (NC): NC-Steuerungen werden häufig in modernen Abkantpressen verwendet und nutzen elektronische Komponenten und Computertechnologie, um die Bewegung der Maschine zu steuern. Sie bieten hohe Steuerungspräzision, umfassende Funktionen und einfache Bedienung. NC-Steuerungen umfassen Komponenten wie Zentralprozessoren, Speicher und Eingabe-/Ausgabegeräte, sodass voreingestellte Programme die Bewegungen der Abkantpresse steuern und verschiedene komplexe Biegeprozesse ermöglichen.
CNC-Steuerungen: CNC-Steuerungen sind eine erweiterte Version von NC-Steuerungen und bieten noch höhere Steuerungspräzision und leistungsfähigere Funktionen. CNC-Steuerungen bestehen in der Regel aus Industriecomputern, Servoantrieben und Mensch-Maschine-Schnittstellen und ermöglichen komplexere Biegeprozesse und eine höhere Produktionseffizienz.
Wie wählt man einen Abkantpressen-Controller aus?
Berücksichtigen Sie bei der Auswahl einer Abkantpressensteuerung die folgenden Faktoren:
- Kontrollpräzision: Je höher die Regelpräzision, desto maßhaltiger sind die Biegeteile.
- Funktionalität: Die Steuerung sollte in der Lage sein, die Bewegung der Abkantpresse zu steuern, Biegegeschwindigkeit und Druck anzupassen sowie Biegeprogramme einzustellen. Umfassendere Funktionen bedeuten, dass die Abkantpresse den Bedürfnissen der Benutzer besser gerecht wird.
- Benutzerfreundlichkeit: Die Steuerung sollte leicht zu bedienen sein, sodass auch Laienarbeiter den Umgang damit schnell erlernen können.
- Preis: Die Preise der Controller variieren erheblich, und Benutzer sollten ihre Wahl auf Grundlage ihres Budgets treffen.
Gängige Marken für Abkantpressensteuerungen
- Estún
- Delem
Überblick zu Estun Controllers
Estun ist ein bekannter Hersteller von numerischen Steuerungen und bietet eine Reihe von Steuerungen für Abkantpressen an. Hier ist eine kurze Einführung in zwei beliebte Modelle, E21 und E310P:
E21 Controller
Der E21 ist ein einfacher NC-Controller für Benutzer, die eine einfache und kostengünstige Lösung benötigen. Er bietet:
- 2-Achsen-Steuerung (X und Y)
- Hinteranschlagsteuerung
- Programmierfunktionen (Einzelschritt, Automatik, etc.)
- Fehlerdiagnose
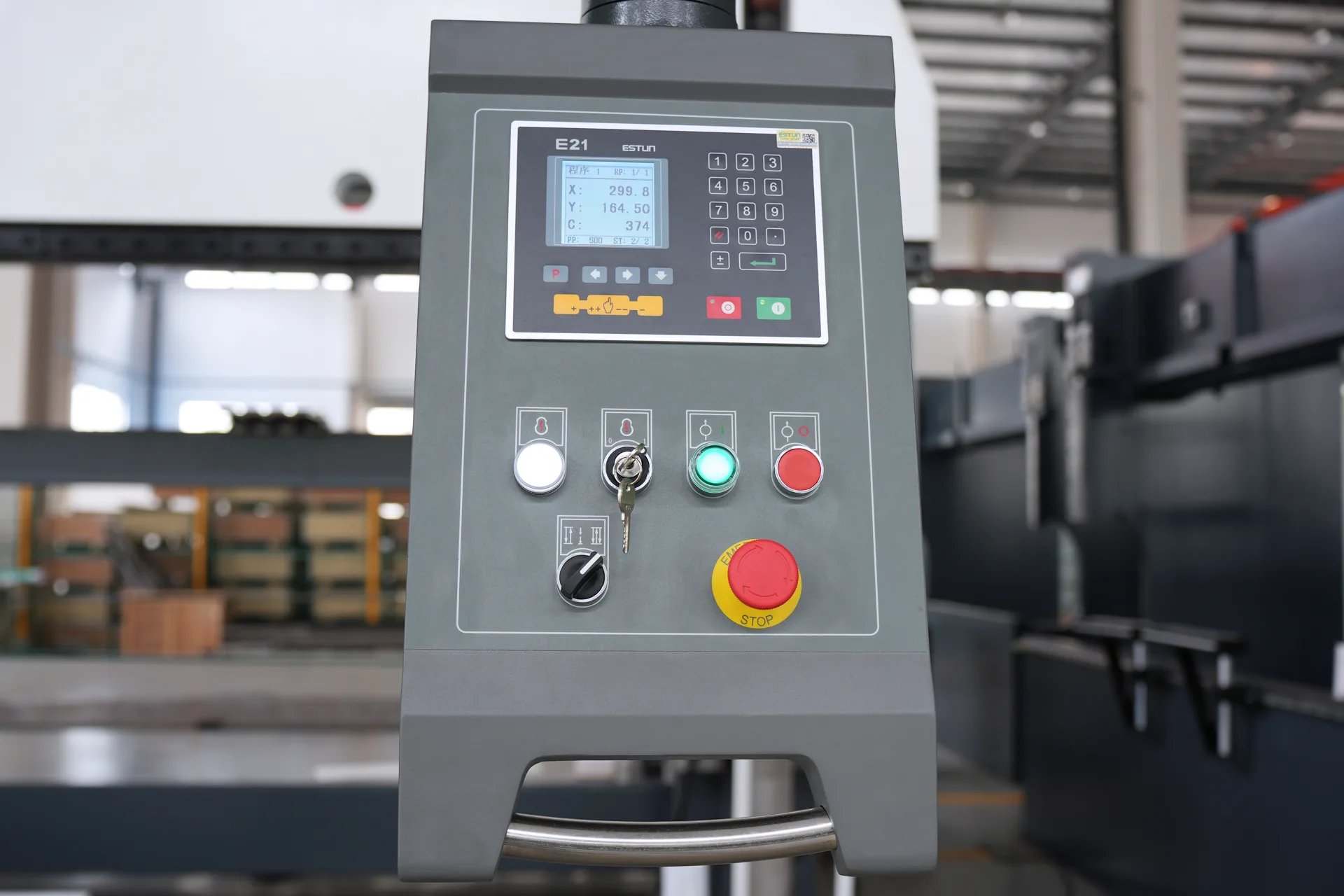
E310P Controller
Der E310P ist ein fortschrittlicherer NC-Controller mit größerer Funktionalität und Flexibilität, der für Benutzer geeignet ist, die mehr Kontrolle und Vielseitigkeit benötigen. Er bietet:
- 3-Achsen-Steuerung (X, Y und R)
- Hinteranschlagsteuerung
- Programmierfunktionen (Einzelschritt, Automatik, etc.)
- Sequenzprogrammierung
- Werkzeugbibliothek
- Fehlerdiagnose
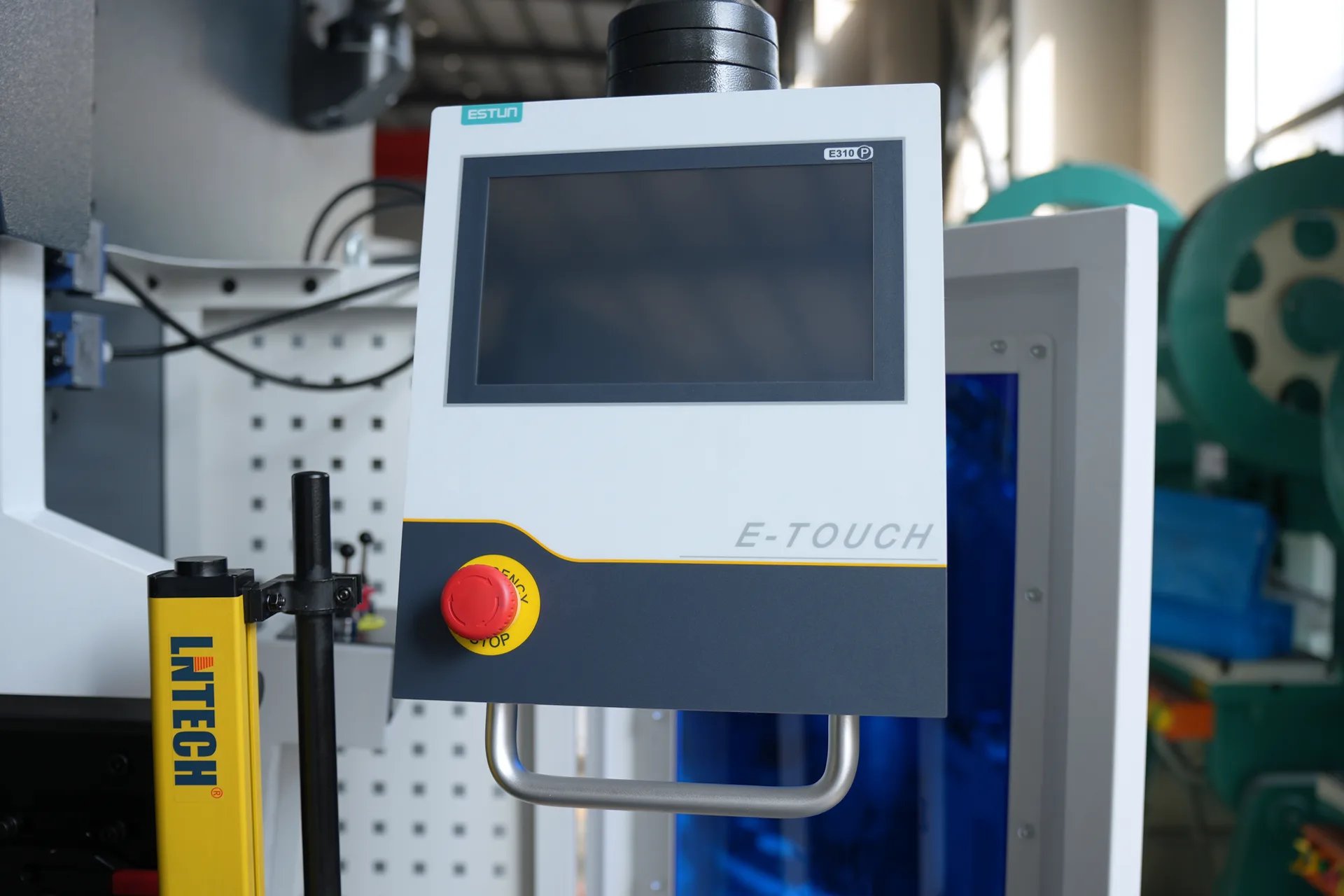
Überblick zu Delem Controllers
Delem ist ein weltweit anerkannter Hersteller von numerischen Steuerungssystemen und bietet Steuerungslösungen für verschiedene Arten von Metallverarbeitungsmaschinen, einschließlich Abkantpressen. Delem-Steuerungen sind für ihre hohe Präzision, Zuverlässigkeit und Benutzerfreundlichkeit bekannt und werden häufig in Branchen wie der Luft- und Raumfahrt, der Automobilindustrie, dem Schiffbau und der Haushaltsgeräteindustrie eingesetzt.
Dies sind die wichtigsten Delem-Abkantpressensteuerungen:
DA-41T
Die DA-41T-Steuerung bietet eine benutzerfreundliche und vielseitige Touch-Steuerungslösung für herkömmliche Abkantpressenanwendungen mit Unterstützung mehrerer Achsen. Sie bietet:
- Panelbasiertes Gehäuse
- Heller LCD-Bildschirm
- Strahlstoppsteuerung (Y)
- Hinteranschlagsteuerung (X)
- Rückzugsfunktion
- Manuelles Verfahren aller Achsen
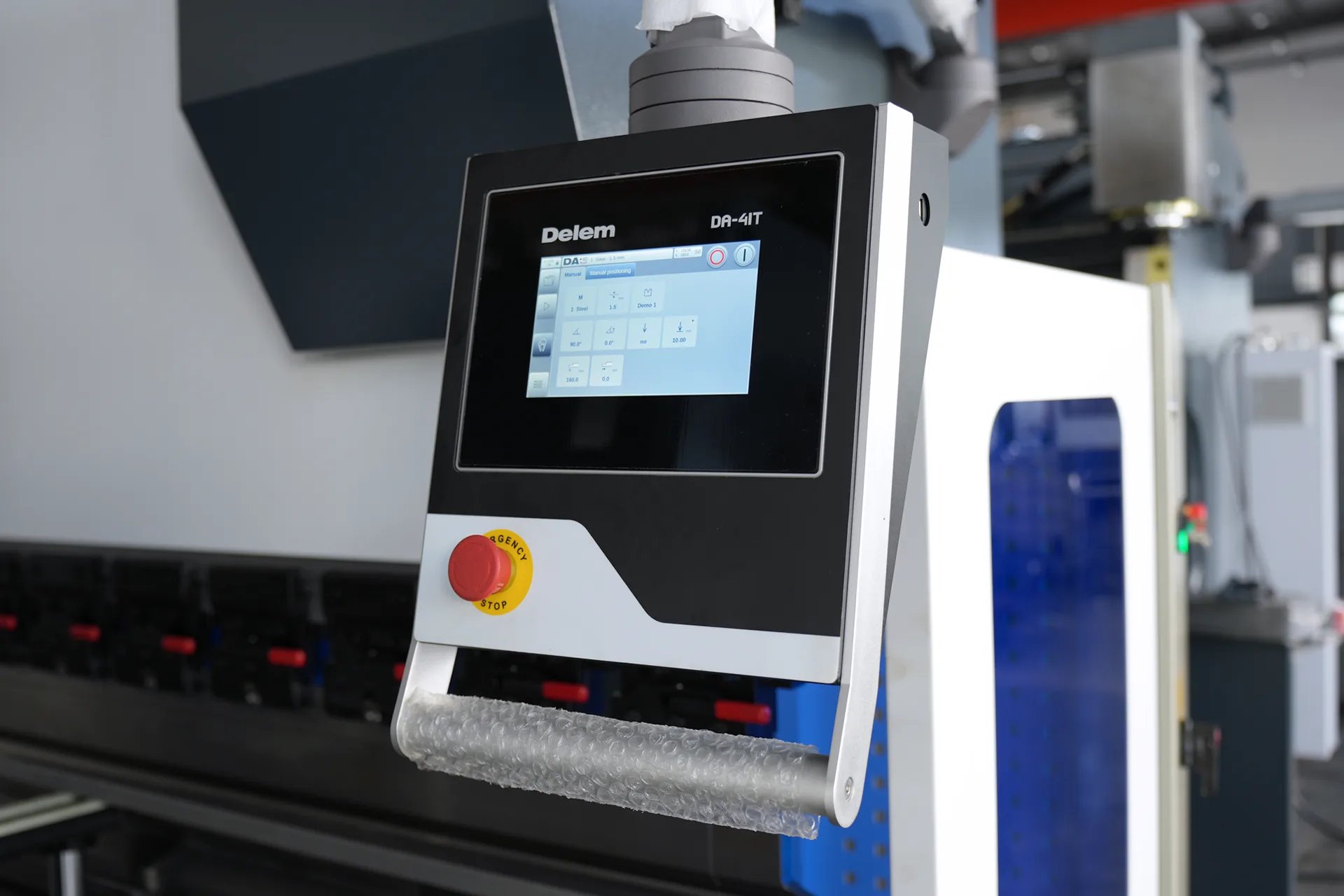
DA-53T
Der kompakte DA-53T bietet eine hochmoderne Komplettlösung zur Touch-Steuerung für synchronisierte Abkantpressen und ermöglicht die einfachste CNC-Programmierung auf Basis der grafischen Delem-Touchscreen-Benutzeroberfläche. Er verfügt über:
- „Hotkey“-Touch-Navigation
- 10,1" hochauflösendes Farb-TFT
- Bis zu 4 Achsen (Y1, Y2 + 2 Hilfsachsen)
- Bombierungskontrolle
- Werkzeug-/Material-/Produktbibliothek
- Servo- und Frequenzumrichtersteuerung
- Erweiterte Y-Achsen-Steuerungsalgorithmen für Ventile mit geschlossenem und offenem Regelkreis
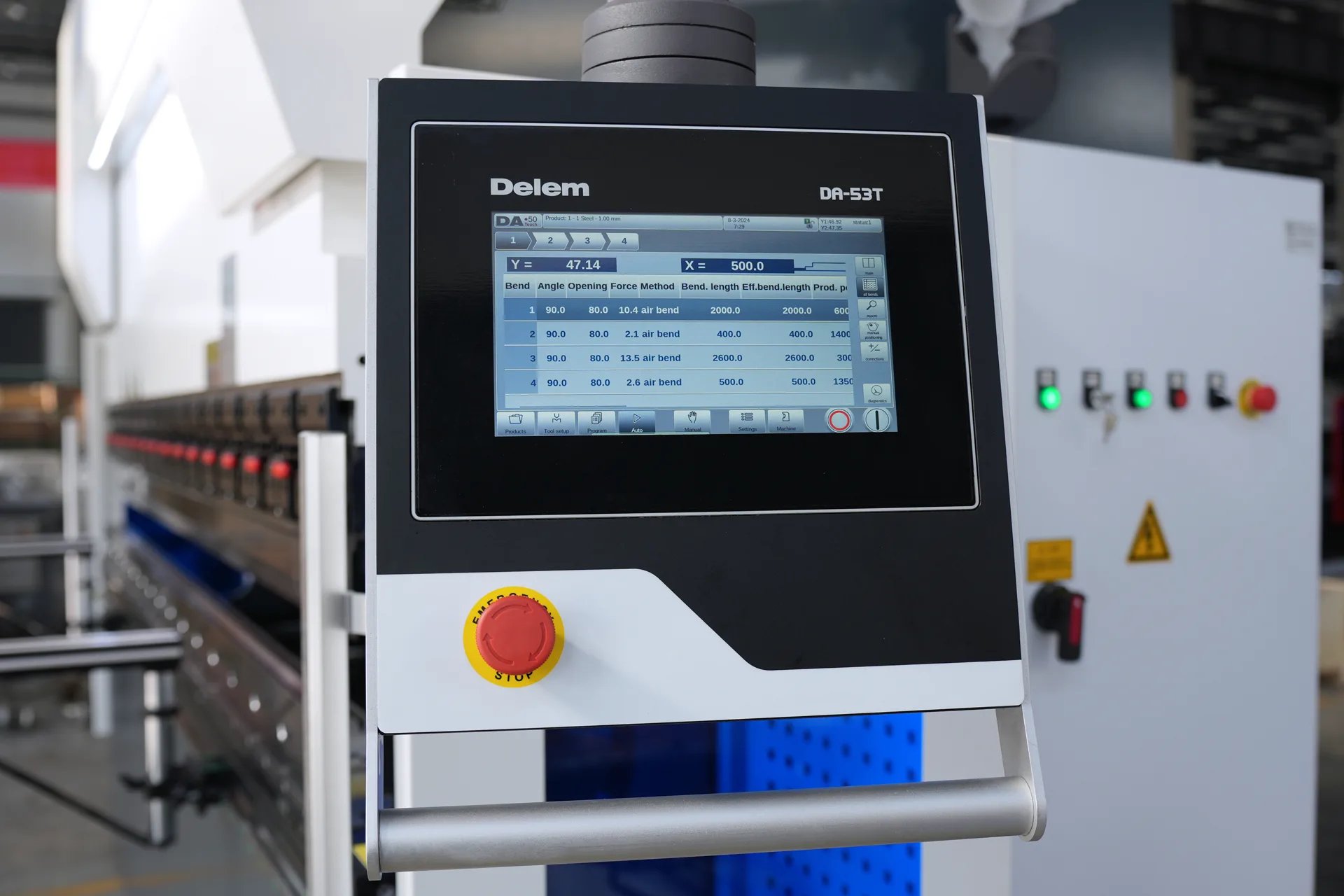
DA-58T
Der DA-58T ist eine hochmoderne, komplette 2D-Grafiksteuerungslösung für synchronisierte Abkantpressen mit automatischer Biegereihenfolgeberechnung und Kollisionserkennung. Er umfasst:
- 2D-grafische Touchscreen-Programmierung
- 15" hochauflösendes Farb-TFT
- Biegefolgeberechnung
- Bombierungskontrolle
- Servo- und Frequenzumrichtersteuerung
- Erweiterte Y-Achsen-Steuerungsalgorithmen für Ventile mit geschlossenem und offenem Regelkreis
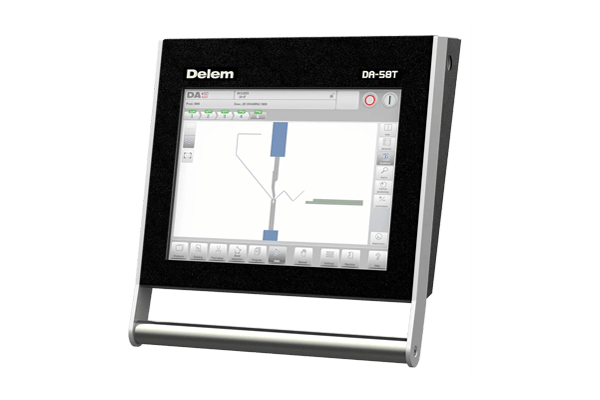
DA-66T
Der DA-66T bietet 2D-Programmierung mit automatischer Biegereihenfolgeberechnung und Kollisionserkennung, wobei die vollständige 3D-Maschineneinrichtung echtes Feedback zur Machbarkeit und Handhabung des Produkts liefert. Er umfasst:
- Programmiermodus mit grafischem 2D-Touchscreen
- 17" hochauflösendes Farb-TFT
- Vollständige Windows-Anwendungssuite
- Kompatibilität mit Delem Modusys (Skalierbarkeit und Adaptivität des Moduls)
- USB, Peripherieschnittstelle
- Benutzerspezifische Anwendungsunterstützung innerhalb der Multitaskingumgebung der Steuerung
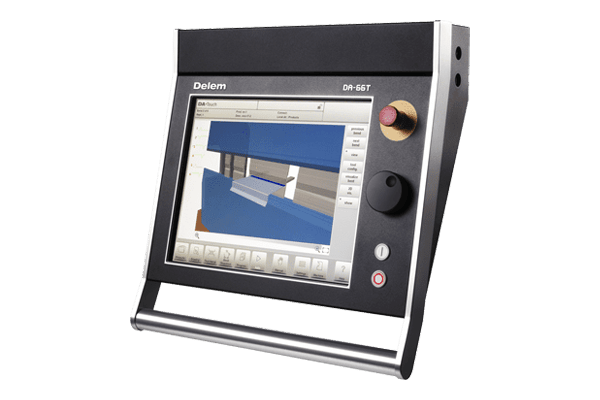
DA-69T
Der DA-69T bietet sowohl 2D- als auch 3D-Programmierung, einschließlich automatischer Biegereihenfolgeberechnung und Kollisionserkennung. Er bietet eine vollständige 3D-Maschineneinrichtung mit mehreren Werkzeugstationen. Er verfügt über:
- 3D- und 2D-Grafik-Touchscreen-Programmiermodus
- 3D-Visualisierung in Simulation und Produktion
- 17" hochauflösendes Farb-TFT
- Vollständige Windows-Anwendungssuite
- Kompatibilität mit Delem Modusys (Skalierbarkeit und Adaptivität des Moduls)
- USB, Peripherieschnittstelle
- Benutzerspezifische Anwendungsunterstützung innerhalb der Multitaskingumgebung der Steuerung
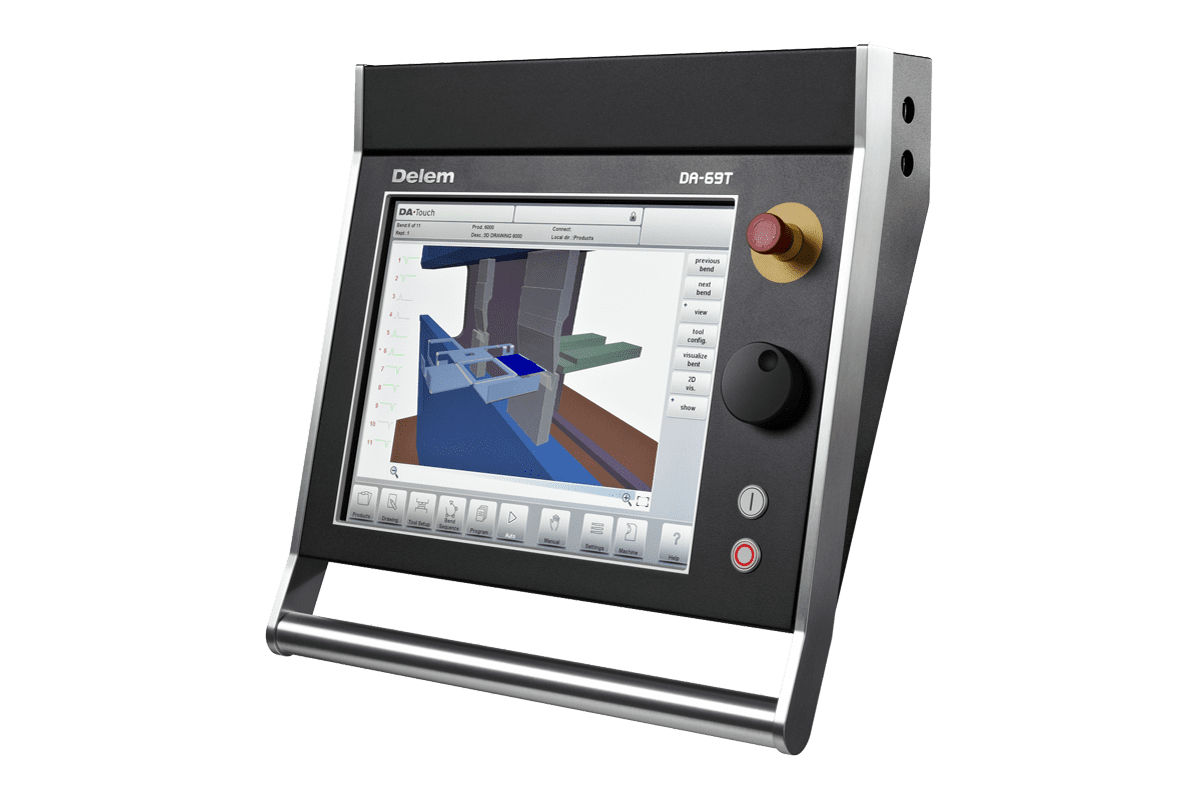
DA-66S
Der DA-66S kombiniert grundlegende Abkantpressen-Steuerungsfunktionen mit den neuesten Verbesserungen zur Steigerung der Produktivität. Er umfasst:
- Programmiermodus mit grafischem 2D-Touchscreen
- 3D-Maschinendarstellung in Simulation und Produktion
- 24" hochauflösendes Farb-TFT
- Kompatibilität mit Delem Modusys (Skalierbarkeit und Adaptivität des Moduls)
- USB, Peripherieschnittstelle
- Benutzerspezifische Anwendungsunterstützung innerhalb der Multitaskingumgebung der Steuerung
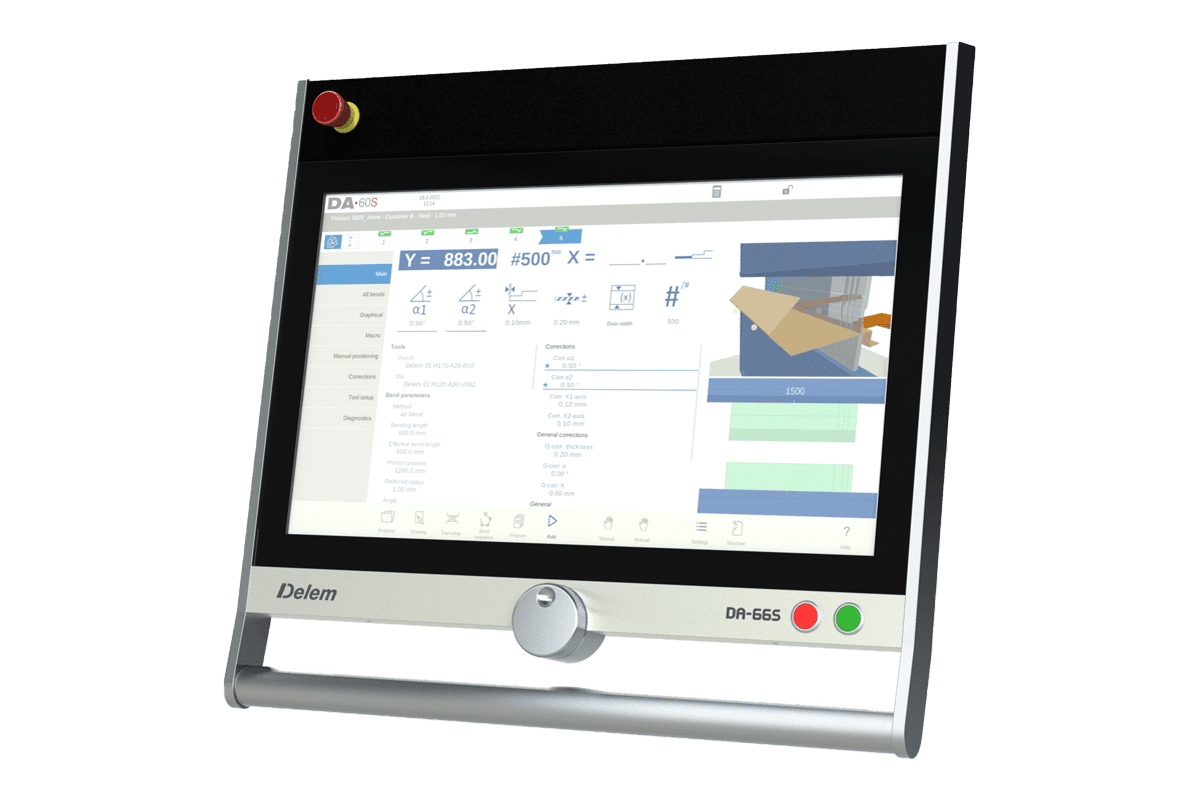
DA-69S
Das Flaggschiff der DA-69S-Steuerung kombiniert grundlegende Abkantpressen-Steuerungsfunktionen mit den neuesten Verbesserungen zur Steigerung der Produktivität. Es umfasst:
- 3D- und 2D-Grafik-Touchscreen-Programmiermodus
- 3D-Visualisierung, einschließlich 3D-Maschinendarstellung in Simulation und Produktion
- 24" hochauflösendes Farb-TFT
- Kompatibilität mit Delem Modusys (Skalierbarkeit und Adaptivität des Moduls)
- USB, Peripherieschnittstelle
- Benutzerspezifische Anwendungsunterstützung innerhalb der Multitaskingumgebung der Steuerung
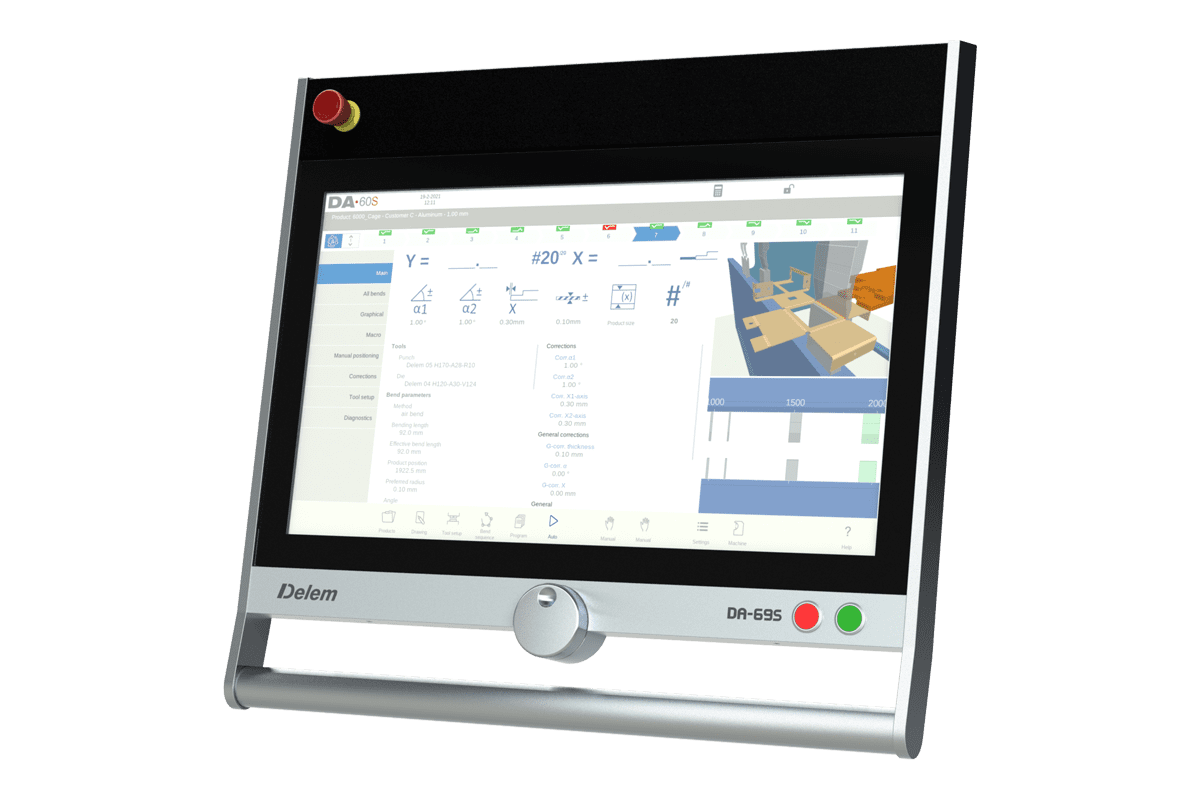
Berücksichtigen Sie bei der Auswahl einer Delem-Abkantpressensteuerung die folgenden Faktoren:
- Der Typ und die Größe Ihrer Abkantpresse
- Ihr Budget
- Die Funktionalitäten, die Sie brauchen
Delem bietet eine Reihe von Controllern an, die Ihren Anforderungen gerecht werden. Weitere Informationen finden Sie auf der Delem-Website: Delem.
Der Hauptmotor der hydraulischen Abkantpresse
Der Hauptmotor eines hydraulische Abkantpresse ist eine entscheidende Komponente des Hydrauliksystems und versorgt die Hydraulikpumpe mit Strom. In hydraulischen Abkantpressen werden hauptsächlich zwei Arten von Hauptmotoren verwendet: konventionelle Motoren und Servomotoren.
Konventionelle Motoren
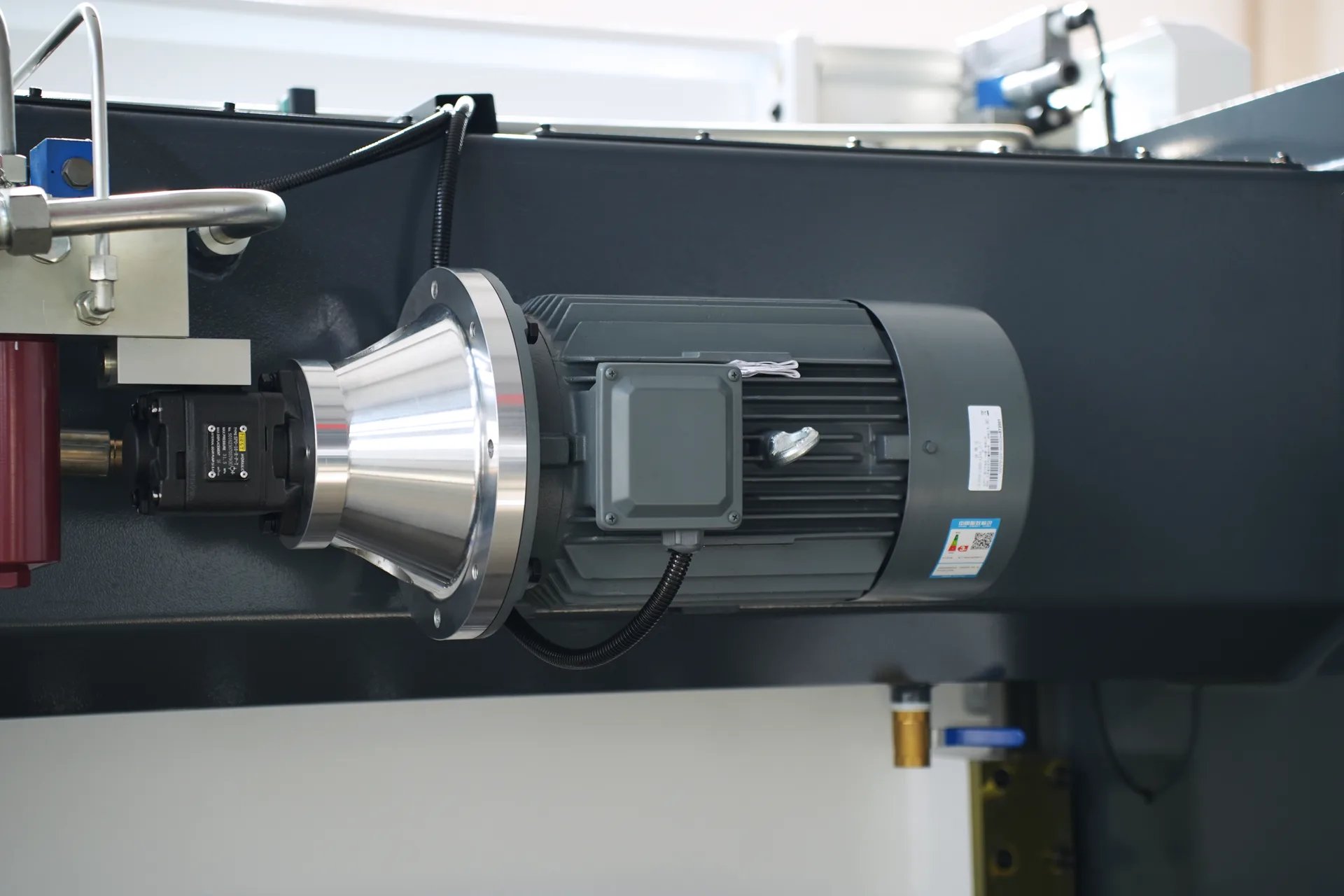
Vorteile:
- Niedrige Kosten: Die Herstellungskosten herkömmlicher Motoren sind geringer und daher für preisbewusste Anwender geeignet.
- Einfache Wartung: Aufgrund ihrer einfachen Struktur sind diese Motoren relativ leicht zu warten und zu reparieren.
- Hohe Zuverlässigkeit: Bewährte Technologie mit geringer Ausfallrate, geeignet für einen langzeitstabilen Betrieb.
Nachteile:
- Geringe Effizienz: Im Vergleich zu Servomotoren weisen herkömmliche Motoren eine geringere Energieeffizienz auf, was zu höheren Betriebskosten führt.
- Geringe Kontrollpräzision: Diese Motoren bieten eine geringere Präzision bei der Drehzahl- und Positionsregelung und sind daher für die hochpräzise Bearbeitung ungeeignet.
- Hohe Startwirkung: Beim Start ziehen sie einen großen Strom und haben dadurch erhebliche Auswirkungen auf das Stromnetz.
Servomotoren
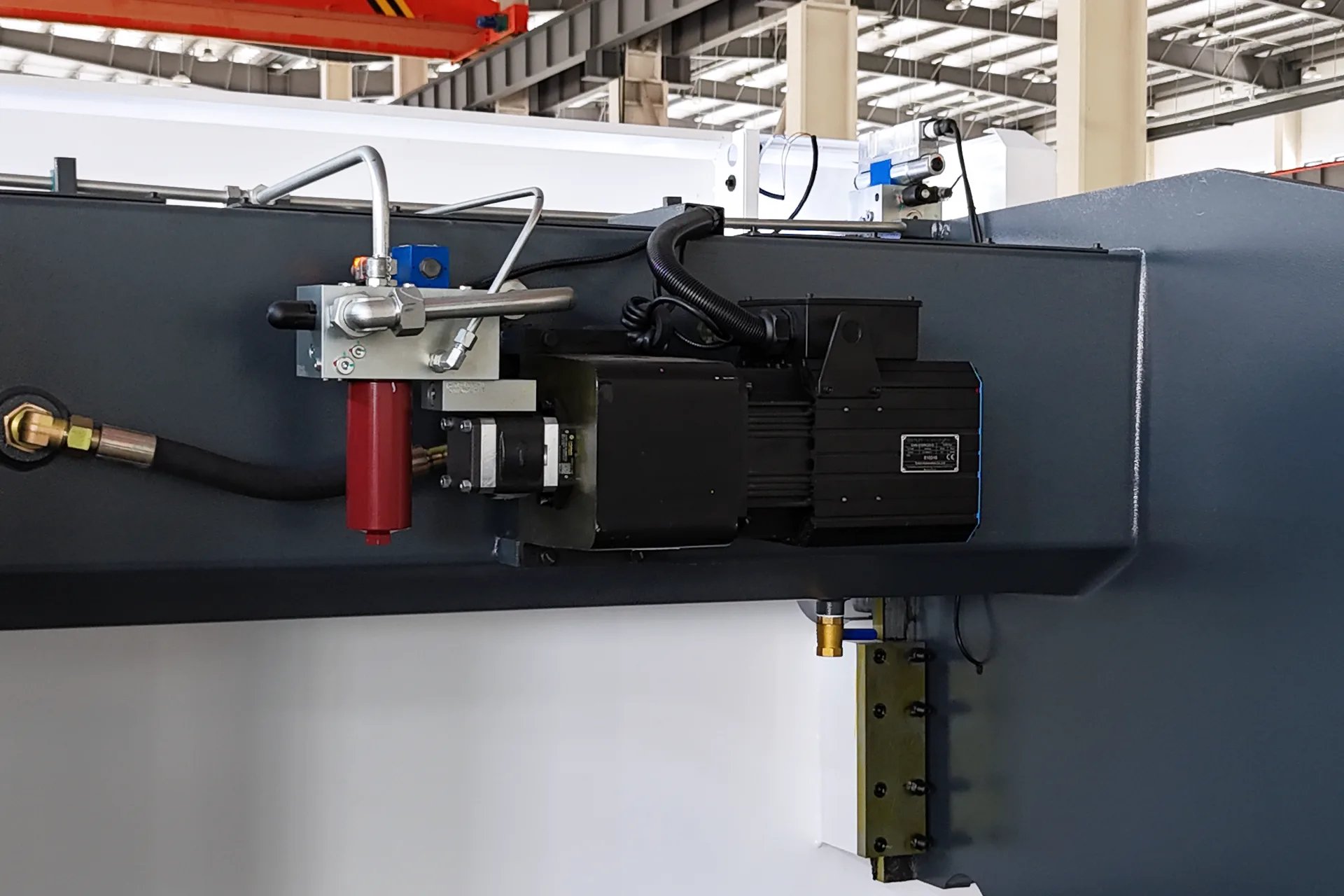
Vorteile:
- Hohe Effizienz: Servomotoren bieten eine höhere Energieeffizienz und senken die Betriebskosten.
- Hochpräzise Steuerung: Ermöglicht eine hochpräzise Geschwindigkeits- und Positionskontrolle, geeignet für hochpräzise Verarbeitung.
- Schnelle Antwort: Sie verfügen über eine schnelle dynamische Reaktionsfähigkeit und werden den Anforderungen komplexer Prozesse gerecht.
- Gute Flexibilität: Geschwindigkeit und Position können entsprechend den Verarbeitungsanforderungen flexibel angepasst werden, wodurch die Produktionseffizienz gesteigert wird.
Nachteile:
- Hohe Kosten: Die Herstellungs- und Wartungskosten von Servomotoren sind höher, sodass eine größere Anfangsinvestition erforderlich ist.
- Komplexe Wartung: Ihre komplexe Struktur erfordert höhere technische und wartungstechnische Fähigkeiten.
- Umgebungsempfindlichkeit: Servomotoren erfordern strenge Umgebungsbedingungen wie Temperatur und Luftfeuchtigkeit und damit eine gute Arbeitsumgebung.
Zusammenfassend lässt sich sagen, dass herkömmliche Motoren für Anwendungen mit begrenztem Budget und geringen Präzisionsanforderungen geeignet sind, während Servomotoren ideal für High-End-Anwendungen sind, die hohe Präzision, Effizienz und flexible Steuerung erfordern. Die Wahl des Motors sollte auf der Grundlage spezifischer Verarbeitungsanforderungen und Budgetbeschränkungen ausgewogen erfolgen.
Mechanischer Bombierungsausgleich in hydraulischen Abkantpressen
Die mechanische Bombierungskompensation ist eine Methode, die bei hydraulischen Abkantpressen verwendet wird, um Verformungen und Fehler zu korrigieren, die durch ungleichmäßige Kräfte während des Biegevorgangs verursacht werden. Sie stellt durch Anpassen der mechanischen Struktur sicher, dass die Werkstücke gleichmäßige Winkel und Formen aufweisen.
Funktionsprinzip
Mechanische Bombierungskompensationssysteme bestehen normalerweise aus einem Satz verstellbarer Keilblöcke oder Keilmechanismen. Diese Keile bewegen sich relativ zueinander, um die Form des Arbeitstisches anzupassen und die durch Biegekräfte verursachte Maschinenverformung auszugleichen. Durch Anpassen der Position der Keile wird beim Biegen eine Gegenverformungskraft ausgeübt, um die während des eigentlichen Betriebs entstehenden Fehler auszugleichen.
Bei der mechanischen Balligkeitskompensation unterscheidet man üblicherweise zwischen manuellen und automatischen Typen, die jeweils ihre eigenen Vor- und Nachteile haben und für unterschiedliche Anwendungen geeignet sind.
Manuelle mechanische Bombierungskompensation
Funktionsprinzip: Die manuelle mechanische Balligkeitskompensation passt die Form des Arbeitstisches durch manuelles Einstellen von Keilen oder anderen mechanischen Komponenten an, um die Verformung während des Biegevorgangs auszugleichen. Die Bediener drehen die Einstellmechanismen je nach Verarbeitungsanforderungen und Erfahrung manuell und bewegen die Keile zur Kompensation in die entsprechenden Positionen.
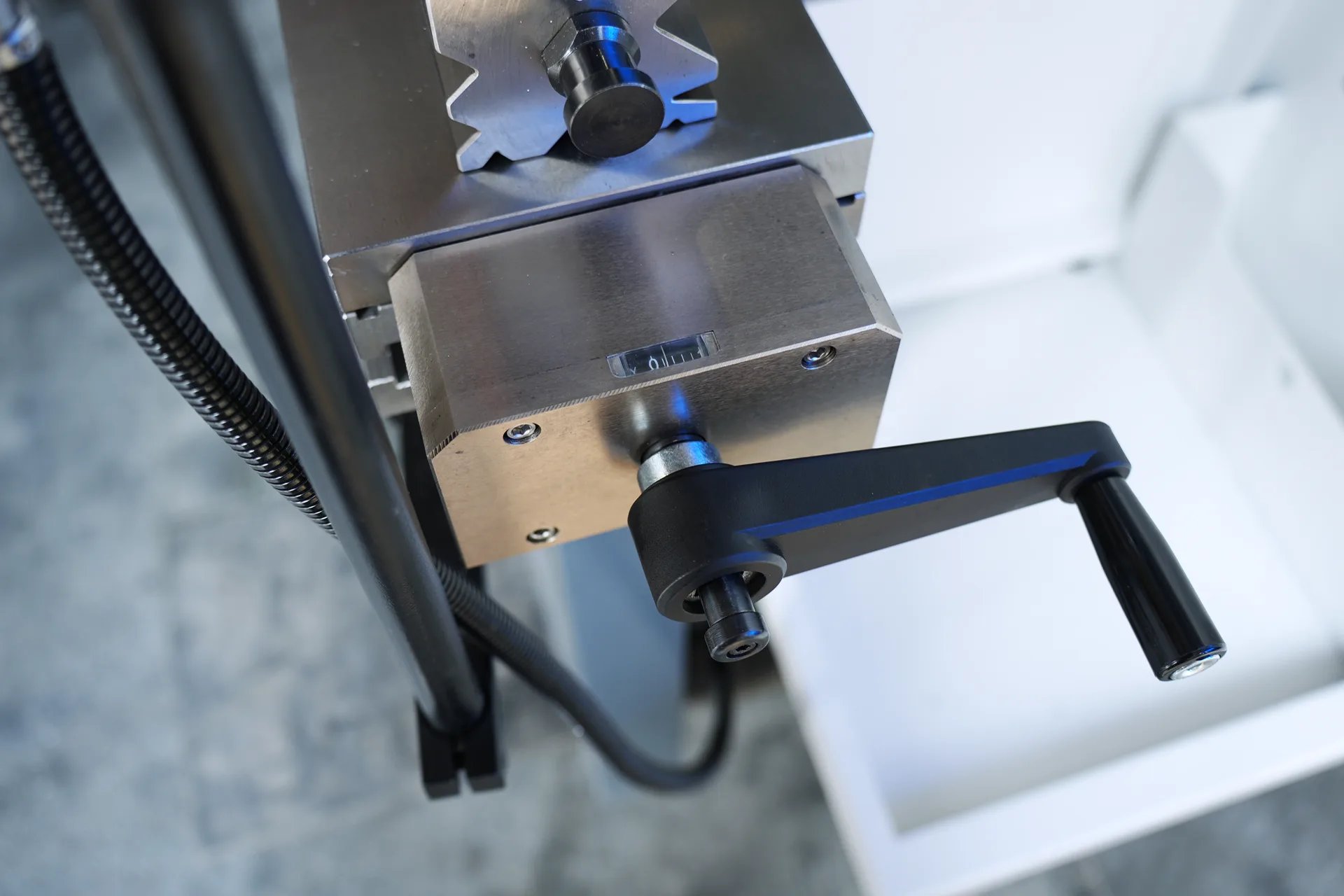
Vorteile:
- Niedrige Kosten: Manuelle Einstellgeräte sind einfach und weisen geringere Herstellungs- und Wartungskosten auf.
- Einfache Bedienung: Der Aufbau ist relativ einfach, leicht zu verstehen und zu bedienen, geeignet für Anfänger und kleine Unternehmen.
Nachteile:
- Geringe Einstellgenauigkeit: Die manuelle Einstellung hängt von der Erfahrung und den Fähigkeiten des Bedieners ab, was zu einer geringeren Präzision führt, was bei hochpräzisen Anforderungen eine Herausforderung darstellt.
- Geringe Effizienz: Der manuelle Anpassungsprozess ist zeitaufwändig und beeinträchtigt die Produktionseffizienz, insbesondere wenn häufige Anpassungen erforderlich sind.
- Schlechte Anpassungsfähigkeit: Nicht geeignet für Szenarien, die schnelle Werkstückwechsel und Prozessparameteranpassungen erfordern.
Geeignete Szenarien:
- Kleinserienfertigung: Geeignet für die Produktion in kleinem Maßstab ohne häufige Anpassungen.
- Geringe Präzisionsanforderungen: Ideal für Biegeaufgaben mit geringen Präzisionsanforderungen.
- Begrenztes Budget: Geeignet für kleine Unternehmen mit Budgetbeschränkungen.
Automatische mechanische Bombierungskompensation
Funktionsprinzip: Die automatische mechanische Bombierungskompensation verwendet CNC-Systeme oder andere automatische Steuergeräte, um die Position der Keile in Echtzeit zu überwachen und anzupassen. Nach Eingabe der erforderlichen Kompensationsparameter steuert das System automatisch den Anpassungsmechanismus, um Biegepräzision sicherzustellen.
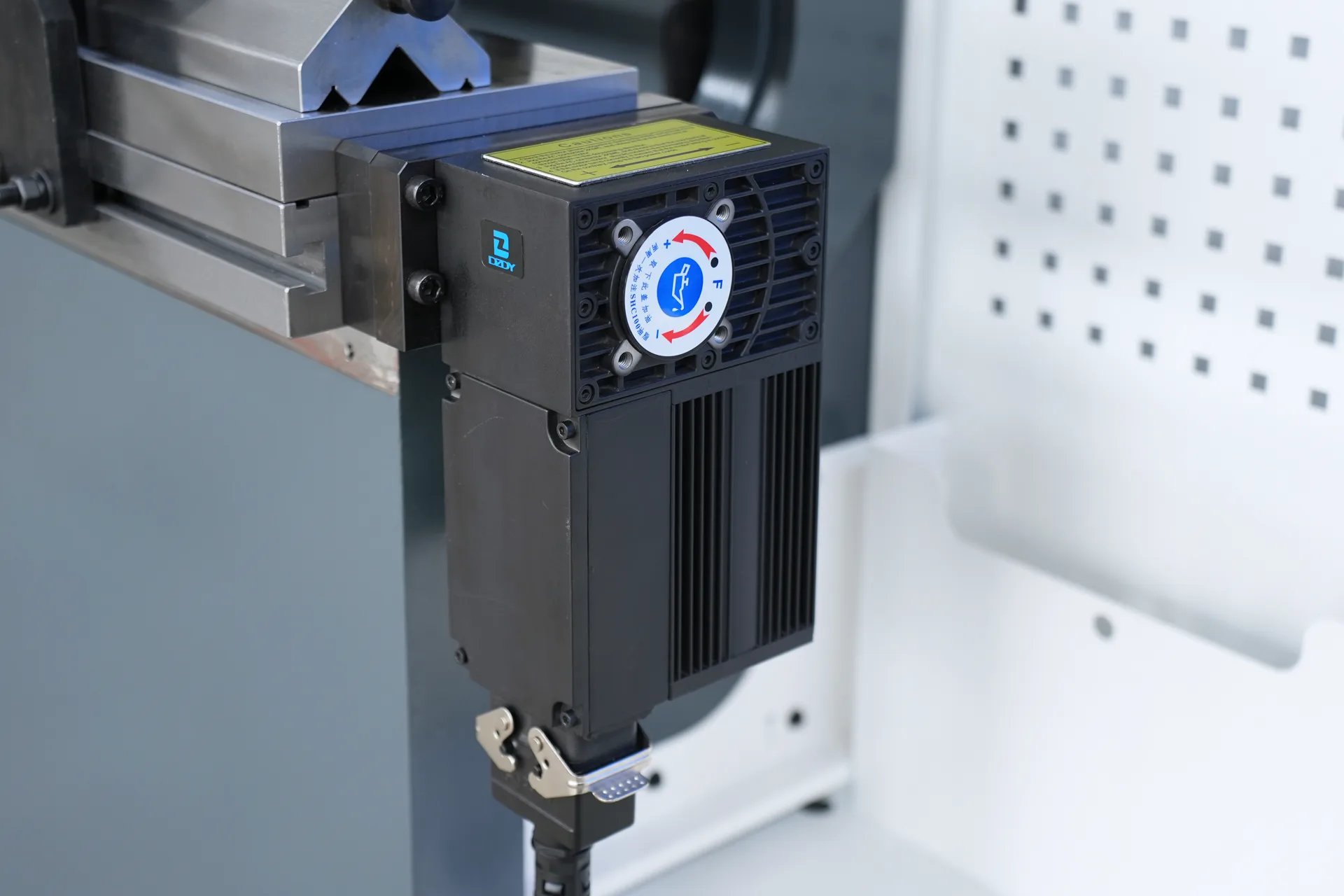
Vorteile:
- Hohe Präzision: Das automatische Steuerungssystem ermöglicht eine hochpräzise Kompensation und erfüllt so die Anforderungen einer hochpräzisen Verarbeitung.
- Hohe Effizienz: Der automatische Anpassungsprozess ist schnell und stabil, verbessert die Produktionseffizienz und ist für die Massenproduktion geeignet.
- Gute Konsistenz: Das automatische System sorgt für stabile und konsistente Kompensationseffekte und reduziert menschliche Fehler.
Nachteile:
- Hohe Kosten: Das automatische Kompensationssystem ist komplex und verursacht höhere Herstellungs- und Wartungskosten.
- Hohe technische Anforderungen: Erfordert professionelles Bedien- und Wartungspersonal, was die Schulungs- und Verwaltungskosten erhöht.
Geeignete Szenarien:
- Massenproduktion: Geeignet für die Produktion großer Stückzahlen, die häufige Anpassungen erfordert.
- Hohe Präzisionsanforderungen: Ideal für Biegeaufgaben mit hohen Präzisionsanforderungen.
- Hoher Automatisierungsbedarf: Geeignet für hochautomatisierte und effiziente Produktionsumgebungen.
Empfehlungen zur Auswahl einer mechanischen Balligkeitskompensation
Wenn Sie sich zwischen manueller oder automatischer mechanischer Balligkeitskompensation entscheiden, berücksichtigen Sie die spezifischen Produktionsanforderungen, das Budget und die technischen Bedingungen umfassend. Für Kleinserien mit geringer Präzision ist die manuelle mechanische Balligkeitskompensation eine wirtschaftliche und praktische Wahl. Für Massenproduktion, hohe Präzision und hohe Effizienzanforderungen bietet die automatische mechanische Balligkeitskompensation bessere Leistung und Produktionsergebnisse.
Mehrachsiges Hinteranschlagsystem in Abkantpressen
Ein mehrachsiges Hinteranschlagsystem ist eine fortschrittliche Komponente in elektrohydraulischen Abkantpressen, die zur präzisen Positionierung und Unterstützung von Werkstücken verwendet wird. Im Vergleich zu ein- oder zweiachsigen Hinteranschlagsystemen in Torsionsstab-Abkantpressen bieten mehrachsige Hinteranschlagsysteme mehr Flexibilität und Präzision und erfüllen die Anforderungen komplexer und vielfältiger Verarbeitungen.
Funktionsprinzip
Ein mehrachsiges Hinteranschlagsystem besteht normalerweise aus mehreren unabhängig gesteuerten Achsen, die von CNC-Systemen über Servomotoren oder Schrittmotoren angetrieben werden, wodurch eine hochpräzise Bewegung und Positionierung erreicht wird. Jede Achse kann ihre Position unabhängig anhand voreingestellter Programme anpassen, um unterschiedliche Formen und Größen von Werkstücken sowie komplexe Biegeprozesse zu ermöglichen.
Hauptkomponenten
- Servomotor oder Schrittmotor: Steuert die Bewegung jeder Achse und ermöglicht eine hochpräzise Positionssteuerung.
- Linearführungen und Kugelumlaufspindeln: Sorgen Sie für eine reibungslose Bewegung und eine hohe Wiederholgenauigkeit der Positionierung.
- CNC-System: Koordiniert das gesamte System und führt voreingestellte Biegeprogramme und Positionsanpassungen aus.
- Sensoren und Feedbacksystem: Überwachen Sie die Position jeder Achse in Echtzeit und geben Sie Feedback zur Korrektur von Abweichungen, um Präzision sicherzustellen.
Merkmale
- Hohe Präzision: Durch die Mehrachsensteuerung wird eine hochpräzise Positionierung und Einstellung erreicht, geeignet für komplexe Biegeprozesse.
- Starke Flexibilität: Jede Achse kann unabhängig gesteuert werden, sodass eine schnelle Anpassung an unterschiedliche Werkstücke und mehrstufige Biegeanforderungen möglich ist.
- Hoher Automatisierungsgrad: Durch die Verbindung mit CNC-Systemen sind hochautomatisierte Abläufe möglich und die Anzahl menschlicher Eingriffe wird reduziert.
- Hohe Effizienz: Automatische Anpassung und schnelle Positionierung verbessern die Produktionseffizienz erheblich und sind für die Massenproduktion geeignet.
- Gute Konsistenz: Präzise Steuerungs- und Rückmeldesysteme sorgen für gleichbleibende und hochwertige Verarbeitungsergebnisse.
Einstufung
Mehrachsige Hinteranschlagsysteme lassen sich je nach Bauart und Funktionalität in folgende Kategorien einteilen, die sich für unterschiedliche Anwendungsszenarien und Bearbeitungsanforderungen eignen:
- X-Achse (Vorne-Hinten): Steuert die Vorwärts-Rückwärtsbewegung der hinteren Anschlagplatte und bestimmt die Tiefenposition des Werkstücks.
- Merkmale: Grundlegende Funktion, weit verbreitet.
- Geeignete Szenarien: Alle Arten von Abkantpressen.
- R-Achse (Auf-Ab): Steuert die Auf- und Abbewegung der Hinteranschlagplatte, geeignet für mehrstufiges Biegen oder unterschiedliche Höhenpositionierung.
- Merkmale: Höhenverstellung, anpassbar an unterschiedliche Dicken und Formen von Werkstücken.
- Geeignete Szenarien: Komplexe Prozesse und mehrstufiges Biegen.
- Z1/Z2-Achsen (links-rechts unabhängig): Steuert die unabhängige Links-Rechts-Bewegung der Hinteranschlagplatten und ermöglicht so eine komplexere Positionierung und Unterstützung.
- Merkmale: Unabhängige Steuerung, geeignet für asymmetrische Werkstücke und spezielle Biegeanforderungen.
- Geeignete Szenarien: Komplexe Positionierung und spezielle Biegeanforderungen.
- X1/X2-Achsen (Vorder- und Rückseite unabhängig): Steuert die unabhängige Vorwärts-Rückwärtsbewegung der linken und rechten Hinteranschlagplatten, die für hochpräzise und komplexe Biegeprozesse verwendet wird.
- Merkmale: Unabhängige Vor- und Zurückbewegung für höhere Verarbeitungspräzision und Flexibilität.
- Geeignete Szenarien: Hochpräzise Bearbeitung und komplexe Biegevorgänge.
- R1/R2-Achsen (Auf-Ab unabhängig): Steuert die unabhängige Auf- und Abbewegung der linken und rechten Hinteranschlagplatten, geeignet für unterschiedliche Höhenpositionierungen und komplexe Biegeprozesse.
- Merkmale: Unabhängige Auf- und Abbewegung, geeignet für komplexe Prozesse und mehrstufiges Biegen.
- Geeignete Szenarien: Mehrstufiges Biegen und komplexe Prozesse.
- Achse zur Kompensation der Wölbung (W-Achse): Für höhere Präzision und höhere Verarbeitungsanforderungen können die meisten Abkantpressen mit weiteren Achsen ausgestattet werden, wie beispielsweise einer Achse zur Bombierungskompensation.
- Merkmale: Individualisierbar, passend für spezielle Prozessanforderungen.
- Geeignete Szenarien: High-End-Fertigung und komplexe Prozess-Szenarien.
Vergleich der Typen
Achsentyp | Funktion | Merkmale | Geeignete Szenarien |
---|---|---|---|
X-Achse (Vorne-Hinten) | Steuert die Vor- und Rückwärtsposition | Grundfunktion, weit verbreitet | Alle Arten von Abkantpressen |
R-Achse (Auf-Ab) | Steuert die Höhenposition | Höhenverstellung, anpassbar | Komplexe Prozesse, mehrstufiges Biegen |
Z1/Z2-Achsen (links-rechts unabhängig) | Unabhängige Links-Rechts-Position | Unabhängige Steuerung, anpassbar | Komplexe Positionierungen, spezielle Biegungen |
X1/X2-Achsen (Vorder- und Rückseite unabhängig) | Unabhängige Vor- und Rückposition | Hochpräzise, unabhängige Bewegung | Hochpräzise, komplexe Biegevorgänge |
R1/R2-Achsen (Auf-Ab unabhängig) | Unabhängige Auf-Ab-Position | Hochpräzise, unabhängige Bewegung | Mehrstufiges Biegen, komplexe Prozesse |
Bombierungskompensationsachse (W-Achse) | Höhere Präzisionsanforderungen | Anpassbare, erweiterte Anwendungen | Hochwertige Fertigung, komplexe Prozesse |
Auswahlempfehlungen
Basierend auf den oben genannten Kombinationen und den Hauptachsen Y1 und Y2 der Abkantpresse verfügen mehrachsige Hinteranschlagsysteme üblicherweise über die folgenden Kombinationstypen:
- 3+1 Achsen (Y1+Y2+X+W)
- 4+1 Achsen (Y1+Y2+X+R+W)
- 5+1 Achsen (Y1+Y2+X1+X2+R+W)
- 6+1 Achsen (Y1+Y2+X+Z1+Z2+R+W)
- 8+1 Achsen (Y1+Y2+X1+X2+Z1+Z2+R1+R2+W)
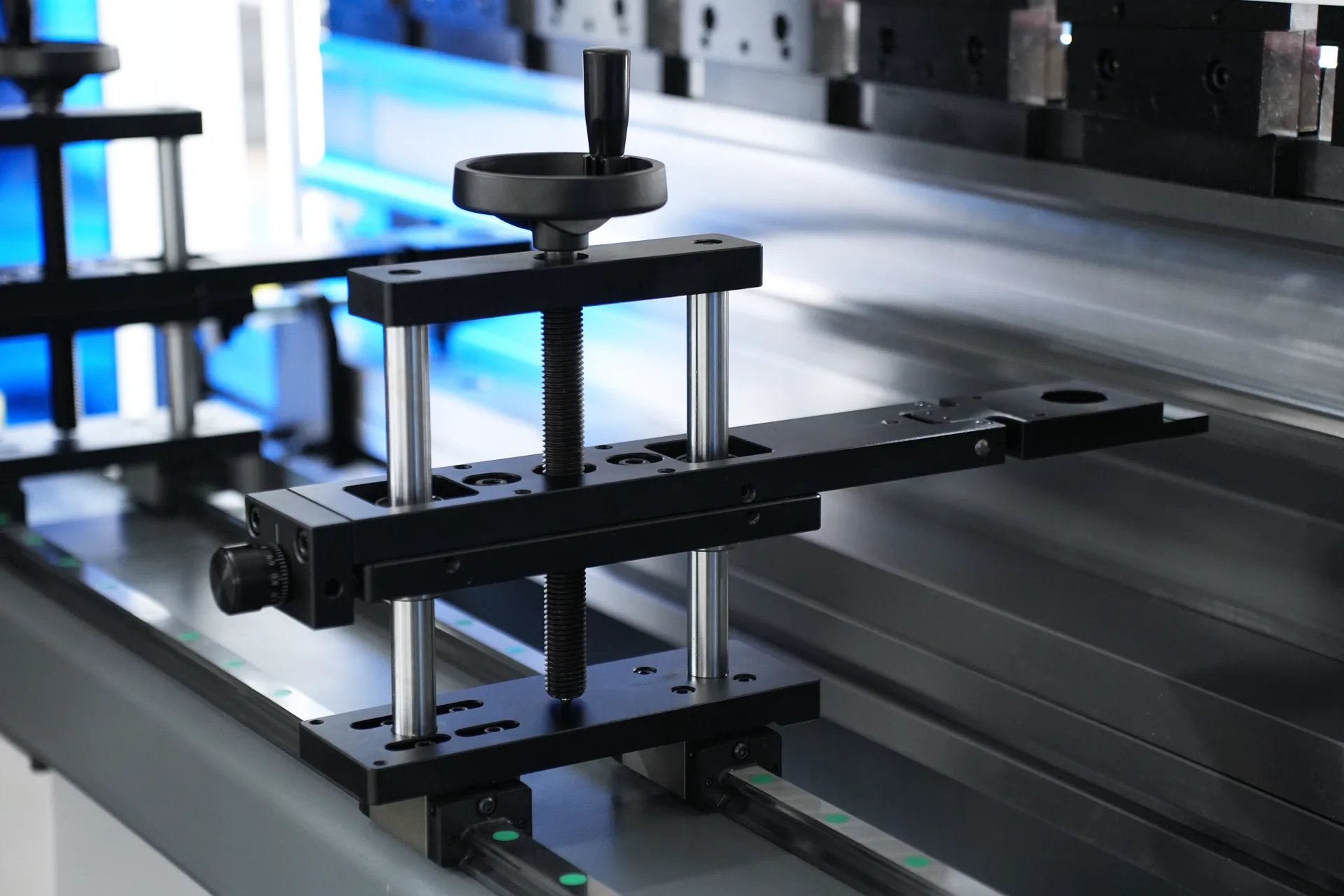
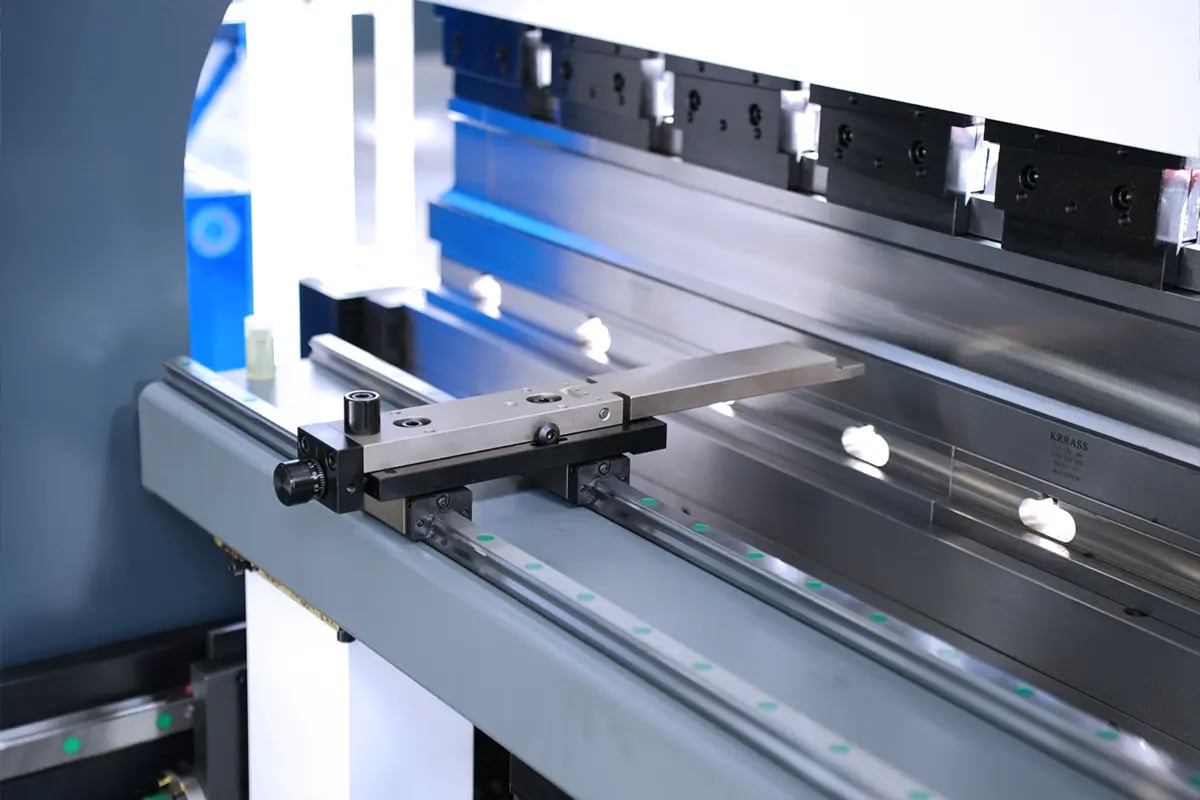
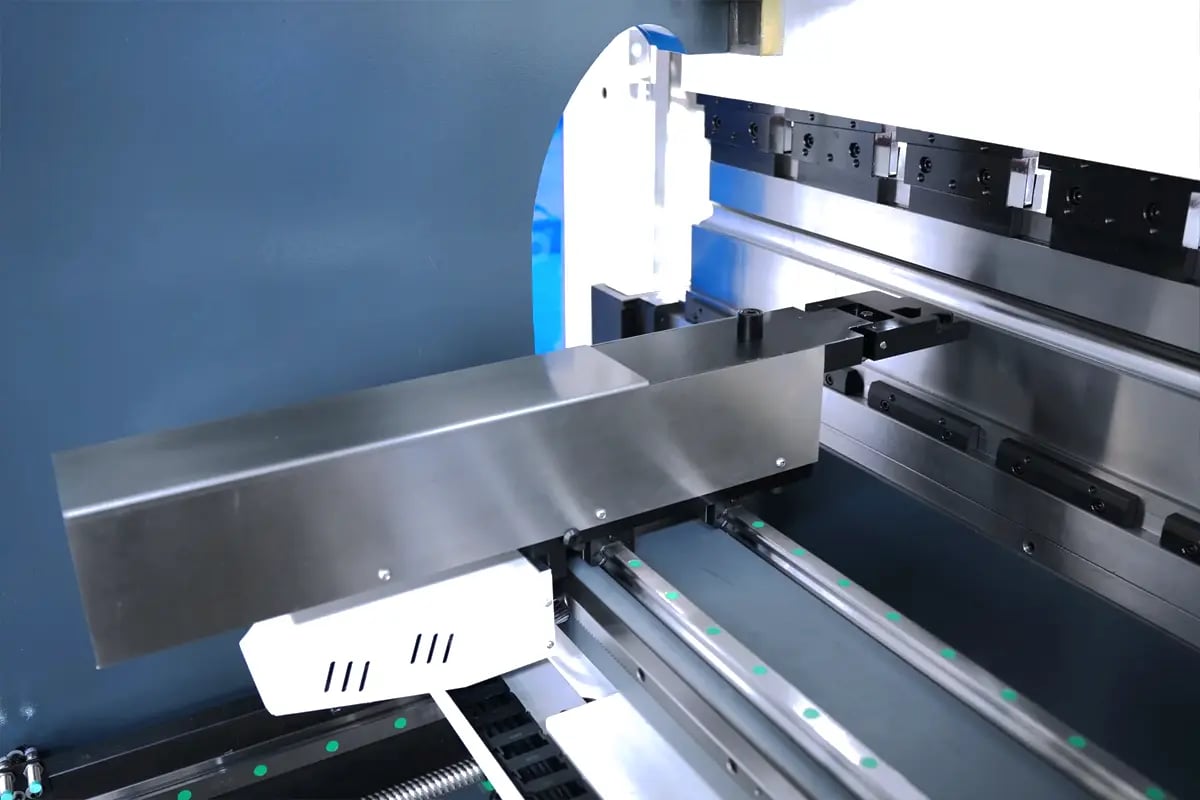
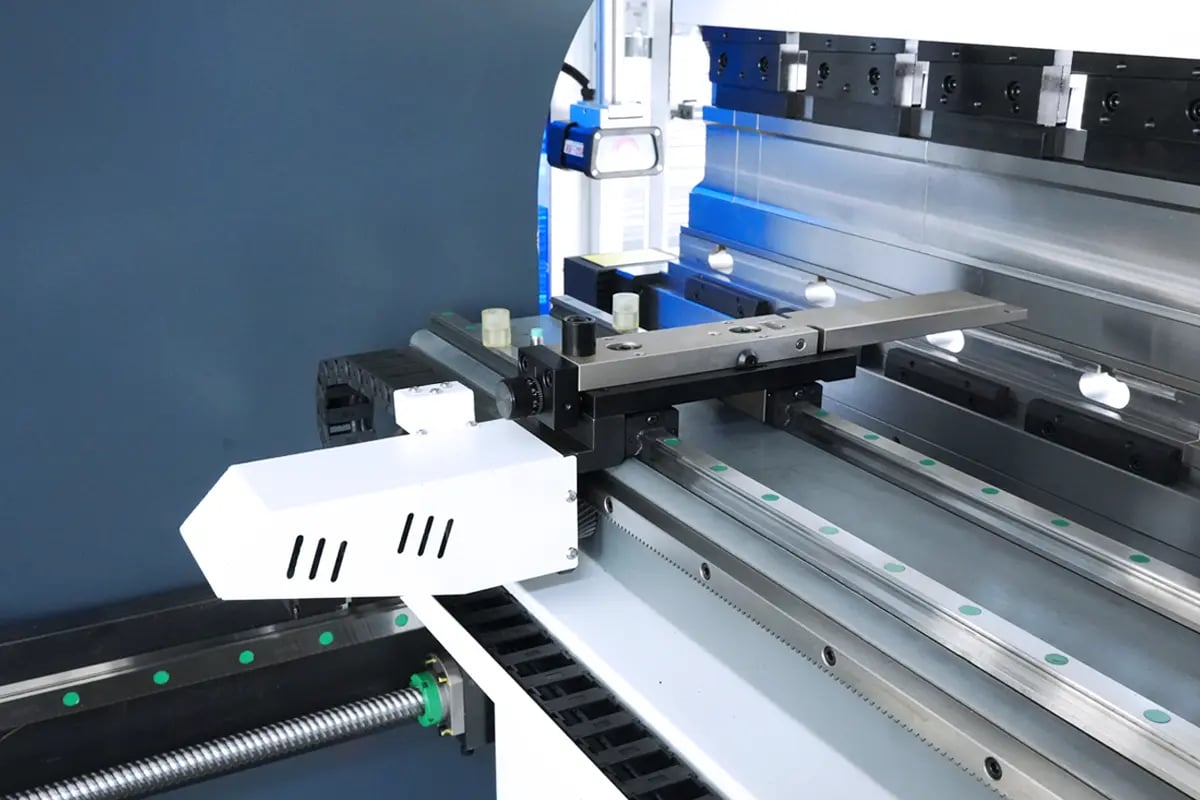
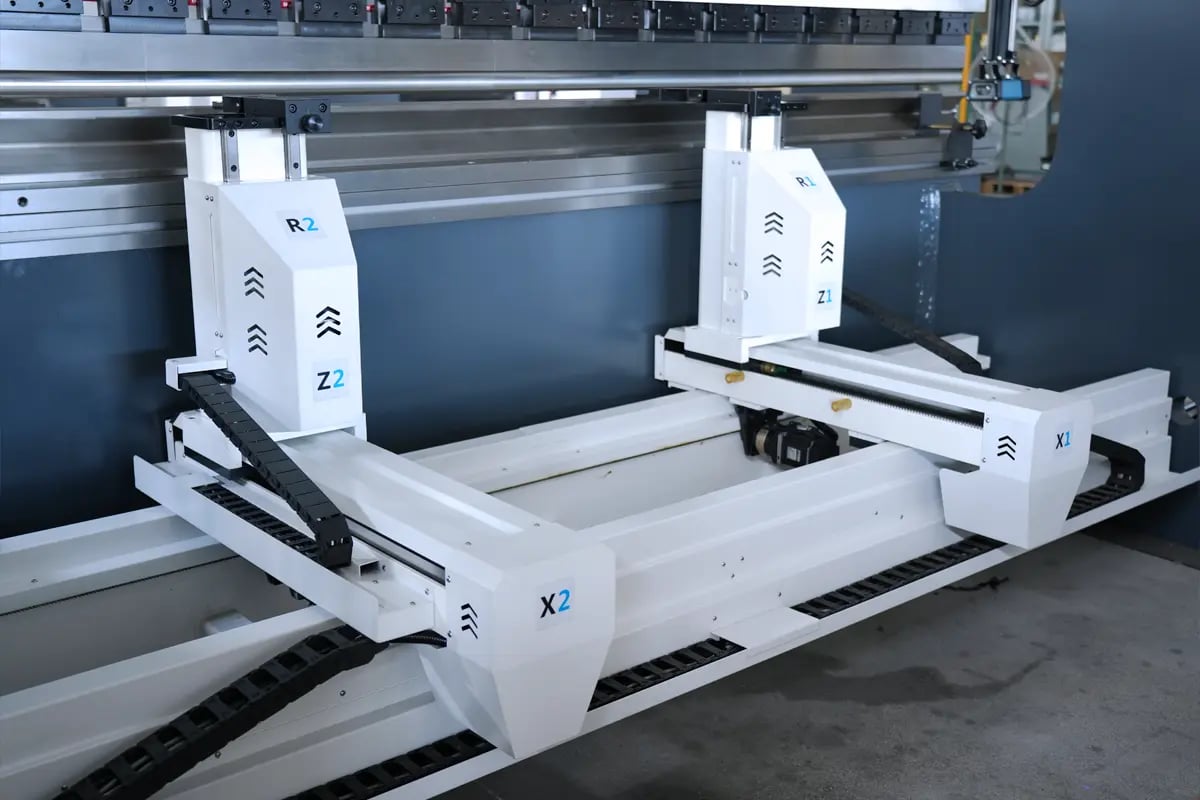
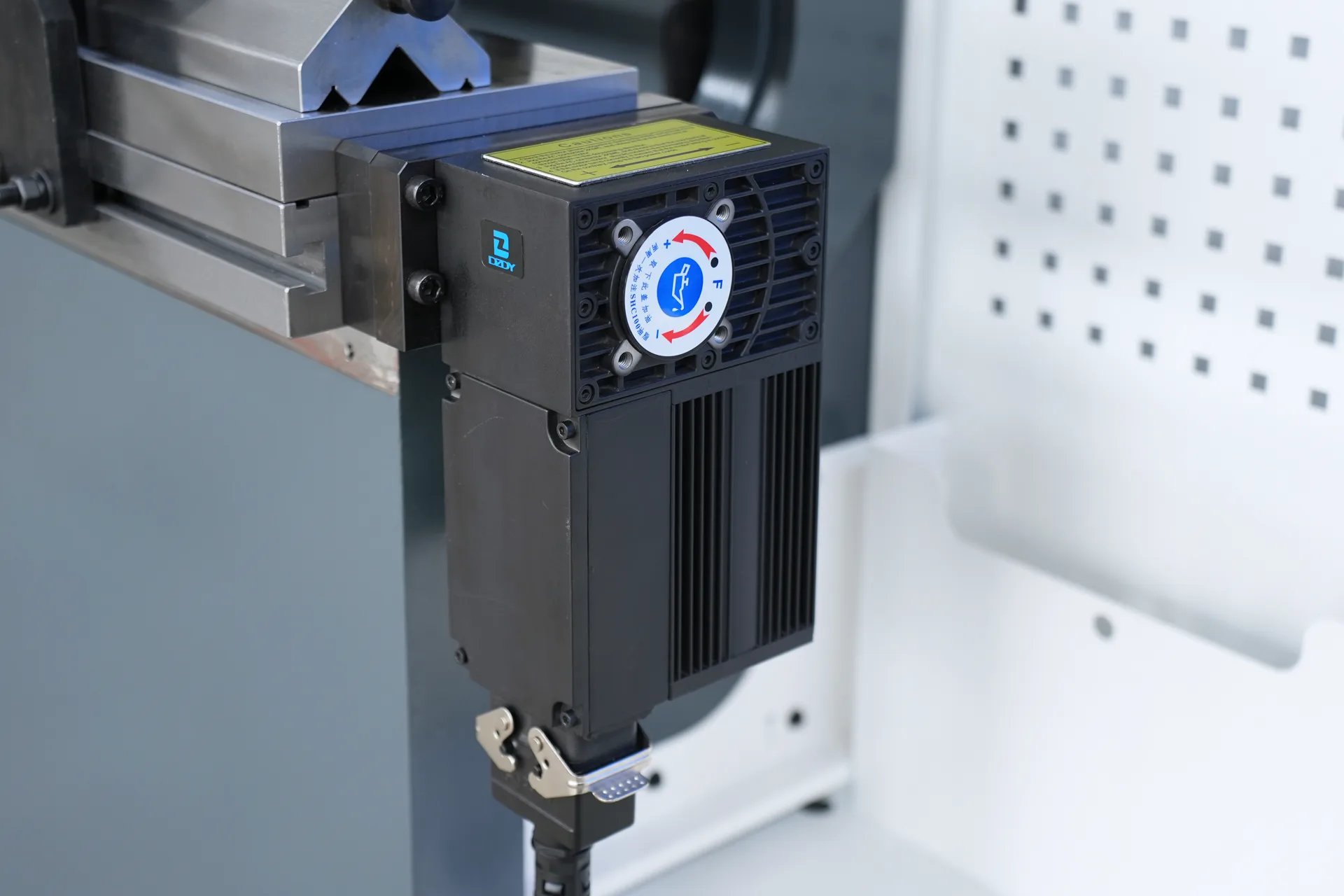
Berücksichtigen Sie bei der Auswahl eines mehrachsigen Hinteranschlagsystems die spezifischen Produktionsanforderungen und Verarbeitungstechniken:
- Grundbedürfnisse: Für reguläre Bearbeitungen sind die X-Achse und die R-Achse ausreichend.
- Hohe Präzisionsanforderungen: Für hochpräzise und komplexe Bearbeitungen bieten die X1/X2-Achsen, Z1/Z2-Achsen und R1/R2-Achsen mehr Flexibilität und Präzision.
- Spezielle Verfahren: Erwägen Sie bei besonderen Prozessanforderungen das Hinzufügen weiterer Spezialachsen, um bestimmte Positionierungs- und Unterstützungsanforderungen zu erfüllen.
Durch eine sinnvolle Auswahl und Konfiguration des mehrachsigen Hinteranschlagsystems können die Verarbeitungskapazität und Produktionseffizienz der Abkantpresse deutlich verbessert werden, sodass die hohen Standards der modernen Fertigung in puncto Präzision, Effizienz und Flexibilität erfüllt werden.
Hydraulische Abkantpressenformen
Die Formen einer Abkantpresse sind entscheidende Komponenten zur Bestimmung der Form und des Winkels der zu biegenden Werkstücke. Sie bestehen typischerweise aus einem oberen und einem unteren Gesenk, wobei das obere Gesenk an der Oberseite der Abkantpresse und das untere Gesenk an der Werkbank befestigt ist. Während des Biegevorgangs übt das obere Gesenk Druck auf das untere Gesenk aus, wodurch das Werkstück zwischen den Formen plastisch verformt wird und der Biegevorgang abgeschlossen wird.
Arten von Schimmelpilzen
Ein kompletter Satz Abkantpressenformen umfasst sowohl die Ober- als auch die Unterwerkzeuge, die je nach Form und Verwendungszweck in unterschiedlichen Ausführungen erhältlich sind:
- Standard-Oberwerkzeug:
- Verwendung: Geeignet für allgemeine Biegeanforderungen, mit einfacher Form und hoher Vielseitigkeit.
- Messerförmiges Obergesenk:
- Verwendung: Wird zum Biegen von spitzen Winkeln verwendet und kann spitze Biegewinkel erreichen.
- Schwanenhals-Obermatrize:
- Verwendung: Verfügt über eine gebogene Kante, geeignet zum Biegen tieferer Werkstücke.
- Einzelne V-Matrize:
- Verwendung: Verfügt über eine einzelne V-förmige Nut, geeignet für allgemeine V-förmige Biegeanforderungen.
- Konzentrische Doppel-V-Matrize:
- Verwendung: Verfügt über zwei konzentrische V-förmige Rillen, geeignet für Werkstücke, die zwei unterschiedliche Biegewinkel erfordern.
- Konzentrische Matrize mit vier V-förmigen Teilen:
- Verwendung: Verfügt über vier konzentrische V-förmige Rillen, geeignet für Biegeanforderungen mit mehreren Winkeln.
- Multi V Die:
- Verwendung: Verfügt über mehrere V-förmige Nuten und ermöglicht so eine flexible Auswahl je nach Form und Größe des Werkstücks.
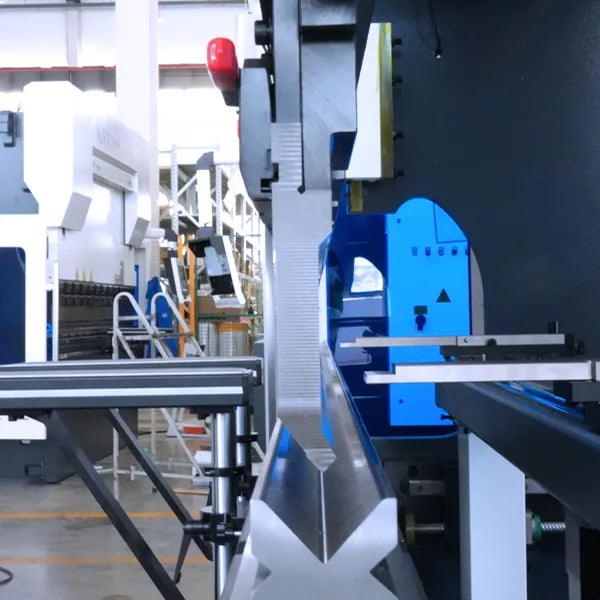
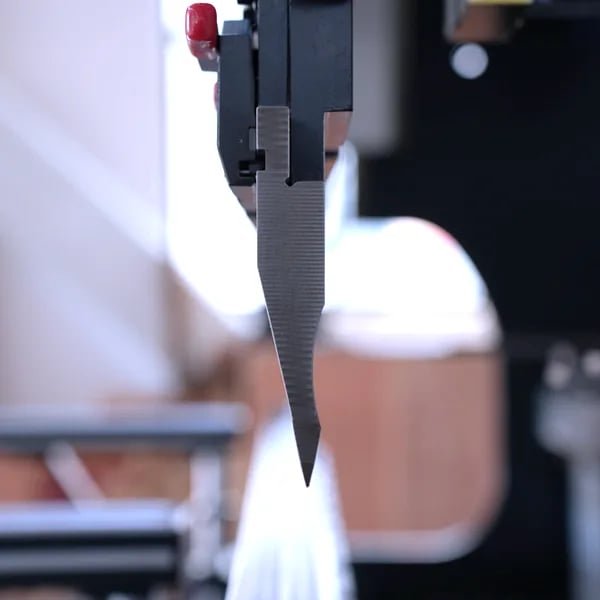
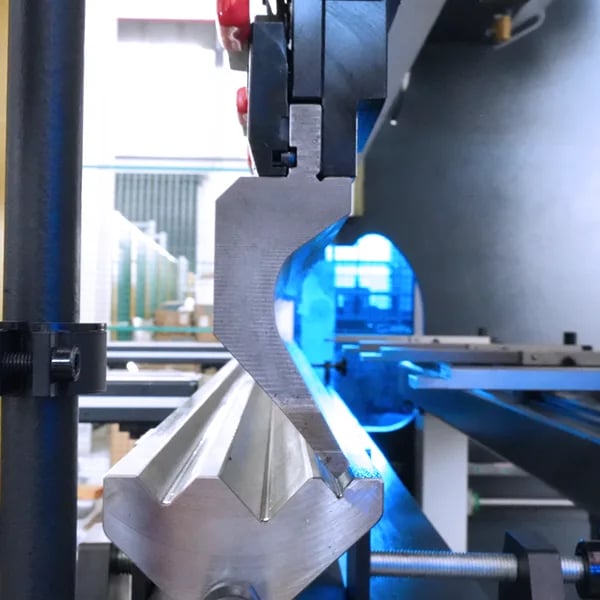
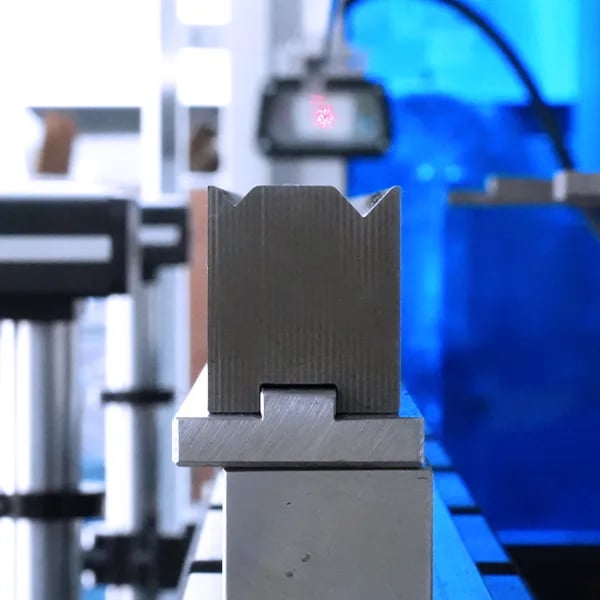
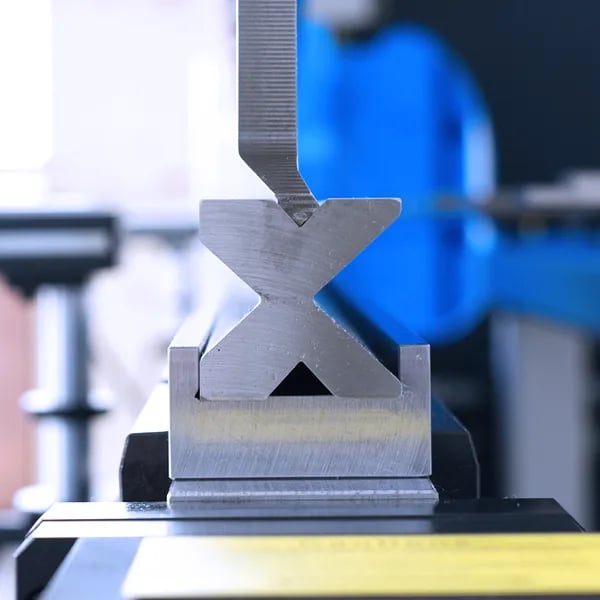
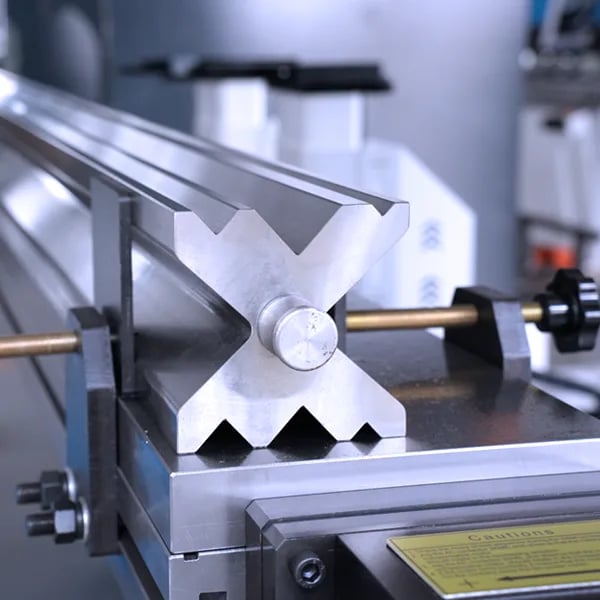
Formauswahl
Bei der Auswahl von Abkantpressenformen sollten folgende Faktoren umfassend berücksichtigt werden:
- Werkstoff des Werkstückes: Verschiedene Materialien stellen unterschiedliche Anforderungen an das Material und die Härte der Form.
- Dicke des Werkstücks: Die Dicke bestimmt die V-Nutbreite der Form und den Krümmungsradius der R-Typ-Form.
- Biegewinkel und Radius: Biegewinkel und Radius bestimmen Form und Größe der Form.
- Präzisionsanforderungen: Je höher die Präzisionsanforderung, desto höher muss die Genauigkeit der Form sein.
- Budget: Der Preis von Formen hängt von Faktoren wie Material, Präzision und Komplexität ab.
Abkantpressenformen sind für die gewünschten Biegevorgänge unerlässlich. Die richtige Auswahl und Verwendung von Formen kann die Verarbeitungseffizienz und Produktqualität verbessern und verschiedene Verarbeitungsanforderungen erfüllen.
Sicherheitsschutzsysteme der Abkantpresse
Als große Metallverarbeitungsmaschine birgt die hydraulische Abkantpresse erhebliche Betriebsrisiken. Daher ist sie mit mehreren Sicherheitsschutzsystemen ausgestattet, um die Sicherheit von Bedienern und Geräten zu gewährleisten. Zu den üblichen Sicherheitsschutzsystemen bei hydraulischen Abkantpressen gehören:
- Lichtvorhang: Besteht aus einem Paar Sender und Empfänger, die rund um den Arbeitsbereich installiert sind. Wenn ein Bediener den Arbeitsbereich betritt, wird der Lichtstrahl unterbrochen und die Maschine stoppt automatisch, um einen versehentlichen Kontakt mit Gefahrenbereichen zu verhindern.
- Zweihandsteuerung: Der Bediener muss die Tasten mit beiden Händen gleichzeitig drücken, um die Abkantpresse zu starten. Dieses System verhindert versehentliche Verletzungen durch Fehlbedienung oder Einhandbedienung.
- Sicherheitstürschalter: An der Tür der Abkantpresse installiert. Wenn die Tür geöffnet wird, stoppt das System automatisch, um zu verhindern, dass Bediener während des Betriebs den Gefahrenbereich betreten.
- Not-Aus-Taster: Normalerweise auf dem Bedienfeld. Im Notfall kann der Bediener die Taste drücken, um die Maschine sofort anzuhalten und so Unfälle zu vermeiden.
- Wächter und Barrieren: An wichtigen Teilen der Maschine, wie etwa im Werkzeugbereich und am Hydrauliksystem, installiert, um einen versehentlichen Kontakt mit gefährlichen Komponenten zu verhindern.
- Überlastschutzsystem: Überwacht den Druck und die Belastung des Hydrauliksystems. Wenn ein Druck oder eine Belastung den eingestellten Bereich überschreitet, wird das System automatisch gestoppt, um Schäden durch Überlastung zu vermeiden.
- Laserschutzsystem (z. B. DSP und MSD): Überwacht den Arbeitsbereich mithilfe von Laserstrahlen. Wenn ein Bediener die Gefahrenzone betritt, wird die Maschine zur Gewährleistung der Sicherheit sofort gestoppt.
- Sicherheitsschilder und -etiketten: Wird rund um die Abkantpresse und auf dem Bedienfeld installiert und enthält Warnungen und Betriebsrichtlinien, um die Bediener an die Sicherheitsvorkehrungen zu erinnern.
Diese Sicherheitsschutzsysteme bilden zusammen einen umfassenden Sicherheitsrahmen für hydraulische Abkantpressen, der Betriebsrisiken effektiv reduziert und die Sicherheit der Bediener und die Integrität der Ausrüstung schützt. Die Bediener sollten die relevanten Sicherheitsvorschriften und -verfahren strikt befolgen und die Sicherheitsschutzsysteme richtig verwenden, um eine sichere Produktion zu gewährleisten.
Erweiterte Funktionen von hydraulischen Abkantpressen
Zusätzlich zu den Standardkonfigurationen bieten hydraulische Abkantpressen häufig verschiedene optionale Funktionen, um den spezifischen Anforderungen verschiedener Kunden gerecht zu werden. Zu den üblichen optionalen Funktionen und ihren Merkmalen gehören:
- Automatische Werkzeuganpassung: Ermöglicht der Maschine, den Abstand zwischen den oberen und unteren Matrizen automatisch anzupassen, um unterschiedliche Materialstärken zu berücksichtigen und so die Produktionseffizienz und den Bedienkomfort zu verbessern.
- WILA Werkzeugaufbewahrungssystem: Eine effiziente Werkzeugverwaltungslösung, die besonders für hydraulische Abkantpressen geeignet ist. Mit dieser optionalen Funktion können Bediener die von der Abkantpresse verwendeten Werkzeuge effektiv organisieren, lagern und verwalten, was die Produktionseffizienz und den reibungslosen Arbeitsablauf verbessert.
- Winkelsensor: Wird auf der oberen Matrize der Maschine installiert und dient zur präzisen Messung des Biegewinkels, um die Genauigkeit und Konsistenz jeder Biegung sicherzustellen.
- Automatische Fütterungsvorrichtung: Kann Werkstücke automatisch zum Biegen in die Maschine einführen, was die Produktionseffizienz verbessert und manuelle Vorgänge reduziert.
- CNC-Frontstütze für Hinteranschlag: Eine weitere wichtige optionale Funktion für hydraulische Abkantpressen, die normalerweise zur Unterstützung und Stabilisierung der Vorderseite des Werkstücks verwendet wird und so Genauigkeit und Stabilität während des Biegevorgangs gewährleistet.
- Tandem-Abkantpressensystem: Verbindet zwei hydraulische Abkantpressen zur synchronisierten Steuerung miteinander, ermöglicht das gleichzeitige Biegen von Werkstücken und verbessert so die Produktionseffizienz. Dieses System wird typischerweise zur Bearbeitung großer Werkstücke verwendet und kann symmetrische oder asymmetrische Biegevorgänge durchführen.
- Flexible Biegeeinheit: Ein modulares Design, das das Hinzufügen zusätzlicher Arbeitseinheiten oder Geräte an der hydraulischen Abkantpresse für bestimmte Formen, komplexe Kurven oder spezielle Werkstücke ermöglicht. Diese Einheit kann je nach tatsächlichem Bedarf angepasst werden, was die Flexibilität und Anwendbarkeit der Maschine verbessert.
Diese optionalen Funktionen können je nach den spezifischen Anforderungen der Kunden ausgewählt und angepasst werden und verbessern die Verarbeitungseffizienz, Qualität und den Bedienkomfort von hydraulische Abkantpressen.
Abschluss
Hydraulische Abkantpressen sind unverzichtbare Geräte in der Blechverarbeitung und sind in verschiedenen Typen und Funktionen erhältlich. Die Wahl des richtigen Modells hängt von den spezifischen Verarbeitungsanforderungen und Produktionsbedingungen ab. Hydraulische Torsionsstab-Abkantpressen eignen sich für die Produktion großer Stückzahlen mit geringer Präzision, während hydraulische elektrohydraulische Abkantpressen ideal für die hochpräzise, komplexe Verarbeitung sind. Steuerung, Antriebsmethode, Biegekompensation und Werkzeuge wirken sich alle erheblich auf die Leistung und den Anwendungsbereich hydraulischer Abkantpressen aus. Daher sollten diese Faktoren beim Kauf einer hydraulischen Abkantpresse umfassend berücksichtigt werden, um die Auswahl der am besten geeigneten Geräte sicherzustellen und so die Produktionseffizienz und Verarbeitungsqualität zu verbessern.