Erstellen einer Betriebsanleitung für eine Schwingbalken-Schermaschine beinhaltet detaillierte Anweisungen zur sicheren und effektiven Bedienung der Geräte. Hier ist eine strukturierte Gliederung für ein solches Handbuch:
Inhaltsverzeichnis
Standardfunktionen der hydraulischen Schwenkbalkenschere
Der hydraulische Schwenkbalkenschere ist zum Schneiden von Metallstahlplatten konzipiert, wobei die Kapazität auf einer Plattenfestigkeit von 450 N/mm2 basiert.
Bitte passen Sie die Plattendicke an, wenn Sie andere Materialien mit unterschiedlicher Stärke schneiden.
Die Maschine verfügt über eine Blechschweißkonstruktion, die eine einfache Bedienung und zuverlässige Leistung gewährleistet.
Der Schneidvorgang erfolgt durch Hydraulikdruck und der Rücklauf wird durch eine Stickstoffgasflasche gesteuert, was dazu beiträgt, die Maschine vor Überlastung zu schützen.
Die Maschine kann je nach Kundenwunsch mit einem digitalen Anzeigesystem oder einem numerischen Steuerungssystem ausgestattet werden.
Für bequeme und schnelle Anpassungen ist außerdem eine Klingenspaltanzeige vorhanden.
Die Maschine ist mit einer Ausrichtungsvorrichtung mit Beleuchtung ausgestattet und der Schnitthub kann eingestellt werden, um die Effizienz beim Schneiden schmaler Platten zu verbessern.
Zusätzlich sind vordere Stützarme und ein Hinteranschlag vorhanden. Der Hinteranschlag ist mechanisch verschiebbar und seine Position kann numerisch angezeigt oder von einer NC-Steuerung über Encoder gesteuert werden. Die Feineinstellung erfolgt über ein Handrad. Die vorderen Stützarme sind mit Linealen ausgestattet.
Auf dem Arbeitstisch befindet sich eine rollende Materialstützkugel, um das Schlingern mit Blechen zu minimieren und den Reibungswiderstand zu verringern.
Um einen sicheren Betrieb zu gewährleisten, wurde ein Sicherheitszaun installiert.
Rahmen der hydraulischen Schwenkbalkenschere
Maschinenrahmen
Die hochsteife, stahlgeschweißte Platte verfügt über zwei Zylinder, die an der linken und rechten vertikalen Stange befestigt sind.
Auf dem Arbeitstisch ist ein Schraubstock-Schneidbrett installiert, um das untere Schneidbrett bequem einzustellen und sicherzustellen, dass der Abstand zwischen dem oberen und unteren Schneidbrett ausgerichtet ist. Für eine bequeme und schnelle Bedienung ist auf dem Arbeitstisch auch eine Zuführkugel installiert.
Schneidrahmen
Die hochsteife Schweißplatte wird an der Exzenterbuchse (9) abgestützt und von den linken und rechten Zylindern sowie dem Hubzylinder angetrieben, um den Schneidvorgang durch Pendelwiederholung abzuschließen. Die vertikale Oberfläche der Aufwärtsschnittstütze ist gekrümmt, um die Ausrichtung des Spalts zwischen Aufwärts- und Unterschnitt beizubehalten.
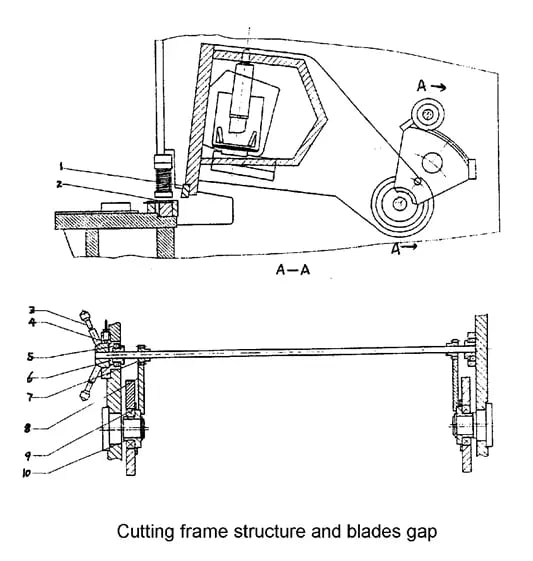
Druckvorrichtung (Niederhalten)
Es besteht aus Druckvorschubzylindern, die auf der Stützplatte vor dem Maschinenrahmen montiert sind. Der Ölfluss im Druckvorschubzylinder erzeugt Druck, der gegen die Zugkraft der Spannfeder (18) nach unten drückt und so die Pressplatte fest fixiert. Nach dem Schneiden werden die Zylinder durch die Zugkraft der Spannfeder zurückgesetzt. Der Druck steigt mit der Plattendicke.
Vorderanschlag und Hinteranschlag
Vorderes Messgerät:
Der Arbeitstisch ist mit einer Ventilanzeige am Lineal ausgestattet, sodass die bewegliche Stange auf das gewünschte Ventil eingestellt werden kann. Das Schneiden dünner Stahlplatten kann bequem am vorderen Anschlag erfolgen. Der hintere Anschlag (siehe Abbildung 5) ist am oberen Schneidbrett befestigt und bewegt sich mit diesem auf und ab.
Der Hinteranschlag wird durch einen 0,55-kW-Motor eingestellt, der das Drehmoment über ein Getriebe reduziert und die Steuerstange antreibt. Durch Drücken der Tasten „+“ oder „-“ kann der Anschlag vorwärts oder rückwärts verstellt werden. Falls der gewünschte Wert nicht durch mechanische Einstellung erreicht werden kann, kann das Handrad (50) gedreht werden, um den gewünschten Wert einzustellen. Dies macht die Einstellung des Hinteranschlags bequem und zuverlässig.
Der Standardbereich des Hinteranschlags beträgt 20–750 mm. Überschreitet die Länge der Schneidplatte den maximalen Abstand des Hinteranschlags, kann der Hinteranschlag (43) auf die Minimalposition zurückgefahren und die Platte mithilfe der schrägen Fläche des Stützrahmens (47) angehoben werden. So können Platten beliebiger Länge geschnitten werden. (Siehe Abb. 4)
Installation einer Schwingbalkenschere
Verpackung / Versand der hydraulischen Schermaschine
Alle Maschinen verlassen das Werk in der Verpackung mit einem Winkelanschlag und einer am Handschutz befestigten Fußplatte. Die Arbeitswerkzeuge und eine Bedienungsanleitung sind in einem Karton verpackt.
Alle freiliegenden Oberflächen der Maschine sind mit einem Rostschutzmittel beschichtet, das sich leicht mit Kerosin oder einem Lösungsmittel entfernen lässt.
Anheben der hydraulischen Schermaschine
Verwenden Sie zum Anheben dieser Maschine an den beiden Hebepunkten an beiden Seiten der Maschine nur zugelassene und sichere Drahtseile. (Siehe Abbildung 5)
Stiftung
Alle unsere Scheren sind für die Fundamentmontage konzipiert. Details entnehmen Sie bitte der beigefügten Fundamentzeichnung.
Installation
Für eine optimale Schneidleistung muss diese hydraulische Schermaschine korrekt nivelliert werden. Dies kann durch die Verwendung einer hochwertigen Nivellierlehre im Bereich der Plattenhalterung erreicht werden.
Stellen Sie vor dem Nivellieren sicher, dass Sie fünf Grundplatten (mindestens 150 x 150 x 9 mm groß) unter den Füßen der Maschine platziert haben, um zu verhindern, dass sich die Nivellierschrauben in den Betonboden graben.
Sobald die Maschine nivelliert ist, sichern Sie ihre Position, indem Sie den Raum unter und um ihre Füße mit einer Zementmörtelmischung füllen.
Elektrische Installation
Stellen Sie sicher, dass die örtliche Stromversorgung mit dieser hydraulischen Schermaschine kompatibel ist, bevor Sie den Strom einschalten.
Schließen Sie das Netzkabel unten links am Schaltschrank an. Manche Geräte benötigen möglicherweise einen Neutralleiter.
Einstellung der Schwingbalkenschere
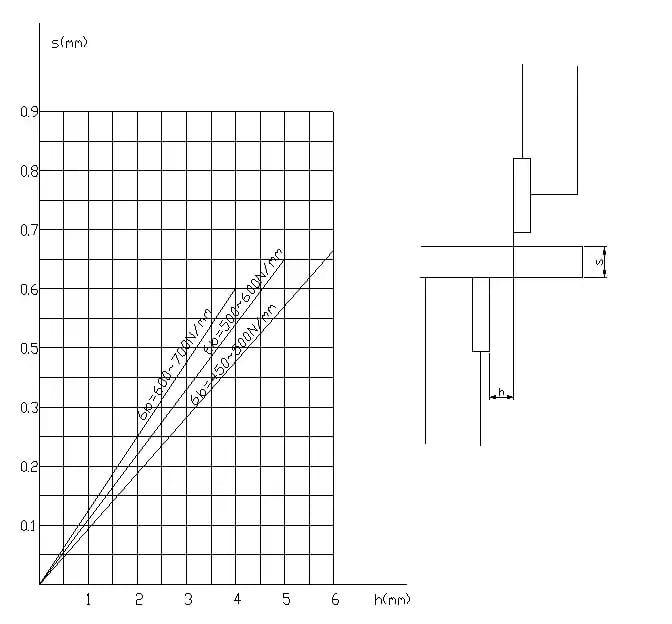
Passen Sie den Abstand zwischen den Klingen der hydraulischen Schermaschine an
Der Klingenabstand ist entscheidend für die Schnittqualität und die Lebensdauer der Klingen. Bitte stellen Sie ihn gemäß der unten stehenden Tabelle ein.
Passen Sie den Abstand zwischen den Klingen an
Zum Einstellen des Spalts (siehe Abbildung 2) müssen Sie die Feststellschraube (4) lösen, dann das Handrad (3) auf den gewünschten Wert drehen, der anhand der Plattendicke berechnet werden sollte, und schließlich die Schraube (4) festziehen.
Es gibt ein Kugelventil (auf der rechten Seite der Maschine, außerhalb des Zylinders), mit dem der Abstand zwischen den oberen und unteren Klingen gemessen werden kann.
Weitere Informationen: Im manuellen Modus, wenn der Schneidrahmen den unteren Totpunkt erreicht, schließen Sie schnell den Ölkreislauf, sodass der Schneidrahmen im unteren Totpunkt verbleibt. Öffnen Sie anschließend langsam das Kugelventil, sodass sich der Schneidrahmen schrittweise über den gesamten Hub nach oben bewegt. So können Sie den Spalt zwischen den Klingen messen.
Betrieb der hydraulischen Schermaschine
Vorbereitung der Maschine
(1) Den Winkelanschlag und das Fußpedal aus dem Handschutzbereich entfernen. Den Winkelanschlag mit Schrauben und den beiden seitlichen Löchern an der linken Seite des Maschinentisches befestigen. Der Anschlag sollte sich in der Nähe des Schaltschranks befinden.
(2) Reinigen Sie die Komponenten von verschmutztem Öl und achten Sie dabei darauf, dass sich das Kugelventil in der geöffneten Stellung befindet.
(3) Schmieren Sie alle erforderlichen Bereiche.
(4) Füllen Sie den Öltank für jede Maschine unter dem 12-mm-Modell mit 200 l HL46-Hydrauliköl.
(5) Schließen Sie die Erdungsleitung an, schalten Sie die Stromversorgung ein und überprüfen Sie die Funktion aller elektrischen Komponenten.
Starten der Maschine
(1) Drücken Sie die Taste „START“ und lassen Sie sie wieder los.
(2) Die Kontrollleuchte „Motor ein“ sollte aufleuchten.
(3) Ändern Sie den Moduswähler von „MAN“ auf „AUTO“.
(4) Durch Betätigen des Fußschalters senkt sich der Schneidrahmen ab und führt einen Schnitt aus.
(5) Wenn der Schneidrahmen nicht absenkt, läuft der Motor wahrscheinlich in die falsche Richtung. Schalten Sie den Strom ab und vertauschen Sie einen der beiden Phasenleiter, um den Motor neu zu starten.
(6) Der obere Klingenträger hebt sich und stoppt, wenn er den Endschalter erreicht.
Motorisierter Hinteranschlag
(1) Die Anzeige des motorisierten Hinteranschlags muss im Werk genau eingestellt werden und dem Abstand zwischen der Hinteranschlagstange und der Schneide entsprechen.
(2) Drücken Sie die Taste „+“, um den hinteren Messbalken nach hinten zu bewegen. Die Anzeige steigt an und stoppt, wenn der maximale Wegschalter L/S 3 erreicht ist.
(3) Drücken Sie die Taste „-“, um den hinteren Messbalken nach vorne zu bewegen. Die Anzeige verringert sich und stoppt, wenn der Mindestwegbegrenzungsschalter L/S 4 erreicht ist.
(4) Die Parallelität des Hinteranschlags sollte im Werk eingestellt werden, kann aber bei Bedarf kalibriert werden.
(5) Bewegen Sie den hinteren Anschlag nach hinten, um die Rostschutzbeschichtung vor dem Schneiden zu entfernen.
Notiz:
(1) Die Drucktabelle sollte während des Schneidens eingeschaltet sein. Bei fehlerhaftem Druck sollte der Druck überprüft werden. Gegebenenfalls muss das Überlaufventil angepasst werden.
(2) Sollten während des Betriebs ungewöhnliche Geräusche oder eine Überhitzung des Öltanks auftreten, muss die Maschine sofort gestoppt werden. Die Temperatur des Öltanks darf 60 °C nicht überschreiten.