Inhaltsverzeichnis
Die Wunder der Biegemaschinen in der Metallverarbeitung
Einführung in Biegemaschinen
Biegemaschinen, fester Bestandteil des Schmiedemaschinenbaus, sind unverzichtbare Werkzeuge in der Metallverarbeitung. Ihre vielseitigen Einsatzmöglichkeiten erstrecken sich über verschiedene Branchen, darunter die Leichtindustrie, Luftfahrt, Schifffahrt, Metallurgie und darüber hinaus.
Innovationen in Hydrauliksystemen
Der Grundstein von Biegemaschinen liegt in ihren Hydrauliksystemen, die sorgfältig für optimale Leistung konstruiert wurden. Kolbenpumpen für Druckausgleich und präzise Ölzufuhr sowie eine Drosselsteuerung für die Ölrückführung sorgen für höchste Energieeffizienz. Vertikale Hydraulikzylinder, verstärkt mit Ausgleichs- und Verriegelungsmechanismen, gewährleisten einen sicheren und zuverlässigen Betrieb und liefern enorme Klemm- und Scherkräfte für höchste Leistung beim Biegen.
Design-Exzellenz und strukturelle Innovation
Die Design-Feinheiten von Biegemaschinen Dies gilt auch für Pressensysteme, Blechscheren und hydraulische Pumpstationen. Dabei wird größter Wert auf Schaltungsdesign, Strukturaufbau und die Integration nicht standardisierter Komponenten gelegt. Durch diesen Designprozess wird eine harmonische Kombination aus kompakter Struktur, rationalem Aufbau und vereinfachter Fertigung erreicht, die die Effizienz und Bedienbarkeit dieser Maschinen steigert.
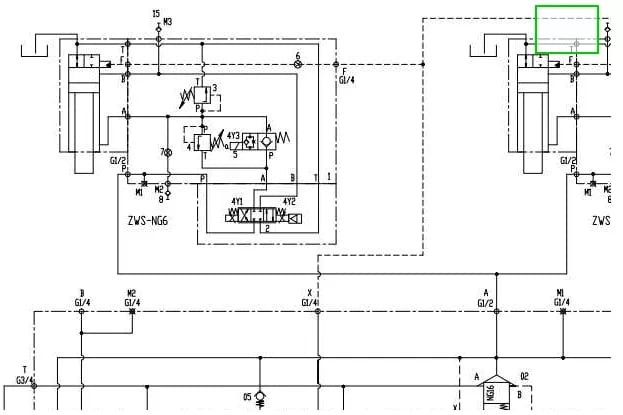
Eintauchen in Hydrauliksysteme
Grundlagen der Fluidtechnik erkunden
Fluidtechniksysteme nutzen die Energieübertragung durch verschiedene Medien, sei es Flüssigkeit oder Gas. Ausgehend von wasserbasierten Systemen hat die Entwicklung der Hydraulik eine neue Ära eingeleitet, die überwiegend durch Kreisläufe mit Mineralöl gekennzeichnet ist. Zusätzlich dient Druckluft als weiteres gängiges Medium und bietet eine sinnvolle Alternative zur Energieübertragung.
Navigieren durch die Branchendynamik
Trotz ihrer Bedeutung wird die Fluidtechnik in der Branche oft vernachlässigt. Da es nur wenige Fachkräfte für die Schaltungskonstruktion und -wartung gibt, ist die Abhängigkeit vom Fachwissen der Fluidtechnik-Händler weit verbreitet. Maschinenbauingenieure, denen eine fundierte Fluidtechnik-Ausbildung fehlt, wenden sich oft an Vertriebsmitarbeiter von Händlern, um sich beraten zu lassen. Dies unterstreicht den Bedarf an umfassender Branchenausbildung.
Die Vorteile hydraulischer Systeme entdecken
Kompakt, effizient und vielseitig: Hydraulikzylinder und -motoren verkörpern den Höhepunkt moderner Ingenieurskunst. Ihre Fähigkeit, problemlos auf engstem Raum zu arbeiten, gepaart mit sofortiger Umkehrbarkeit und variabler Drehzahl, macht sie zu unschätzbarem Wert. Dennoch bestehen weiterhin Herausforderungen, die vor allem auf mangelndes Verständnis und suboptimales Schaltungsdesign zurückzuführen sind und zu Problemen wie Überhitzung und Leckagen führen.
Optimierung von Leistung und Effizienz
Strategische Entscheidungsfindung: Hydraulik vs. Pneumatik
Bei der Wahl zwischen hydraulischen und pneumatischen Systemen ist die Ermittlung des optimalen Kraftbedarfs entscheidend. Pneumatische Schaltungen eignen sich hervorragend für Anwendungen mit geringen Kräften, Hydrauliksysteme hingegen sind bei hohen Kräften unschlagbar. Ein differenziertes Verständnis der jeweiligen Stärken und Schwächen unterstützt strategische Entscheidungen und gewährleistet eine optimale Systemleistung.
Betriebliche Herausforderungen bewältigen
Die Bewältigung betrieblicher Herausforderungen erfordert einen vielschichtigen Ansatz, der die Optimierung des Schaltungsdesigns und proaktive Maßnahmen zur Leckageprävention umfasst. Durch die Minimierung von Stößen und die Gewährleistung eines kühlen Betriebs kann das Auftreten von Leckagen erheblich reduziert und so die Systemzuverlässigkeit und -lebensdauer erhöht werden.
Das Pascalsche Gesetz: Die Grundlage der Fluidtechnik
Das Herzstück hydraulischer und pneumatischer Systeme ist das Pascalsche Gesetz, ein grundlegendes Prinzip, das das Verhalten eingeschlossener Flüssigkeiten bestimmt. Dieses unveränderliche Gesetz ist die Grundlage für die Funktionalität von Biegemaschinen und ermöglicht präzise Steuerung und effiziente Energieübertragung.
Herausforderungen der Kompressibilität meistern
Minderung der Kompressibilität: Eine Voraussetzung für Effizienz
Hydraulikflüssigkeiten gelten üblicherweise als inkompressibel, doch eingeschlossene Luft führt zu einer gewissen Kompressibilität. Strategische Maßnahmen zur Minimierung der Kompressibilität sowie eine sorgfältige Schaltungsauslegung sind für die Optimierung der Systemeffizienz und -leistung unerlässlich.
Beseitigung betrieblicher Hindernisse
Die Beseitigung eingeschlossener Luft in Hydraulikkreisläufen ist ein wichtiges Unterfangen und entscheidend für die Verbesserung der Systemsteifigkeit und Betriebseffizienz. Durch die Reduzierung der negativen Auswirkungen der Kompressibilität können Biegemaschinen in verschiedenen Anwendungen reibungslos arbeiten und so optimale Leistung und Zuverlässigkeit gewährleisten.
Fazit: Pionierarbeit für die Zukunft der Metallverarbeitung
Zusammenfassend lässt sich sagen, dass Biegemaschinen wahre Wunderwerke moderner Ingenieurskunst sind und die Metallverarbeitung in unzähligen Branchen revolutionieren. Durch unermüdliche Innovation und ein unerschütterliches Streben nach Exzellenz erweitern diese Maschinen immer wieder die Grenzen des Möglichen und gestalten die Zukunft der Metallverarbeitung mit beispielloser Präzision und Effizienz. Im Wandel der industriellen Automatisierung bleibt die Rolle der Biegemaschinen von größter Bedeutung und läutet eine neue Ära der Innovation und Produktivität in der Metallverarbeitung ein.