Inhaltsverzeichnis
Was ist der innere Biegeradius
Das Innere Biegeradius bezieht sich auf die Krümmung der Innenfläche eines gebogenen Metallwerkstücks, die typischerweise während des Biegeprozesses auf einer Abkantpresse oder Biegemaschine entsteht. Dieser Radius ist bei der Blechbearbeitung wichtig, da er die Gesamtform und die Abmessungen des gebogenen Teils beeinflusst.
Der innere Biegeradius wird durch Faktoren wie Biegewinkel, Materialstärke, Biegemethode (z. B. Luftformung, Bodenbiegen, Prägen) und die Art der verwendeten Matrize bestimmt. Er ist ein kritischer Parameter bei Biegeberechnungen, da er die Biegezugabe, den Biegeabzug und die Gesamtgenauigkeit des fertigen Teils beeinflusst.
Beim Airforming wird die Innenseite Biegeradius ist normalerweise ein Prozentsatz der Matrizenöffnung, während er beim Bodenbiegen und Prägen durch den Stempelspitzenradius und die Materialeigenschaften beeinflusst wird. Das Erreichen des gewünschten Innenbiegeradius ist für die Herstellung von Teilen, die die Maßanforderungen und Funktionsspezifikationen erfüllen, von entscheidender Bedeutung.
Wie entsteht der Biegeradius?
Wie genau wird dieser innere Biegeradius erreicht? Um dies herauszufinden, müssen wir uns zunächst die verschiedenen Biegemethoden auf einer Abkantpresse ansehen: Luftformen, Bodenbiegen und Prägen.
Prägung
Beachten Sie, dass es drei Biegeverfahren gibt, nicht zwei. Bodenbiegen und Prägen werden oft verwechselt und als dasselbe Verfahren bezeichnet, aber das ist nicht der Fall. Anders als Bodenbiegen dringt beim Prägen das Material tatsächlich ein und dünnt es aus.
Das Prägen ist die älteste Methode und wird größtenteils nicht mehr praktiziert, da dafür extreme Tonnagen erforderlich sind. Beim Prägen wird die Spitze des Stempels in das Material gedrückt und durchdringt die neutrale Achse (siehe Abbildung 1). Technisch gesehen können beliebige Radien geprägt werden, aber traditionell wurde das Prägen verwendet, um eine absolut scharfe Biegung zu erzielen.
This method not only requires excessive tonnages, it also destroys the material’s integrity. Coining forces the entire tool profile to less than the material thickness, and thins the material at the point of bend. It requires dedicated, special tool sets for each bend and bend angle. The punch nose produces the inside radius, which is used to establish the bend deduction.
Bodenbiegung
Bottom bending forces the material around the punch nose. It uses various punch angles along with a V die (see Figure 2). In coining, the entire face of the punch is stamped into the workpiece. In bottom bending, only the punch nose radius is “stamped” into the material.
Beim Luftformen (das später ausführlicher beschrieben wird) senkt sich der Stempelkolben, um den erforderlichen Biegewinkel plus einen kleinen Betrag zur Berücksichtigung der Rückfederung zu erzeugen. Dann fährt der Stempel aus der Matrize zurück und das Material federt in den gewünschten Winkel zurück. Wie beim Luftformen muss der Kolben beim Bodenbiegen bis zu einem Punkt abgesenkt werden, der den Biegewinkel plus einen kleinen Betrag erzeugt. Aber anders als beim Luftformen geht der Kolben weiter über diesen Punkt hinaus und senkt sich weiter in den Matrizenraum, wodurch das Werkstück zurück in den eingestellten Biegewinkel gedrückt wird. (Nebenbei bemerkt: Auch Spezialmatrizen wie Rolla-Vs und Urethanwerkzeuge drücken den Radius der Stempelnase in das Material.)
On average, the bend attains 90 degrees at a point in the die space that’s about 20 percent the material thickness, as measured from the bottom of the V die. For instance, 0.062-in.-thick cold-rolled steel will bottom once the punch nose is 0.074 to 0.078 in. from the bottom of the V die.
Wie beim Prägen bestimmt der Radius der Stempelspitze den Innenradius des Materials, der zur Festlegung der Biegeverkürzung verwendet wird. Anders als beim Prägen können mit dem Bodenprägen jedoch Innenbiegeradien von bis zu dreimal oder mehr der Materialstärke erzeugt werden.
Luftformung
Bisher scheint alles ziemlich unkompliziert. Beim Prägen und Bodenbiegen bestimmt der Radius der Stempelnase den Wert des inneren Biegeradius, der in die Formeln für die Biegeabzüge eingesetzt werden muss. Beim Luftformen kommt jedoch eine gewisse Komplexität hinzu, da die Biegemethode auf eine völlig andere Weise einen inneren Biegeradius am Teil erzeugt.
Der Stempel senkt sich (links), bis sich das Material um die Stempelnase wickelt (Mitte). Danach übt der Stößel weiterhin Druck nach unten aus und drückt das Material in den gewünschten Biegewinkel (rechts).
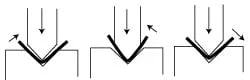
In air forming, the radius is produced as a percentage of the die opening regardless of the die style, be it a V, channel, or acute. The die opening determines the inside bend radius on the part. To determine the inside radius developed over a given die opening and for various material types and thicknesses, technicians have used what’s known as the 20 percent rule. This states that to produce a desired radius, or to find the resulting inside radius, the material thickness must be a certain percentage of the width of the die opening.
Ja, bei vielen heutigen Legierungen, darunter auch neuen und recycelten Metallen, ist es unmöglich, einen standardmäßigen Prozentmultiplikator mit absoluter Genauigkeit zu bestimmen. Dennoch bietet Ihnen die Regel einen guten Ausgangspunkt.
Die Prozentsätze der 20-Prozent-Regel lauten wie folgt:
304 stainless steel: 20-22 percent of the die opening
AISI 1060 cold-rolled steel, 60,000-PSI tensile: 15-17 percent of the die opening
H series soft aluminum: 13-15 percent of the die opening
Hot-rolled pickled and oiled (HRPO): 14-16 percent of the die opening
Wenn Sie mit diesen Prozentsätzen arbeiten, beginnen Sie mit dem Median, bis Sie den Wert finden, der den Materialeigenschaften, die Sie von Ihrem Metalllieferanten erhalten, am besten entspricht. Multiplizieren Sie die Öffnung mit dem Prozentsatz, um den entwickelten Innenradius des Teils zu erhalten. Das Endergebnis ist der Innenradiuswert, den Sie bei der Berechnung des Biegeabzugs verwenden müssen.
If you have a 0.472-in. die opening, and you’re bending 60,000-PSI cold-rolled steel, start with the median percentage, 16 percent of the die opening: 0.472 × 0.16 = 0.0755. So in this case, a 0.472-in. die opening will give you a 0.0755-in. floated inside bend radius on the part.
When your die opening changes, so does your inside radius. If the die opening is 0.551 in. (0.551 × 0.16), the inside bend radius changes to 0.088; if the die opening is 0.972 in. (0.972 × 0.16), the inside bend radius changes to 0.155.
If you’re working with 304 stainless steel, multiply its median percentage value—21 percent—by the die opening. So, that same 0.472-in. die opening now gives you a much different inside radius: 0.472 × 0.21 = 0.099 in. As before, when you change the die opening, you change the inside bend radius. A 0.551-in. die opening (0.551 × 0.21) calculates out to a 0.115-in. inside radius; a 0.972-in. die opening (0.972 × 0.21) gives you a 0.204-in. inside bend radius.
Wenn Sie das Material ändern, ändern Sie den Prozentsatz. Wenn Sie mit Material arbeiten, das hier nicht aufgeführt ist, können Sie das Material im Internet nachschlagen und die Zugfestigkeit mit dem Basiswert von 60.000 PSI für kaltgewalzten AISI 1060-Stahl vergleichen. Wenn der Zugfestigkeitswert 120.000 PSI beträgt, ist Ihr geschätzter Prozentwert doppelt so hoch wie der von kaltgewalztem Stahl, also 30 bis 32 Prozent.
Scharfe Biegungen beim Airforming
Unlike in bottoming or coining, there is a minimum radius that can be produced with air forming. This value is best set at 63 percent of the material thickness. That value moves up or down based on the material’s tensile strength, but 63 percent is a practical working value.
This minimum-radius point is what’s known as a sharp bend (see Figure 4). Understanding the effects of sharp bends is arguably one of the most important things an engineer and press brake operator need to know. Not only do you need to understand what is physically happening when the bend is sharp, but you also need to know how to incorporate that information into your calculations.
Der Radius wird als Prozentsatz der Matrizenöffnung angegeben, unabhängig von der Matrizenart.
Wenn Sie mit einer Materialstärke von 0,100 Zoll arbeiten, multiplizieren Sie diese Zahl mit 0,63, um einen minimalen Innenbiegeradius von 0,063 Zoll zu erhalten. Für dieses Material ist dies der minimale Innenradius, der mit Luftformung erzeugt werden kann. Dies bedeutet, dass selbst wenn Sie mit einem Stanznasenradius von weniger als 63 Prozent der Materialstärke Luftformung durchführen würden, der Innenradius des Teils immer noch 63 Prozent seiner Materialstärke oder 0,063 Zoll betragen würde. Verwenden Sie daher in Ihren Berechnungen keine Innenradien, die kleiner als dieser Wert von 63 Prozent sind.
Say you’re air forming with 0.250-in.-thick material and using a punch with a nose radius that’s 0.063 in.—a value that’s much less than 63 percent of the 0.250-in. material thickness. Regardless of what’s called on the print, this setup will produce an inside bend radius in the part much greater than that of the punch nose. In this case, the minimum producible inside bend radius is 63 percent of that 0.250-in. material thickness, or 0.1575 in.
As another example, say you’re working with 0.125-in.-thick material. For this, a bend “turns sharp” at a radius of 0.078 in. Why? Because 0.125 multiplied by 63 percent gives you 0.078. This means that any punch nose radius less than 0.078 in.—be it 0.062, 0.032, or 0.015 in.—will produce an inside bend radius of 0.078 in.
Scharfe Biegungen sind eine Funktion der Materialstärke, nicht des Radius der Stanznase. Eine Stanznase mit einem Radius von 0,125 Zoll fühlt sich bei Berührung nicht scharf an, bei 0,250 Zoll dickem Material jedoch schon. Und dieses Problem muss in Ihren Berechnungen berücksichtigt werden, wenn Sie erwarten, dass die Biegeableitung und damit Ihr erstes Teil korrekt ist.
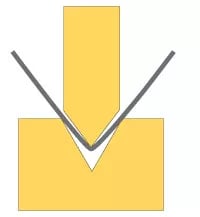
Ein Aktionsplan
In bottoming or coining, use the punch nose radius as the inside bend radius in your bend deduction calculations. But if you are air forming, the inside bend radius is produced as a percentage of the die opening. And if you are designing for an air form and the print calls for a sharp bend, that too will need to be changed to an inside bend radius value that’s 63 percent of the material thickness.
Wenn Sie im Ingenieurwesen arbeiten, lassen Sie sich am besten eine Liste aller in Ihrer Werkstatt verfügbaren Werkzeuge erstellen. Sprechen Sie mit den Mitarbeitern und finden Sie heraus, welche Methoden sie mit welchen Materialarten verwenden, und entwerfen Sie Ihre zukünftigen Teile anhand dieser Parameter.
Sobald die Biegeabzüge berechnet und die flachen Teile hergestellt sind, notieren Sie diese Informationen in der Auftragsmappe oder im Arbeitsordner. Geben Sie unbedingt den Werkzeugtyp und die Werkzeuggröße sowie den Radius an, den der Bediener basierend auf der Formmethode erreichen soll.
Getting all this to work requires buy-in from shop floor workers. Including them in the process and asking them for input will make them much more willing to accept that engineering is telling them which tools to use. Why? Because they told you what they do, and they know you’re designing parts based around that. Ideally, this will all match with the values calculated at the press brake controller and by your CAD system.
Wenn der Radius erreichbar ist, wenn das Teil für diesen Radius berechnet ist und wenn die Bediener die Werkzeuge verwenden, für die der Auftrag ausgelegt ist, werden sie beim ersten Versuch ein perfektes Teil herstellen. Vertrauen Sie mir. Es funktioniert.
Biegeformeln
Bend Allowance (BA) = [(0.017453 × Inside radius) + (0.0078 × Material thickness)] × Complementary bend angle
Figure 4: When air forming, you cannot form an inside bend radius that’s less than 63 percent of the material thickness,
an diesem Punkt wird die Form als scharfe Biegung bezeichnet. Wenn Sie einen schärferen Stanzradius verwenden, erzwingen Sie nur einen Graben
in der Mitte der Biegung. Der resultierende innere Biegeradius des Teils bleibt bei 63 Prozent der Materialstärke.
Outside Setback (OSSB) = [Tangent (Degree of bend angle / 2)] × (Inside bend radius + Material thickness)
Bend Deduction (BD) = (Outside setback × 2) – Bend allowance There are two ways to calculate the flat blank. The calculation to use depends on the application and information available:
Flat-blank Calculation = Dimension to apex + Dimension to apex – Bend deduction
Flachrohling-Berechnung = Abmessung des ersten Schenkels + Abmessung des zweiten Schenkels + Biegezugabe
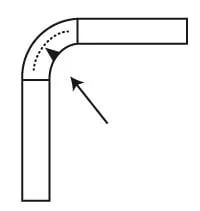